- お役立ち記事
- Key Considerations for Procurement Departments When Upgrading Manufacturing Equipment
月間76,176名の
製造業ご担当者様が閲覧しています*
*2025年3月31日現在のGoogle Analyticsのデータより
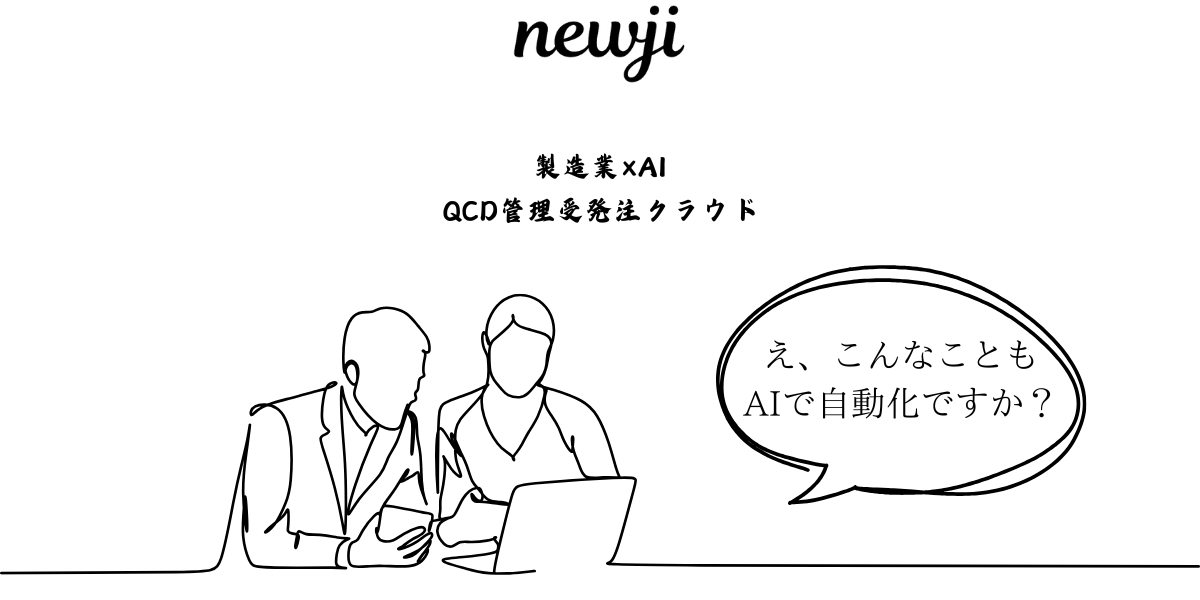
Key Considerations for Procurement Departments When Upgrading Manufacturing Equipment
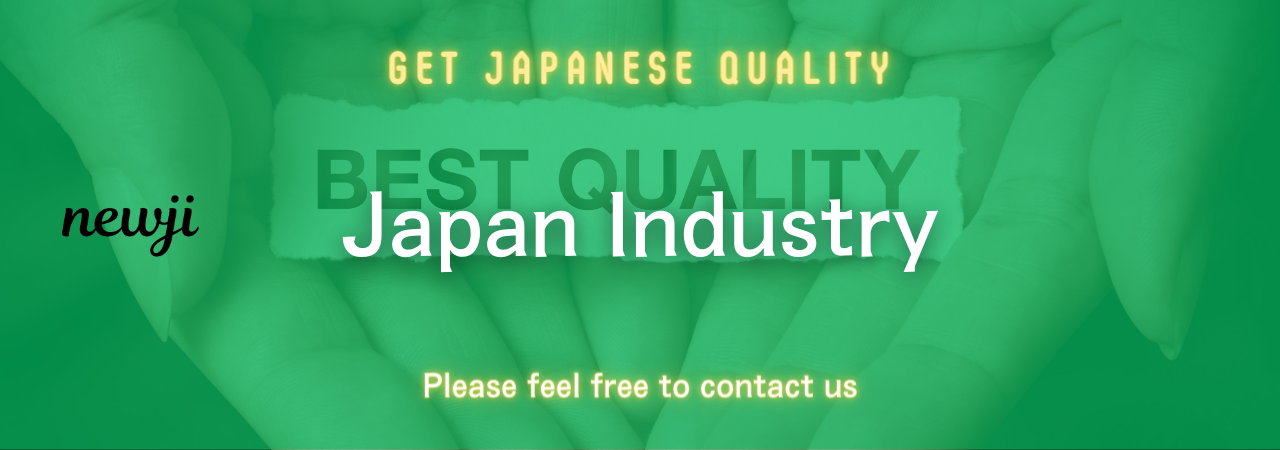
Upgrading manufacturing equipment can be a significant step for any business looking to improve efficiency, productivity, and profitability.
However, the process isn’t as simple as choosing the latest model and making a purchase.
There are several key considerations that procurement departments must take into account to ensure a successful upgrade process.
目次
Understand Business Needs
The first and foremost consideration is to clearly understand your business needs.
Identify the goals you want to achieve with the new equipment.
Are you aiming for increased production speed, improved quality, or reduced operational costs?
Understanding these objectives will guide your procurement process and help you select the equipment that best meets your requirements.
Budget Planning
Upgrading manufacturing equipment is often a significant financial investment.
It is crucial to set a realistic budget and stick to it.
Consider all associated costs, including installation, training, and maintenance.
Budget planning should also include potential downtime during the installation phase.
Proper financial planning ensures that the project remains viable and does not strain the company’s financial resources.
Research and Comparison
Research is a critical step in the procurement process.
Look at various manufacturers and models to compare their features, benefits, and costs.
Seek out reviews and case studies to understand how the equipment has performed in similar settings.
This comparative analysis enables you to make an informed decision based on facts rather than assumptions.
Supplier Reliability
The reliability of the supplier is another critical consideration.
Choose suppliers with a proven track record of delivering high-quality equipment and excellent customer service.
Check their credentials, customer reviews, and after-sale support services.
Reliable suppliers minimize the risk of encountering issues during and after the purchase.
Energy Efficiency
In today’s environmentally conscious world, energy efficiency is an important factor.
Energy-efficient equipment often has lower operational costs and may qualify for government incentives or grants.
Evaluate the energy consumption of the equipment and consider long-term savings in your procurement decision.
Choosing energy-efficient machinery can reduce your company’s carbon footprint and contribute to sustainability goals.
Compatibility with Existing Systems
New manufacturing equipment should be compatible with your existing systems and processes.
Assess the current infrastructure to ensure that the new equipment can be integrated seamlessly.
Compatibility issues can lead to increased downtime and additional costs for modifications.
Conducting a thorough compatibility check will save time and resources in the long run.
Training and Support
New equipment often requires specialized knowledge and skills to operate efficiently.
Ensure that the supplier provides adequate training for your staff.
Inquire about the availability of training programs and support services.
Proper training minimizes the learning curve and helps maximize the productivity of the new equipment.
Regulatory Compliance and Safety
Manufacturing equipment must comply with industry regulations and safety standards.
Non-compliance can lead to legal issues and hefty fines.
Verify that the new equipment meets all regulatory requirements.
Additionally, ensure that it incorporates modern safety features to protect your workforce and reduce accidents.
Maintenance and Spare Parts
Maintenance is essential to keep the new equipment running smoothly.
Investigate the maintenance requirements and the availability of spare parts.
Choose equipment that is known for its durability and ease of maintenance.
Reliable access to spare parts ensures that you can quickly address any issues, minimizing downtime.
Future Scalability
Consider the future growth and scalability of your operations when selecting new equipment.
Opt for machinery that can adapt to increasing production demands or technological advancements.
Scalability ensures that the equipment remains relevant and cost-effective over a longer period.
Total Cost of Ownership
The initial purchase price is only a portion of the total cost.
Consider the total cost of ownership (TCO), which includes installation, operation, maintenance, and disposal costs.
A lower upfront cost may result in higher long-term expenses.
Conducting a comprehensive TCO analysis provides a clearer picture of the equipment’s financial impact.
Implementation Timeline
Develop a detailed implementation plan that outlines the timeline for the upgrade.
Coordinate with various departments to minimize disruptions to production.
A well-structured implementation plan helps ensure a smooth transition and reduces downtime.
Vendor Agreements and Warranties
Carefully review vendor agreements and warranties before finalizing the purchase.
Ensure that the terms and conditions are favorable and provide adequate protection.
A strong warranty can offer peace of mind and financial protection against unexpected issues.
Environmental Impact
Consider the environmental impact of the new equipment.
Assess factors like emissions, waste production, and resource consumption.
Environmentally-friendly equipment aligns with corporate social responsibility goals and may enhance your brand’s reputation.
Feedback from Operators
Involve the operators who will be using the new equipment in the decision-making process.
Their feedback can provide valuable insights into the practical aspects of the equipment.
Operators can highlight potential challenges and suggest features that would enhance efficiency.
Customized Solutions
Sometimes, standard equipment may not meet your specific needs.
Explore the possibility of customized solutions that are tailored to your unique requirements.
Custom equipment can offer a better fit and improved performance.
Making the right decisions when upgrading manufacturing equipment is crucial for the success of your operations.
By considering these key factors, procurement departments can make informed choices that align with business objectives, enhance efficiency, and provide long-term value.
資料ダウンロード
QCD管理受発注クラウド「newji」は、受発注部門で必要なQCD管理全てを備えた、現場特化型兼クラウド型の今世紀最高の受発注管理システムとなります。
ユーザー登録
受発注業務の効率化だけでなく、システムを導入することで、コスト削減や製品・資材のステータス可視化のほか、属人化していた受発注情報の共有化による内部不正防止や統制にも役立ちます。
NEWJI DX
製造業に特化したデジタルトランスフォーメーション(DX)の実現を目指す請負開発型のコンサルティングサービスです。AI、iPaaS、および先端の技術を駆使して、製造プロセスの効率化、業務効率化、チームワーク強化、コスト削減、品質向上を実現します。このサービスは、製造業の課題を深く理解し、それに対する最適なデジタルソリューションを提供することで、企業が持続的な成長とイノベーションを達成できるようサポートします。
製造業ニュース解説
製造業、主に購買・調達部門にお勤めの方々に向けた情報を配信しております。
新任の方やベテランの方、管理職を対象とした幅広いコンテンツをご用意しております。
お問い合わせ
コストダウンが利益に直結する術だと理解していても、なかなか前に進めることができない状況。そんな時は、newjiのコストダウン自動化機能で大きく利益貢献しよう!
(β版非公開)