- お役立ち記事
- Joint development methods and partner selection for products that utilize mesh integrated molding technology
月間77,185名の
製造業ご担当者様が閲覧しています*
*2025年2月28日現在のGoogle Analyticsのデータより
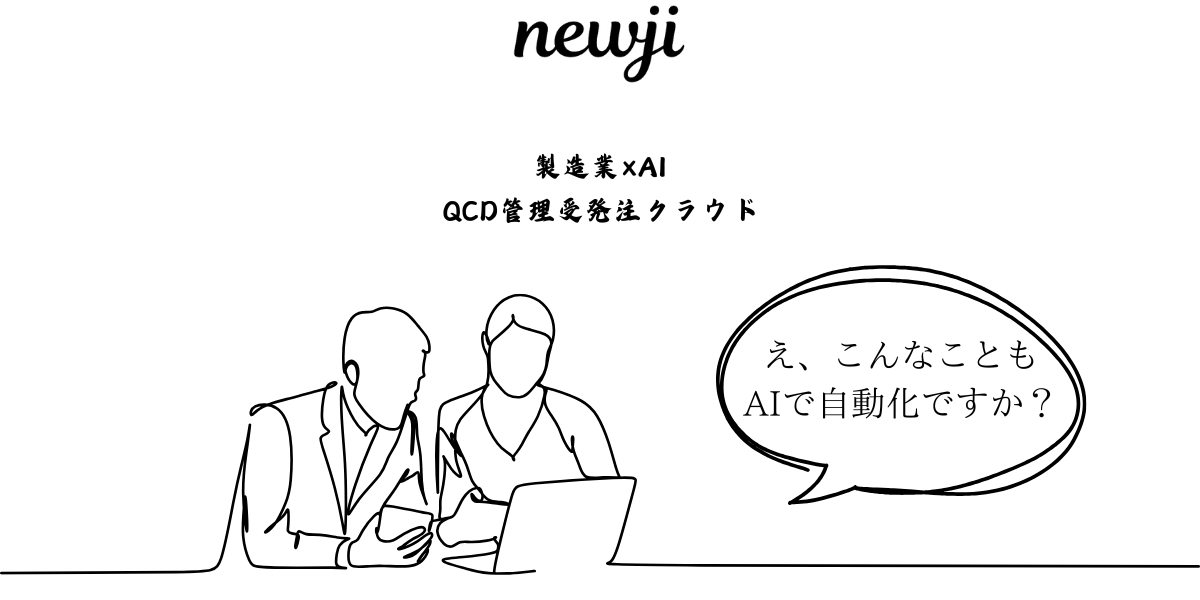
Joint development methods and partner selection for products that utilize mesh integrated molding technology
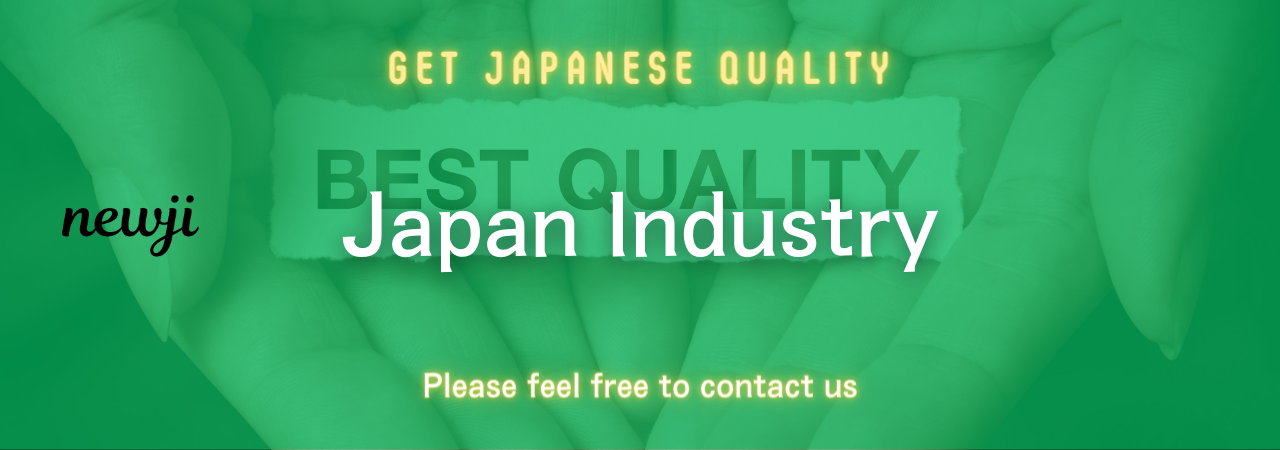
目次
Introduction to Mesh Integrated Molding Technology
Mesh integrated molding technology is a revolutionary process that combines different materials, typically plastics and metal meshes, to create products with enhanced functionality and durability.
This technology is increasingly being adopted across various industries due to its ability to produce lightweight and strong products.
The integration of mesh into the molding process allows for improved structural integrity and offers a unique solution for making hybrid components that are more efficient and cost-effective than traditional manufacturing methods.
Understanding the Joint Development Process
The development of products using mesh integrated molding technology often requires collaboration between different entities.
This joint development process ensures that all necessary expertise and resources are pooled together to achieve the desired outcome efficiently.
The process typically includes several crucial steps, each involving specific tasks and collaborations.
Identify Product Requirements
At the beginning of the joint development process, it is vital to clearly define the product requirements.
This involves determining the desired functionalities, strength, flexibility, and other characteristics of the final product.
Collaboration between engineers, designers, and product managers is essential at this stage to ensure that everyone has a clear understanding of the product’s goals and limitations.
Selecting the Right Materials
One of the key aspects of mesh integrated molding technology is the selection of appropriate materials.
The choice of plastic and metal mesh combinations will directly impact the quality and performance of the final product.
Material scientists and engineers should work closely to test various combinations and select the best materials that meet the product requirements.
Design and Prototyping
Once the materials are selected, the next stage is designing and prototyping the product.
Advanced computer-aided design (CAD) tools are typically used to create detailed models of the product.
Engineers and designers collaborate to refine the design and prepare it for prototyping.
Rapid prototyping techniques, such as 3D printing, are often employed to create physical models quickly, allowing for testing and further refinement before mass production.
Partner Selection for Joint Development
Choosing the right partners for joint development is a critical component of a successful collaboration.
The right partners bring valuable expertise, skills, and resources that can significantly enhance the development process.
Identify Potential Partners
The first step in partner selection is identifying potential partners with the necessary expertise and capabilities.
This might include companies with specialized knowledge in mesh integrated molding technology, material suppliers, or research institutions.
Industry directories and networking events can be excellent resources for identifying potential partners.
Evaluate Expertise and Capabilities
After identifying potential partners, it is essential to evaluate their expertise and capabilities.
This evaluation should include a review of their past projects, technological capabilities, and experience in working with similar technologies.
References from previous collaborations can also provide insights into their track record and reliability.
Assess Compatibility
Compatibility is another crucial factor to consider when selecting partners.
Partners should share similar values and have compatible working cultures to ensure smooth collaboration.
Aligning goals and expectations from the outset can prevent conflicts and misunderstandings later in the process.
Negotiate Agreements
Once the potential partners have been evaluated and selected, the next step is negotiating agreements.
These agreements should define the roles, responsibilities, and expectations of each partner.
Legal contracts should also specify intellectual property rights, confidentiality agreements, and terms for collaboration termination if necessary.
Having a clear agreement in place helps to protect the interests of all parties involved and provides a framework for a successful collaboration.
Challenges and Solutions in Joint Development
Joint development of products utilizing mesh integrated molding technology comes with its own set of challenges.
However, these challenges can be managed effectively with the right strategies.
Communication Barriers
Communication barriers can arise when collaborating with partners from different regions or industries.
Establishing clear communication channels and regular meetings can help overcome language barriers and ensure that all partners are on the same page.
Utilizing digital collaboration tools can also facilitate better communication among team members.
Intellectual Property Concerns
Intellectual property (IP) disputes can hinder the development process.
To avoid such issues, it is crucial to have well-drafted IP agreements in place from the beginning of the collaboration.
Engaging legal experts with experience in joint development agreements can help protect each partner’s intellectual property rights.
Technical Challenges
Technical challenges related to mesh integration and material compatibility can impact the development process.
Continuous research and development, as well as rigorous testing, can help identify and address these technical hurdles early on.
Leveraging the expertise of experienced engineers and scientists can also lead to innovative solutions that overcome these challenges.
Conclusion
Mesh integrated molding technology offers exciting opportunities for developing innovative products that are both lightweight and strong.
Joint development methods and careful partner selection play a crucial role in harnessing the full potential of this technology.
By establishing clear communication, evaluating potential partners, and addressing challenges proactively, companies can successfully develop products that meet market needs and push the boundaries of design and performance.
As mesh integrated molding technology continues to evolve, collaborative efforts will be fundamental in driving its advancement and application across various industries.
資料ダウンロード
QCD管理受発注クラウド「newji」は、受発注部門で必要なQCD管理全てを備えた、現場特化型兼クラウド型の今世紀最高の受発注管理システムとなります。
ユーザー登録
受発注業務の効率化だけでなく、システムを導入することで、コスト削減や製品・資材のステータス可視化のほか、属人化していた受発注情報の共有化による内部不正防止や統制にも役立ちます。
NEWJI DX
製造業に特化したデジタルトランスフォーメーション(DX)の実現を目指す請負開発型のコンサルティングサービスです。AI、iPaaS、および先端の技術を駆使して、製造プロセスの効率化、業務効率化、チームワーク強化、コスト削減、品質向上を実現します。このサービスは、製造業の課題を深く理解し、それに対する最適なデジタルソリューションを提供することで、企業が持続的な成長とイノベーションを達成できるようサポートします。
製造業ニュース解説
製造業、主に購買・調達部門にお勤めの方々に向けた情報を配信しております。
新任の方やベテランの方、管理職を対象とした幅広いコンテンツをご用意しております。
お問い合わせ
コストダウンが利益に直結する術だと理解していても、なかなか前に進めることができない状況。そんな時は、newjiのコストダウン自動化機能で大きく利益貢献しよう!
(β版非公開)