- お役立ち記事
- Inventory optimization challenges and solutions faced by purchasing departments
月間76,176名の
製造業ご担当者様が閲覧しています*
*2025年3月31日現在のGoogle Analyticsのデータより
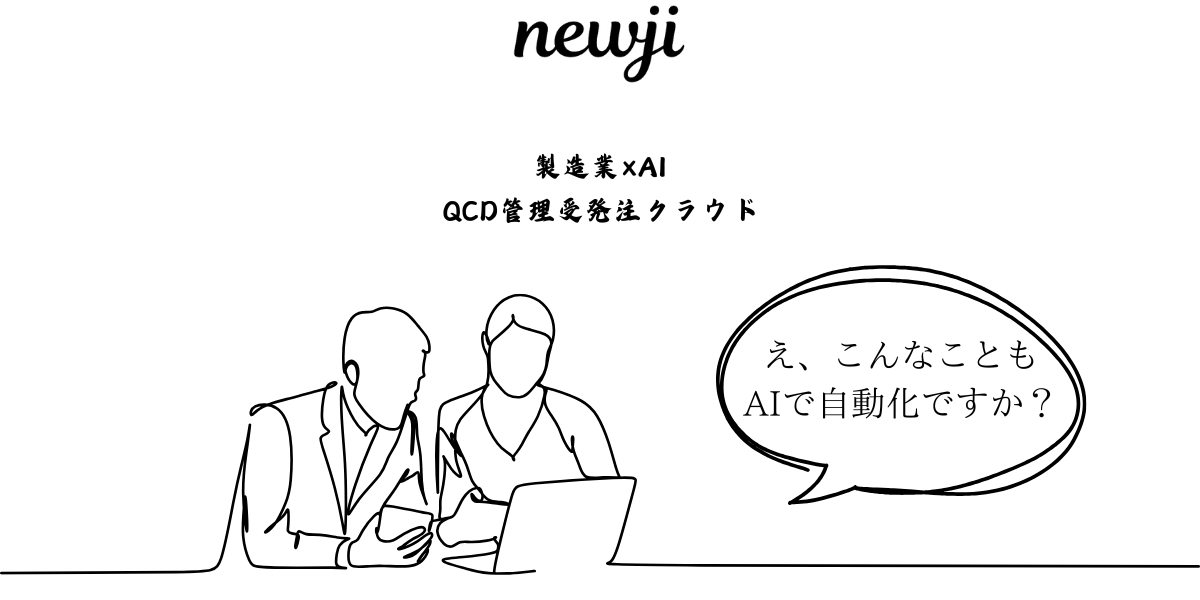
Inventory optimization challenges and solutions faced by purchasing departments
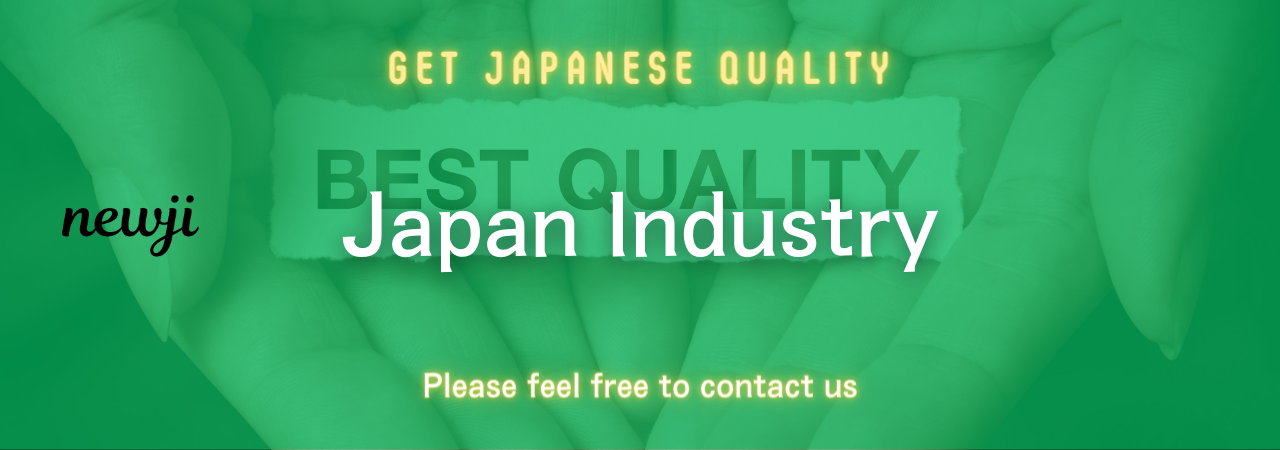
目次
Understanding Inventory Optimization
Inventory optimization is a critical process for purchasing departments in businesses of all sizes.
It involves managing stock levels to meet customer demand while minimizing costs and maximizing efficiency.
Achieving the right balance is crucial to ensure that operations run smoothly without overstocking, understocking, or incurring unnecessary expenses.
The Challenges of Inventory Optimization
1. Demand Forecasting
One of the primary challenges in inventory optimization is demand forecasting.
Predicting customer demand with accuracy is essential, as inaccurate forecasts can lead to either excess inventory or stockouts.
This is particularly challenging because customer demand can be influenced by a range of factors such as seasonality, market trends, and economic conditions.
Purchasing departments must gather and analyze a significant amount of data to make informed forecasts, and even then, there is always an element of uncertainty.
2. Supply Chain Variability
Supply chain variability is another significant challenge for inventory optimization.
Delays in deliveries, changes in supplier lead times, or disruptions due to external factors like natural disasters can all affect inventory levels.
Purchasing departments must develop strategies to manage these uncertainties, such as maintaining safety stock or implementing buffer systems, which can complicate the optimization process.
3. Balancing Costs and Customer Satisfaction
Balancing the costs associated with inventory management while ensuring customer satisfaction is a delicate task.
Holding costs, such as storage and insurance, can erode profitability if inventory levels are too high.
Conversely, frequent stockouts can lead to dissatisfied customers and lost sales.
Purchasing departments must constantly evaluate their inventory policies to achieve a balance that minimizes costs yet satisfies customer expectations.
4. Integrating Technology
Technological integration is crucial for effective inventory optimization, but it presents its own set of challenges.
Implementing advanced inventory management systems or transitioning from manual processes to automated ones can be costly and time-consuming.
Moreover, training staff to effectively use new systems can be a hurdle.
However, these technologies are essential for real-time data analysis and decision-making, which are vital for maintaining optimal inventory levels.
5. Product Lifecycle Management
Managing product lifecycles is another tricky aspect of inventory optimization.
Products go through various stages from introduction to decline, and purchasing departments must adjust inventory levels accordingly.
This might involve phasing out products that are reaching the end of their lifecycle or ramping up inventory for new product launches.
Handling these transitions smoothly is crucial to avoid obsolescence or missing out on potential sales opportunities.
Effective Solutions for Inventory Optimization
1. Implementing Advanced Forecasting Tools
To address the challenge of demand forecasting, purchasing departments can leverage advanced forecasting tools.
These tools use historical data, market trends, and predictive analytics to generate more accurate demand forecasts.
By reducing the risk of overstocking or stockouts, these tools help in maintaining optimal inventory levels and reducing costs.
2. Enhancing Supplier Relationships
Developing strong relationships with suppliers can mitigate supply chain variability.
By collaborating closely with suppliers, purchasing departments can gain better insights into lead times and potential disruptions.
Negotiating flexible delivery schedules or securing consignment inventory agreements can also provide a buffer against unexpected changes in supply.
3. Adopting Just-in-Time (JIT) Inventory
The Just-in-Time inventory system aims to reduce holding costs by ordering and receiving goods as they are needed in production.
This approach requires precise demand forecasting and reliable suppliers but can significantly cut down on inventory costs and improve cash flow.
JIT can be an effective strategy for balancing inventory-related costs with customer demands.
4. Utilizing Inventory Management Software
Inventory management software can streamline inventory optimization processes.
These programs often come with features like real-time tracking, automated reordering, and detailed analytics.
By providing a comprehensive view of inventory levels and movements, such software simplifies decision-making and allows purchasing departments to respond swiftly to changes in demand.
5. Implementing a Regular Review Cycle
Regularly reviewing and adjusting inventory policies is crucial for effective optimization.
This involves analyzing metrics such as turnover rates, lead times, and holding costs to identify inefficiencies or areas of improvement.
By making data-driven adjustments, purchasing departments can ensure that their inventory strategies evolve in line with business needs and external factors.
Conclusion
Inventory optimization is an ongoing challenge that purchasing departments must navigate carefully.
By addressing key challenges such as demand forecasting, supply chain variability, and integrating technology, organizations can significantly enhance their inventory management processes.
Implementing effective solutions, like advanced forecasting tools, strong supplier relationships, and modern inventory software, can lead to improved efficiency, reduced costs, and increased customer satisfaction.
Recognizing both the challenges and the solutions available is the first step towards a more effective and efficient inventory management system.
資料ダウンロード
QCD管理受発注クラウド「newji」は、受発注部門で必要なQCD管理全てを備えた、現場特化型兼クラウド型の今世紀最高の受発注管理システムとなります。
ユーザー登録
受発注業務の効率化だけでなく、システムを導入することで、コスト削減や製品・資材のステータス可視化のほか、属人化していた受発注情報の共有化による内部不正防止や統制にも役立ちます。
NEWJI DX
製造業に特化したデジタルトランスフォーメーション(DX)の実現を目指す請負開発型のコンサルティングサービスです。AI、iPaaS、および先端の技術を駆使して、製造プロセスの効率化、業務効率化、チームワーク強化、コスト削減、品質向上を実現します。このサービスは、製造業の課題を深く理解し、それに対する最適なデジタルソリューションを提供することで、企業が持続的な成長とイノベーションを達成できるようサポートします。
製造業ニュース解説
製造業、主に購買・調達部門にお勤めの方々に向けた情報を配信しております。
新任の方やベテランの方、管理職を対象とした幅広いコンテンツをご用意しております。
お問い合わせ
コストダウンが利益に直結する術だと理解していても、なかなか前に進めることができない状況。そんな時は、newjiのコストダウン自動化機能で大きく利益貢献しよう!
(β版非公開)