- お役立ち記事
- Key points for effective use of industrial robots and ensuring safety for production automation
月間76,176名の
製造業ご担当者様が閲覧しています*
*2025年3月31日現在のGoogle Analyticsのデータより
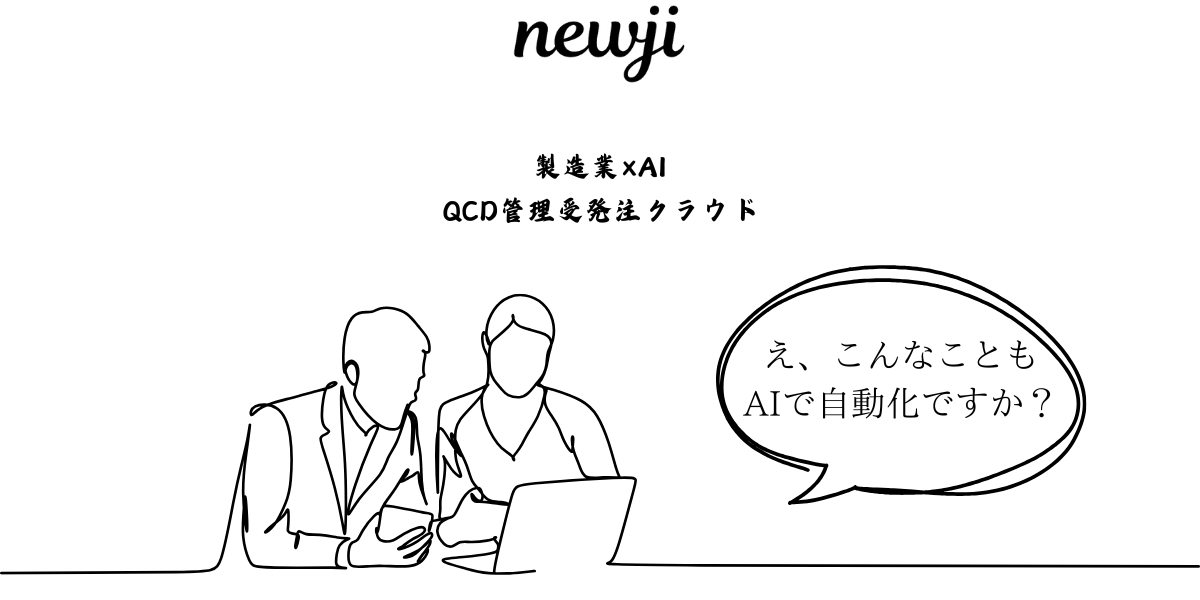
Key points for effective use of industrial robots and ensuring safety for production automation
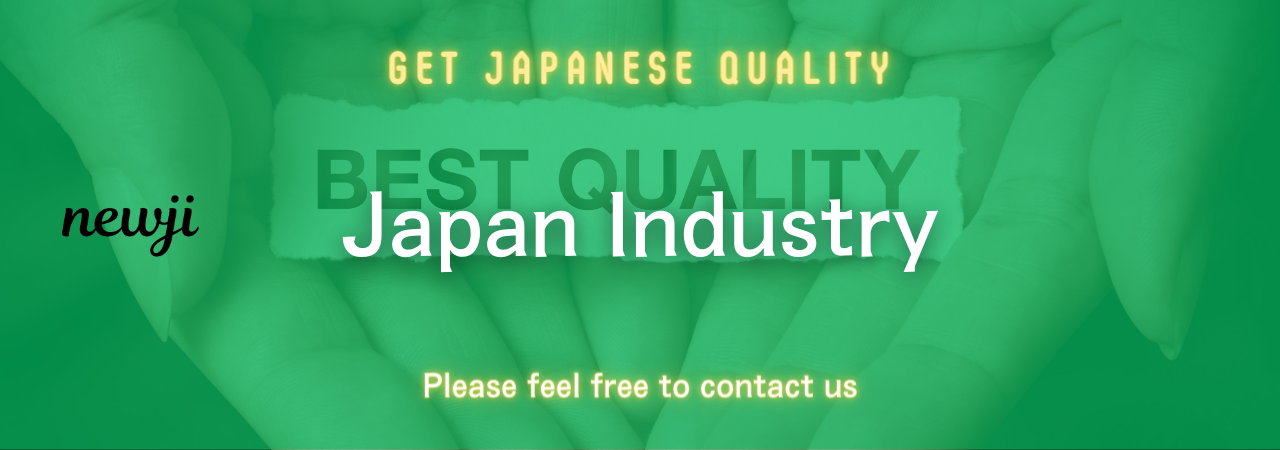
目次
Introduction to Industrial Robots
Industrial robots have revolutionized the manufacturing and production sectors, offering unprecedented precision, speed, and efficiency.
They are used for tasks ranging from simple assembly to complex machining processes.
As automation becomes increasingly central to production, understanding how to effectively leverage industrial robots while ensuring safety is crucial for modern businesses.
The Role of Industrial Robots in Automation
Industrial robots excel in repetitive tasks and environments that may be hazardous to humans.
Their ability to operate both continuously and consistently makes them ideal for enhancing productivity.
By redefining production processes, robots minimize human error and maximize resource utilization.
However, integrating robots into production lines requires careful planning and strategy.
Key Benefits of Industrial Robots
1. **Increased Productivity**: Robots can operate around the clock without fatigue, significantly increasing production rates.
2. **Quality Control**: With precision programming, robots perform tasks with high accuracy, reducing errors and ensuring consistent product quality.
3. **Cost Efficiency**: Although the initial investment may be high, robots considerably lower labor and production costs over time.
Factors to Consider When Implementing Robots
1. **Assessment of Needs**: Determine the specific tasks where robots could improve efficiency or safety.
2. **Cost Analysis**: Evaluate the cost-effectiveness of different robotic systems, including maintenance and potential savings generated by automation.
3. **Integration Plan**: Develop a comprehensive plan to integrate robots into existing workflows, ensuring minimal disruption.
Ensuring Safety with Industrial Robots
With the introduction of robots, safety becomes a paramount concern in any automated production environment.
Ensuring that human workers and robots can coexist safely requires stringent measures and considerations.
Safety Guidelines for Industrial Robots
1. **Risk Assessment**: Conduct thorough risk assessments to identify potential hazards associated with robotic systems.
2. **Safety Training**: Provide detailed training for all employees on interacting safely with robotic equipment.
3. **Emergency Protocols**: Implement emergency procedures and accessible shutdown systems in case of malfunction or danger.
Technological Safety Features
1. **Sensors and Cameras**: Modern robots are equipped with sensors and cameras that can detect human presence and obstacles, preventing accidents.
2. **Physical Barriers**: Safety cages and barriers prevent unauthorized access to robot work areas.
3. **Collaborative Robots**: These robots are designed to work alongside humans safely, with built-in features to minimize impact in case of contact.
Optimizing the Use of Industrial Robots
To make the most out of industrial robots, strategic optimization of their use is necessary.
This involves not only leveraging their capabilities but also continuously monitoring and improving their functions.
Maintenance and Upkeep
1. **Regular Inspections**: Conduct routine checks to ensure that robot components are functioning properly and replace parts as needed.
2. **Software Updates**: Keep robotic software up-to-date with the latest versions to improve performance and security.
3. **Preventive Maintenance**: Implement a schedule that anticipates wear and tear, preventing unexpected downtime.
Employee Involvement
1. **Skills Development**: Train employees in robotics technology to empower them to manage, operate, and troubleshoot issues.
2. **Feedback Mechanism**: Establish channels for employees to provide feedback on robot operations, contributing to continuous improvement.
Conclusion
The integration of industrial robots in production processes is a critical step towards achieving heightened levels of automation and efficiency.
However, it comes with the responsibility of ensuring safe interactions between humans and machines.
By understanding key points, such as safety protocols and effective robot utilization, businesses can make informed decisions that enhance productivity, reduce expenses, and maintain a safe working environment.
Embracing these strategies not only boosts operations but also prepares industries for a future where robots play an even greater role in manufacturing.
資料ダウンロード
QCD管理受発注クラウド「newji」は、受発注部門で必要なQCD管理全てを備えた、現場特化型兼クラウド型の今世紀最高の受発注管理システムとなります。
ユーザー登録
受発注業務の効率化だけでなく、システムを導入することで、コスト削減や製品・資材のステータス可視化のほか、属人化していた受発注情報の共有化による内部不正防止や統制にも役立ちます。
NEWJI DX
製造業に特化したデジタルトランスフォーメーション(DX)の実現を目指す請負開発型のコンサルティングサービスです。AI、iPaaS、および先端の技術を駆使して、製造プロセスの効率化、業務効率化、チームワーク強化、コスト削減、品質向上を実現します。このサービスは、製造業の課題を深く理解し、それに対する最適なデジタルソリューションを提供することで、企業が持続的な成長とイノベーションを達成できるようサポートします。
製造業ニュース解説
製造業、主に購買・調達部門にお勤めの方々に向けた情報を配信しております。
新任の方やベテランの方、管理職を対象とした幅広いコンテンツをご用意しております。
お問い合わせ
コストダウンが利益に直結する術だと理解していても、なかなか前に進めることができない状況。そんな時は、newjiのコストダウン自動化機能で大きく利益貢献しよう!
(β版非公開)