- お役立ち記事
- Japanese Manufacturing Unveiled: The Surprising Power of Blind OEM in Global Supply Chains
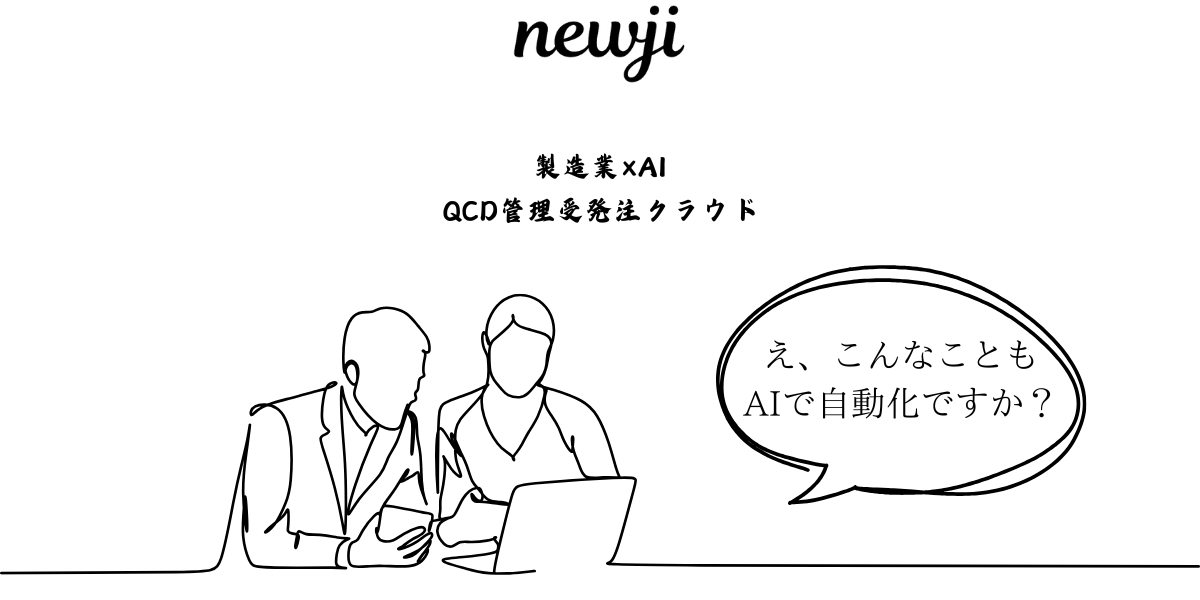
Japanese Manufacturing Unveiled: The Surprising Power of Blind OEM in Global Supply Chains
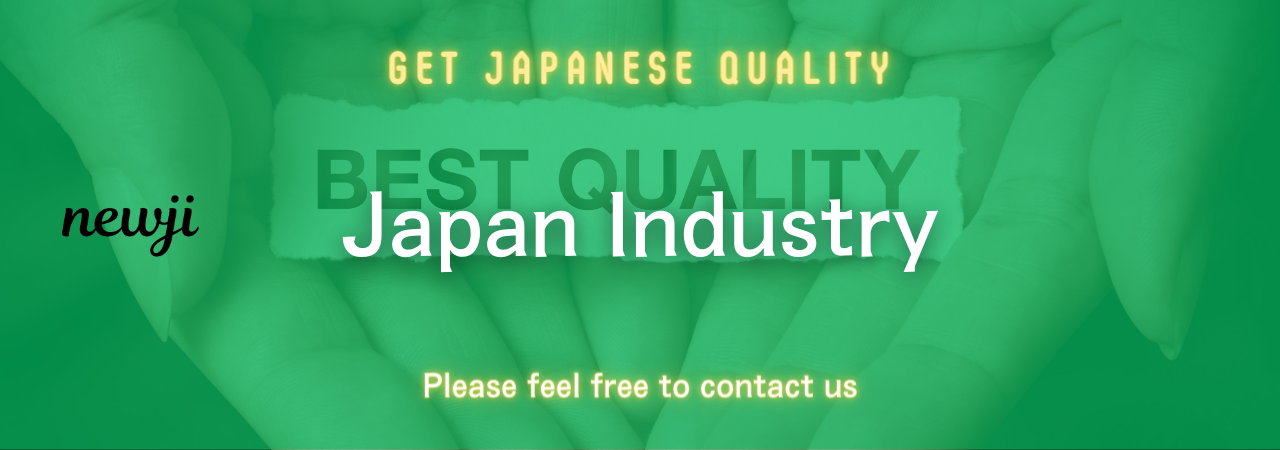
目次
Introduction
In the ever-evolving landscape of global manufacturing, Japanese companies have consistently been at the forefront of technological innovation, quality control, and efficient production methods.
When it comes to international procurement and purchasing, one of the most intriguing and powerful practices emerging from Japan is Blind OEM (Original Equipment Manufacturer).
This unique approach boasts various advantages and has the potential to bring significant benefits to global supply chains.
In this article, we will delve into the intricacies of Blind OEM, shedding light on the practical aspects, supplier negotiation techniques, market conditions, best practices, and more.
Understanding Blind OEM in the Context of Japanese Manufacturing
What is Blind OEM?
Blind OEM is a business model where a product is designed, manufactured, and tested by a third-party Japanese manufacturer but is sold under the brand name of another company.
The OEM supplier remains “blind” to the end-users or final customers, as the branding company takes full ownership of the product’s marketing, sales, and distribution.
This model capitalizes on the technical expertise and advanced manufacturing capabilities of Japanese suppliers while allowing global brands to penetrate markets with high-quality products.
Why Opt for Blind OEM?
There are several compelling reasons why companies might choose Blind OEM, particularly from Japanese suppliers.
These include high-quality manufacturing standards, innovative technology, cost-effectiveness, and flexibility.
The Japanese focus on continuous improvement (Kaizen) and their ingrained principles of craftsmanship (Monozukuri) ensure that the products meet stringent quality standards.
Furthermore, partnering with a proficient OEM can significantly reduce the time and resources required for in-house production.
Advantages of Blind OEM in Japanese Manufacturing
Quality Assurance and Control
One of the most prominent advantages of engaging with Japanese OEMs is the assurance of quality.
Japanese manufacturers are renowned for their meticulous attention to detail and adherence to strict quality control measures.
This ensures that the final product is of superior quality, minimizing the risk of defects and enhancing customer satisfaction.
Moreover, the use of advanced quality testing protocols and state-of-the-art machinery further contributes to the high standards maintained by Japanese OEMs.
Access to Cutting-Edge Technology
Japanese manufacturers are often at the leading edge of technological advancements, particularly in fields like robotics, electronics, and precision engineering.
By leveraging the know-how and technological capabilities of Japanese OEMs, companies can introduce innovative products to the market more quickly.
This not only provides a competitive edge but also aligns with the growing consumer demand for cutting-edge and reliable products.
Cost Efficiency
Outsourcing production to a Japanese OEM can be a cost-effective solution.
Manufacturing in Japan, although sometimes perceived as expensive, offers long-term savings through reduced labor costs, minimized wastage, and efficient production processes.
Furthermore, the initial higher investment in Japanese manufacturing often translates to lower costs in the future due to fewer defects, superior product lifespan, and decreased returns or customer complaints.
Flexibility and Scalability
Japanese OEMs tend to be highly versatile and adaptable, capable of scaling production volumes to meet varying demands.
Whether your requirement is for a limited batch of specialized components or mass production of consumer goods, Japanese manufacturers possess the operational flexibility to meet these needs without compromising quality.
This scalability can be particularly advantageous for companies looking to test new products before a full-scale launch.
Disadvantages and Challenges of Blind OEM
Loss of Direct Control
One of the primary disadvantages of Blind OEM is the potential loss of direct control over the manufacturing process.
While Japanese OEMs are known for their excellence, entrusting a third party with critical production tasks means relinquishing some degree of oversight.
This can pose challenges in maintaining consistent communication and ensuring that production aligns with the specific requirements and standards of your brand.
Dependency on Supplier
Relying heavily on an OEM can lead to dependency issues.
If the supplier faces operational disruptions, quality issues, or fails to meet delivery schedules, it can adversely affect the entire supply chain.
Therefore, it is crucial to establish contingency plans and maintain open lines of communication with the OEM to mitigate such risks.
Confidentiality Concerns
Though Japanese companies are typically trustworthy partners, sharing proprietary information and designs inherently carries risks.
There is always a potential for intellectual property misuse or misalignment with the OEM’s other clients, leading to competitive disadvantages.
Contracts should include stringent confidentiality agreements and regularly reviewed security measures to protect intellectual property.
Supplier Negotiation Techniques
Building Strong Relationships
In Japanese business culture, relationships play a pivotal role.
Establishing and nurturing a strong relationship with your Japanese OEM supplier can lead to better collaboration and trust.
Frequent visits, open communication, and respect for cultural norms can go a long way in building a robust partnership.
This relationship-based approach can also facilitate smoother negotiations and mutual understanding.
Comprehensive Cost Analysis
When negotiating with Japanese suppliers, a thorough cost analysis is essential.
Understanding the breakdown of costs, including labor, materials, transportation, and overheads, allows for more informed and effective negotiations.
Presenting a clear picture of how costs align with your budget and expectations can aid in reaching a mutually beneficial agreement.
Flexibility and Compromise
Flexibility is key to successful negotiations.
Recognize that certain demands may need to be adjusted to accommodate the supplier’s capabilities and limitations.
Engaging in a collaborative rather than adversarial negotiation process, where compromise is sought, often yields better long-term partnerships and favorable terms.
Market Conditions and Analysis
Current Trends
The global manufacturing landscape is constantly evolving, and Japan continues to be a significant player due to its technological advancements and high-quality production standards.
Currently, there is a considerable emphasis on automation, IoT (Internet of Things), and AI-driven manufacturing processes.
Japanese manufacturers are at the forefront of integrating these technologies, making them highly attractive partners for Blind OEM arrangements.
Economic Factors
The economic environment greatly influences manufacturing and procurement strategies.
Fluctuations in exchange rates, labor costs, and raw material availability can impact the overall cost structure.
Japan’s stable economic conditions and robust industrial policies make it a favorable location for OEM partnerships.
However, staying updated with economic trends and potential trade regulations is crucial for strategic planning.
Supply Chain Dynamics
Efficient supply chain management is critical for leveraging the benefits of Blind OEM.
Japan’s advanced logistics infrastructure ensures timely delivery and reduced lead times.
However, global supply chain disruptions, such as those caused by pandemics or geopolitical conflicts, necessitate a resilient and adaptable supply chain strategy.
Diversifying suppliers and maintaining buffer inventories can mitigate risks and ensure continuity.
Best Practices in Procuring from Japanese OEMs
Thorough Due Diligence
Conducting thorough due diligence on potential Japanese OEM partners is essential.
This includes evaluating their production capabilities, financial health, quality control measures, and previous performance.
Site visits and audits can provide valuable insights into their operations and commitment to quality.
Clear and Detailed Contracts
Clear contract agreements are the foundation of a successful Blind OEM partnership.
Contracts should outline detailed specifications, quality standards, delivery schedules, pricing structures, and confidentiality clauses.
Regularly revisiting and updating contracts to reflect any changes in requirements or market conditions ensures ongoing alignment and reduces the risk of disputes.
Regular Performance Reviews
Regular performance reviews are critical in maintaining high standards and addressing any issues proactively.
Establishing key performance indicators (KPIs) and monitoring them systematically helps in ensuring that the OEM meets the agreed-upon standards.
Feedback loops and continuous improvement initiatives can further enhance the partnership’s effectiveness.
Leverage Technology
Utilizing technology can streamline the procurement and production process.
Implementing advanced supply chain management software, real-time monitoring systems, and communication platforms can enhance transparency and efficiency.
Japanese manufacturers are often equipped with state-of-the-art technology, so leveraging these resources can optimize the overall production process.
Conclusion
Blind OEM in Japanese manufacturing represents a powerful strategy for companies aiming to bring high-quality products to market efficiently and cost-effectively.
While there are inherent challenges, the advantages of quality assurance, access to advanced technology, cost efficiency, and flexibility make it an attractive option.
By understanding the nuances of supplier negotiation, staying attuned to market conditions, and adhering to best practices, businesses can successfully harness the potential of Japanese OEM partnerships.
Navigating this landscape requires diligence, strategic planning, and a commitment to building strong, collaborative relationships with Japanese manufacturers.
In doing so, companies can not only enjoy the benefits of Japanese manufacturing excellence but also gain a competitive edge in the global marketplace.
資料ダウンロード
QCD調達購買管理クラウド「newji」は、調達購買部門で必要なQCD管理全てを備えた、現場特化型兼クラウド型の今世紀最高の購買管理システムとなります。
ユーザー登録
調達購買業務の効率化だけでなく、システムを導入することで、コスト削減や製品・資材のステータス可視化のほか、属人化していた購買情報の共有化による内部不正防止や統制にも役立ちます。
NEWJI DX
製造業に特化したデジタルトランスフォーメーション(DX)の実現を目指す請負開発型のコンサルティングサービスです。AI、iPaaS、および先端の技術を駆使して、製造プロセスの効率化、業務効率化、チームワーク強化、コスト削減、品質向上を実現します。このサービスは、製造業の課題を深く理解し、それに対する最適なデジタルソリューションを提供することで、企業が持続的な成長とイノベーションを達成できるようサポートします。
オンライン講座
製造業、主に購買・調達部門にお勤めの方々に向けた情報を配信しております。
新任の方やベテランの方、管理職を対象とした幅広いコンテンツをご用意しております。
お問い合わせ
コストダウンが利益に直結する術だと理解していても、なかなか前に進めることができない状況。そんな時は、newjiのコストダウン自動化機能で大きく利益貢献しよう!
(Β版非公開)