- お役立ち記事
- Key points for building and effectively utilizing an integrated BOM
月間76,176名の
製造業ご担当者様が閲覧しています*
*2025年3月31日現在のGoogle Analyticsのデータより
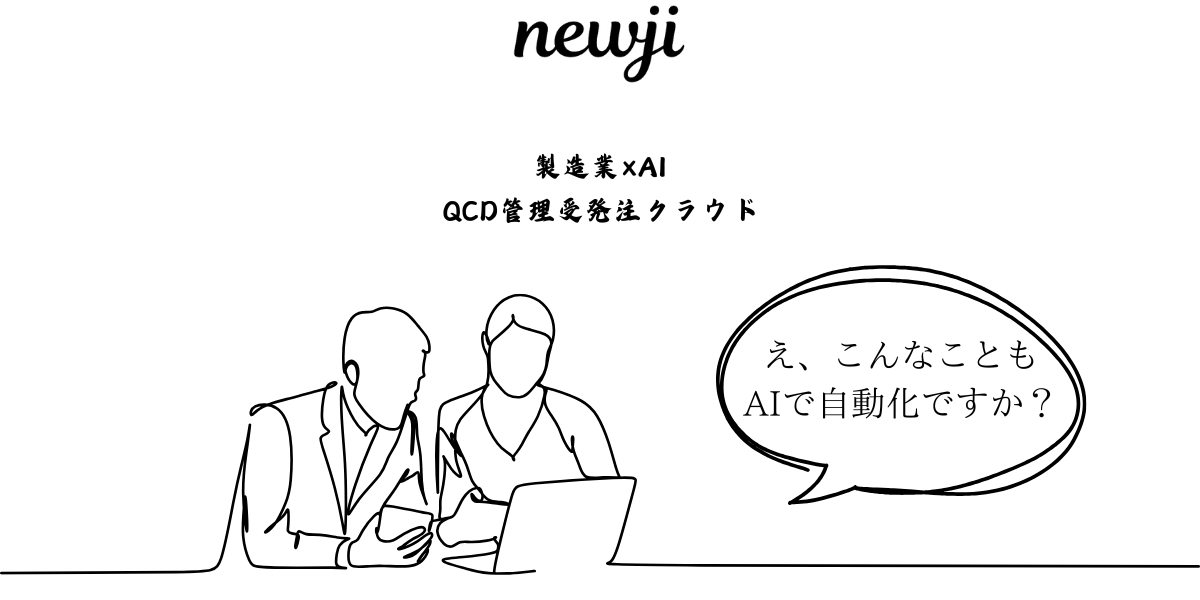
Key points for building and effectively utilizing an integrated BOM
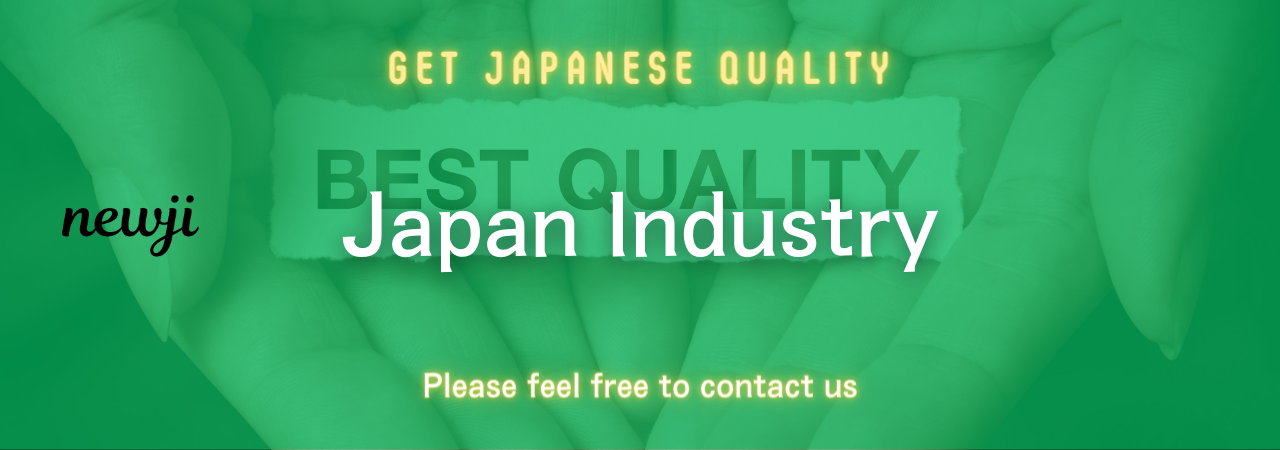
目次
Understanding BOM: The Basics
A Bill of Materials, commonly known as BOM, is an essential component in the manufacturing and production industry.
At its core, a BOM is a detailed list of all items, parts, components, and assemblies required to construct, manufacture, or repair a product.
It acts as a guide for production, ensuring all necessary elements are considered and available for creating a finished product.
Whether you’re making a car, an electronic gadget, or a piece of furniture, using an integrated BOM can streamline the process and increase efficiency.
Integrated BOMs take this concept one step further by combining multiple BOMs into a single, well-organized framework.
This integration facilitates better communication and coordination across various departments, like engineering, purchasing, and production.
The Significance of an Integrated BOM
Using an integrated BOM is crucial for several reasons.
Firstly, it ensures that everyone involved in the production process has access to the latest and most accurate information.
This minimizes mistakes and reduces the chances of costly errors or rework.
Moreover, an integrated BOM enhances collaboration between different teams.
When multiple departments work from the same data, it leads to improved understanding and cooperation.
This connected approach fosters more efficient decision-making and helps in resolving issues that may arise in the production process more swiftly.
Lastly, an integrated BOM is vital for inventory management.
By having a comprehensive list of all parts needed, businesses can better manage their stock levels, reducing waste and keeping costs under control.
Key Steps in Building an Integrated BOM
1. Identify the Scope
Before diving into creating an integrated BOM, it’s important to define the scope of your product.
Identify all the components, materials, and assemblies required.
This initial step lays the foundation for building a comprehensive BOM that accurately reflects your product.
2. Organize Components and Subassemblies
Group related components and subassemblies logically.
For instance, categorize items based on their function or where they fit in the production line.
This organization helps in visualizing the product structure better and makes it easier to manage changes or updates.
3. Use Suitable Software Tools
Leveraging technology is crucial when building an integrated BOM.
Software tools like Enterprise Resource Planning (ERP) systems or Product Lifecycle Management (PLM) platforms can simplify the process.
These tools offer features like automatic updates, version control, and real-time data sharing, which are essential for maintaining an efficient BOM.
4. Standardize Data Entry
Ensure that data entry procedures are standardized across all departments.
This reduces discrepancies and errors, ensuring that everyone is on the same page.
Consistency in data entry formats and protocols makes the BOM more reliable and easy to understand.
5. Ensure Regular Updates and Reviews
A BOM is not a one-time setup; it requires constant updates and reviews.
Regular revisions ensure that the BOM reflects any changes in design, parts, or processes.
Schedule periodic reviews to verify the accuracy of the data and make necessary adjustments.
Challenges in Implementing an Integrated BOM
While the benefits are significant, implementing an integrated BOM also comes with challenges.
One major hurdle is the initial setup and integration of different BOMs from various departments.
This process can be complex and time-consuming, especially in large organizations.
Resistance to change is another potential challenge.
Adapting to new systems and methods may face pushback from employees who are accustomed to existing processes.
Proper training and illustrating the benefits of an integrated BOM can help mitigate this resistance.
Data management is another concern.
Handling large volumes of information and ensuring its accuracy across different systems requires diligence and robust processes.
Employing efficient software solutions and maintaining a disciplined approach to data management is crucial for overcoming this hurdle.
Effective Utilization of an Integrated BOM
To maximize the effectiveness of an integrated BOM, consider adopting the following best practices:
Foster Cross-Departmental Communication
Encourage regular communication between departments that use the BOM.
Regular meetings and open lines of communication ensure that everyone is aligned with the latest updates and any changes in the BOM are understood across the board.
Invest in Continuous Training
Train employees on how to effectively use software tools associated with the integrated BOM.
Continuous training initiatives keep staff updated on best practices and any new features or updates to the software being used.
Leverage Analytical Insights
Use the data from your BOM to gain insights that can lead to process improvements.
Analyzing trends and identifying inefficiencies can help you make informed decisions that drive better results and optimize production processes.
Conclusion
Building and effectively utilizing an integrated BOM is a strategic advantage in production and manufacturing.
By understanding its significance, following best practices in its creation, and overcoming potential challenges, businesses can reap numerous benefits.
An integrated BOM not only improves efficiency but also enhances collaboration, reduces costs, and ensures a streamlined production process.
Investing the time and resources to develop and maintain a comprehensive BOM can significantly impact your business’s overall success and productivity.
資料ダウンロード
QCD管理受発注クラウド「newji」は、受発注部門で必要なQCD管理全てを備えた、現場特化型兼クラウド型の今世紀最高の受発注管理システムとなります。
ユーザー登録
受発注業務の効率化だけでなく、システムを導入することで、コスト削減や製品・資材のステータス可視化のほか、属人化していた受発注情報の共有化による内部不正防止や統制にも役立ちます。
NEWJI DX
製造業に特化したデジタルトランスフォーメーション(DX)の実現を目指す請負開発型のコンサルティングサービスです。AI、iPaaS、および先端の技術を駆使して、製造プロセスの効率化、業務効率化、チームワーク強化、コスト削減、品質向上を実現します。このサービスは、製造業の課題を深く理解し、それに対する最適なデジタルソリューションを提供することで、企業が持続的な成長とイノベーションを達成できるようサポートします。
製造業ニュース解説
製造業、主に購買・調達部門にお勤めの方々に向けた情報を配信しております。
新任の方やベテランの方、管理職を対象とした幅広いコンテンツをご用意しております。
お問い合わせ
コストダウンが利益に直結する術だと理解していても、なかなか前に進めることができない状況。そんな時は、newjiのコストダウン自動化機能で大きく利益貢献しよう!
(β版非公開)