- お役立ち記事
- Iron Manufacturing Process and Temperature Adjustment Function Improvement
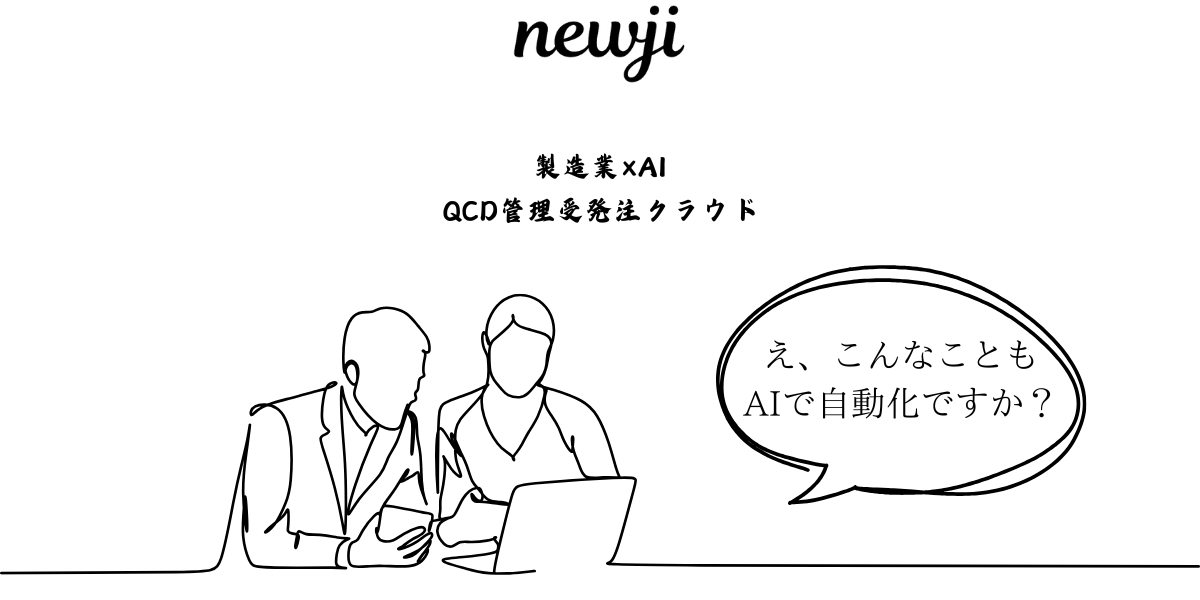
Iron Manufacturing Process and Temperature Adjustment Function Improvement
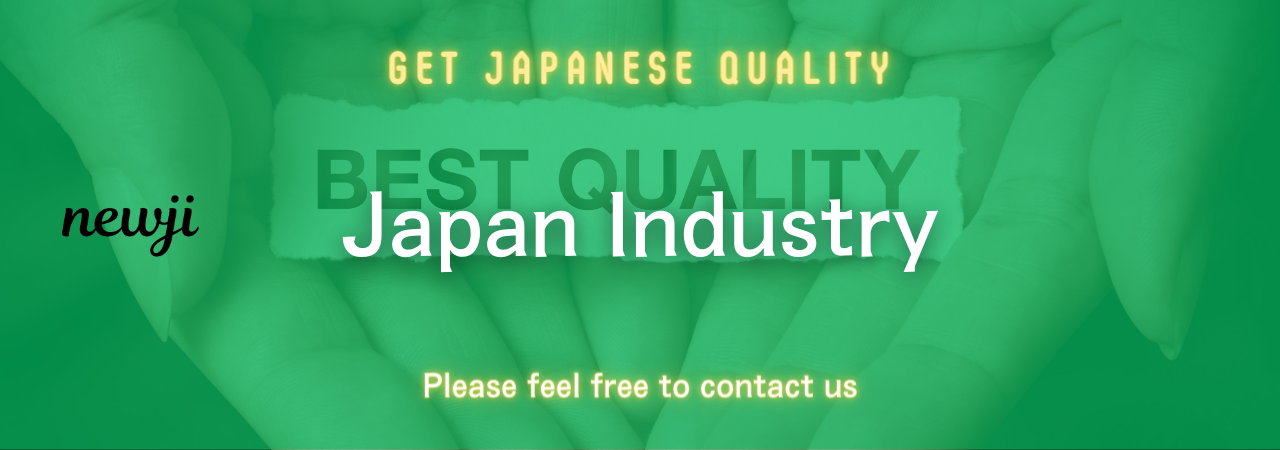
目次
Introduction to Iron Manufacturing
Iron manufacturing is a crucial process in the steel industry, providing the foundation for the production of various iron-based products.
Understanding the intricacies of this process, including temperature control, is essential for improving quality and efficiency.
This article will explore the iron manufacturing process and how advancements in temperature adjustment functions can enhance production.
The Basics of Iron Manufacturing
Iron is primarily manufactured using raw materials like iron ore, coke, and limestone.
These materials are combined in a blast furnace, where the iron ore is transformed into molten iron.
The goal is to eliminate impurities and achieve the desired chemical composition for further processing into steel or other iron products.
Step-by-Step Iron Manufacturing Process
1. **Preparation of Raw Materials:**
The iron ore is crushed and mixed with coke and limestone.
This mixture is known as the burden, which will be fed into the blast furnace.
2. **Reduction Reaction in the Blast Furnace:**
Once the burden is loaded, the furnace is heated to a high temperature.
As the coke burns, it produces carbon monoxide, which reacts with iron ore to form molten iron and carbon dioxide.
3. **Collection of Molten Iron:**
The molten iron gathers at the bottom of the furnace, separate from other byproducts like slag, which can be removed.
4. **Refinement:**
The molten iron is further purified and adjusted to meet specific requirements by adding elements such as carbon, manganese, or silicon.
5. **Shaping and Cooling:**
The refined iron is cast into different shapes according to its final use and allowed to cool and solidify.
Importance of Temperature Control
Temperature control plays a pivotal role in the iron manufacturing process.
Precise temperature adjustments ensure that chemical reactions occur efficiently and that the quality of the iron is up to industrial standards.
Poor temperature management can lead to defects, reducing the usability of the final product.
Challenges in Temperature Management
1. **Consistency:**
Maintaining a consistent temperature throughout the process is challenging due to fluctuations in raw material quality or furnace performance.
2. **Energy Consumption:**
High temperatures require significant energy, leading to increased operational costs.
3. **Precision:**
Achieving the precise temperature needed for each reaction phase is critical but difficult due to the dynamic nature of the blast furnace.
Improving Temperature Adjustment Functions
Advancements in technology have paved the way for improved temperature control functions in iron manufacturing.
These innovations focus on enhancing accuracy, reducing energy consumption, and minimizing human error.
Technological Innovations
1. **Automation and Control Systems:**
Modern iron manufacturing incorporates automated systems that continuously monitor furnace temperatures and make real-time adjustments.
These systems rely on sensors and algorithms to maintain optimal conditions.
2. **Predictive Analytics:**
Using predictive models allows manufacturers to anticipate temperature changes and proactively adjust settings.
This leads to fewer disruptions and more efficient operations.
3. **Energy-Efficient Furnaces:**
New furnace designs aim to maximize energy efficiency through better insulation and heat recovery mechanisms.
These innovations help maintain temperature stability with less energy input.
Benefits of Enhanced Temperature Control
1. **Improved Product Quality:**
By maintaining precise temperatures, the final iron product meets stringent quality standards, with fewer defects and impurities.
2. **Cost Reduction:**
Efficient temperature management reduces energy costs and minimizes resource waste.
3. **Environmental Benefits:**
Better energy usage results in decreased emissions, contributing to a more sustainable manufacturing process.
Conclusion
The iron manufacturing process is a complex series of steps that transforms raw materials into high-quality iron products.
Within this process, temperature control is of paramount importance to ensure efficiency and product quality.
As technology evolves, improved temperature adjustment functions offer a promising future for the industry, leading to enhanced performance, reduced costs, and greater sustainability.
Understanding and implementing these advancements can significantly benefit manufacturers, helping them meet the demands of an ever-evolving market.
資料ダウンロード
QCD調達購買管理クラウド「newji」は、調達購買部門で必要なQCD管理全てを備えた、現場特化型兼クラウド型の今世紀最高の購買管理システムとなります。
ユーザー登録
調達購買業務の効率化だけでなく、システムを導入することで、コスト削減や製品・資材のステータス可視化のほか、属人化していた購買情報の共有化による内部不正防止や統制にも役立ちます。
NEWJI DX
製造業に特化したデジタルトランスフォーメーション(DX)の実現を目指す請負開発型のコンサルティングサービスです。AI、iPaaS、および先端の技術を駆使して、製造プロセスの効率化、業務効率化、チームワーク強化、コスト削減、品質向上を実現します。このサービスは、製造業の課題を深く理解し、それに対する最適なデジタルソリューションを提供することで、企業が持続的な成長とイノベーションを達成できるようサポートします。
オンライン講座
製造業、主に購買・調達部門にお勤めの方々に向けた情報を配信しております。
新任の方やベテランの方、管理職を対象とした幅広いコンテンツをご用意しております。
お問い合わせ
コストダウンが利益に直結する術だと理解していても、なかなか前に進めることができない状況。そんな時は、newjiのコストダウン自動化機能で大きく利益貢献しよう!
(Β版非公開)