- お役立ち記事
- Japanese Manufacturing Excellence: Leading Innovations in France’s Non-Ferrous Metal Processing Industry
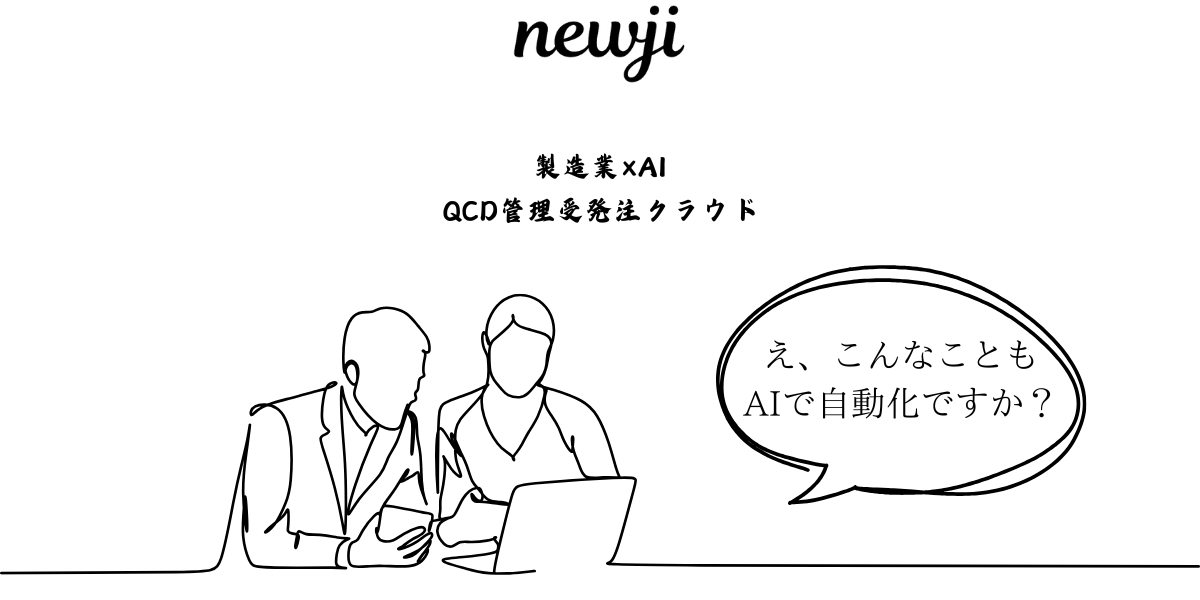
Japanese Manufacturing Excellence: Leading Innovations in France’s Non-Ferrous Metal Processing Industry
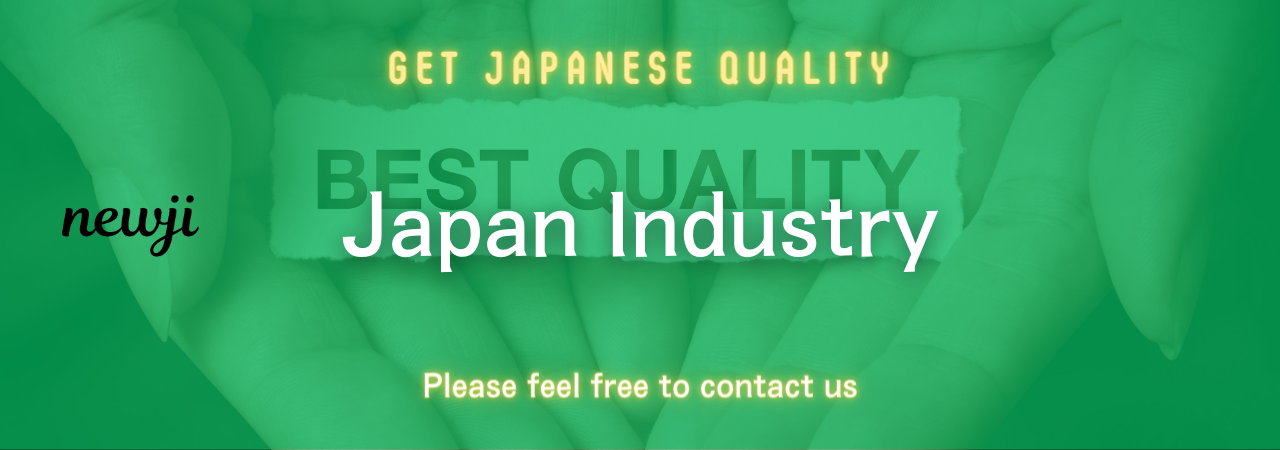
目次
Introduction
When it comes to manufacturing excellence, Japan has long been a global leader, frequently setting benchmarks for quality, efficiency, and innovation. For companies within France’s non-ferrous metal processing industry, partnering with Japanese suppliers can unlock a myriad of benefits. In this article, we will delve into the intricacies of Japanese manufacturing, its technical skills, and how best to negotiate and collaborate with Japanese suppliers. The insights shared here are grounded in years of experience in procurement and purchasing, offering practical knowledge to help your enterprise leverage Japanese expertise.
The Legacy of Japanese Manufacturing
Quality at its Core
One cannot discuss Japanese manufacturing without mentioning its unwavering commitment to quality. The concept of “kaizen,” or continuous improvement, is embedded deeply within Japanese corporate culture. Manufacturing processes are continually refined, ensuring the highest levels of precision and minimal deviations. This focus on quality is especially crucial in the non-ferrous metal processing industry, where material properties and process consistency significantly impact final products.
Advanced Technological Capabilities
Japanese companies invest heavily in research and development, ensuring they remain at the cutting edge of technology. This investment has led to innovations such as highly automated production lines, precision machining, and state-of-the-art quality control systems. For French companies, collaborating with Japanese suppliers means access to these advanced technologies, which can result in superior product quality, enhanced efficiency, and reduced costs.
Industry-Specific Advantages
The non-ferrous metal processing industry can capitalize on specific Japanese technological advancements. For example, high-precision CNC machines developed in Japan enable extremely fine adjustments and consistent production outcomes. Additionally, Japanese metallurgy offers innovative alloy compositions that can improve material properties such as strength, ductility, and thermal resistance, critical for various applications in aerospace, automotive, and electronics industries.
Advantages of Japanese Suppliers
Reliability and Consistency
Japanese suppliers are known for their reliability. Consistent delivery schedules and stringent quality control measures ensure that production processes are rarely disrupted. This reliability is vital for maintaining the integrity of supply chains, especially in industries where delays or inconsistencies can have significant economic impacts.
Cost Efficiency Through Lean Manufacturing
The principles of lean manufacturing, another cornerstone of Japanese production philosophy, aim to minimize waste while optimizing efficiency. These practices not only result in cost savings but also enhance sustainability. Reduced wastes mean fewer raw materials consumed and lower energy expenditure—valuable benefits for any manufacturing process.
Strong Ethical Standards
Japanese companies maintain high ethical standards, adhering to stringent regulations and international norms. This commitment ensures that activities such as procurement and production are conducted transparently and responsibly, fostering trust between suppliers and clients.
Challenges and Disadvantages
Cost Considerations
High quality and sophisticated technology often come with a higher price tag. While Japanese suppliers offer tremendous value, their products and services can be more expensive than alternatives from other regions. However, it’s crucial to consider the total cost of ownership, including potential savings from lower defect rates and higher efficiency.
Communication Barriers
Language and cultural differences can pose challenges in initial negotiations and ongoing collaborations. Misunderstandings can arise, potentially leading to delays or complications. Overcoming these barriers requires effort, including hiring bilingual staff or using professional translation services.
Logistics Challenges
Geographical distance can complicate logistics. Shipping costs, lead times, and potential supply chain disruptions must be meticulously managed. Utilizing advanced logistics software and maintaining strong communication channels can mitigate some of these challenges.
Effective Supplier Negotiation Techniques
Research and Preparation
Before entering negotiations with Japanese suppliers, thorough research and preparation are crucial. Understand the market conditions, your supplier’s background, and the specific capabilities they offer. This knowledge will not only help in formulating realistic expectations but also demonstrate your commitment and professionalism.
Emphasize Long-Term Relationships
Japanese business culture highly values long-term relationships and trust. Rather than focusing solely on immediate financial gains, emphasize mutually beneficial, long-term partnerships. Highlighting your commitment to collaborative growth can significantly enhance a supplier’s willingness to offer favorable terms.
Adopt a Respectful and Patient Approach
Respect and patience are key when negotiating with Japanese suppliers. Decisions may take longer due to the hierarchical nature of Japanese companies, where multiple levels of approval may be needed. Patience and respect for these processes will go a long way in building strong, sustainable relationships.
Current Market Conditions
Supply Chain Resilience
The recent global disruptions have underscored the importance of resilient supply chains. Japanese manufacturers, known for their meticulous planning and risk management, have weathered these storms relatively well. Their strategies can offer valuable lessons and advantages for companies in the non-ferrous metal processing industry.
Technological Advances
Innovations such as the Internet of Things (IoT), artificial intelligence (AI), and blockchain are transforming the manufacturing landscape. Japanese companies are at the forefront of integrating these technologies into their processes, offering enhanced traceability, predictive maintenance, and smarter production systems.
Environmental Regulations
Stringent environmental regulations worldwide are pushing industries towards greener practices. Japanese manufacturers, already leaders in sustainable manufacturing, offer materials and processes that comply with or exceed these regulations. Partnering with them can help French companies stay ahead of the curve in terms of environmental responsibility.
Best Practices for Collaboration
Foster Open Communication
Effective communication is the bedrock of any successful partnership. Establish clear channels of communication and ensure that expectations, feedback, and updates are regularly shared. Combining regular video conferences with occasional face-to-face meetings can significantly enhance mutual understanding and trust.
Leverage Their Expertise
Japanese suppliers bring a wealth of knowledge and expertise. Be open to their suggestions and willing to adapt your processes where beneficial. Leveraging their insights on materials, production techniques, or quality control can result in significant improvements in your operations.
Implement Joint Problem-Solving
When challenges arise, approach them collaboratively. Engaging in joint problem-solving sessions can not only resolve issues more efficiently but also strengthen the partnership. This approach demonstrates your investment in the relationship and commitment to mutual success.
Case Studies and Practical Applications
Case Study 1: Enhanced Material Properties
A French aerospace company collaborated with a Japanese supplier to develop a new alloy for jet engine components. The Japanese supplier’s advanced metallurgy capabilities resulted in an alloy with superior thermal resistance and strength, extending the component lifespan and performance. This collaboration also involved joint R&D efforts, enabling the French company to benefit from cutting-edge technological advancements.
Case Study 2: Improved Production Efficiency
A company in the automotive sector partnered with a Japanese supplier specializing in precision CNC machines. The introduction of these machines into the production line drastically reduced setup times and improved part consistency. Lean manufacturing principles and training from the Japanese experts further optimized production processes, resulting in significant cost savings and productivity boosts.
Case Study 3: Sustainable Manufacturing
An electronics manufacturer sought to reduce its environmental footprint and collaborated with a Japanese supplier known for its green manufacturing practices. The Japanese company provided materials with lower environmental impact and shared best practices for waste reduction and energy efficiency. This partnership not only improved the sustainability of the French company’s products but also enhanced its reputation as an environmentally responsible manufacturer.
Conclusion
The Japanese approach to manufacturing excellence offers invaluable benefits for France’s non-ferrous metal processing industry. From advanced technological capabilities to rigorous quality control and lean manufacturing principles, Japanese suppliers can significantly enhance your operations. However, navigating the challenges such as cost considerations, communication barriers, and logistics requires careful planning and respectful collaboration.
By adopting best practices in supplier negotiation, fostering open communication, and leveraging the expertise of Japanese partners, companies can unlock substantial value. The lessons learned from successful case studies underscore the transformative potential of these collaborations.
In an era where innovation, efficiency, and sustainability are more critical than ever, partnering with Japanese suppliers can offer a competitive edge. Embrace the opportunity to tap into Japan’s manufacturing prowess, and watch your enterprise thrive in the ever-evolving global landscape.
資料ダウンロード
QCD調達購買管理クラウド「newji」は、調達購買部門で必要なQCD管理全てを備えた、現場特化型兼クラウド型の今世紀最高の購買管理システムとなります。
ユーザー登録
調達購買業務の効率化だけでなく、システムを導入することで、コスト削減や製品・資材のステータス可視化のほか、属人化していた購買情報の共有化による内部不正防止や統制にも役立ちます。
NEWJI DX
製造業に特化したデジタルトランスフォーメーション(DX)の実現を目指す請負開発型のコンサルティングサービスです。AI、iPaaS、および先端の技術を駆使して、製造プロセスの効率化、業務効率化、チームワーク強化、コスト削減、品質向上を実現します。このサービスは、製造業の課題を深く理解し、それに対する最適なデジタルソリューションを提供することで、企業が持続的な成長とイノベーションを達成できるようサポートします。
オンライン講座
製造業、主に購買・調達部門にお勤めの方々に向けた情報を配信しております。
新任の方やベテランの方、管理職を対象とした幅広いコンテンツをご用意しております。
お問い合わせ
コストダウンが利益に直結する術だと理解していても、なかなか前に進めることができない状況。そんな時は、newjiのコストダウン自動化機能で大きく利益貢献しよう!
(Β版非公開)