- お役立ち記事
- Kaizen Activities to Reduce Structural Waste and Create Profitable Factories
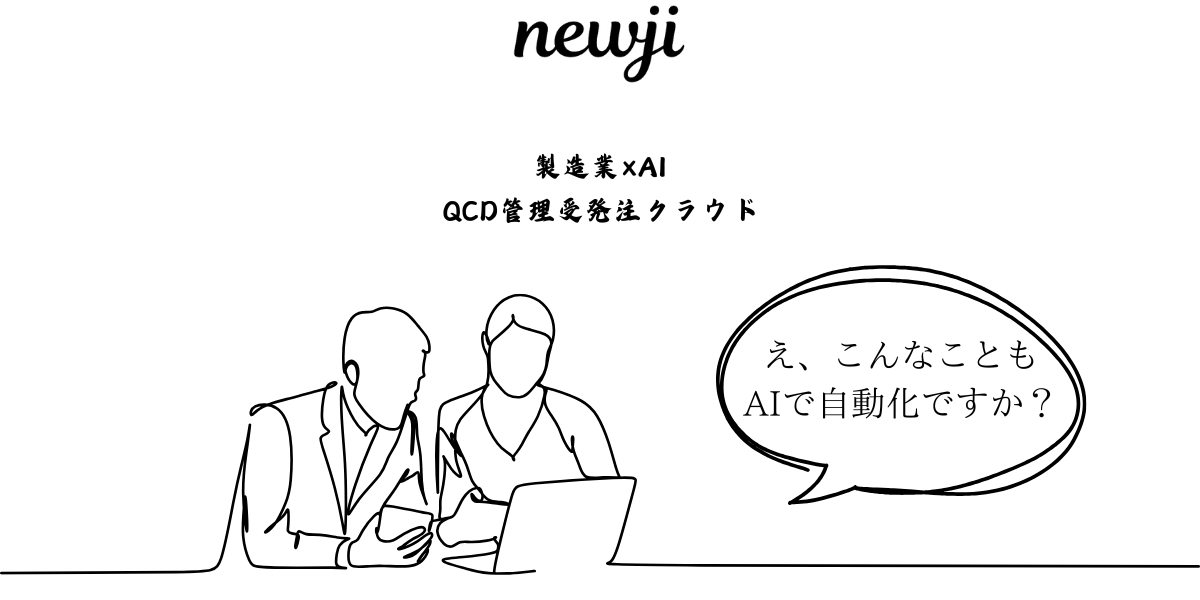
Kaizen Activities to Reduce Structural Waste and Create Profitable Factories
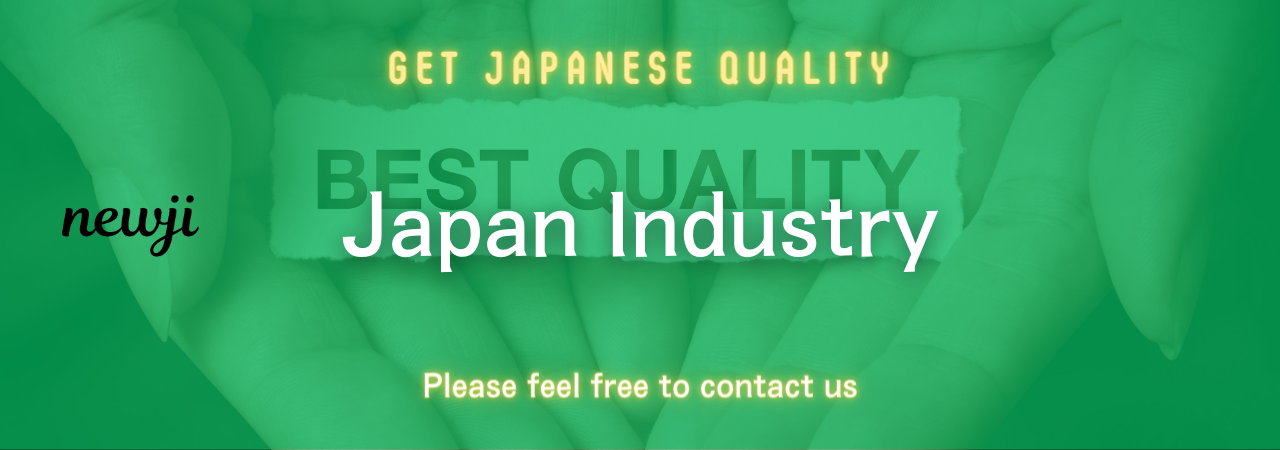
Kaizen is a Japanese philosophy that focuses on continuous improvement. It is widely used in manufacturing and has been proven effective in reducing waste and enhancing productivity. This approach can transform a factory into a more efficient and profitable enterprise. In this article, we’ll explore how Kaizen activities can help in reducing structural waste and create profitable factories.
目次
What is Kaizen?
Kaizen means “change for better” in Japanese. It involves everyone in the organization, from top management to workers, in the continuous effort to improve processes, reduce waste, and enhance efficiency. Unlike other methodologies, Kaizen is an ongoing, incremental approach rather than a one-time effort.
Key Principles of Kaizen
Several core principles underpin Kaizen:
1. **Continuous Improvement**: Improvement is a never-ending process.
2. **Employee Involvement**: Encourage employees at all levels to contribute ideas for improvement.
3. **Quality Control**: Prioritize quality to reduce errors and rework.
4. **Standardized Work**: Create and maintain standardized processes.
5. **Customer Focus**: Always aim to meet or exceed customer expectations.
Understanding Structural Waste
Structural waste refers to inefficiencies built into the system or processes within a factory. This could include poor layout designs, outdated machinery, excessive movement, and ineffective communication channels. Identifying and eliminating these wastes is crucial for creating a more profitable factory.
Types of Structural Waste
There are several types of structural waste that Kaizen activities target:
1. **Overproduction**: Producing more than what is needed or before it is needed.
2. **Waiting Time**: Idle time due to machine downtimes or waiting for materials.
3. **Transport**: Unnecessary movement of products or materials.
4. **Overprocessing**: Doing more work than necessary.
5. **Inventory**: Excess stock that ties up capital and storage.
Kaizen Activities to Reduce Structural Waste
Here are several Kaizen activities that can help reduce structural waste in a manufacturing environment:
Value Stream Mapping
Value Stream Mapping (VSM) is a visualization tool used to analyze and design the flow of materials and information required to bring a product to the customer. By mapping the current state and designing a future state, companies can identify and eliminate waste.
5S Methodology
The 5S Methodology is a systematic approach to workplace organization:
1. **Sort**: Remove unnecessary items from the workplace.
2. **Set in Order**: Arrange items in an orderly manner.
3. **Shine**: Clean the work area.
4. **Standardize**: Establish standards for cleanliness and organization.
5. **Sustain**: Maintain and review standards.
Kanban System
The Kanban system is a scheduling method that uses visual signals to control the flow of materials within a factory. It ensures that inventory levels are kept at an optimum level, reducing waste from overproduction and excess inventory.
Kaizen Events
Kaizen events, also known as “Kaizen Blitz,” are short-term events focused on achieving rapid improvements. They bring together a cross-functional team to identify waste, brainstorm solutions, and implement changes within a short period, usually lasting from a few days to a week.
Standardized Work
Creating standardized work involves documenting the current best practices for a particular process. This ensures that every worker performs tasks in the most efficient way, reducing variations and waste caused by different methods.
Benefits of Reducing Structural Waste
Reducing structural waste through Kaizen activities has several benefits:
Increased Productivity
By eliminating inefficiencies, factories can produce more with the same resources, increasing overall productivity.
Cost Savings
Reduction in waste leads directly to cost savings. Lower inventory levels mean less capital tied up, and streamlined processes reduce labor costs and increase output efficiency.
Improved Quality
Standardized work and continuous improvement lead to higher quality products with fewer defects, enhancing customer satisfaction.
Employee Engagement
Involving employees in Kaizen activities fosters a culture of continuous improvement and makes workers feel valued and engaged. Engaged employees are more productive and committed to the organization’s goals.
Better Space Utilization
Reducing waste often involves reorganizing the workspace, leading to better space utilization. Optimized layouts can reduce unnecessary movement and make the workflow more efficient.
Implementing Kaizen in Your Factory
To start implementing Kaizen in your factory, follow these steps:
Form a Kaizen Team
Develop a cross-functional team that can bring diverse perspectives to the table. This should include employees from different departments and levels within the organization.
Conduct Training
Educate your team on Kaizen principles and tools such as Value Stream Mapping, 5S, and the Kanban system. Use workshops and hands-on practice to reinforce learning.
Identify Areas for Improvement
Use tools like VSM to identify areas with significant structural waste. Prioritize these areas for improvement activities.
Set Goals and Metrics
Establish clear goals and metrics to measure the success of your Kaizen activities. This could include reducing cycle time, increasing output, or lowering defect rates.
Implement Changes
Carry out the planned changes using the Kaizen team. Focus on small, incremental improvements that can be easily monitored and adjusted.
Review and Adjust
Regularly review the results of your Kaizen activities. Use metrics to evaluate success and adjust strategies as needed. Continuous feedback loops are crucial for sustained improvement.
Implementing Kaizen activities is a proven approach to reduce structural waste and create more profitable factories. By fostering a culture of continuous improvement and focusing on eliminating inefficiencies, businesses can achieve significant gains in productivity, cost savings, quality, and employee engagement. Start small, involve everyone, and continuously strive for better. With commitment and persistence, the transformative power of Kaizen can turn any factory into a highly profitable and efficient operation.
資料ダウンロード
QCD調達購買管理クラウド「newji」は、調達購買部門で必要なQCD管理全てを備えた、現場特化型兼クラウド型の今世紀最高の購買管理システムとなります。
ユーザー登録
調達購買業務の効率化だけでなく、システムを導入することで、コスト削減や製品・資材のステータス可視化のほか、属人化していた購買情報の共有化による内部不正防止や統制にも役立ちます。
NEWJI DX
製造業に特化したデジタルトランスフォーメーション(DX)の実現を目指す請負開発型のコンサルティングサービスです。AI、iPaaS、および先端の技術を駆使して、製造プロセスの効率化、業務効率化、チームワーク強化、コスト削減、品質向上を実現します。このサービスは、製造業の課題を深く理解し、それに対する最適なデジタルソリューションを提供することで、企業が持続的な成長とイノベーションを達成できるようサポートします。
オンライン講座
製造業、主に購買・調達部門にお勤めの方々に向けた情報を配信しております。
新任の方やベテランの方、管理職を対象とした幅広いコンテンツをご用意しております。
お問い合わせ
コストダウンが利益に直結する術だと理解していても、なかなか前に進めることができない状況。そんな時は、newjiのコストダウン自動化機能で大きく利益貢献しよう!
(Β版非公開)