- お役立ち記事
- Introduction of poka-yoke techniques and error reduction that new employees in the equipment management department of the glass products industry should know
月間76,176名の
製造業ご担当者様が閲覧しています*
*2025年3月31日現在のGoogle Analyticsのデータより
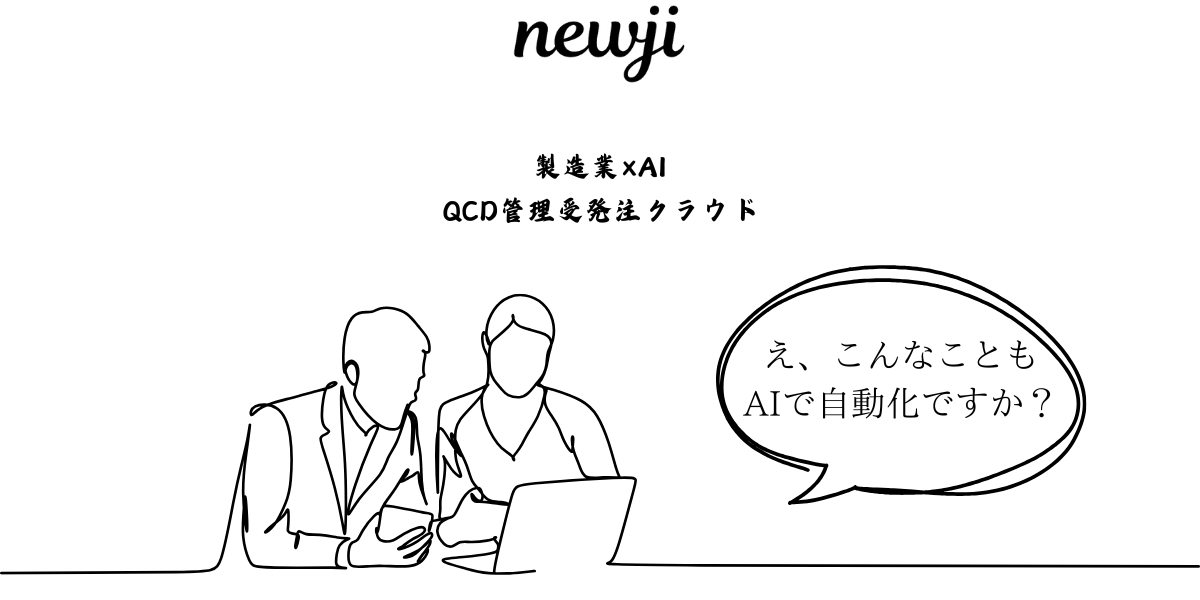
Introduction of poka-yoke techniques and error reduction that new employees in the equipment management department of the glass products industry should know
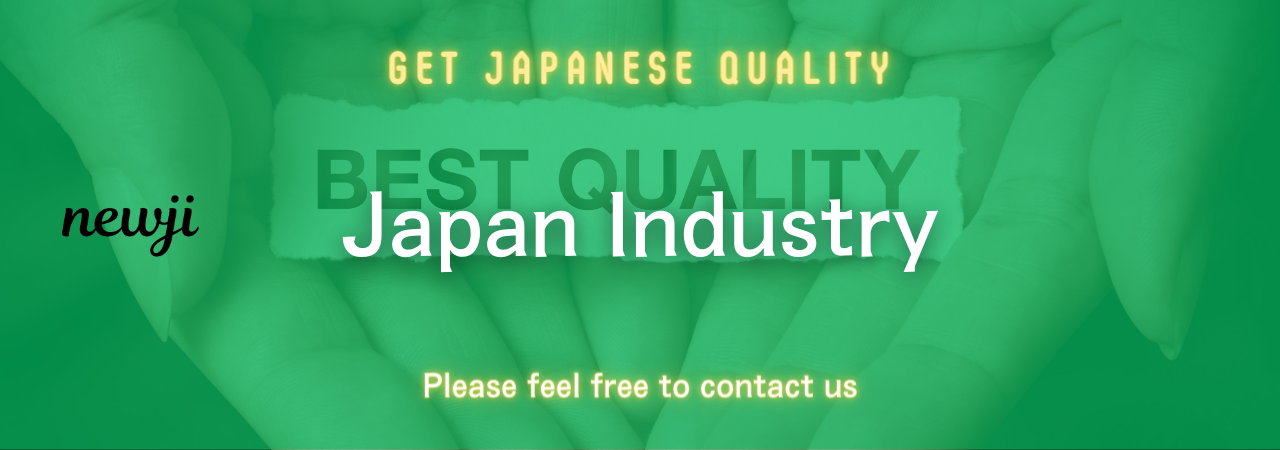
目次
Understanding Poka-Yoke: A Beginner’s Guide
Poka-Yoke is a Japanese term that translates to “mistake-proofing” or “error-proofing.”
It is a technique used in various industries, including the glass products sector, to eliminate errors by designing equipment, processes, or systems that prevent mistakes before they occur.
In the equipment management department, understanding poka-yoke can be particularly beneficial for new employees.
Let’s dive into how these techniques work and why they are essential.
The Origins of Poka-Yoke
Poka-Yoke was developed by Shigeo Shingo, an industrial engineer at Toyota, during the 1960s.
Originally called “baka-yoke,” which means “fool-proofing,” the term was later changed to be more positive and respectful.
Shingo introduced this approach to emphasize prevention over correction, which has become a cornerstone of quality assurance in manufacturing worldwide.
Why Is Poka-Yoke Important in the Glass Industry?
In the glass products industry, errors can lead to costly disruptions, safety hazards, and quality issues.
This is where poka-yoke becomes invaluable.
By implementing poka-yoke techniques, the equipment management department can ensure smoother operations, limit mistakes, and enhance overall efficiency and safety.
For new employees, familiarizing themselves with poka-yoke principles can significantly bolster their understanding and approach to minimizing errors.
How Does Poka-Yoke Work?
Poka-Yoke works by using simple, often low-cost solutions to prevent errors in process workflows.
It essentially forces the correct action or prevents an incorrect action from happening (a concept known as “fail-safing”).
Three Main Functions of Poka-Yoke
1. **Prevention**: This involves designing processes that prevent errors from occurring in the first place.
For example, using fixtures or guides to ensure components are assembled correctly.
2. **Facilitation**: This function revolves around making it easier for workers to do the right thing.
Color coding or specialized tools that fit only certain parts can guide workers effortlessly.
3. **Detection**: It allows for the identification of errors before they escalate into significant problems.
Automated alarm systems or sensors that detect anomalies in operation fall under this category.
Implementing Poka-Yoke Techniques
New employees in the equipment management department should understand how to properly implement poka-yoke techniques to maximize their benefits.
Step 1: Identify Common Errors
The first step is recognizing where errors frequently occur.
This could involve analyzing past mistake data or observing existing processes closely.
Step 2: Evaluate Root Causes
Understand why these errors happen.
This could be due to complex equipment design, insufficient training, or unclear instructions.
Addressing the root causes can lead to more effective poka-yoke solutions.
Step 3: Design Poka-Yoke Solutions
After identifying the errors and their causes, the next step is to design appropriate poka-yoke solutions.
These solutions should be simple yet effective.
For instance, introducing physical barriers to prevent misassembly or using electronic counters to monitor production outputs.
Step 4: Test and Refine Solutions
Once the solutions are in place, they should be tested thoroughly.
Any deficiencies or areas of improvement should be refined continually to ensure optimal performance and error reduction.
Examples of Poka-Yoke in the Glass Industry
To better understand poka-yoke, let’s explore some examples specific to the glass products industry.
Example 1: Color-Coded Labels
In a glass manufacturing plant, color-coded labels can help workers quickly and correctly identify different types of glass products, reducing the likelihood of mixing incorrect materials during the fabrication process.
Example 2: Safety Alarms
Safety alarms can be set for machinery that handles glass cutting or heating to alert operators if any deviation from the safe operational parameters is detected, enabling real-time adjustments to prevent accidents.
Example 3: Fixture Guides
Using fixture guides for assembling glass parts ensures only correctly aligned components are inserted, minimizing the chances of misalignment or damage during assembly.
The Benefits of Embracing Poka-Yoke
For new employees, understanding and applying poka-yoke techniques offer several benefits in the equipment management department.
Improved Product Quality
Consistent application of poka-yoke ensures higher quality products, as the majority of errors are eliminated through preventive measures.
Increased Safety
Reducing errors inherently improves the safety of operations, protecting both employees and machinery.
Enhanced Efficiency
With fewer mistakes to rectify, the overall efficiency of the production process increases, contributing to higher throughput and reduced downtime.
Conclusion
For new employees in the equipment management department of the glass products industry, mastering poka-yoke techniques is a valuable skill.
It not only promotes a deep understanding of the importance of error prevention but also equips them to contribute significantly to a more efficient and safer working environment.
As the industry continues to evolve, so does the relevance and adaptation of poka-yoke methodologies, making them an indispensable aspect of modern manufacturing processes.
資料ダウンロード
QCD管理受発注クラウド「newji」は、受発注部門で必要なQCD管理全てを備えた、現場特化型兼クラウド型の今世紀最高の受発注管理システムとなります。
ユーザー登録
受発注業務の効率化だけでなく、システムを導入することで、コスト削減や製品・資材のステータス可視化のほか、属人化していた受発注情報の共有化による内部不正防止や統制にも役立ちます。
NEWJI DX
製造業に特化したデジタルトランスフォーメーション(DX)の実現を目指す請負開発型のコンサルティングサービスです。AI、iPaaS、および先端の技術を駆使して、製造プロセスの効率化、業務効率化、チームワーク強化、コスト削減、品質向上を実現します。このサービスは、製造業の課題を深く理解し、それに対する最適なデジタルソリューションを提供することで、企業が持続的な成長とイノベーションを達成できるようサポートします。
製造業ニュース解説
製造業、主に購買・調達部門にお勤めの方々に向けた情報を配信しております。
新任の方やベテランの方、管理職を対象とした幅広いコンテンツをご用意しております。
お問い合わせ
コストダウンが利益に直結する術だと理解していても、なかなか前に進めることができない状況。そんな時は、newjiのコストダウン自動化機能で大きく利益貢献しよう!
(β版非公開)