- お役立ち記事
- Ion Nitriding OEM for Durable Components
月間76,176名の
製造業ご担当者様が閲覧しています*
*2025年3月31日現在のGoogle Analyticsのデータより
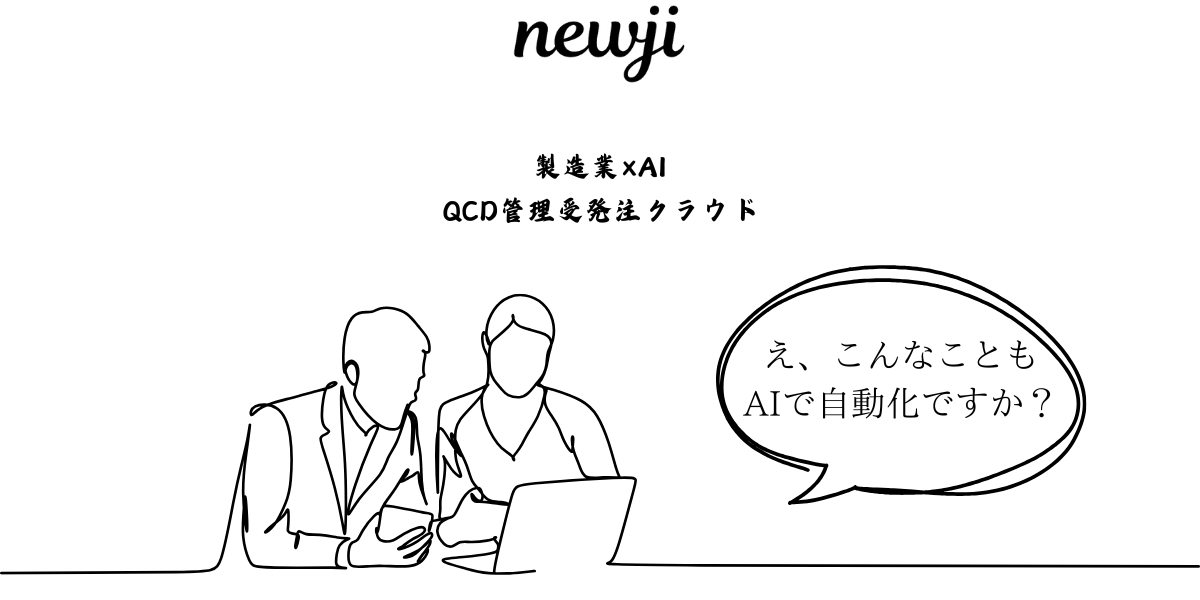
Ion Nitriding OEM for Durable Components
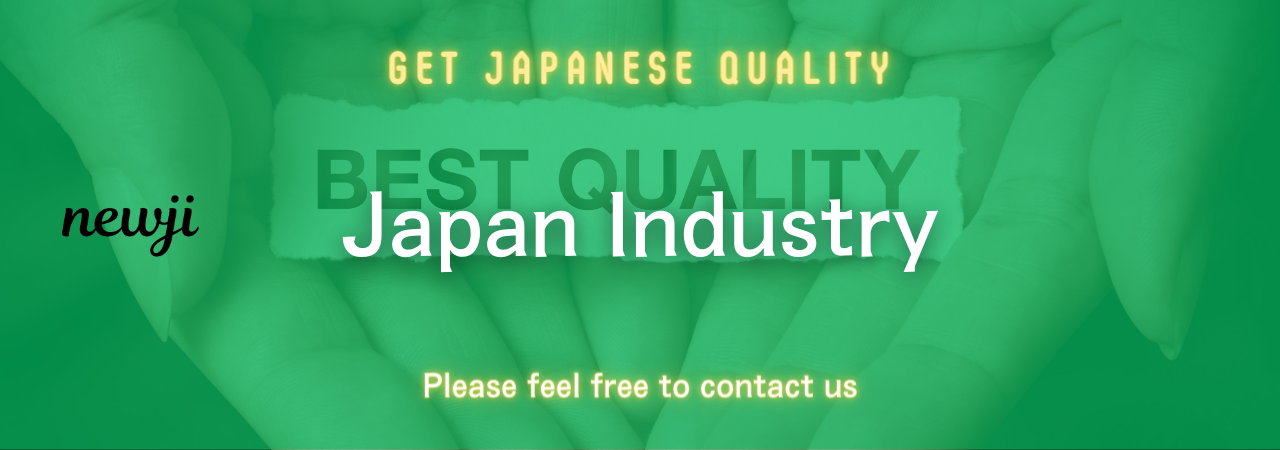
目次
What is Ion Nitriding?
Ion nitriding, also known as plasma nitriding, is a surface hardening treatment that involves diffusing nitrogen into the surface of metal components.
This process creates a hard, wear-resistant surface that greatly enhances the durability and fatigue resistance of the metal.
The treatment is carried out in a vacuum chamber where the metal is exposed to a plasma field formed by electrifying a gas, usually nitrogen or a nitrogen-hydrogen mix.
Why Choose Ion Nitriding for Component Hardening?
Ion nitriding offers several advantages over traditional hardening techniques.
First and foremost, it creates a uniform hard surface without altering the core material properties of the component.
This means that the component retains its original toughness and flexibility, while the surface is significantly hardened.
Moreover, ion nitriding operates at lower temperatures compared to conventional hardening methods.
This reduces the risk of distortion in precision components and helps retain the dimensional accuracy of parts.
Another key benefit is the environmental aspect.
Ion nitriding is a cleaner process as it avoids the pollution associated with salt bath or cyanide-based nitriding methods.
This makes it a more sustainable choice for companies looking to minimize their environmental impact.
Applications of Ion Nitriding
Ion nitriding is widely used across various industries due to its ability to enhance the wear resistance and fatigue life of components.
In the automotive industry, it’s applied to gears, crankshafts, and camshafts to prolong their service life.
In the aerospace sector, ion nitriding is used for critical components like turbine blades and structural aircraft parts to ensure they withstand significant stress and harsh operating environments.
The medical industry utilizes ion nitriding for surgical tools and implants, requiring a hard, wear-resistant surface without compromising the biocompatibility of the metal.
In the energy sector, it is used for pump shafts, valve components, and other equipment exposed to abrasive materials and extreme conditions.
OEM Ion Nitriding Services
Original Equipment Manufacturers (OEMs) can greatly benefit from incorporating ion nitriding into their production processes.
OEM ion nitriding services provide customized solutions, ensuring that the specific needs and requirements of the component design are met.
When working with an OEM nitriding service provider, businesses can expect a thorough consultation to understand the material composition, intended usage, and environmental conditions the parts will face.
This collaboration ensures the precise application of ion nitriding, optimizing performance and longevity.
Advantages of OEM Ion Nitriding
Partnering with an OEM ion nitriding service offers several advantages, particularly when it comes to quality control and consistency.
OEM service providers have established protocols and thorough testing processes to ensure each component meets industry standards and customer expectations.
Furthermore, OEMs often invest in advanced technologies and skilled expertise to adapt their processes according to the latest market developments.
This allows companies to access state-of-the-art nitride treatments that might be unavailable in-house.
Lastly, delegating the nitriding process to an OEM service can free up resources and reduce overhead costs for businesses, allowing them to focus on their core competencies while maintaining high-quality standards.
Factors to Consider When Selecting an OEM for Ion Nitriding
Choosing the right OEM for ion nitriding services is critical to ensuring successful component treatment.
One of the primary factors to consider is the provider’s experience and reputation in the industry.
A well-established OEM with a proven track record can offer the reliability and expertise needed for high-quality results.
It’s also important to assess the OEM’s capability to handle the specific requirements of a project.
This includes evaluating their equipment, technology, and ability to process a variety of materials.
Another crucial aspect is communication and customer support.
A good OEM should be transparent, providing clear timelines and regular updates on the progress of the nitriding process.
Finally, consider the cost-effectiveness of their services.
While the cheapest option might be tempting, it’s essential to assess the quality and long-term benefits of the treatment in relation to the price.
Conclusion
Ion nitriding is an advanced surface hardening technique that significantly enhances the durability and performance of metal components.
It offers numerous advantages, such as a uniform hard surface, reduced risk of distortion, and environmental benefits.
OEM ion nitriding services provide a tailored approach to ensuring that industrial components meet specific standards and requirements.
By selecting the right OEM partner, businesses can ensure high-quality nitriding treatments that extend the life and efficiency of their components.
Investing in ion nitriding is a smart choice for industries seeking durable, reliable, and cost-effective solutions for their metal parts.
資料ダウンロード
QCD管理受発注クラウド「newji」は、受発注部門で必要なQCD管理全てを備えた、現場特化型兼クラウド型の今世紀最高の受発注管理システムとなります。
ユーザー登録
受発注業務の効率化だけでなく、システムを導入することで、コスト削減や製品・資材のステータス可視化のほか、属人化していた受発注情報の共有化による内部不正防止や統制にも役立ちます。
NEWJI DX
製造業に特化したデジタルトランスフォーメーション(DX)の実現を目指す請負開発型のコンサルティングサービスです。AI、iPaaS、および先端の技術を駆使して、製造プロセスの効率化、業務効率化、チームワーク強化、コスト削減、品質向上を実現します。このサービスは、製造業の課題を深く理解し、それに対する最適なデジタルソリューションを提供することで、企業が持続的な成長とイノベーションを達成できるようサポートします。
製造業ニュース解説
製造業、主に購買・調達部門にお勤めの方々に向けた情報を配信しております。
新任の方やベテランの方、管理職を対象とした幅広いコンテンツをご用意しております。
お問い合わせ
コストダウンが利益に直結する術だと理解していても、なかなか前に進めることができない状況。そんな時は、newjiのコストダウン自動化機能で大きく利益貢献しよう!
(β版非公開)