- お役立ち記事
- Key points for blade vibration strength design and troubleshooting of turbomachinery (rotating machinery)
月間77,185名の
製造業ご担当者様が閲覧しています*
*2025年2月28日現在のGoogle Analyticsのデータより
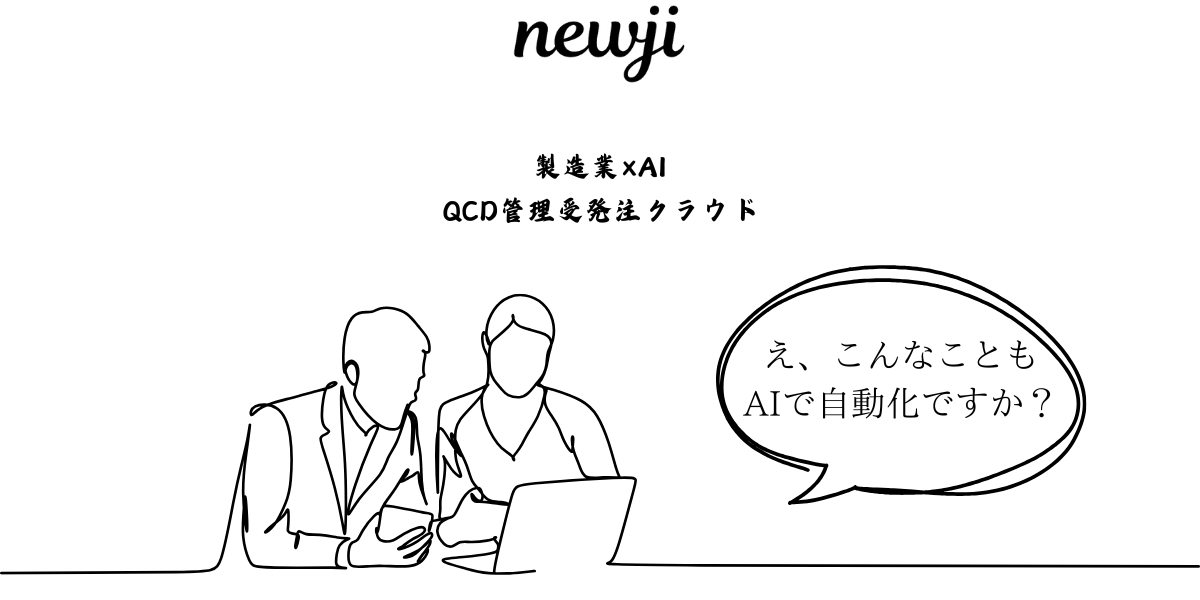
Key points for blade vibration strength design and troubleshooting of turbomachinery (rotating machinery)
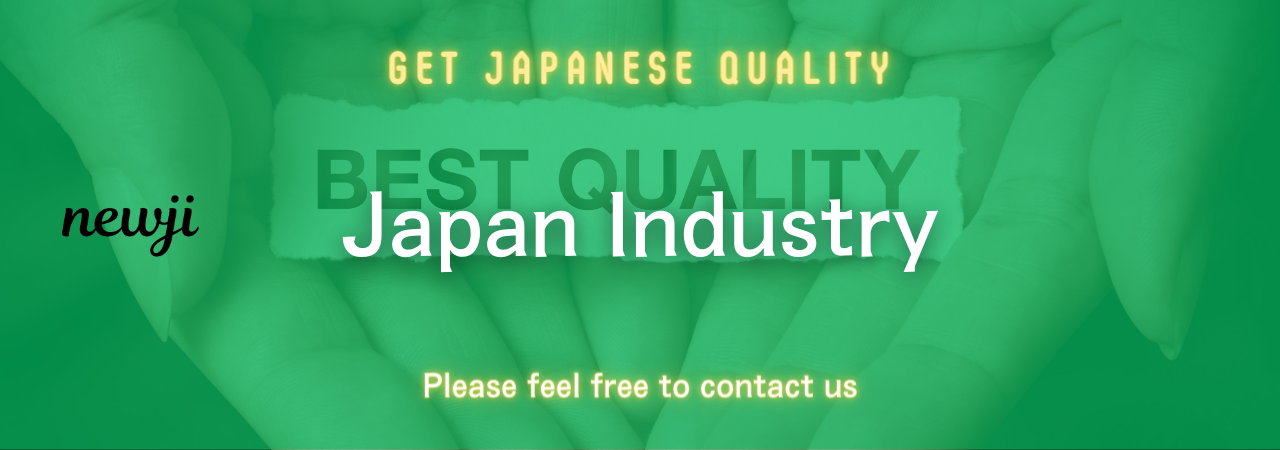
目次
Understanding Blade Vibration in Turbomachinery
Turbomachinery, or rotating machinery, plays a critical role in various industries, from power generation to aerospace.
The efficiency and performance of these machines significantly depend on the design and maintenance of their components.
One of the most crucial components in this machinery is the blade, which is subject to various forces during operation.
Understanding blade vibration and its impact on turbomachinery is essential for ensuring operational reliability and efficiency.
Vibrations in blades can originate from many sources, such as aerodynamic forces, imbalances, mechanical noise, and changes in operating conditions.
These vibrations can lead to structural fatigue, damage, and ultimately, failure, if not adequately addressed.
Thus, consideration of vibration strength is paramount in both the design and troubleshooting stages.
Key Points in Blade Vibration Strength Design
Material Selection
The choice of materials is a fundamental aspect of blade design.
Materials must withstand high stress and strain during operation.
They should also possess the ability to endure fluctuating temperatures and environmental conditions without compromising performance.
Engineers often use alloys like titanium and nickel-based superalloys, which offer high strength-to-weight ratios and excellent corrosion resistance.
These materials help in minimizing vibrations and improving the overall durability of the blades.
Blade Geometry
The geometry of blades significantly influences their vibration characteristics.
Parameters such as blade length, thickness, and curvature need careful consideration.
A well-balanced geometrical design can distribute stress evenly, reducing the likelihood of vibration-induced stresses.
Sophisticated computational tools can model and simulate various geometric configurations to optimize blade shape and improve vibration resistance.
Blade Damping
Incorporating damping solutions is crucial to manage vibrations effectively.
Damping reduces the amplitude of vibrations, thus mitigating potential damage.
Blades can be designed with internal damping mechanisms or coatings that absorb vibrational energy.
Additionally, interlocking shrouds and damping wires can further enhance the vibrational damping characteristics.
Operational Conditions
Understanding and designing for the specific operational conditions of the machinery is essential.
Designers must account for factors such as operational speed, environmental conditions, and the machinery’s intended use.
These factors influence how blades behave under stress and how vibrations might affect their performance and longevity.
Optimizing operational parameters during the design phase can prevent excessive vibration and prolong the life of the blades.
Troubleshooting Blade Vibration
Vibration Monitoring
Regular monitoring of blade vibrations is critical for early detection of potential issues.
Advanced sensors and monitoring systems can provide real-time data on blade performance.
This information allows operators to make informed decisions about maintenance and operational adjustments.
Such proactive measures can prevent catastrophic failures and reduce downtime.
Root Cause Analysis
When addressing blade vibration issues, understanding the root cause is vital.
Typically, blade vibrations can result from misalignment, wear and tear, imbalance, or manufacturing defects.
Conducting a thorough analysis helps in pinpointing the exact cause, allowing for precise corrective actions.
Utilizing failure analysis tools and techniques can significantly improve the troubleshooting process.
Corrective Measures
Once the root cause of vibration is identified, implementing corrective measures is the next step.
This might involve adjusting operating conditions, replacing faulty components, or redesigning certain parts of the machinery.
In some cases, adding or adjusting damping systems can resolve vibration issues.
The goal is to minimize vibrations effectively without compromising the performance or safety of the machinery.
Regular Maintenance
Routine maintenance is essential to keeping blade vibrations in check.
Regular inspections, testing, and recalibrations can prevent minor issues from escalating.
Maintenance schedules should consider the machinery’s operational history and current performance data.
By adhering to a structured maintenance plan, the risk of unexpected downtimes and expensive repairs can be minimized.
Conclusion
Blade vibration strength is a vital component of turbomachinery design and maintenance.
It requires a comprehensive understanding of materials, blade geometry, damping mechanisms, and operational conditions.
Through proactive monitoring, root cause analysis, and regular maintenance, industries can enhance the reliability and efficiency of turbomachinery.
Investing in these design and troubleshooting processes not only extends the lifespan of the machinery but also ensures optimal performance and safety in various operational settings.
資料ダウンロード
QCD管理受発注クラウド「newji」は、受発注部門で必要なQCD管理全てを備えた、現場特化型兼クラウド型の今世紀最高の受発注管理システムとなります。
ユーザー登録
受発注業務の効率化だけでなく、システムを導入することで、コスト削減や製品・資材のステータス可視化のほか、属人化していた受発注情報の共有化による内部不正防止や統制にも役立ちます。
NEWJI DX
製造業に特化したデジタルトランスフォーメーション(DX)の実現を目指す請負開発型のコンサルティングサービスです。AI、iPaaS、および先端の技術を駆使して、製造プロセスの効率化、業務効率化、チームワーク強化、コスト削減、品質向上を実現します。このサービスは、製造業の課題を深く理解し、それに対する最適なデジタルソリューションを提供することで、企業が持続的な成長とイノベーションを達成できるようサポートします。
製造業ニュース解説
製造業、主に購買・調達部門にお勤めの方々に向けた情報を配信しております。
新任の方やベテランの方、管理職を対象とした幅広いコンテンツをご用意しております。
お問い合わせ
コストダウンが利益に直結する術だと理解していても、なかなか前に進めることができない状況。そんな時は、newjiのコストダウン自動化機能で大きく利益貢献しよう!
(β版非公開)