- お役立ち記事
- Introduction and utilization of software to register and analyze parts replacement information at production sites
月間76,176名の
製造業ご担当者様が閲覧しています*
*2025年3月31日現在のGoogle Analyticsのデータより
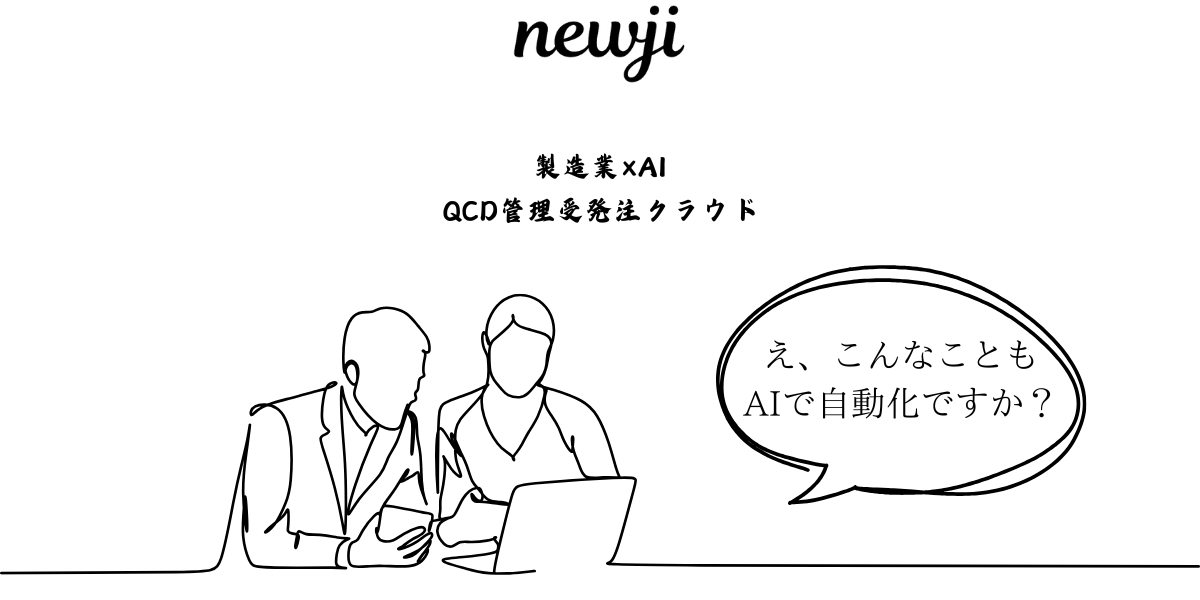
Introduction and utilization of software to register and analyze parts replacement information at production sites
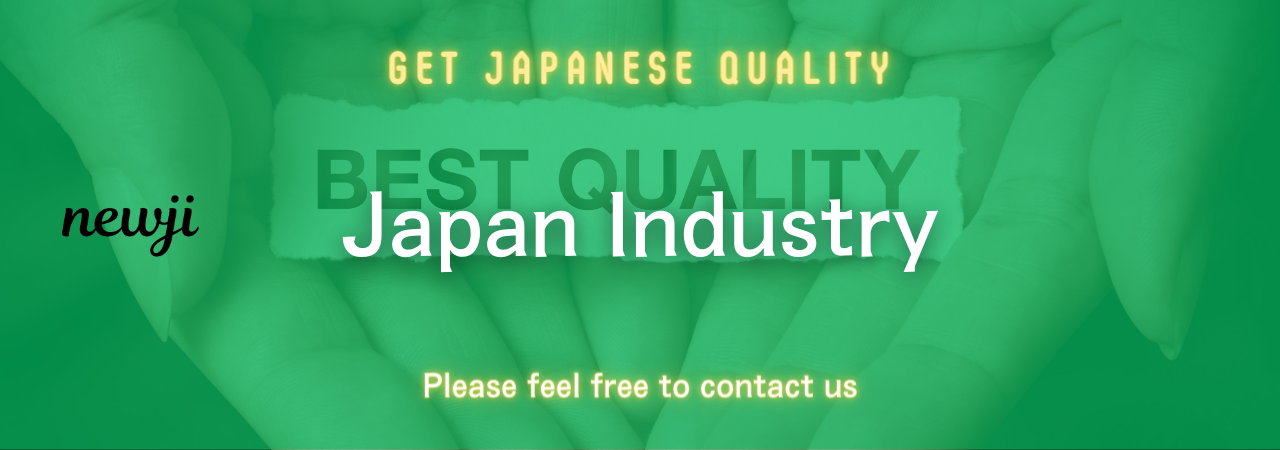
目次
Understanding the Importance of Parts Replacement Information
In the world of production and manufacturing, keeping track of parts and their replacements is vital for maintaining efficiency and productivity.
Each component within machinery plays a crucial role in ensuring smooth operations.
When a part fails or reaches the end of its life cycle, timely replacement becomes necessary.
Not only does it prevent unexpected downtimes, but it also enhances the longevity of the entire system.
This means systems need to run efficiently, and any downtime can lead to significant financial losses.
Having an efficient system to register and analyze parts replacement information is therefore indispensable.
The Role of Software in Parts Replacement Management
Modern production sites often rely on software solutions to manage parts replacement information.
This approach offers several advantages over traditional paper-based or manual tracking systems.
Firstly, software provides a centralized database where all relevant information about parts and their replacements can be stored.
This makes it easier to maintain records and retrieve data when needed.
Furthermore, software solutions often come with advanced features that enable users to analyze data, predict future needs, and plan for replacements effectively.
Enhanced Data Accuracy
One of the most significant benefits of using software is the accuracy it brings to data management.
Manual tracking methods are prone to errors, which can result in incorrect inventory counts or missed replacements.
Software systems, on the other hand, reduce human error by automating data entry processes.
This ensures that the information is accurate and up-to-date, thereby supporting informed decision-making.
Improved Efficiency and Productivity
Utilizing software for parts replacement management translates to enhanced efficiency and productivity.
With automated alerts and notifications, maintenance teams can be proactively informed about upcoming parts replacement schedules.
This allows them to prepare in advance, reducing downtime and ensuring seamless operations.
Moreover, with quick access to data, employees are empowered to make faster, data-driven decisions that contribute to overall productivity.
Choosing the Right Software for Your Production Site
Selecting the right software to manage parts replacement information is crucial for maximizing the benefits it offers.
There are several factors to consider during this selection process.
To begin with, it is essential to assess your specific needs.
What features are critical to your operations?
Understanding this will help narrow down the options available in the market.
Key Features to Look For
Certain features can significantly enhance a software’s effectiveness.
These include user-friendly interfaces that simplify navigation, real-time data tracking, and the ability to integrate with existing systems and processes.
Software that offers predictive maintenance capabilities is also beneficial, as it can analyze trends and predict future parts replacement needs.
This allows for better planning and budgeting, minimizing unexpected costs.
Scalability and Customization
As your operations grow, your parts replacement management needs may evolve.
Thus, choosing a software that is scalable and customizable is crucial.
This ensures that the solution remains relevant and effective as your production site expands.
Customizable software allows you to tailor features and reports according to your specific needs, providing a more personalized and efficient experience.
Implementing Software for Seamless Parts Management
Once the right software has been chosen, it’s time to focus on its implementation.
A well-planned implementation strategy is key to ensuring a smooth transition from manual to automated systems.
Begin by training employees on how to use the software effectively.
Proper training ensures that everyone is on the same page and can utilize the system to its full potential.
Data Migration
If you are transitioning from a traditional system, ensuring a seamless migration of data is critical.
This involves transferring existing records to the new software while maintaining data integrity.
Working with experienced IT professionals can simplify this process and reduce the risk of data loss.
Continuous Evaluation and Improvement
Implementing software is not a one-time task.
It’s important to regularly evaluate the system’s performance and make necessary adjustments.
Gathering feedback from users can be immensely valuable in understanding any challenges they face.
This feedback can be used to make improvements and enhance the software’s utility further, continually refining its effectiveness.
Benefits of Utilizing Software for Parts Replacement
Incorporating software into parts replacement management offers numerous benefits that extend beyond accuracy and efficiency.
One major advantage is cost savings.
Timely replacements and reduced downtime mean that production sites can avoid unnecessary repair costs and maximize profits.
Additionally, having a robust system in place fosters a proactive maintenance culture within the organization.
Employees become more engaged and are better positioned to address issues before they become major problems.
This not only boosts morale but also contributes to creating a more resilient and future-ready organization.
Conclusion
In today’s fast-paced manufacturing environment, the importance of efficient parts replacement management cannot be overstated.
Utilizing software to register and analyze data not only optimizes operations but also empowers businesses to stay competitive.
With the right software solution in place, production sites can look forward to improved accuracy, enhanced productivity, and significant cost savings.
Investing in such technology today means a more sustainable and successful tomorrow.
資料ダウンロード
QCD管理受発注クラウド「newji」は、受発注部門で必要なQCD管理全てを備えた、現場特化型兼クラウド型の今世紀最高の受発注管理システムとなります。
ユーザー登録
受発注業務の効率化だけでなく、システムを導入することで、コスト削減や製品・資材のステータス可視化のほか、属人化していた受発注情報の共有化による内部不正防止や統制にも役立ちます。
NEWJI DX
製造業に特化したデジタルトランスフォーメーション(DX)の実現を目指す請負開発型のコンサルティングサービスです。AI、iPaaS、および先端の技術を駆使して、製造プロセスの効率化、業務効率化、チームワーク強化、コスト削減、品質向上を実現します。このサービスは、製造業の課題を深く理解し、それに対する最適なデジタルソリューションを提供することで、企業が持続的な成長とイノベーションを達成できるようサポートします。
製造業ニュース解説
製造業、主に購買・調達部門にお勤めの方々に向けた情報を配信しております。
新任の方やベテランの方、管理職を対象とした幅広いコンテンツをご用意しております。
お問い合わせ
コストダウンが利益に直結する術だと理解していても、なかなか前に進めることができない状況。そんな時は、newjiのコストダウン自動化機能で大きく利益貢献しよう!
(β版非公開)