- お役立ち記事
- Introduction of TOC (Theory of Constraints) and process control that manufacturing departments should effectively implement
Introduction of TOC (Theory of Constraints) and process control that manufacturing departments should effectively implement
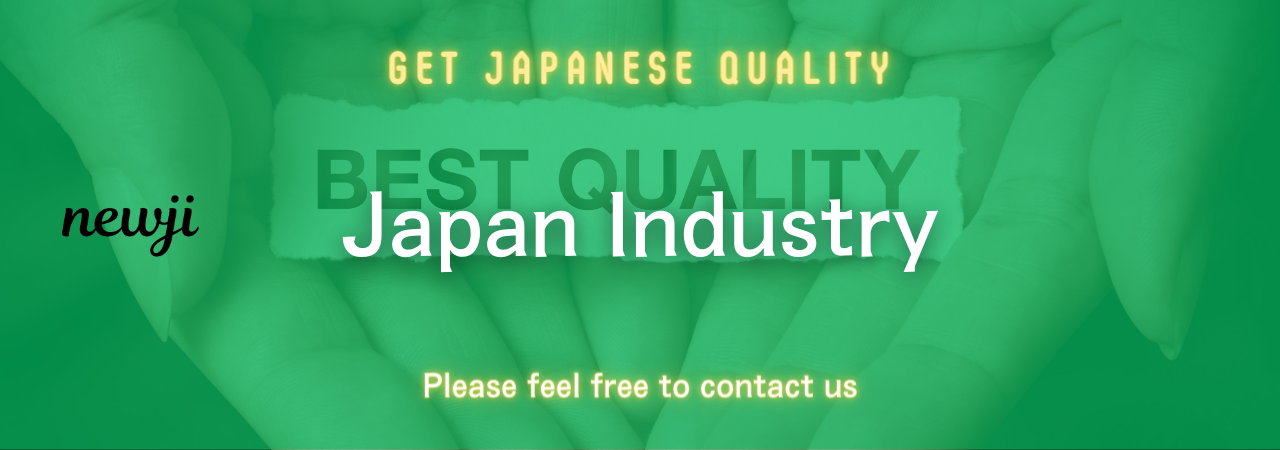
目次
Understanding the Theory of Constraints (TOC)
The Theory of Constraints (TOC) is a management philosophy that helps businesses improve their processes and achieve their goals efficiently.
TOC is based on the idea that every organization has a constraint or a bottleneck that limits its performance.
By identifying and managing this constraint, companies can enhance their productivity and profitability.
TOC assumes that any complex system, including those in manufacturing, is limited in achieving its goals by at least one constraint.
Therefore, the most significant potential for improvement lies in addressing these constraints.
The central principle of TOC is to find this limiting factor and make focused efforts to eliminate it, thereby improving the system’s overall performance.
Five Focusing Steps of TOC
The Theory of Constraints provides a simple framework known as the Five Focusing Steps.
These steps are designed to help organizations systematically identify and address their constraints.
Step 1: Identify the Constraint
The first step is to pinpoint the system’s bottleneck.
This could be a machine, a process, or any other factor that limits the overall output.
Determining the constraint requires a thorough analysis of your production process to see where work piles up or slows down.
Step 2: Exploit the Constraint
Once the constraint is identified, the next step is to maximize its throughput.
This means doing everything possible to ensure that the bottleneck operates at peak efficiency.
This may involve increasing resource availability, reducing downtime, or expediting work that passes through this constraint.
Step 3: Subordinate Other Processes
The third step involves aligning all other processes to support the constraint.
Adjust other operations to ensure they enable the constraint to work effectively.
The goal here is to prevent delays or interruptions that can hinder the performance of the bottleneck.
Step 4: Elevate the Constraint
After exploiting and subordinating, organizations should take actions to eliminate the constraint entirely.
This might include investing in new technology, hiring additional staff, or reengineering processes.
The idea is to increase capacity at the bottleneck, thereby improving the system’s overall performance.
Step 5: Repeat the Process
Once the constraint is resolved, a new one will often emerge.
TOC is an ongoing process, so repeat these steps as new constraints become apparent.
This continuous cycle of improvement helps organizations maintain high performance and adapt to changing conditions.
Implementing Process Control in Manufacturing
In addition to TOC, effective process control in manufacturing is crucial.
Process control involves monitoring and adjusting production processes to ensure they operate at optimal levels.
This is essential for maintaining quality, reducing waste, and maximizing efficiency.
Key Elements of Process Control
Implementing process control effectively requires attention to several key elements:
Data Collection
Accurate data is the foundation of good process control.
Collect relevant data on your manufacturing processes, including variables such as temperature, pressure, speed, and output rates.
This data will serve as the basis for analysis and decision-making.
Monitoring and Analysis
Consistently monitor the data to identify trends or deviations from standards.
Analyzing this data helps in understanding process behavior and pinpointing areas where adjustments are necessary.
Real-time monitoring systems can provide alerts to operators, enabling immediate corrective actions.
Standard Operating Procedures (SOPs)
Establish clear SOPs for each process to ensure consistency and reliability.
SOPs should be detailed and easy for operators to follow.
Regular updates of these procedures are necessary to adapt to any changes in the production process or technology.
Feedback Loop
Establish a feedback mechanism that enables continuous improvements.
Use insights from data analysis and operator feedback to adjust processes.
This loop ensures that corrections are not just reactive but are informed and systematic.
Training and Development
Invest in training to ensure that staff understand process control principles and procedures.
Operators should be skilled in using equipment, analyzing data, and implementing SOPs.
Ongoing education is vital to keep up with technological advancements and process innovations.
Benefits of Combining TOC with Process Control
By integrating TOC with effective process control, manufacturing departments can achieve significant gains.
Enhanced Efficiency
Together, these approaches ensure that every part of the system functions optimally and aligns with overarching goals.
This synergy eliminates waste and increases throughput, leading to enhanced efficiency.
Improved Quality
Process control ensures consistency, reducing variation and defects.
TOC helps focus improvements where they matter most, leading to better product quality and reduced rework.
Increased Profitability
With constraints minimized and processes optimized, manufacturers can produce more with the same resources.
This increase in productivity and quality translates into higher profitability.
Conclusion
Effective implementation of the Theory of Constraints and process control can transform manufacturing operations.
By identifying and managing bottlenecks and ensuring consistent process performance, organizations can enjoy increased efficiency, improved quality, and greater profitability.
These strategies require commitment but offer significant rewards for the effort.
Invest in training, data collection, and continuous improvement to maximize the potential of your manufacturing processes.
資料ダウンロード
QCD調達購買管理クラウド「newji」は、調達購買部門で必要なQCD管理全てを備えた、現場特化型兼クラウド型の今世紀最高の購買管理システムとなります。
ユーザー登録
調達購買業務の効率化だけでなく、システムを導入することで、コスト削減や製品・資材のステータス可視化のほか、属人化していた購買情報の共有化による内部不正防止や統制にも役立ちます。
NEWJI DX
製造業に特化したデジタルトランスフォーメーション(DX)の実現を目指す請負開発型のコンサルティングサービスです。AI、iPaaS、および先端の技術を駆使して、製造プロセスの効率化、業務効率化、チームワーク強化、コスト削減、品質向上を実現します。このサービスは、製造業の課題を深く理解し、それに対する最適なデジタルソリューションを提供することで、企業が持続的な成長とイノベーションを達成できるようサポートします。
オンライン講座
製造業、主に購買・調達部門にお勤めの方々に向けた情報を配信しております。
新任の方やベテランの方、管理職を対象とした幅広いコンテンツをご用意しております。
お問い合わせ
コストダウンが利益に直結する術だと理解していても、なかなか前に進めることができない状況。そんな時は、newjiのコストダウン自動化機能で大きく利益貢献しよう!
(Β版非公開)