- お役立ち記事
- Key points for cost reduction design and optimization design in mechanical design
月間76,176名の
製造業ご担当者様が閲覧しています*
*2025年3月31日現在のGoogle Analyticsのデータより
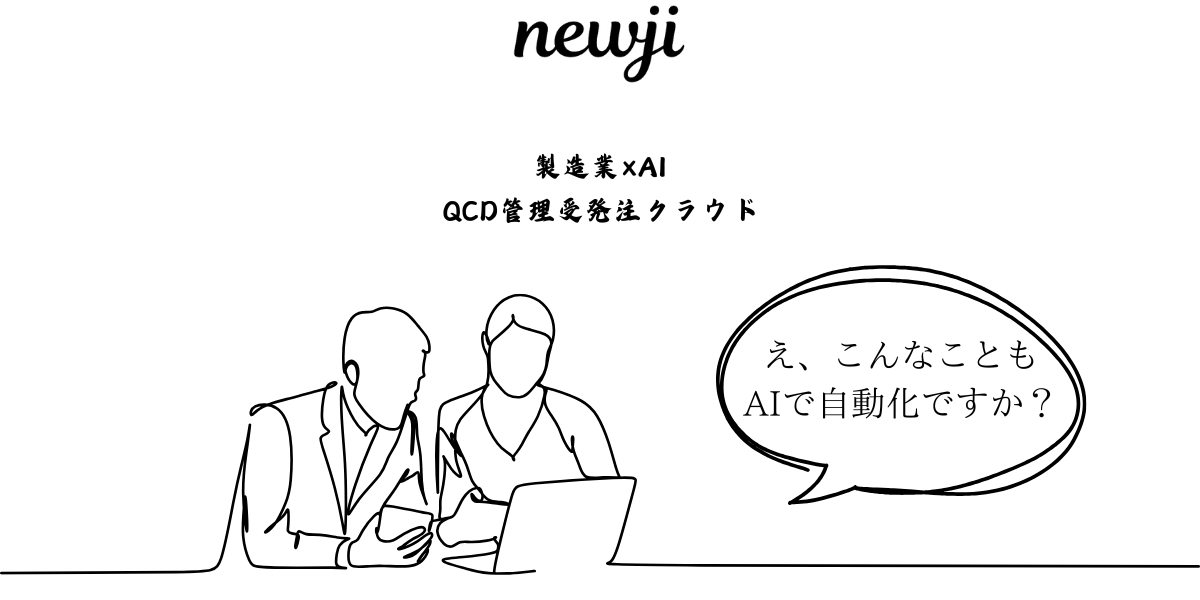
Key points for cost reduction design and optimization design in mechanical design
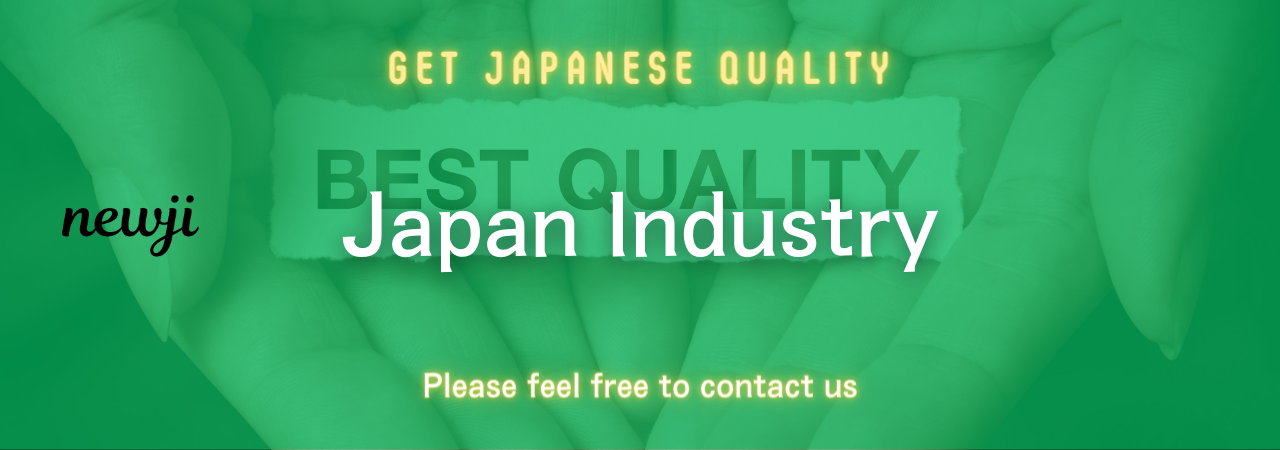
目次
Understanding Cost Reduction in Mechanical Design
Mechanical design is a complex field that involves creating products and systems to meet specific requirements.
One of the main challenges mechanical engineers face is balancing performance with cost efficiency.
Cost reduction in mechanical design is crucial because it directly impacts the profitability of products.
By focusing on reducing costs, companies can offer competitive pricing without compromising on quality.
The key to successful cost reduction is to identify areas where expenses can be minimized without affecting the product’s functionality.
This can be achieved through smart selection of materials, efficient manufacturing processes, and thoughtful design decisions.
Choosing the Right Materials
Material selection is a critical factor in cost reduction.
Different materials have varying costs, and choosing the right one can significantly affect the overall expense.
Engineers should consider using materials that offer the desired properties at a lower cost.
This might involve selecting alternative materials that provide similar strength, durability, and performance.
For instance, using composite materials instead of metals can reduce weight and cost.
Additionally, recycled or locally sourced materials can be more affordable and sustainable options.
Careful analysis of the material’s lifecycle, including manufacturing and disposal, can lead to substantial cost savings.
Design for Manufacturability
Design for manufacturability (DFM) involves creating products that are easy to manufacture with minimal costs.
By simplifying design and reducing the number of components, engineers can decrease the cost of production.
Less complex designs often translate to fewer assembly steps, reduced labor, and lower chances of errors.
Moreover, using common parts and standardized components can lead to economies of scale.
Manufacturers can produce larger batches, resulting in lower per-unit costs.
DFM also considers the design’s adaptability to different manufacturing methods, making it easier and cheaper to produce.
Efficient Manufacturing Processes
Optimizing manufacturing processes is another key aspect of cost reduction.
Implementing lean manufacturing techniques helps eliminate waste, streamline operations, and enhance productivity.
By focusing on continuous improvement, companies can reduce the time and resources needed to produce a product.
Automation is another effective strategy for cost reduction.
Robotics and automated systems can perform repetitive tasks with precision, reducing labor costs and increasing consistency.
However, it’s crucial to weigh the initial investment against long-term savings to ensure automation is a viable solution.
Optimizing the Design Process
Optimizing the design process is fundamental for cost reduction.
A well-structured design process ensures efficient use of resources and minimizes waste.
Using computer-aided design (CAD) software can enhance visualization and testing, reducing the need for physical prototypes.
Virtual simulations can identify potential issues early in the design phase, preventing costly errors later.
By integrating simulation tools, engineers can test different scenarios and optimize the design before production begins.
Additionally, collaboration among cross-functional teams during the design phase can provide valuable insights into cost-saving opportunities.
Such collaboration ensures that all aspects of the design, from technical specifications to commercial considerations, are aligned.
The Role of Optimization Design
Optimization design is another crucial aspect of mechanical engineering that focuses on enhancing performance and efficiency.
It involves fine-tuning the design to maximize output while minimizing resources.
By optimizing design, engineers can achieve the best possible performance at the lowest possible cost.
Structural Optimization
Structural optimization is about refining the geometry of a product to improve performance and reduce material usage.
Using techniques like topology optimization, engineers can identify the best material distribution for maximum strength and minimal weight.
This approach is particularly beneficial in industries like aerospace and automotive, where reducing weight without compromising strength is essential.
By removing unnecessary material, companies can also lower production costs and improve energy efficiency.
Thermal and Fluid Dynamics Optimization
Optimizing thermal and fluid dynamics is crucial for products that involve heat exchange or fluid movement.
For instance, in cooling systems, optimizing the flow paths can enhance heat dissipation and improve energy efficiency.
Simulation tools are invaluable for analyzing these dynamics and identifying potential improvements.
By understanding how heat and fluids behave within the system, engineers can design more efficient products and reduce operational costs.
Energy Efficiency Optimization
Energy efficiency is a key consideration in modern mechanical design.
Optimizing for energy use not only reduces operational costs but also benefits the environment.
Electrical, mechanical, and thermal optimization techniques can lead to significant energy savings.
Designers should consider factors like friction, aerodynamics, and thermal insulation to enhance efficiency.
Smart design choices can lead to products that consume less power and offer sustainable solutions to consumers.
Conclusion
Balancing cost reduction with optimization design in mechanical engineering requires a strategic approach.
By selecting the right materials, streamlining manufacturing processes, and optimizing designs, engineers can create cost-effective and high-performing products.
As technology advances, leveraging simulation tools and modern manufacturing techniques will be vital for competitive advantage.
Equally important is the need for a collaborative approach across teams, ensuring that all stakeholders contribute to a holistic design strategy.
By integrating insights from different experts, companies can uncover innovative solutions that achieve both cost efficiency and excellence in performance.
資料ダウンロード
QCD管理受発注クラウド「newji」は、受発注部門で必要なQCD管理全てを備えた、現場特化型兼クラウド型の今世紀最高の受発注管理システムとなります。
ユーザー登録
受発注業務の効率化だけでなく、システムを導入することで、コスト削減や製品・資材のステータス可視化のほか、属人化していた受発注情報の共有化による内部不正防止や統制にも役立ちます。
NEWJI DX
製造業に特化したデジタルトランスフォーメーション(DX)の実現を目指す請負開発型のコンサルティングサービスです。AI、iPaaS、および先端の技術を駆使して、製造プロセスの効率化、業務効率化、チームワーク強化、コスト削減、品質向上を実現します。このサービスは、製造業の課題を深く理解し、それに対する最適なデジタルソリューションを提供することで、企業が持続的な成長とイノベーションを達成できるようサポートします。
製造業ニュース解説
製造業、主に購買・調達部門にお勤めの方々に向けた情報を配信しております。
新任の方やベテランの方、管理職を対象とした幅広いコンテンツをご用意しております。
お問い合わせ
コストダウンが利益に直結する術だと理解していても、なかなか前に進めることができない状況。そんな時は、newjiのコストダウン自動化機能で大きく利益貢献しよう!
(β版非公開)