- お役立ち記事
- Japanese Manufacturing’s Cutting-Edge Approach to Lightning Strike Information Technology
Japanese Manufacturing’s Cutting-Edge Approach to Lightning Strike Information Technology
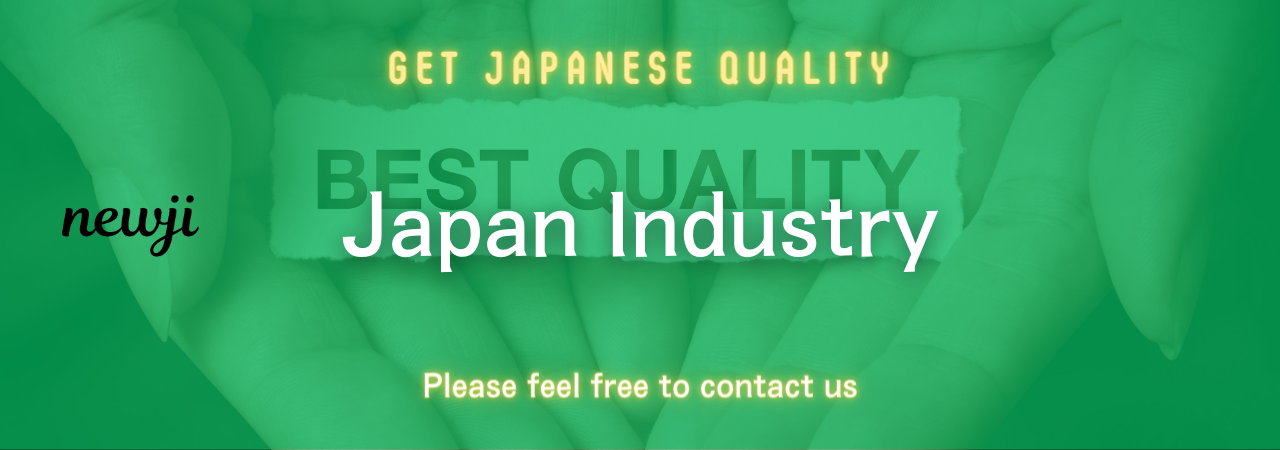
目次
Introduction to Japanese Manufacturing Excellence
Japan has long been recognized as a global leader in manufacturing, celebrated for its precision, quality, and innovation.
One of the most intriguing advancements in recent years has been the integration of cutting-edge lightning strike information technology (LSIT) within their production and manufacturing processes.
This technology is not only beneficial but is truly revolutionizing the way manufacturers approach safety, efficiency, and quality control.
This article aims to delve into the nuanced world of Japanese manufacturing, outlining the advantages and disadvantages of their approaches, the core elements of supplier negotiation, market conditions, and best practices that can be adopted globally.
The Advantages of Lightning Strike Information Technology in Manufacturing
Enhanced Safety Measures
Lightning strikes, though relatively rare, pose a significant risk to manufacturing operations, particularly those with extensive outdoor components or heavy electrical machinery.
LSIT is a proactive approach to minimize this risk by monitoring lightning activity, predicting potential strikes, and triggering safety protocols in real-time.
By integrating LSIT, Japanese manufacturers can effectively mitigate the risks to workers and equipment, ensuring a safer working environment.
Incorporating this technology aligns with Japan’s rigorous safety standards and cultural emphasis on meticulous planning.
Improved Production Efficiency
Another substantial advantage of LSIT is the enhancement of production efficiency.
By predicting lightning events, companies can preemptively adjust their operations to prevent downtime and damage to sensitive equipment.
For instance, operations involving critical machinery can be paused or adjusted to safeguard against potential disruptions.
Furthermore, LSIT allows for better planning and allocation of resources.
With accurate lightning strike data, manufacturers can avoid unscheduled downtimes, leading to higher overall productivity.
Superior Quality Control
Japan’s manufacturing sector is renowned for its high quality standards, and LSIT contributes significantly to maintaining these standards.
Lightning can cause electrical surges that lead to defects and inconsistencies in the production process.
By monitoring and predicting lightning activity, manufacturers can take preventative measures to ensure that the integrity of their products is maintained.
Additionally, integrating LSIT into the quality control process can help manufacturers maintain meticulous records of incidents and deviations.
This data can be invaluable for continuous improvement and certifying that quality standards are consistently met.
Reduction in Maintenance Costs
Reactive maintenance due to lightning strikes can be both costly and time-consuming.
LSIT enables predictive maintenance by providing early warnings of potential risks, allowing manufacturers to address issues before they escalate.
This reduces the frequency of sudden, catastrophic failures and helps in scheduling routine maintenance more effectively, ultimately leading to cost savings.
Disadvantages of LSIT in Manufacturing
Initial Investment and Implementation Costs
One of the primary disadvantages of LSIT is the significant initial investment required for implementation.
The technology involves sophisticated detection systems, data analysis software, and integration with existing operational procedures.
These costs can be a barrier, especially for smaller manufacturing companies operating on tight margins.
Moreover, implementing LSIT requires extensive training for personnel, further adding to the initial costs.
Companies must ensure that their staff are proficient in using the technology and interpreting the data it provides.
Complexity of Integration
Integrating LSIT into existing manufacturing processes can be complex.
The technology must seamlessly interface with other operational systems, such as production management software, safety protocols, and quality control measures.
This complexity can lead to potential disruptions during the integration phase, posing short-term challenges for manufacturers.
Additionally, companies may need to upgrade their existing infrastructure to accommodate the new technology, leading to further complications and expenses.
Data Management Challenges
LSIT generates vast amounts of data that must be accurately processed, analyzed, and stored.
Managing this data can be challenging, especially for manufacturers without robust data management systems in place.
Ensuring that the data is utilized effectively to drive decision-making processes is crucial but can also be resource-intensive.
Supplier Negotiation Techniques
Navigating relationships with suppliers is a critical aspect of the procurement and purchasing functions in manufacturing.
Japan’s emphasis on long-term, trust-based supplier relationships offers several unique negotiation techniques worth noting.
Emphasizing Quality and Reliability
Japanese suppliers are known for their commitment to quality and reliability.
During negotiations, it is essential to highlight these attributes.
Discussing the importance of consistent quality and punctual delivery times can strengthen trust and align the supplier’s objectives with your manufacturing needs.
Additionally, demonstrating a clear understanding of the supplier’s capabilities and limitations fosters respect and transparency, leading to more productive and amicable negotiations.
Building Long-Term Relationships
Unlike some Western business practices focusing on short-term gains, Japanese companies prioritize long-term relationships.
When negotiating with Japanese suppliers, it is beneficial to illustrate a long-term vision for the partnership.
Clarifying how both parties can grow and benefit over time creates a foundation of mutual trust and cooperation.
Focus on Continuous Improvement
Continuous improvement, or Kaizen, is a cornerstone of Japanese manufacturing philosophy.
Emphasize your commitment to Kaizen principles during negotiations.
Discuss opportunities for joint initiatives to enhance efficiency, reduce costs, and improve product quality.
Collaborative efforts towards continuous improvement can lead to innovative solutions and strengthen the relationship with your supplier.
Understanding Cultural Nuances
Cultural sensitivity is vitally important when negotiating with Japanese suppliers.
Understanding and respecting Japanese business etiquette, communication style, and decision-making processes can facilitate smoother negotiations.
For instance, Japanese business culture often values consensus and collective decision-making, so be prepared for discussions that involve multiple stakeholders.
Moreover, patience and humility are prized qualities in Japanese culture.
Approaching negotiations with these values in mind can lead to more favorable outcomes and foster stronger partnerships.
Market Conditions in Japanese Manufacturing
High Demand for Innovation
Japan’s manufacturing sector is characterized by high demand for innovation and technological advancements.
Adopting LSIT is a testament to this drive for continuous improvement.
Manufacturers keen to stay competitive must invest in cutting-edge technologies and maintain an active interest in emerging trends and innovations.
To thrive in this environment, companies should allocate resources towards research and development, and actively participate in industry forums and trade shows to stay abreast of market developments.
Stringent Quality Standards
The Japanese market maintains some of the strictest quality standards globally.
Manufacturers are held to rigorous benchmarks ensuring that products meet precise specifications and regulatory requirements.
Understanding these standards is crucial for any business operations in Japan.
It necessitates meticulous attention to detail in all aspects of production, from material sourcing to final product inspections.
Focus on Sustainability
There is an increasing focus on sustainability within the Japanese manufacturing sector.
Companies are investing in eco-friendly practices, aiming to reduce carbon footprints, and improve energy efficiency.
Consumers and regulatory bodies alike are pushing for greener manufacturing practices.
Adopt sustainable manufacturing practices to align with these market conditions.
This not only complies with regulations but also enhances brand image and appeal to environmentally conscious consumers.
Best Practices for Adopting LSIT
Comprehensive Training Programs
To successfully integrate LSIT into manufacturing operations, it is essential to have comprehensive training programs.
Ensure that employees at all levels are proficient in using the technology and understand its implications for safety, efficiency, and quality control.
Regular training updates and simulations can help keep staff prepared for any potential lightning-related events, enhancing overall readiness and responsiveness.
Collaborative Integration
Work closely with technology providers during the integration phase.
Collaborative efforts can help customize LSIT solutions tailored to your specific manufacturing needs.
Engage cross-functional teams, including IT, operations, and safety departments, to facilitate seamless integration.
Collaborative integration ensures that all stakeholders understand the technology’s benefits and limitations, fostering a unified approach to its implementation.
Effective Data Management Strategies
Implement robust data management strategies to handle the extensive data generated by LSIT.
Utilize advanced analytics tools to process and interpret data accurately, transforming raw information into actionable insights.
This approach aids in making informed decisions and maintaining optimal operational efficiency.
Investing in cybersecurity measures to protect sensitive data is also crucial, preventing potential breaches and ensuring data integrity.
Commitment to Continuous Improvement
Embrace a culture of continuous improvement by regularly reviewing and enhancing LSIT protocols.
Gather feedback from employees and stakeholders to identify areas for improvement and implement iterative changes.
Staying proactive and adaptive to evolving technological advancements can ensure that your LSIT capabilities remain cutting-edge.
Conclusion
The integration of lightning strike information technology into Japanese manufacturing exemplifies the country’s commitment to innovation, safety, and quality.
While there are challenges to overcome, the benefits of enhanced safety measures, improved production efficiency, superior quality control, and reduced maintenance costs make LSIT a valuable investment.
Practices such as focusing on quality and reliability, building long-term relationships, and understanding cultural nuances can significantly enhance supplier negotiations.
Moreover, adapting to stringent quality standards, a high demand for innovation, and growing sustainability focus are essential for thriving in the Japanese manufacturing market.
By adopting best practices in training, collaboration, data management, and continuous improvement, manufacturers can leverage LSIT to its full potential, ensuring they remain competitive and efficient in a rapidly evolving industry landscape.
In summary, Japanese manufacturing’s approach to LSIT offers valuable insights and practical applications that can benefit global manufacturers aiming to enhance their operations.
資料ダウンロード
QCD調達購買管理クラウド「newji」は、調達購買部門で必要なQCD管理全てを備えた、現場特化型兼クラウド型の今世紀最高の購買管理システムとなります。
ユーザー登録
調達購買業務の効率化だけでなく、システムを導入することで、コスト削減や製品・資材のステータス可視化のほか、属人化していた購買情報の共有化による内部不正防止や統制にも役立ちます。
NEWJI DX
製造業に特化したデジタルトランスフォーメーション(DX)の実現を目指す請負開発型のコンサルティングサービスです。AI、iPaaS、および先端の技術を駆使して、製造プロセスの効率化、業務効率化、チームワーク強化、コスト削減、品質向上を実現します。このサービスは、製造業の課題を深く理解し、それに対する最適なデジタルソリューションを提供することで、企業が持続的な成長とイノベーションを達成できるようサポートします。
オンライン講座
製造業、主に購買・調達部門にお勤めの方々に向けた情報を配信しております。
新任の方やベテランの方、管理職を対象とした幅広いコンテンツをご用意しております。
お問い合わせ
コストダウンが利益に直結する術だと理解していても、なかなか前に進めることができない状況。そんな時は、newjiのコストダウン自動化機能で大きく利益貢献しよう!
(Β版非公開)