- お役立ち記事
- Introduction of non-destructive testing technology as an efficient inspection method for infrastructure equipment
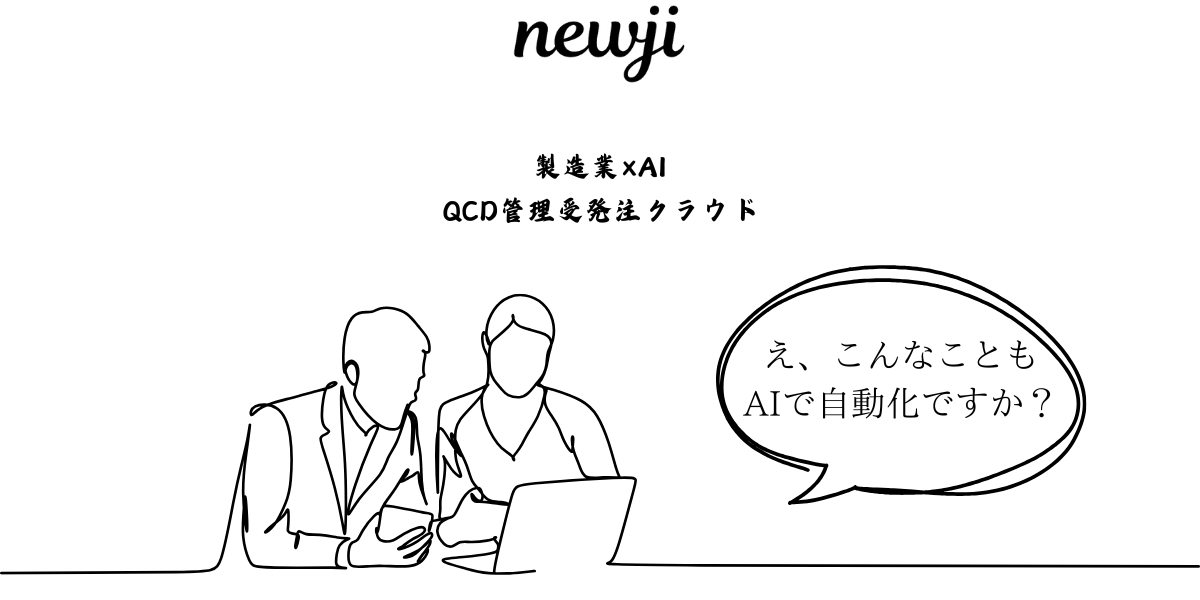
Introduction of non-destructive testing technology as an efficient inspection method for infrastructure equipment
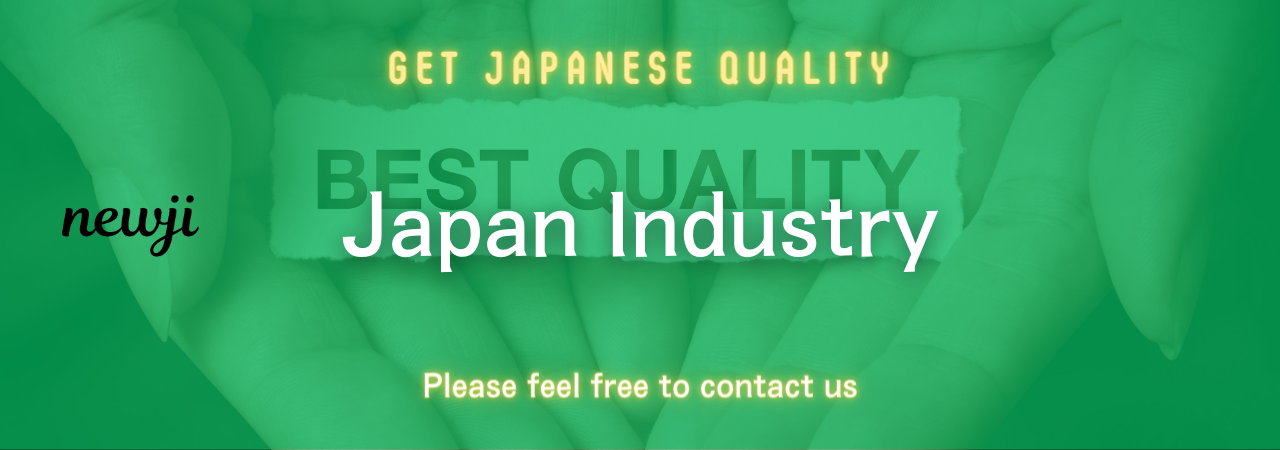
目次
Understanding Non-Destructive Testing (NDT)
Non-destructive testing (NDT) is a vital inspection tool that enables the assessment of infrastructure equipment without causing any damage to the material or components being tested.
This technology is crucial for ensuring the safety and reliability of structures such as bridges, pipelines, and power plants, where degradation could lead to significant failures.
By employing various techniques, NDT provides insights into the integrity and performance of materials, allowing for timely maintenance and effective management of infrastructure assets.
Why Non-Destructive Testing is Important
The importance of non-destructive testing lies in its ability to detect potential issues without dismantling or altering the equipment.
This makes it an economically sound approach, as it preserves the asset’s value while providing critical data about its condition.
In industries where downtime can lead to substantial financial loss, NDT is an efficient solution, as it enables ongoing monitoring without interrupting service.
In addition, NDT helps to prevent catastrophic failures by identifying flaws or weaknesses before they evolve into critical problems.
This proactive approach not only extends the lifespan of infrastructure but also enhances its safety for users.
Types of Non-Destructive Testing Techniques
Several NDT techniques are available, each suited to specific applications and types of materials.
Understanding these methods is crucial for selecting the appropriate inspection strategy.
Visual Inspection
Visual inspection is the simplest form of NDT and involves examining the surface of materials with the naked eye or using magnification tools.
This technique is useful for detecting surface-level defects, such as cracks, corrosion, or misalignment.
While it provides immediate results, it is often used in conjunction with other methods for a more comprehensive analysis.
Ultrasonic Testing
Ultrasonic testing employs high-frequency sound waves to detect internal flaws in materials.
A transducer emits sound waves, which travel through the material and reflect back upon encountering a defect.
By analyzing these wave patterns, technicians can identify anomalies such as internal cracks or voids.
Ultrasonic testing is highly effective for inspecting metal components and composite materials.
Radiographic Testing
Radiographic testing uses X-rays or gamma rays to capture images of the internal structure of materials.
Similar to medical X-rays, this technique can reveal hidden defects such as welding flaws, voids, or inclusions.
Radiographic testing is favored for its ability to provide a permanent record of the inspection and its effectiveness in thicker materials.
Magnetic Particle Testing
This method involves applying a magnetic field to the surface of ferromagnetic materials to detect surface and slightly subsurface discontinuities.
After magnetization, iron particles are applied, highlighting the location of any flaws.
Magnetic particle testing excels in detecting small cracks and weld discontinuities on metal surfaces.
Eddy Current Testing
Eddy current testing is utilized for inspecting conductive materials.
An electromagnetic coil introduces alternating currents, which generate eddy currents in the test material.
The presence of flaws disrupts these currents, and variations are detected using a probe.
This technique is particularly effective for surface and near-surface defect detection in tubing and aircraft components.
Applications of Non-Destructive Testing
NDT is widely used across various industries, contributing to the safety and reliability of numerous infrastructure systems.
Transportation Sector
In the transportation sector, NDT is crucial for maintaining the integrity of railways, bridges, and highways.
Regular inspections help identify structural weaknesses that could pose a threat to public safety.
This ensures that any necessary repairs can be conducted before issues escalate, preventing accidents and service disruptions.
Oil and Gas Industry
For the oil and gas industry, NDT is employed to inspect pipelines, storage tanks, and refineries.
Given the potential hazards involved, ensuring the integrity of these infrastructures is paramount.
NDT allows for the early detection of corrosion, leaks, or other defects, reducing the risk of environmental damage and operational failures.
Aerospace Sector
In aerospace, the utilization of NDT methods ensures the safe and efficient operation of aircraft.
Regular inspections of fuselages, wings, and engines are conducted to detect fatigue, corrosion, or other damages that may compromise flight safety.
The reliability of NDT contributes significantly to maintaining high safety standards in the industry.
Benefits of Non-Destructive Testing
The advantages of NDT extend beyond cost-effective maintenance.
This inspection approach offers several key benefits:
– **Safety enhancement:** By identifying potential failures before they occur, NDT ensures the safety of both infrastructure and its users.
– **Cost savings:** Preventative maintenance enabled by NDT reduces repair costs and minimizes unscheduled downtimes.
– **Preservation of assets:** The non-invasive nature of NDT means materials and components remain intact during testing.
– **Environmental protection:** Early detection of issues prevents leaks and structural failures, reducing environmental impact.
Future Trends in Non-Destructive Testing
The future of non-destructive testing looks promising, driven by advancements in technology and increased demand for infrastructure maintenance.
Emerging trends include the integration of digital imaging and data analytics, which allow for more precise detection and diagnosis of defects.
Additionally, the use of drones for aerial inspections and remote monitoring is on the rise, providing access to hard-to-reach areas with greater efficiency.
As NDT technology continues to evolve, it will undoubtedly play an even more critical role in maintaining the safety and operational longevity of infrastructure assets.
Investing in these technologies not only ensures continued safety and reliability but also helps in adopting a sustainable approach to infrastructure management.
資料ダウンロード
QCD調達購買管理クラウド「newji」は、調達購買部門で必要なQCD管理全てを備えた、現場特化型兼クラウド型の今世紀最高の購買管理システムとなります。
ユーザー登録
調達購買業務の効率化だけでなく、システムを導入することで、コスト削減や製品・資材のステータス可視化のほか、属人化していた購買情報の共有化による内部不正防止や統制にも役立ちます。
NEWJI DX
製造業に特化したデジタルトランスフォーメーション(DX)の実現を目指す請負開発型のコンサルティングサービスです。AI、iPaaS、および先端の技術を駆使して、製造プロセスの効率化、業務効率化、チームワーク強化、コスト削減、品質向上を実現します。このサービスは、製造業の課題を深く理解し、それに対する最適なデジタルソリューションを提供することで、企業が持続的な成長とイノベーションを達成できるようサポートします。
オンライン講座
製造業、主に購買・調達部門にお勤めの方々に向けた情報を配信しております。
新任の方やベテランの方、管理職を対象とした幅広いコンテンツをご用意しております。
お問い合わせ
コストダウンが利益に直結する術だと理解していても、なかなか前に進めることができない状況。そんな時は、newjiのコストダウン自動化機能で大きく利益貢献しよう!
(Β版非公開)