- お役立ち記事
- Issue analysis/review of defects
月間76,176名の
製造業ご担当者様が閲覧しています*
*2025年3月31日現在のGoogle Analyticsのデータより
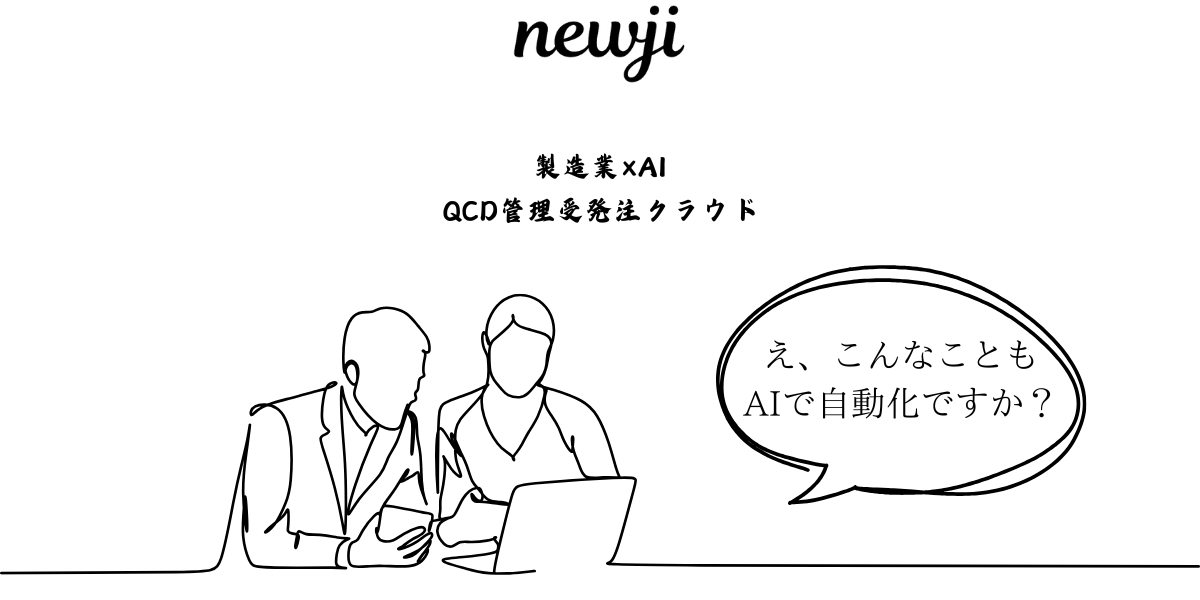
Issue analysis/review of defects
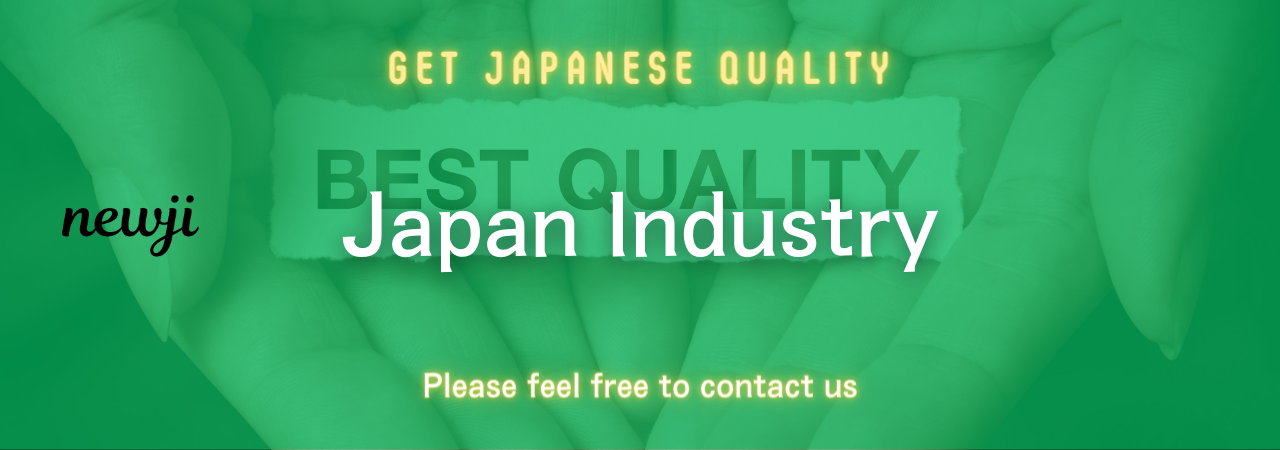
目次
Understanding the Importance of Defect Analysis
Defect analysis is a crucial part of any product development cycle.
By thoroughly understanding where and why defects occur, companies can improve their products, enhance customer satisfaction, and reduce costs.
When defects are caught and addressed early, it prevents more significant issues from arising later.
This is not only cost-effective but also crucial for maintaining a company’s reputation.
What is Defect Analysis?
Defect analysis involves systematically reviewing and assessing the defects that have been identified in a product.
This process includes categorizing defects, understanding their root causes, and identifying patterns or trends in their occurrence.
The goal is to eliminate these defects in future iterations of the product or process.
Steps in Defect Analysis
The defect analysis process can be broken down into several key steps:
1. **Identify Defects**:
The first step is recognizing that a defect exists.
This might be through product testing, customer feedback, or internal audits.
2. **Document Defects**:
Once a defect is identified, it needs to be documented thoroughly.
This documentation should include details like the nature of the defect, conditions under which it was discovered, and its impact.
3. **Categorize Defects**:
Defects should be categorized based on their severity, frequency, and area of impact.
Common categories include cosmetic, functional, and system-critical defects.
4. **Prioritize Defects**:
Not all defects require immediate attention.
Prioritizing them helps to address the most critical issues first.
Factors influencing priority include the defect’s impact on users and the resources required to fix it.
5. **Root Cause Analysis**:
Understanding the underlying cause of a defect is essential to prevent its recurrence.
Tools such as the “5 Whys” or fishbone diagrams can be of great help in determining root causes.
6. **Develop Solutions**:
Once causes are identified, teams can work on developing solutions.
Solutions can range from simple fixes to redesign of parts of the product.
7. **Implement Changes**:
Implementing changes means taking action on the solutions devised during the previous step.
This can involve updating code, altering designs, or tweaking processes.
8. **Review and Monitor**:
After changes have been implemented, it’s important to review their effectiveness.
Monitoring systems should be in place to ensure defects do not reoccur.
Benefits of Effective Defect Analysis
Carrying out thorough defect analysis has numerous advantages:
– **Improved Product Quality**:
By fixing issues at their core, the overall quality of the product improves.
– **Customer Satisfaction**:
A defect-free product satisfies customers, enhances brand reputation, and promotes customer loyalty.
– **Cost Savings**:
Early identification and resolution of defects can lead to significant cost savings.
The cost to fix an error increases exponentially the later it is found in the product lifecycle.
– **Enhanced Team Efficiency**:
Understanding where mistakes happen enables teams to improve their processes and work more efficiently.
– **Innovation**:
The insights gained from defect analysis can provide valuable guidance for future product development, encouraging innovation.
Tools and Techniques for Defect Analysis
Various tools and techniques can facilitate a more effective defect analysis process:
– **Fishbone Diagrams**:
These are also known as cause-and-effect diagrams and help identify potential causes of defects.
– **Pareto Charts**:
These charts can be used to identify the most significant defects so that resources can be concentrated on solving them.
– **Failure Mode and Effects Analysis (FMEA)**:
This is a proactive approach to foresee potential defects and address them before they occur.
– **Root Cause Analysis (RCA)**:
This involves a structured investigation to determine the root causes of defects.
Challenges in Defect Analysis
Defect analysis is not without its challenges:
– **Data Overload**:
Companies may face an overwhelming amount of data to sift through, making it hard to focus on pertinent issues.
– **Identifying Root Causes**:
Determining the exact cause of a defect can be complex and time-consuming.
– **Resource Limitations**:
Sometimes, the resources required to perform an exhaustive analysis may not be readily available.
– **Resistance to Change**:
Implementing the changes suggested by defect analysis can encounter resistance within an organization.
Conclusion
Defect analysis is an indispensable part of creating high-quality products.
By methodically identifying and addressing defects, companies can drive improvements that benefit both their customers and their bottom line.
Despite the challenges, with the right tools and commitment, defect analysis can significantly enhance product development processes.
資料ダウンロード
QCD管理受発注クラウド「newji」は、受発注部門で必要なQCD管理全てを備えた、現場特化型兼クラウド型の今世紀最高の受発注管理システムとなります。
ユーザー登録
受発注業務の効率化だけでなく、システムを導入することで、コスト削減や製品・資材のステータス可視化のほか、属人化していた受発注情報の共有化による内部不正防止や統制にも役立ちます。
NEWJI DX
製造業に特化したデジタルトランスフォーメーション(DX)の実現を目指す請負開発型のコンサルティングサービスです。AI、iPaaS、および先端の技術を駆使して、製造プロセスの効率化、業務効率化、チームワーク強化、コスト削減、品質向上を実現します。このサービスは、製造業の課題を深く理解し、それに対する最適なデジタルソリューションを提供することで、企業が持続的な成長とイノベーションを達成できるようサポートします。
製造業ニュース解説
製造業、主に購買・調達部門にお勤めの方々に向けた情報を配信しております。
新任の方やベテランの方、管理職を対象とした幅広いコンテンツをご用意しております。
お問い合わせ
コストダウンが利益に直結する術だと理解していても、なかなか前に進めることができない状況。そんな時は、newjiのコストダウン自動化機能で大きく利益貢献しよう!
(β版非公開)