- お役立ち記事
- “Kaizen activities” led by managers—the effects expected by management and how to disseminate them to the workplace
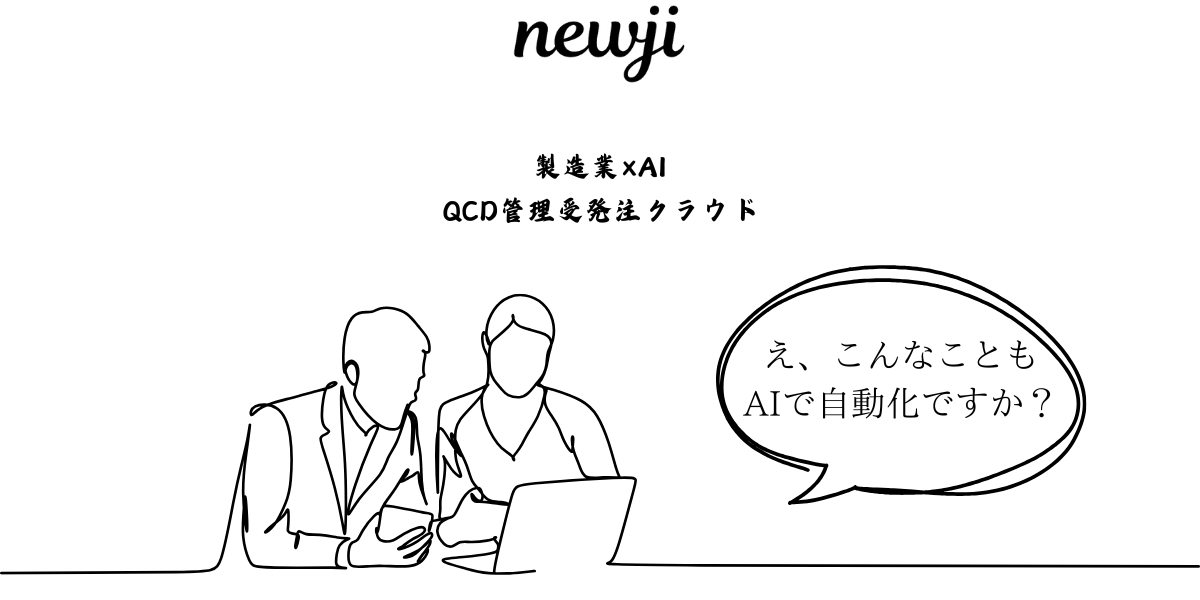
“Kaizen activities” led by managers—the effects expected by management and how to disseminate them to the workplace
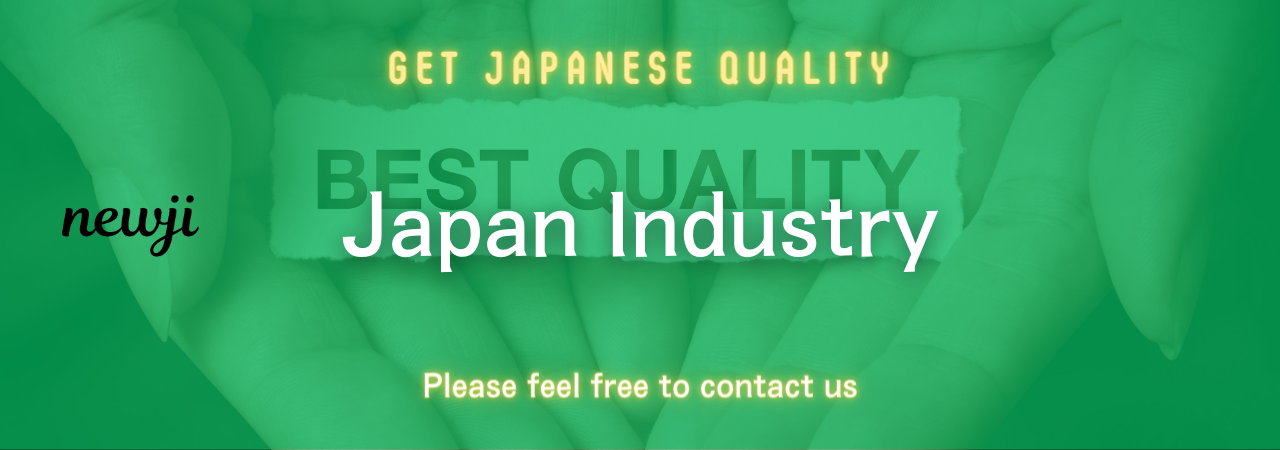
目次
Understanding Kaizen Activities and Their Importance
Kaizen is a Japanese term that translates to “continuous improvement” in English.
It is a philosophy that encourages all members of an organization to work together to achieve regular, incremental improvements to the manufacturing process.
These improvements aim to enhance quality, productivity, safety, and efficiency.
Kaizen activities are not just about making changes.
They are about creating an environment where employees are continuously involved in suggesting and implementing positive changes.
This philosophy encourages creativity, fosters teamwork, and, most importantly, leads to substantial improvements over time.
The Role of Managers in Kaizen Activities
Managers play a critical role in facilitating and supporting Kaizen activities within an organization.
They serve as the bridge between the strategic objectives of the company and the implementation of Kaizen at the grassroots level.
By demonstrating commitment and leadership, managers can motivate and engage employees in the continuous improvement process.
Effective managers encourage open communication, allowing employees to express their ideas freely.
They also provide the necessary resources and training to implement these improvements.
By actively participating in Kaizen activities, managers can lead by example and reinforce the importance of these activities to the workforce.
Effects Expected by Management from Kaizen Activities
Management can expect several positive outcomes from well-implemented Kaizen activities.
Firstly, it leads to increased productivity due to streamlined processes and reduced waste.
By continuously improving operational procedures, organizations can achieve higher output with the same resources.
Secondly, Kaizen can improve product quality by identifying and eliminating defects or inefficiencies in the production process.
This leads to higher customer satisfaction and can be reflected in increased sales and market share.
Moreover, engaging employees in Kaizen activities can boost morale and job satisfaction.
When employees see their ideas being valued and implemented, they feel more connected to the organization and motivated to contribute further.
Additionally, Kaizen activities can enhance workplace safety by constantly reviewing and improving safety protocols.
A safer work environment reduces the number of accidents and associated costs.
How to Disseminate Kaizen to the Workplace
To successfully implement Kaizen activities in the workplace, management should focus on fostering a culture that embraces change and continuous improvement.
This begins with strong communication of the Kaizen philosophy.
Management should communicate the importance of Kaizen and how it aligns with the organization’s goals.
Training sessions and workshops can be organized to educate employees about Kaizen principles and techniques.
Such sessions should aim to increase awareness and build the skills needed to identify and implement improvement opportunities.
Creating cross-functional Kaizen teams is another effective way to disseminate Kaizen.
These teams consist of members from different departments who can bring diverse perspectives and insights to problem-solving.
This collaboration encourages innovation and helps identify improvements that might not be apparent to individuals working in isolation.
Recognition and rewards can help reinforce a culture of continuous improvement.
Acknowledging the contributions of employees to Kaizen activities can motivate others to participate and share their ideas.
Encouraging Employee Participation
To ensure widespread adoption, it is crucial to encourage employee participation in Kaizen activities.
This can be achieved by making the process inclusive and empowering employees at all levels to contribute.
Management should establish a system for collecting and evaluating ideas from employees.
Regular feedback loops can help track the progress of implemented improvements and recognize successful initiatives.
Hosting regular meetings to discuss ongoing Kaizen activities can keep everyone informed and engaged.
This also provides a platform for sharing success stories and learning from challenges encountered in previous initiatives.
Overcoming Resistance to Change
Change can often be met with resistance, especially in long-established processes.
To overcome this, it is important for management to communicate the benefits of Kaizen clearly and consistently.
Employees need to understand how these activities lead to better outcomes for the organization and themselves.
Involving employees early in the decision-making process can also reduce resistance.
When employees feel they have a stake in the changes being implemented, they are more likely to support and contribute to them.
Addressing concerns and providing support during the transition phase is crucial.
Managers should be approachable and ready to assist employees who may have difficulties adapting to new procedures.
Sustaining Kaizen Activities for Long-Term Success
For Kaizen to yield long-term benefits, it should not be treated as a one-time project but rather as an ongoing endeavor.
Building a strong Kaizen culture within the organization ensures that continuous improvement becomes a core value.
Regular reviews of Kaizen activities can help assess their impact and identify areas for further improvement.
Celebrating successes and learning from failures are important parts of the process.
Emphasizing the importance of Kaizen in strategic planning and aligning it with the overall vision of the organization can ensure its sustainability.
Management must remain committed to providing the resources and support necessary for Kaizen activities to thrive.
In conclusion, Kaizen activities led by managers are a powerful tool for driving continuous improvement and achieving organizational goals.
With the right approach and commitment, these activities can lead to substantial benefits for the organization, its employees, and its customers.
資料ダウンロード
QCD調達購買管理クラウド「newji」は、調達購買部門で必要なQCD管理全てを備えた、現場特化型兼クラウド型の今世紀最高の購買管理システムとなります。
ユーザー登録
調達購買業務の効率化だけでなく、システムを導入することで、コスト削減や製品・資材のステータス可視化のほか、属人化していた購買情報の共有化による内部不正防止や統制にも役立ちます。
NEWJI DX
製造業に特化したデジタルトランスフォーメーション(DX)の実現を目指す請負開発型のコンサルティングサービスです。AI、iPaaS、および先端の技術を駆使して、製造プロセスの効率化、業務効率化、チームワーク強化、コスト削減、品質向上を実現します。このサービスは、製造業の課題を深く理解し、それに対する最適なデジタルソリューションを提供することで、企業が持続的な成長とイノベーションを達成できるようサポートします。
オンライン講座
製造業、主に購買・調達部門にお勤めの方々に向けた情報を配信しております。
新任の方やベテランの方、管理職を対象とした幅広いコンテンツをご用意しております。
お問い合わせ
コストダウンが利益に直結する術だと理解していても、なかなか前に進めることができない状況。そんな時は、newjiのコストダウン自動化機能で大きく利益貢献しよう!
(Β版非公開)