- お役立ち記事
- Japanese Mastery in Manufacturing: Unleashing the Power of Beta Titanium Alloys
月間76,176名の
製造業ご担当者様が閲覧しています*
*2025年3月31日現在のGoogle Analyticsのデータより
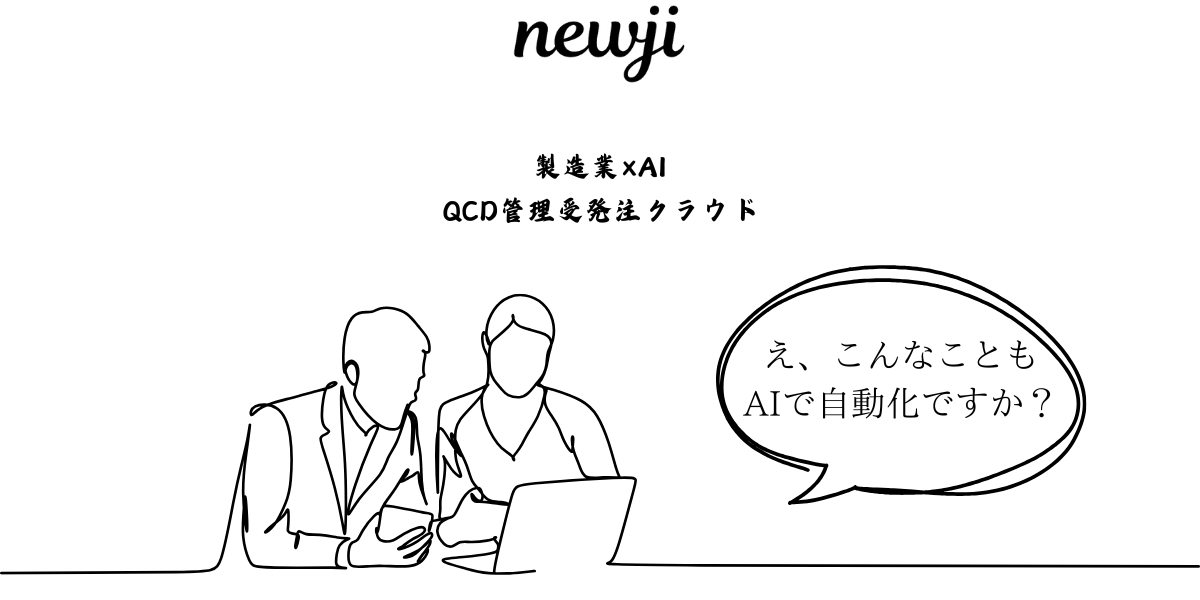
Japanese Mastery in Manufacturing: Unleashing the Power of Beta Titanium Alloys
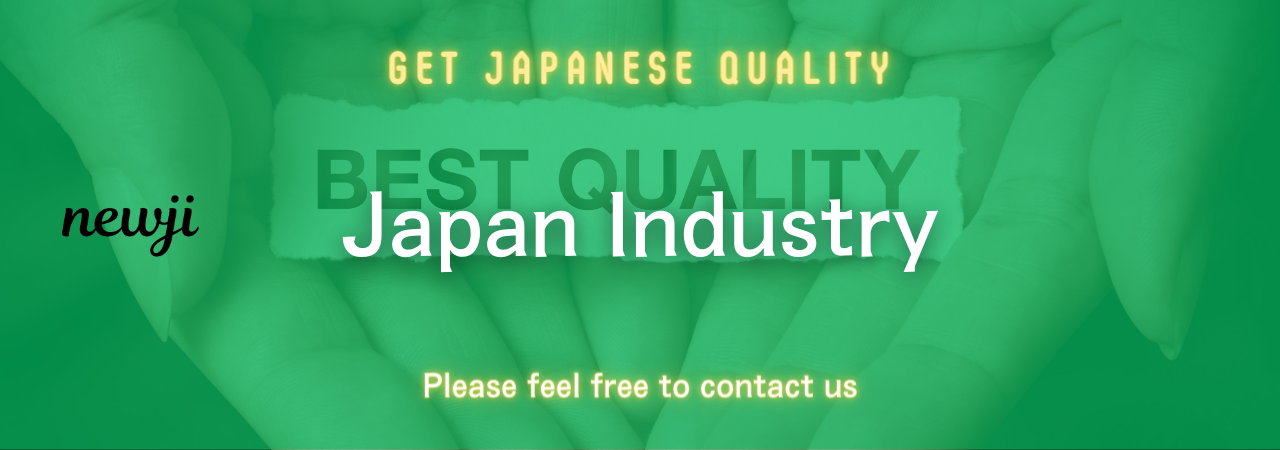
目次
Introduction to Beta Titanium Alloys in Japanese Manufacturing
Japan has long been recognized for its excellence in manufacturing, particularly in the development and utilization of advanced materials. Among these, beta titanium alloys stand out due to their unique properties and versatility. These alloys, known for their superior strength, corrosion resistance, and biocompatibility, have found applications across various industries, including aerospace, medical devices, and automotive sectors.
The Significance of Beta Titanium Alloys
Beta titanium alloys are a class of titanium alloys that contain a higher proportion of beta-phase stabilizing elements, such as vanadium, molybdenum, and niobium. This composition grants them enhanced mechanical properties compared to their alpha and near-alpha counterparts.
Advantages of Beta Titanium Alloys
Beta titanium alloys offer several advantages that make them highly sought after in manufacturing:
Their high strength-to-weight ratio allows for the production of lightweight yet robust components.
Excellent corrosion resistance ensures longevity and reliability in harsh environments.
Good formability and weldability facilitate manufacturing processes, enabling complex shapes and structures.
Biocompatibility makes them ideal for medical implants and devices.
Thermal stability allows for consistent performance under varying temperature conditions.
Disadvantages of Beta Titanium Alloys
Despite their numerous benefits, beta titanium alloys also present certain challenges:
Higher cost compared to other materials can impact project budgets.
Sensitivity to processing conditions requires precise manufacturing control.
Potential for reduced fatigue life if not properly treated or fabricated.
Japanese Mastery in Manufacturing Beta Titanium Alloys
Japan’s prowess in manufacturing beta titanium alloys stems from its commitment to quality, innovation, and efficiency. Japanese manufacturers have developed advanced techniques and processes that maximize the performance and reliability of these alloys.
Procurement and Purchasing Strategies
Effective procurement and purchasing are crucial in securing high-quality beta titanium alloys. Japanese companies employ strategic approaches to ensure they source the best materials at competitive prices.
Supplier Selection
Selecting the right suppliers is paramount. Japanese manufacturers prioritize suppliers with a proven track record of quality, reliability, and adherence to international standards. They often engage in long-term partnerships to foster collaboration and continuous improvement.
Supplier Negotiation Techniques
Japanese companies excel in negotiation techniques, focusing on creating mutually beneficial agreements. Key strategies include:
Building Trust: Establishing strong relationships based on trust and transparency.
Detailed Contracts: Ensuring all terms and conditions are clearly defined to avoid misunderstandings.
Win-Win Approach: Striving for agreements that benefit both parties, fostering long-term collaboration.
Flexibility: Being open to adjusting terms to accommodate supplier capabilities and market fluctuations.
Market Conditions and Trends
Understanding market conditions is essential for effective procurement. Japanese manufacturers stay ahead by monitoring global trends, technological advancements, and economic factors that influence the availability and cost of beta titanium alloys.
Global Demand
The demand for beta titanium alloys is increasing, driven by their application in high-performance industries. Japan’s ability to meet this demand is supported by its advanced manufacturing infrastructure and skilled workforce.
Technological Innovations
Continuous innovation in alloy composition and manufacturing processes enhances the performance of beta titanium alloys. Japanese manufacturers invest heavily in research and development to stay at the forefront of these advancements.
Economic Factors
Economic stability and favorable trade policies in Japan facilitate smooth procurement and purchasing processes. Manufacturers benefit from a robust economy that supports investment in high-quality materials and cutting-edge technologies.
Best Practices in Procuring Beta Titanium Alloys from Japan
Adopting best practices in procurement ensures that manufacturers can effectively leverage the advantages of Japanese beta titanium alloys while mitigating potential drawbacks.
Quality Assurance
Maintaining high-quality standards is non-negotiable. Japanese manufacturers implement rigorous quality control measures throughout the production process, from raw material selection to final product inspection.
Certification and Standards
Adhering to international certifications and standards, such as ISO 9001, ensures consistency and reliability in product quality. These certifications provide assurance to buyers about the integrity of the manufacturing process.
Inspection and Testing
Comprehensive inspection and testing protocols are in place to detect and address any defects or inconsistencies. Advanced testing methods, including non-destructive testing and material analysis, are employed to verify the properties of beta titanium alloys.
Supply Chain Management
Efficient supply chain management is critical in sourcing beta titanium alloys. Japanese manufacturers utilize sophisticated logistics and inventory management systems to ensure timely and cost-effective delivery.
Just-In-Time (JIT) Delivery
The JIT approach minimizes inventory costs and reduces waste by coordinating production schedules with supplier deliveries. This method enhances efficiency and responsiveness to market demands.
Inventory Optimization
Balancing inventory levels helps prevent shortages and overstocking. Advanced forecasting tools and data analytics are used to predict demand and optimize inventory accordingly.
Collaboration and Communication
Effective collaboration and communication between manufacturers and suppliers foster a productive partnership. Regular meetings, transparent information sharing, and collaborative problem-solving are key components.
Joint Development Initiatives
Collaborative development projects allow manufacturers and suppliers to innovate together, enhancing the quality and functionality of beta titanium alloys.
Feedback Mechanisms
Implementing feedback loops ensures continuous improvement. Manufacturers provide constructive feedback to suppliers, who in turn make necessary adjustments to meet evolving requirements.
Logistics and Production Management
Efficient logistics and production management are essential in maintaining the flow of materials and ensuring timely delivery of finished products.
Logistics Strategies
Japanese manufacturers employ advanced logistics strategies to streamline the transportation and distribution of beta titanium alloys.
Transportation Optimization
Optimizing transportation routes and methods reduces costs and improves delivery times. Utilizing a mix of air, sea, and land transport ensures flexibility and reliability.
Warehousing Solutions
State-of-the-art warehousing facilities equipped with modern tracking systems enhance inventory management and reduce lead times.
Production Efficiency
Maximizing production efficiency minimizes costs and enhances competitiveness. Japanese manufacturers leverage lean manufacturing principles and automation to achieve high levels of productivity.
Lean Manufacturing
Implementing lean principles eliminates waste and improves workflow. Continuous improvement practices foster a culture of efficiency and excellence.
Automation and Advanced Technologies
Integrating automation and robotics into the production process increases precision and reduces manual labor. Advanced technologies, such as computer-aided design and manufacturing (CAD/CAM), enhance design accuracy and production speed.
Quality Control and Assurance
Ensuring the quality of beta titanium alloys is paramount. Japanese manufacturers adhere to stringent quality control protocols to maintain high standards.
Quality Control Processes
Comprehensive quality control processes are embedded in every stage of production.
Raw Material Inspection
Inspecting raw materials upon arrival ensures that only high-quality inputs are used in manufacturing. This step prevents defects and inconsistencies in the final product.
In-Process Quality Checks
Regular quality checks during production identify and address issues promptly. This proactive approach minimizes defects and maintains product integrity.
Certification and Compliance
Meeting international certifications and compliance standards is essential for global market access.
ISO Certification
Achieving ISO certification demonstrates a commitment to quality management and assures customers of consistent product quality.
Regulatory Compliance
Adhering to regulatory requirements in various markets ensures that beta titanium alloys meet the necessary safety and performance standards.
Supplier Relationship Management
Building and maintaining strong relationships with suppliers is crucial for long-term success.
Building Trust and Reliability
Trust and reliability are the foundation of successful supplier relationships. Japanese manufacturers prioritize transparency, honesty, and mutual respect in their interactions.
Long-Term Partnerships
Fostering long-term partnerships with suppliers encourages collaboration and continuous improvement. These relationships enable manufacturers to secure preferential terms and prioritize supply during peak demand periods.
Performance Monitoring
Regularly monitoring supplier performance ensures that they meet quality, delivery, and cost expectations. Key performance indicators (KPIs) are used to evaluate and provide feedback.
Risk Management
Effective risk management strategies mitigate potential disruptions in the supply chain.
Diversification of Suppliers
Diversifying the supplier base reduces dependency on a single source and minimizes the impact of supply disruptions.
Contingency Planning
Developing contingency plans for potential risks, such as natural disasters or economic uncertainties, ensures resilience and continuity in procurement.
Economic and Environmental Considerations
Sustainable practices and economic efficiency are integral to modern manufacturing.
Economic Efficiency
Balancing cost and quality is essential for maintaining competitiveness. Japanese manufacturers optimize procurement and production processes to achieve cost savings without compromising on quality.
Cost Optimization
Identifying areas for cost reduction, such as negotiating better pricing with suppliers or improving production efficiency, enhances profitability.
Value Engineering
Value engineering involves analyzing products to improve function and reduce costs. This practice ensures that beta titanium alloys provide maximum value to end-users.
Environmental Sustainability
Sustainable manufacturing practices are increasingly important in today’s environmentally conscious market.
Eco-Friendly Production
Implementing eco-friendly production methods reduces the environmental impact of manufacturing beta titanium alloys. This includes minimizing waste, recycling materials, and reducing energy consumption.
Regulatory Compliance
Adhering to environmental regulations ensures that manufacturing processes are sustainable and compliant with local and international laws.
Technological Innovations in Beta Titanium Alloy Production
Continuous technological innovation drives the advancement and application of beta titanium alloys.
Advanced Alloy Composition
Research and development efforts focus on optimizing alloy compositions to enhance performance characteristics.
Alloying Elements
Incorporating various alloying elements allows for the customization of beta titanium alloys to meet specific application requirements.
Microstructural Control
Controlling the microstructure of the alloy enhances its mechanical properties and reliability.
Manufacturing Techniques
Innovative manufacturing techniques improve the efficiency and quality of beta titanium alloy production.
Additive Manufacturing
Additive manufacturing, or 3D printing, enables the production of complex and lightweight components with high precision.
Heat Treatment Processes
Advanced heat treatment processes optimize the mechanical properties of beta titanium alloys, enhancing their performance in demanding applications.
Case Studies: Success Stories in Japan
Examining successful implementations of beta titanium alloys in Japanese manufacturing provides valuable insights.
Aerospace Industry
Japanese aerospace manufacturers utilize beta titanium alloys in the production of aircraft components, enhancing performance and reliability.
Lightweight Structures
The use of beta titanium alloys allows for the creation of lightweight structures that improve fuel efficiency and reduce emissions.
High-Temperature Applications
Beta titanium alloys perform exceptionally well in high-temperature environments, making them ideal for critical aerospace components.
Medical Devices
The medical industry benefits from the biocompatibility and corrosion resistance of beta titanium alloys.
Implants and Prosthetics
Beta titanium alloys are used in the production of implants and prosthetics, offering superior integration with human tissue and long-term durability.
Surgical Instruments
The corrosion resistance of beta titanium alloys ensures that surgical instruments remain reliable and sterile over extended use.
Future Outlook and Opportunities
The future of beta titanium alloys in Japanese manufacturing looks promising, with numerous opportunities for growth and innovation.
Emerging Applications
New applications for beta titanium alloys continue to emerge, driven by advancements in technology and changing market demands.
Renewable Energy
Beta titanium alloys are being explored for use in renewable energy systems, such as wind turbines and solar panels, due to their durability and lightweight properties.
Electric Vehicles
The automotive industry’s shift towards electric vehicles presents opportunities for beta titanium alloys in battery components and structural parts.
Research and Development
Ongoing research and development efforts aim to further enhance the properties and applications of beta titanium alloys.
Nanotechnology
Integrating nanotechnology with beta titanium alloys can lead to the development of materials with unprecedented strength and functionality.
Smart Materials
The creation of smart beta titanium alloys that can adapt to environmental changes holds potential for advanced manufacturing applications.
Conclusion
Japan’s mastery in manufacturing beta titanium alloys is a testament to its dedication to quality, innovation, and efficiency. Through strategic procurement and purchasing practices, robust supplier relationships, and a focus on technological advancements, Japanese manufacturers continue to lead the way in harnessing the power of beta titanium alloys. As industries evolve and new applications emerge, the expertise and commitment of Japanese manufacturers ensure that beta titanium alloys will remain a cornerstone of advanced manufacturing solutions worldwide.
資料ダウンロード
QCD管理受発注クラウド「newji」は、受発注部門で必要なQCD管理全てを備えた、現場特化型兼クラウド型の今世紀最高の受発注管理システムとなります。
ユーザー登録
受発注業務の効率化だけでなく、システムを導入することで、コスト削減や製品・資材のステータス可視化のほか、属人化していた受発注情報の共有化による内部不正防止や統制にも役立ちます。
NEWJI DX
製造業に特化したデジタルトランスフォーメーション(DX)の実現を目指す請負開発型のコンサルティングサービスです。AI、iPaaS、および先端の技術を駆使して、製造プロセスの効率化、業務効率化、チームワーク強化、コスト削減、品質向上を実現します。このサービスは、製造業の課題を深く理解し、それに対する最適なデジタルソリューションを提供することで、企業が持続的な成長とイノベーションを達成できるようサポートします。
製造業ニュース解説
製造業、主に購買・調達部門にお勤めの方々に向けた情報を配信しております。
新任の方やベテランの方、管理職を対象とした幅広いコンテンツをご用意しております。
お問い合わせ
コストダウンが利益に直結する術だと理解していても、なかなか前に進めることができない状況。そんな時は、newjiのコストダウン自動化機能で大きく利益貢献しよう!
(β版非公開)