- お役立ち記事
- Introduction to Thermoplastic Molding Techniques: A Guide for SMEs
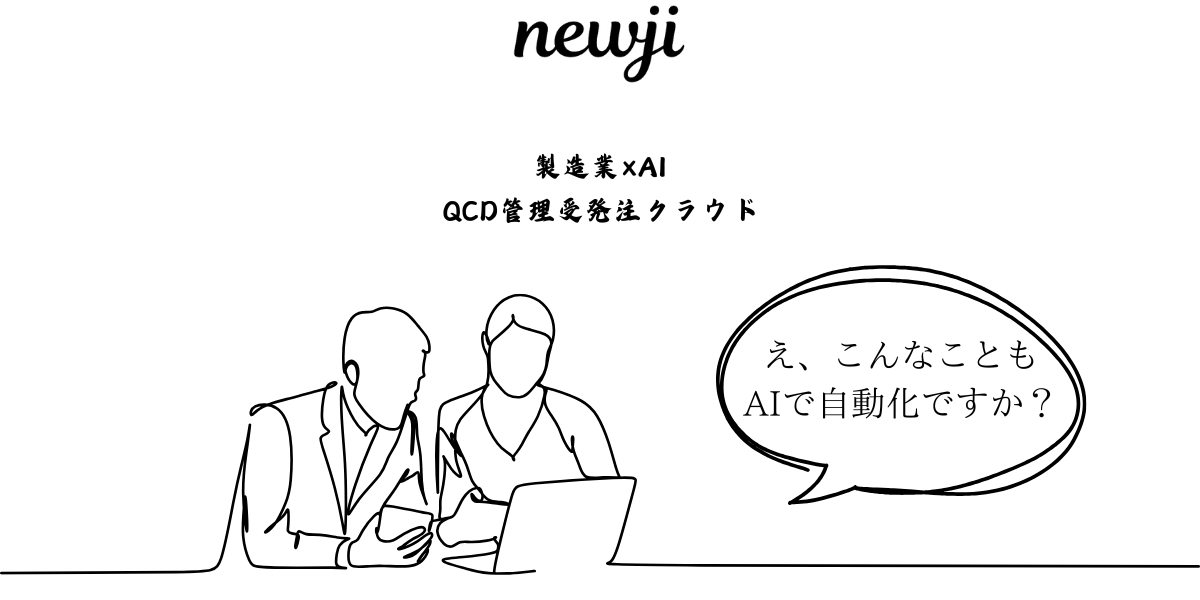
Introduction to Thermoplastic Molding Techniques: A Guide for SMEs
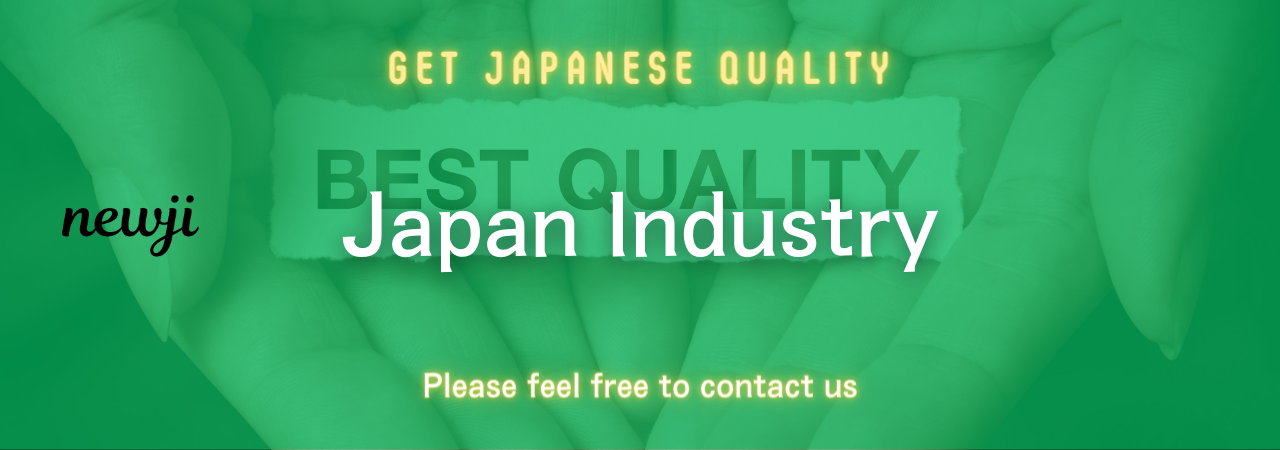
目次
What is Thermoplastic Molding?
Thermoplastic molding is a manufacturing process that shapes plastic materials into desired forms using heat and pressure.
The essential quality of thermoplastic materials is their ability to soften when heated and harden when cooled, which allows them to be reshaped multiple times.
This versatility makes thermoplastics an ideal choice for creating a wide range of products from simple containers to complex industrial parts.
Why Small and Medium Enterprises (SMEs) Should Consider Thermoplastic Molding
For small and medium enterprises (SMEs) looking into manufacturing processes, thermoplastic molding offers several compelling advantages.
Firstly, it allows for efficient mass production with a high degree of accuracy and repeatability.
This means products can be consistently manufactured to meet specific specifications, reducing waste and ensuring quality.
In addition, thermoplastic molding processes can be cost-effective.
While the initial setup may require investment in molds and machinery, the long-term savings in materials and production time can be significant, especially when compared to other manufacturing methods.
Another benefit is the flexibility in design.
Thermoplastics can be molded into complex shapes that might be challenging or impossible to achieve with metal or other materials.
This flexibility can lead to innovative product designs and improvements in functionality and aesthetics.
Types of Thermoplastic Molding Techniques
There are several methods used in thermoplastic molding, each offering unique benefits.
Understanding these processes can help SMEs determine the best approach for their manufacturing needs.
Injection Molding
Injection molding is one of the most popular methods, particularly for large-scale production.
In this process, melted thermoplastic is injected into a mold cavity where it cools and hardens into the desired shape.
Injection molding is known for its ability to produce high-quality components with minimal waste.
It’s ideal for creating parts for the automotive, electronics, and consumer goods industries.
Blow Molding
Blow molding is primarily used to produce hollow plastic parts, such as bottles and containers.
The process begins by creating a preform or parison of thermoplastic, which is then placed inside a mold and inflated to take the shape of the mold’s cavity.
Blow molding is excellent for producing lightweight, durable, and uniform parts.
Extrusion Molding
Extrusion molding is used to create long, continuous shapes like pipes, tubes, and sheets.
The thermoplastic material is melted and forced through a die of the desired cross-section.
As the plastic exits the die, it cools and hardens to maintain its shape.
This method is efficient for producing products with a constant profile over their length.
Thermoforming
Thermoforming involves heating a plastic sheet until it’s pliable, then shaping it over a mold before cooling.
This process is ideal for producing large parts with detailed features, such as vehicle panels and packaging trays.
Thermoforming is relatively simple and cost-effective, making it suitable for small production runs.
Choosing the Right Thermoplastic for Your Application
Selecting the appropriate thermoplastic material is crucial for ensuring the success of a molding project.
Various factors, such as durability, flexibility, temperature resistance, and cost, should be considered when choosing a material.
Common Thermoplastic Materials
– Polyethylene (PE): Known for its flexibility and resistance to impact and moisture, PE is widely used in packaging and containers.
– Polypropylene (PP): Offers excellent chemical resistance and is often used for automotive parts and textiles.
– Polyvinyl Chloride (PVC): Commonly used in construction for pipes and fittings due to its strength and weather resistance.
– Polyethylene Terephthalate (PET): Highly durable and commonly used in beverage bottles and food containers.
– Acrylonitrile Butadiene Styrene (ABS): Combines strength and rigidity, making it suitable for electronics and automobile components.
Implementing Thermoplastic Molding in SMEs
For SMEs planning to implement thermoplastic molding, the first step is understanding the specific needs and capabilities of the business.
It’s crucial to evaluate the product requirements and the scale of production to determine the suitable molding technique and material.
Investing in quality molds and machinery is also essential.
While this can be a significant upfront cost, it ensures precision, durability, and efficiency in the long run.
Additionally, partnering with skilled operators or training existing staff on the molding equipment can help maintain consistent product quality.
SMEs should also consider the environmental impact of their manufacturing processes.
Thermoplastics are recyclable, so developing a system for reprocessing and reusing materials can result in cost savings and a more sustainable operation.
Conclusion
Thermoplastic molding provides SMEs with numerous opportunities for growth and innovation.
By understanding and leveraging various techniques, businesses can enhance their production capabilities, reduce costs, and create high-quality products.
With careful planning and execution, thermoplastic molding can be a pivotal part of an SME’s manufacturing strategy.
資料ダウンロード
QCD調達購買管理クラウド「newji」は、調達購買部門で必要なQCD管理全てを備えた、現場特化型兼クラウド型の今世紀最高の購買管理システムとなります。
ユーザー登録
調達購買業務の効率化だけでなく、システムを導入することで、コスト削減や製品・資材のステータス可視化のほか、属人化していた購買情報の共有化による内部不正防止や統制にも役立ちます。
NEWJI DX
製造業に特化したデジタルトランスフォーメーション(DX)の実現を目指す請負開発型のコンサルティングサービスです。AI、iPaaS、および先端の技術を駆使して、製造プロセスの効率化、業務効率化、チームワーク強化、コスト削減、品質向上を実現します。このサービスは、製造業の課題を深く理解し、それに対する最適なデジタルソリューションを提供することで、企業が持続的な成長とイノベーションを達成できるようサポートします。
オンライン講座
製造業、主に購買・調達部門にお勤めの方々に向けた情報を配信しております。
新任の方やベテランの方、管理職を対象とした幅広いコンテンツをご用意しております。
お問い合わせ
コストダウンが利益に直結する術だと理解していても、なかなか前に進めることができない状況。そんな時は、newjiのコストダウン自動化機能で大きく利益貢献しよう!
(Β版非公開)