- お役立ち記事
- Inventory optimization methods for purchasing departments to reduce waste in the processing process
Inventory optimization methods for purchasing departments to reduce waste in the processing process
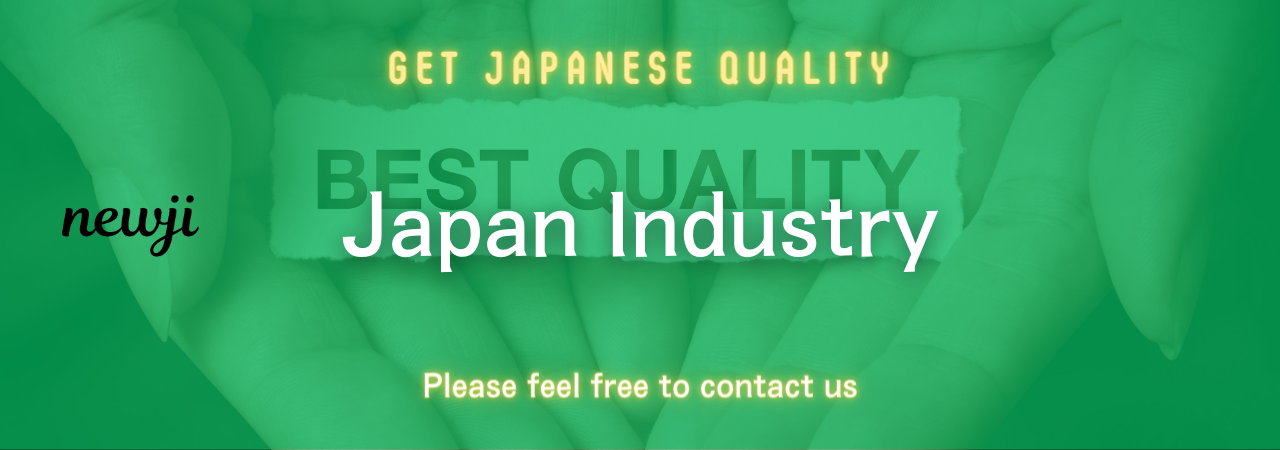
Inventory optimization is crucial for purchasing departments to reduce waste and ensure efficient processing.
Balancing supply and demand can drive cost savings and operational efficiency.
This article will delve into various methods for achieving inventory optimization and highlight their importance in a purchasing department.
目次
Understanding Inventory Optimization
Inventory optimization involves managing stock levels efficiently to meet demand while minimizing costs.
It aims to strike a balance where the right amount of inventory is available at the right time, without excess or shortage.
Effective inventory optimization can lead to a reduction in waste, improved cash flow, and increased profitability.
Methods for Inventory Optimization
There are several proven methods purchasing departments can employ to optimize inventory.
Each method has its unique advantages and can be tailored to fit specific business needs.
Just-In-Time (JIT) Inventory
Just-In-Time inventory management involves ordering and receiving goods only as they are needed in the production process.
This method minimizes holding costs and reduces waste due to overstocking.
By keeping inventory levels low, companies can respond more flexibly to changes in market demand.
Economic Order Quantity (EOQ)
Economic Order Quantity is a formula used to determine the optimal order quantity that minimizes total inventory costs, including ordering and holding costs.
The EOQ formula considers demand rate, ordering cost, and holding cost to find the ideal order size.
Implementing EOQ helps avoid overstocking and understocking, striking an efficient balance.
ABC Analysis
ABC Analysis categorizes inventory into three classes based on their value and turnover rates:
– **A items**: High-value products with low turnover.
– **B items**: Moderate value products with moderate turnover.
– **C items**: Low-value products with high turnover.
Focusing more on A items can help ensure sufficient stock levels of high-value goods without excessive investment in lower-value items.
This method aids in prioritizing inventory management efforts.
Safety Stock
Safety stock refers to additional quantities of inventory kept on hand to prevent stockouts caused by uncertainties in demand or supply.
Determining the right amount of safety stock is critical; too much can lead to excessive holding costs, while too little can result in missed sales opportunities.
Careful calculation of safety stock levels based on historical data and demand forecasts is essential.
Demand Forecasting
Accurate demand forecasting is vital for effective inventory optimization.
Utilizing historical sales data, market trends, and predictive analytics can help purchasing departments predict future demand more accurately.
With reliable forecasts, companies can make informed decisions about inventory levels, reducing the risk of excess stock or shortages.
Inventory Turnover Ratio
Monitoring the inventory turnover ratio helps determine how frequently inventory is sold and replaced over a given period.
A high turnover ratio indicates efficient inventory management, while a low ratio suggests overstocking or slow-moving goods.
By analyzing this ratio, purchasing departments can identify areas for improvement and adjust their inventory strategies accordingly.
Benefits of Inventory Optimization
Effective inventory optimization offers several significant benefits to purchasing departments:
Reduced Waste
By maintaining optimal inventory levels, companies can minimize wasted resources due to overstocking or obsolescence.
This leads to cost savings and more sustainable operations.
Improved Cash Flow
Optimized inventory levels reduce the capital tied up in stock, freeing up cash for other essential business operations.
Better cash flow management can enhance overall financial health and enable investment in growth opportunities.
Enhanced Customer Satisfaction
With adequate stock levels, companies can fulfill customer orders promptly, improving service levels and customer satisfaction.
Meeting customer demand consistently can lead to repeat business and positive brand reputation.
Operational Efficiency
Efficient inventory management reduces the time and effort spent on stock handling, storage, and management.
This improves overall operational efficiency and allows teams to focus on value-added activities.
Challenges in Inventory Optimization
While inventory optimization has numerous benefits, it also comes with challenges that purchasing departments must address:
Demand Variability
Fluctuations in demand can make it challenging to maintain optimal inventory levels consistently.
Accurate forecasting and flexible strategies are needed to adapt to changing market conditions.
Supplier Reliability
Dependence on suppliers for timely deliveries can impact inventory levels.
Building strong relationships with reliable suppliers and having contingency plans in place can mitigate risks.
Data Accuracy
Accurate and up-to-date inventory data is critical for effective optimization.
Implementing robust inventory management systems and regular audits can ensure data integrity.
Conclusion
Inventory optimization is an ongoing process that requires a strategic approach and continuous improvement.
By employing methods such as Just-In-Time inventory, Economic Order Quantity, ABC Analysis, and accurate demand forecasting, purchasing departments can achieve optimal inventory levels.
The benefits of reduced waste, improved cash flow, enhanced customer satisfaction, and operational efficiency make inventory optimization a vital aspect of modern business operations.
Understanding and addressing the challenges involved will lead to more effective inventory management and overall business success.
資料ダウンロード
QCD調達購買管理クラウド「newji」は、調達購買部門で必要なQCD管理全てを備えた、現場特化型兼クラウド型の今世紀最高の購買管理システムとなります。
ユーザー登録
調達購買業務の効率化だけでなく、システムを導入することで、コスト削減や製品・資材のステータス可視化のほか、属人化していた購買情報の共有化による内部不正防止や統制にも役立ちます。
NEWJI DX
製造業に特化したデジタルトランスフォーメーション(DX)の実現を目指す請負開発型のコンサルティングサービスです。AI、iPaaS、および先端の技術を駆使して、製造プロセスの効率化、業務効率化、チームワーク強化、コスト削減、品質向上を実現します。このサービスは、製造業の課題を深く理解し、それに対する最適なデジタルソリューションを提供することで、企業が持続的な成長とイノベーションを達成できるようサポートします。
オンライン講座
製造業、主に購買・調達部門にお勤めの方々に向けた情報を配信しております。
新任の方やベテランの方、管理職を対象とした幅広いコンテンツをご用意しております。
お問い合わせ
コストダウンが利益に直結する術だと理解していても、なかなか前に進めることができない状況。そんな時は、newjiのコストダウン自動化機能で大きく利益貢献しよう!
(Β版非公開)