- お役立ち記事
- Is Inspector “Error” the Cause of Defect Leakage? Eradicating Defect Leakage Through “Process Improvement” in Visual Inspection: Ensuring Visual Quality and the “Correct Method” of Visual Inspection
Is Inspector “Error” the Cause of Defect Leakage? Eradicating Defect Leakage Through “Process Improvement” in Visual Inspection: Ensuring Visual Quality and the “Correct Method” of Visual Inspection
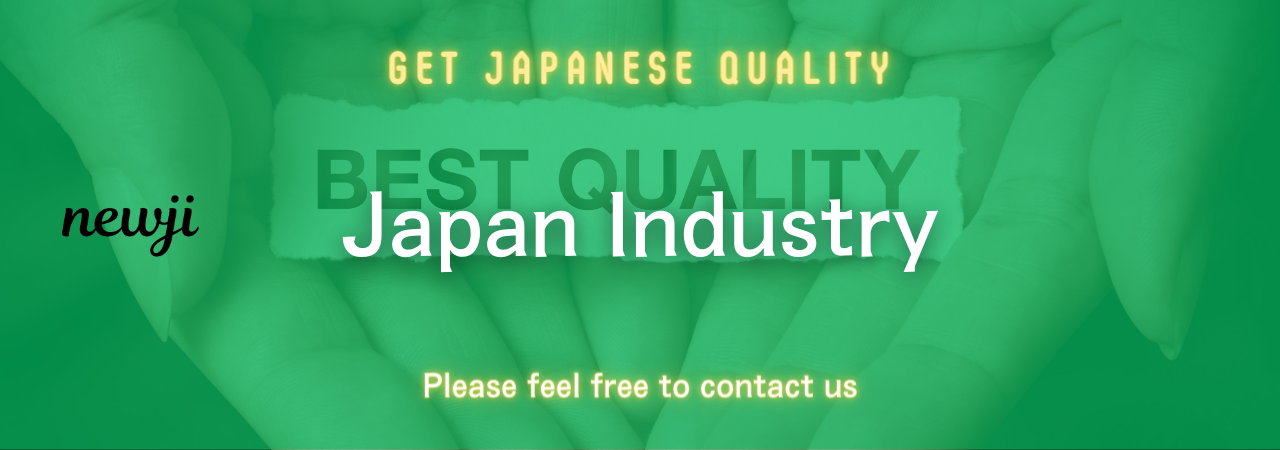
Visual inspection is a fundamental aspect of ensuring quality in manufacturing and production processes.
While other technologies such as automated systems and machine learning have made significant strides in recent times, the human eye’s precision cannot be overlooked.
However, errors during visual inspections can lead to defect leakage, subsequently affecting product quality and customer satisfaction.
In this article, we’ll explore how process improvement can help eradicate defect leakage, ensuring reliable visual quality and the correct method of visual inspection.
目次
Understanding the Role of Visual Inspection
Visual inspection is primarily used to detect surface defects, color variations, and physical deformations that might affect a product’s functionality or aesthetics.
It includes examining products or components for compliance with predefined standards and specifications.
Although simple in concept, visual inspection demands extensive attention, experience, and precision.
Types of Visual Inspection
In the realm of visual inspection, two main types are prevalent: direct visual inspection and remote visual inspection.
– **Direct Visual Inspection:** This method involves inspectors examining components or products directly with the naked eye or with the aid of magnifying tools. It is commonly used in smaller scale operations.
– **Remote Visual Inspection:** Involves the use of tools such as borescopes, endoscopes, or cameras to examine areas that are not easily accessible by direct inspection. This method is often utilized in larger or more complex assemblies.
Understanding these types helps in choosing the right approach to achieve accurate results.
Common Errors in Visual Inspection
Human error is inevitable, and visual inspection is no exception.
The common errors can be categorized into several areas:
Fatigue and Attention Span
Prolonged periods of concentration can lead to inspector fatigue, reducing their ability to detect defects accurately. The decreasing attention span as a result of extended hours of inspection often results in overlooked defects.
Lack of Standardization
Without a standardized method or guidelines, inspectors may follow varied practices, leading to inconsistent quality. This inconsistency becomes evident when different inspectors generate divergent results for similar inspections.
Inadequate Training
Undertrained inspectors might not possess the necessary skills or knowledge to identify specific defects. Proper training is crucial to ensure inspectors know what to look for and how to handle various inspection scenarios.
Strategies for Process Improvement in Visual Inspection
Eradicating defect leakage demands a commitment to process improvement.
Here are effective strategies to achieve this goal:
Implementing Standard Operating Procedures (SOPs)
The first step towards reducing errors is to develop clear and comprehensive SOPs for visual inspection. SOPs provide a well-defined process, outlining each step an inspector must follow. This standardization ensures consistency and accuracy.
Incorporating Breaks and Alternating Tasks
Scheduling regular breaks and alternating tasks can significantly minimize fatigue. Short breaks and varied tasks reduce the monotony and help maintain an inspector’s focus and efficiency.
Continuous Training and Skill Development
Continuous training programs ensure that inspectors stay updated with the latest practices and standards. Regular skill-enhancement workshops can equip them with the requisite knowledge to identify defects accurately.
Utilizing Technology for Assistance
While the human eye is critical, technology can assist in reducing errors. Implementing tools like digital microscopes, high-resolution cameras, and automated inspection systems can complement manual inspections. These tools help in magnifying and identifying defects that might go unnoticed.
Regular Audits and Feedback Mechanisms
Conducting regular audits helps identify potential gaps in the inspection process. Audits provide a platform for feedback and improvement, ensuring any identified shortcomings are promptly addressed. Establishing a feedback mechanism where inspectors can share their observations and suggestions for improvement also proves beneficial.
Ensuring Visual Quality
Ensuring visual quality relies on a combination of accurate inspections and the implementation of process improvements. Here are some additional tips to enhance visual quality:
Clear Communication
Maintaining clear communication between inspectors and other stakeholders is vital. Regular meetings to discuss inspection findings and potential areas of improvement can foster a collaborative approach toward quality maintenance.
Setting Realistic Expectations
It is important to set realistic and achievable goals for visual inspections. Overburdening inspectors with unrealistic expectations can lead to rushed inspections and missed defects.
Peer Reviews and Cross-Training
Incorporating peer reviews where inspectors cross-check each other’s work can help identify any overlooked defects. Cross-training ensures that inspectors are versatile and well-versed with different aspects of the inspection process.
The Correct Method of Visual Inspection
To achieve accurate and reliable results, a correct method must be established.
Here are the steps involved in an effective visual inspection process:
Pre-Inspection Preparation
Before the actual inspection, prepare the area and the product. Ensure proper lighting and cleanliness of both the inspection environment and the product. Familiarize yourself with the specifications and standard requirements for the product.
Initial Examination
Conduct an overall examination, looking for obvious defects or irregularities. Utilize any available inspection aids such as magnifying lenses or digital tools.
Detailed Examination
Thoroughly inspect the product or component for minute details. Follow the established SOPs, checking every aspect systematically. Note down any defects or deviations observed during the examination.
Documenting Findings
Accurately document all findings, including photographs or screenshots if using digital inspection tools. Detailed documentation helps in record-keeping and future reference.
Reporting and Feedback
Prepare a detailed report highlighting the defects identified and any corrective actions taken or suggested. Share the report with relevant stakeholders for further action.
By following these steps and integrating the strategies for process improvement, defect leakage through visual inspection can be significantly reduced.
The ultimate goal is to ensure consistent quality and reliability in the products manufactured.
Through a combination of human expertise and technological advancements, visual inspection can continue to play a pivotal role in maintaining high standards in production processes.
資料ダウンロード
QCD調達購買管理クラウド「newji」は、調達購買部門で必要なQCD管理全てを備えた、現場特化型兼クラウド型の今世紀最高の購買管理システムとなります。
ユーザー登録
調達購買業務の効率化だけでなく、システムを導入することで、コスト削減や製品・資材のステータス可視化のほか、属人化していた購買情報の共有化による内部不正防止や統制にも役立ちます。
NEWJI DX
製造業に特化したデジタルトランスフォーメーション(DX)の実現を目指す請負開発型のコンサルティングサービスです。AI、iPaaS、および先端の技術を駆使して、製造プロセスの効率化、業務効率化、チームワーク強化、コスト削減、品質向上を実現します。このサービスは、製造業の課題を深く理解し、それに対する最適なデジタルソリューションを提供することで、企業が持続的な成長とイノベーションを達成できるようサポートします。
オンライン講座
製造業、主に購買・調達部門にお勤めの方々に向けた情報を配信しております。
新任の方やベテランの方、管理職を対象とした幅広いコンテンツをご用意しております。
お問い合わせ
コストダウンが利益に直結する術だと理解していても、なかなか前に進めることができない状況。そんな時は、newjiのコストダウン自動化機能で大きく利益貢献しよう!
(Β版非公開)