- お役立ち記事
- Introduction to QFD for Manufacturing: Basic Concepts and Practical Approaches
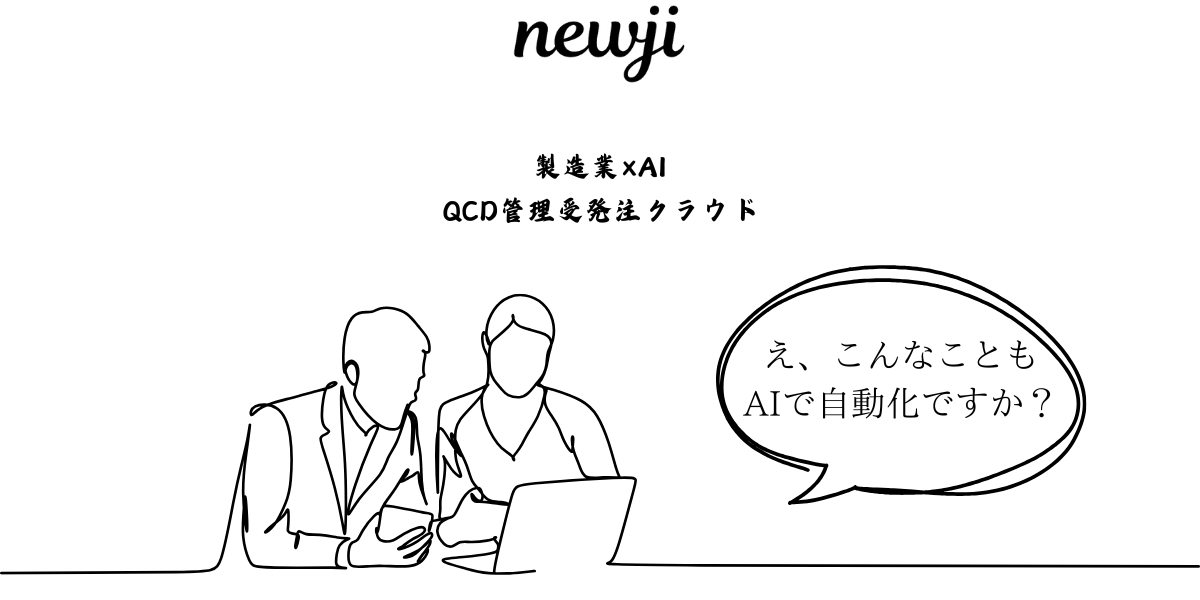
Introduction to QFD for Manufacturing: Basic Concepts and Practical Approaches
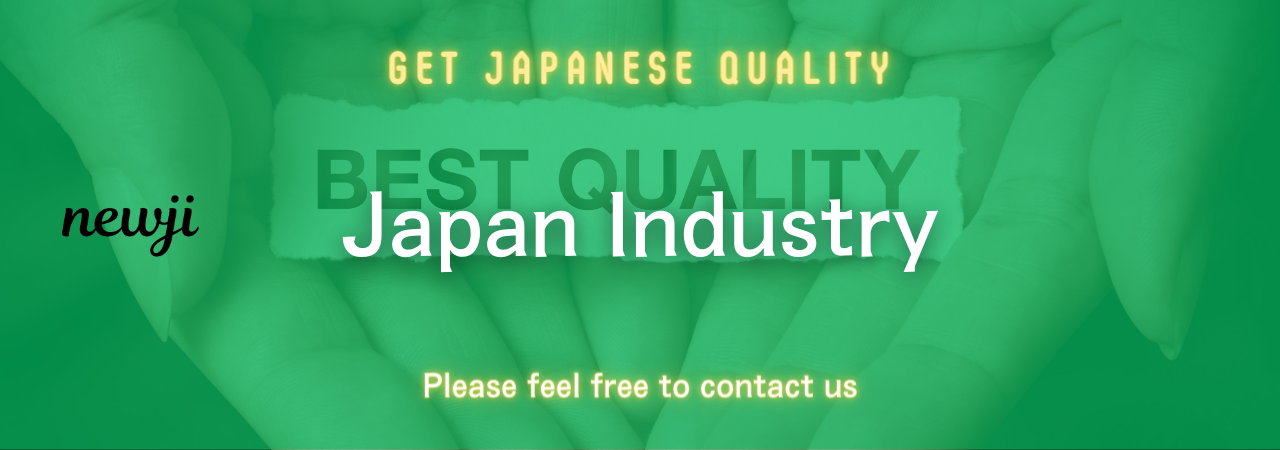
Introduction
Quality Function Deployment (QFD) is a powerful tool used in manufacturing to ensure that the final product meets customer needs and expectations.
By translating customer requirements into specific technical features and production processes, manufacturers can produce high-quality products that satisfy the market.
In this article, we will delve into the basic concepts of QFD, its benefits, and practical approaches to implementing it in a manufacturing environment.
目次
What is Quality Function Deployment (QFD)?
QFD is a systematic process that helps manufacturers understand and prioritize customer needs.
It involves various stages where customer requirements are translated into specific product features and technical specifications.
This ensures that every step of the production process aligns with what the customer wants.
The History of QFD
QFD originated in Japan in the late 1960s and was first applied by Mitsubishi’s shipbuilding division.
Since then, it has spread globally and has been adopted by many industries, including automotive, electronics, and consumer goods.
Key Components of QFD
To implement QFD effectively, it is crucial to understand its key components.
These include the Voice of the Customer (VoC), the House of Quality (HoQ), and the various matrices used to prioritize and map customer requirements to technical features.
Voice of the Customer (VoC)
Voice of the Customer is the term used to describe the process of capturing customer needs and preferences.
This can be done through surveys, interviews, focus groups, and other methods.
The collected data is then analyzed to identify the most critical requirements.
House of Quality (HoQ)
The House of Quality is a visual tool used in QFD to map customer needs to product features.
It is typically represented as a matrix, with customer requirements on one axis and technical features on the other.
By filling in this matrix, manufacturers can see how well they meet each customer need and where improvements can be made.
Prioritization Matrices
Prioritization matrices are used to rank customer needs and technical features based on their importance and feasibility.
These matrices help manufacturers focus on the most critical areas that will have the greatest impact on customer satisfaction.
Benefits of Implementing QFD in Manufacturing
There are numerous benefits to adopting QFD in the manufacturing process.
These include improved product quality, better customer satisfaction, reduced development time, and increased efficiency.
Improved Product Quality
By aligning product features with customer needs, manufacturers can produce higher-quality products.
This leads to fewer defects, less rework, and a more reliable product.
Better Customer Satisfaction
When products meet or exceed customer expectations, it results in higher satisfaction and increased brand loyalty.
This is achieved by focusing on the key features that customers value the most.
Reduced Development Time
QFD helps streamline the development process by identifying critical requirements early on.
This reduces the need for revisions and rework, leading to faster time-to-market.
Increased Efficiency
With a clear understanding of customer needs and priorities, manufacturers can optimize their production processes.
This leads to better resource allocation, reduced waste, and overall higher efficiency.
Practical Approaches to Implementing QFD
Implementing QFD involves several practical steps, from gathering customer data to creating and analyzing matrices.
Here are some of the essential steps in the QFD process.
Step 1: Collect Customer Data
The first step in QFD is to gather data on customer needs and preferences.
This can be done through surveys, interviews, focus groups, and other methods.
The goal is to have a comprehensive understanding of what the customers want.
Step 2: Identify Key Customer Requirements
Once the data is collected, the next step is to identify the most critical customer requirements.
This involves analyzing the data to find common themes and priorities.
Step 3: Develop the House of Quality
With the key requirements identified, the next step is to create the House of Quality matrix.
This involves mapping customer needs to specific technical features and evaluating how well each feature meets those needs.
Step 4: Prioritize Requirements and Features
Using prioritization matrices, manufacturers can rank customer requirements and technical features based on their importance and feasibility.
This helps focus efforts on the most critical areas.
Step 5: Implement and Monitor the Production Process
With the priorities set, the next step is to implement the production processes that align with the identified requirements.
Continuous monitoring and feedback are essential to ensure that the final product meets customer expectations.
Conclusion
Quality Function Deployment is a powerful tool that can significantly improve the manufacturing process.
By understanding and prioritizing customer needs, manufacturers can produce high-quality products that satisfy the market.
Implementing QFD requires a systematic approach, from collecting customer data to creating and analyzing matrices.
The benefits of adopting QFD include improved product quality, better customer satisfaction, reduced development time, and increased efficiency.
In a competitive market, these advantages can provide a significant edge.
Whether you are new to QFD or looking to refine your existing processes, understanding its basic concepts and practical approaches can help you achieve better results.
資料ダウンロード
QCD調達購買管理クラウド「newji」は、調達購買部門で必要なQCD管理全てを備えた、現場特化型兼クラウド型の今世紀最高の購買管理システムとなります。
ユーザー登録
調達購買業務の効率化だけでなく、システムを導入することで、コスト削減や製品・資材のステータス可視化のほか、属人化していた購買情報の共有化による内部不正防止や統制にも役立ちます。
NEWJI DX
製造業に特化したデジタルトランスフォーメーション(DX)の実現を目指す請負開発型のコンサルティングサービスです。AI、iPaaS、および先端の技術を駆使して、製造プロセスの効率化、業務効率化、チームワーク強化、コスト削減、品質向上を実現します。このサービスは、製造業の課題を深く理解し、それに対する最適なデジタルソリューションを提供することで、企業が持続的な成長とイノベーションを達成できるようサポートします。
オンライン講座
製造業、主に購買・調達部門にお勤めの方々に向けた情報を配信しております。
新任の方やベテランの方、管理職を対象とした幅広いコンテンツをご用意しております。
お問い合わせ
コストダウンが利益に直結する術だと理解していても、なかなか前に進めることができない状況。そんな時は、newjiのコストダウン自動化機能で大きく利益貢献しよう!
(Β版非公開)