- お役立ち記事
- Key Points for Building and Operating a Global Quality Management System in Manufacturing Quality Assurance
月間76,176名の
製造業ご担当者様が閲覧しています*
*2025年3月31日現在のGoogle Analyticsのデータより
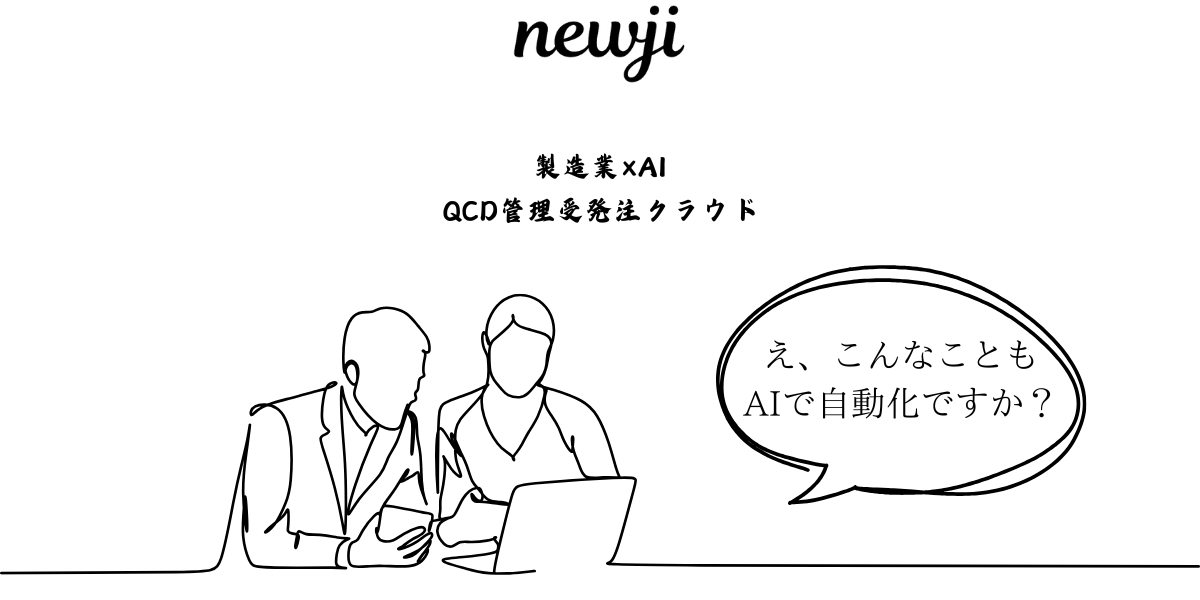
Key Points for Building and Operating a Global Quality Management System in Manufacturing Quality Assurance
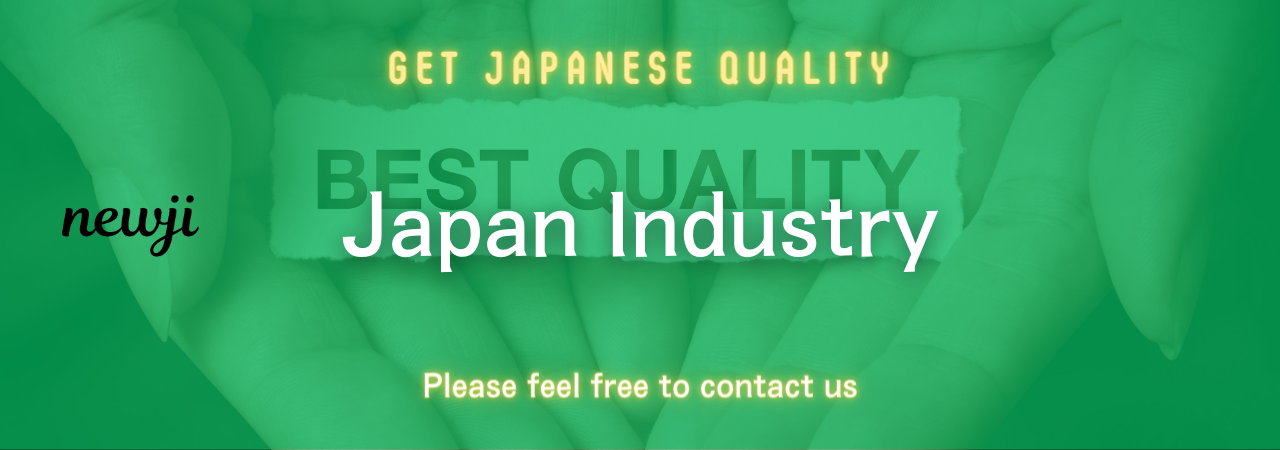
In an ever-connected world, having a robust global quality management system in manufacturing is more essential than ever.
Manufacturers who aim to achieve consistent quality across international borders face numerous challenges.
This article will discuss key points for building and operating such a system, highlighting how to ensure that quality assurance standards are met worldwide.
目次
Understanding the Importance of a Global Quality Management System
A global quality management system (QMS) is critical for manufacturers operating in multiple countries.
It ensures that all products meet the same quality standards, regardless of where they are made.
Such a system fosters customer trust, reduces waste, and minimizes the risk of product recalls.
Furthermore, a well-established QMS can streamline operations, improve compliance with international regulations, and enhance overall efficiency.
Establishing a Solid Foundation
Defining Quality Standards
The first step in building a global QMS is to clearly define quality standards.
These should be consistent across all manufacturing sites.
Utilize internationally recognized standards such as ISO 9001 to ensure that your benchmarks are globally accepted.
Every aspect of your product, from raw materials to final inspection, must meet these standards.
Setting Up a Centralized System
A centralized QMS allows for better control and coordination among different manufacturing locations.
Centralizing your quality management processes can help ensure uniformity.
This includes documenting procedures, setting up a shared database, and utilizing cloud-based software for real-time updates.
Implementing Consistent Training Programs
Employee training is a fundamental component of any QMS.
Standardize training programs across all global sites to ensure everyone is on the same page.
Training should cover quality control procedures, safety protocols, and any machinery or technology used in the manufacturing process.
Leveraging Technology for Quality Assurance
Adopting Advanced Manufacturing Technologies
Technologies such as Artificial Intelligence (AI), the Internet of Things (IoT), and big data analytics can significantly enhance your QMS.
AI can predict potential quality issues, IoT devices can provide real-time data on equipment performance, and big data analytics can identify trends and patterns.
Utilizing Quality Management Software
Investing in quality management software is crucial for a global QMS.
Such software can provide tools for process auditing, compliance management, and corrective actions.
Look for software that can integrate with your existing systems and offers multilingual support to facilitate global operations.
Maintaining Data Integrity and Security
Secure and reliable data is vital for an effective global QMS.
Ensure that your data storage and transmission methods meet international security standards.
Regular audits and security protocols are necessary to prevent data breaches and ensure data integrity.
Continuous Improvement and Adaptation
Regular Audits and Assessments
Regular audits are essential for maintaining the effectiveness of your QMS.
Conduct both internal and external audits to identify areas that need improvement.
Feedback from these audits should be used to update and refine your quality management processes continually.
Employee Feedback and Engagement
Your employees are on the front lines of quality assurance.
Encourage them to provide feedback on current processes and suggest improvements.
Engaged employees are more likely to be committed to maintaining high-quality standards.
Adapting to Regulatory Changes
Regulations and standards are constantly evolving, especially in international markets.
Stay updated with changes in regulations to ensure your QMS remains compliant.
Adapting quickly to these changes can prevent costly non-compliance issues and potential disruptions in your operations.
Overcoming Cultural and Language Barriers
Understanding Cultural Differences
Cultural differences can significantly impact the implementation of a global QMS.
Understanding and respecting these differences can improve communication and cooperation among your international teams.
Provide cultural sensitivity training to help your employees work more effectively with their global counterparts.
Ensuring Effective Communication
Language barriers can lead to misunderstandings and errors in quality management.
Employ multilingual staff or use translation services to ensure clear and accurate communication.
Documentation and training materials should be available in the local languages of all manufacturing sites.
Building a Robust Supply Chain
Selecting Reliable Suppliers
Your suppliers play a crucial role in maintaining quality standards.
Select suppliers who meet your quality requirements and are willing to adhere to your QMS.
Regular audits and performance evaluations can help ensure they remain committed to maintaining high-quality standards.
Establishing Strong Supplier Relationships
Building strong, collaborative relationships with your suppliers is essential.
Open communication and cooperation can help quickly resolve any quality issues that may arise.
Long-term partnerships with reliable suppliers can also contribute to more consistent quality.
Implementing Supplier Training Programs
Training your suppliers on your quality expectations and standards is equally important as training your internal teams.
Ensure that your suppliers are adequately trained on your quality management processes and are equipped with the necessary tools and knowledge to meet your standards.
Conclusion
Implementing and operating a global quality management system in manufacturing quality assurance requires a well-thought-out strategy and a commitment to continuous improvement.
By defining clear quality standards, leveraging technology, and fostering a culture of continuous improvement, manufacturers can achieve consistent, high-quality products across all their global operations.
Understanding cultural differences and building strong relationships with suppliers further enhance the effectiveness of a global QMS.
With these key points in mind, manufacturers can build a robust system that ensures quality and efficiency worldwide.
資料ダウンロード
QCD管理受発注クラウド「newji」は、受発注部門で必要なQCD管理全てを備えた、現場特化型兼クラウド型の今世紀最高の受発注管理システムとなります。
ユーザー登録
受発注業務の効率化だけでなく、システムを導入することで、コスト削減や製品・資材のステータス可視化のほか、属人化していた受発注情報の共有化による内部不正防止や統制にも役立ちます。
NEWJI DX
製造業に特化したデジタルトランスフォーメーション(DX)の実現を目指す請負開発型のコンサルティングサービスです。AI、iPaaS、および先端の技術を駆使して、製造プロセスの効率化、業務効率化、チームワーク強化、コスト削減、品質向上を実現します。このサービスは、製造業の課題を深く理解し、それに対する最適なデジタルソリューションを提供することで、企業が持続的な成長とイノベーションを達成できるようサポートします。
製造業ニュース解説
製造業、主に購買・調達部門にお勤めの方々に向けた情報を配信しております。
新任の方やベテランの方、管理職を対象とした幅広いコンテンツをご用意しております。
お問い合わせ
コストダウンが利益に直結する術だと理解していても、なかなか前に進めることができない状況。そんな時は、newjiのコストダウン自動化機能で大きく利益貢献しよう!
(β版非公開)