- お役立ち記事
- Key points and practical know-how on machine design considering accuracy, processing, and cost
Key points and practical know-how on machine design considering accuracy, processing, and cost
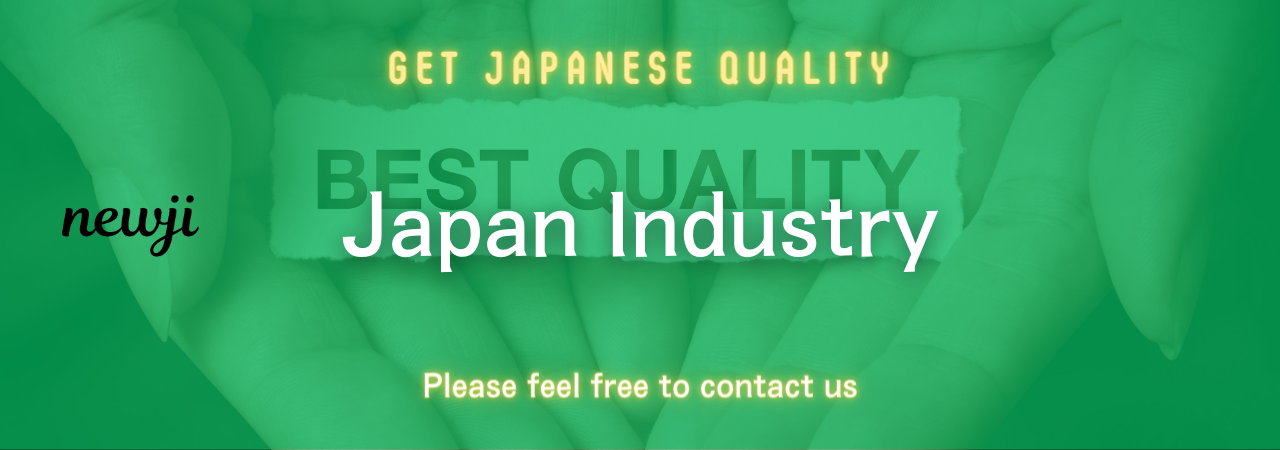
目次
Understanding Machine Design
Machine design is a crucial aspect of engineering that involves creating new machinery or improving existing ones to meet specific needs and functions.
It entails a detailed analysis of various factors including accuracy, processing, and cost.
A well-designed machine can enhance productivity, ensure safety, and minimize costs.
However, achieving such an optimal design requires a deep understanding of the principles and a strategic approach to balancing the different elements involved.
Accuracy in Machine Design
Accuracy is a key factor in machine design, particularly when machines are tasked with precision work.
Precision in this context refers to the machine’s ability to perform consistently at the specified threshold of tolerance without deviation.
To design a machine with high accuracy, engineers need to consider the materials used, the method of production, and the intended use of the machine.
Using high-quality materials and advanced manufacturing processes can result in more precise machines.
For instance, parts that undergo machining and finishing processes precisely can enhance the machine’s accuracy.
Additionally, using precision components such as ball screws, linear guides, and bearings can reduce errors and improve the overall precision of the design.
Testing and Calibration
Once the design is complete, testing and calibration become vital tasks for ensuring precision.
Regular testing helps identify potential areas of inaccuracy where adjustments might be necessary.
Calibration involves aligning the machine components to conform to standardized measurements, thus improving accuracy.
Incorporating sensors and control systems can also enhance machine accuracy by providing real-time adjustments and feedback.
The Role of Technology
Modern technologies like Computer-Aided Design (CAD) and Computer-Aided Manufacturing (CAM) have significantly influenced accuracy in machine design.
These tools allow engineers to create detailed 3D models and simulate operations to predict how the machine will perform under different conditions.
This foresight helps in identifying inaccuracies early in the design process, reducing the risk and cost of errors in the final product.
Processing Considerations
The processing phase refers to all the activities involved from the initial design to the production of the machine.
Designers strive to streamline this process to achieve high efficiency and functionality.
Material Selection
Material choice impacts both the processing efficiency and the performance of the design.
Different applications require different materials—metals like steel and aluminum are common due to their strength and durability, while plastics may be used for components that require less strength but more flexibility and lightness.
Choosing the right material can reduce processing costs and enhance product functionality.
Engineers should also consider the ease with which materials can be processed, affecting machining speeds, tool wear, and the precision of components.
Manufacturing Techniques
The chosen manufacturing techniques significantly affect processing in machine design.
Advanced methods such as CNC machining, 3D printing, and injection molding offer various benefits in terms of precision, cost-efficiency, and speed.
Automation in manufacturing can also speed up the process and lower labor costs, making it a crucial factor for consideration in today’s competitive market.
Cost Efficiency in Design
Cost is a vital component in the design process.
A large part of an engineer’s task is to ensure that the final product is financially viable while meeting all other design criteria.
Balancing Cost and Quality
While cost reduction is necessary for profitability, it should not come at the expense of quality.
A thorough cost analysis during the design phase can help in identifying areas where savings can be made without compromising quality.
Using cost-effective materials, opting for efficient manufacturing processes, and minimizing waste and rework are ways to keep costs in check.
Lifecycle Cost Analysis
An effective approach to managing cost is considering the machine’s lifecycle, from production to decommissioning.
This involves evaluating not just the initial manufacturing cost but also maintenance, operation, and disposal costs.
Designing for durability and ease of maintenance can significantly reduce long-term costs.
Practical Tips for Balanced Design
Achieving a balance between accuracy, processing, and cost requires a comprehensive understanding of various design principles and practical skills.
Prioritize and Plan
Understanding the primary function and use of the machine is essential.
Prioritize design elements based on the most critical aspects of functionality.
Detailed planning can help in identifying potential issues and mitigating them early.
Continuous Improvement
Incorporating feedback and encouraging continuous improvement can lead to better-designed machines over time.
Designers can learn from past projects, gaining insights to enhance future designs.
Cross-Disciplinary Collaboration
Collaborating across different engineering disciplines can provide unique perspectives and creative solutions, contributing to a well-rounded design.
Communication between teams such as electrical, mechanical, and software engineers ensures that all aspects are considered, leading to a more cohesive outcome.
Conclusion
Designing machines with accuracy, processing efficiency, and cost-effectiveness is a complex task that requires a strategic and informed approach.
By considering all aspects of design—sampling, material choice, technology, and process management—engineers can create machines that meet industry standards and client requirements.
It is through this comprehensive understanding and application of principles that truly effective machine design is achieved.
資料ダウンロード
QCD調達購買管理クラウド「newji」は、調達購買部門で必要なQCD管理全てを備えた、現場特化型兼クラウド型の今世紀最高の購買管理システムとなります。
ユーザー登録
調達購買業務の効率化だけでなく、システムを導入することで、コスト削減や製品・資材のステータス可視化のほか、属人化していた購買情報の共有化による内部不正防止や統制にも役立ちます。
NEWJI DX
製造業に特化したデジタルトランスフォーメーション(DX)の実現を目指す請負開発型のコンサルティングサービスです。AI、iPaaS、および先端の技術を駆使して、製造プロセスの効率化、業務効率化、チームワーク強化、コスト削減、品質向上を実現します。このサービスは、製造業の課題を深く理解し、それに対する最適なデジタルソリューションを提供することで、企業が持続的な成長とイノベーションを達成できるようサポートします。
オンライン講座
製造業、主に購買・調達部門にお勤めの方々に向けた情報を配信しております。
新任の方やベテランの方、管理職を対象とした幅広いコンテンツをご用意しております。
お問い合わせ
コストダウンが利益に直結する術だと理解していても、なかなか前に進めることができない状況。そんな時は、newjiのコストダウン自動化機能で大きく利益貢献しよう!
(Β版非公開)