- お役立ち記事
- Key Points for Establishing and Operating a Global Quality Control System in Manufacturing Quality Assurance
Key Points for Establishing and Operating a Global Quality Control System in Manufacturing Quality Assurance
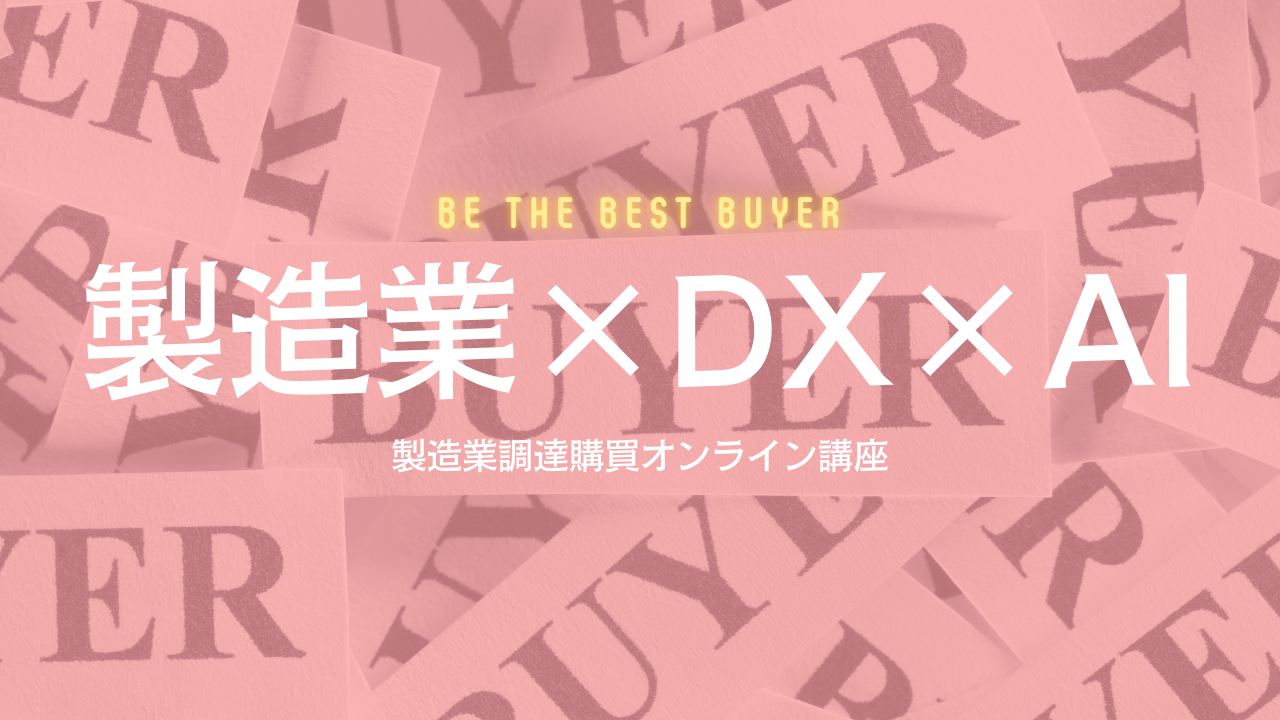
Quality control is essential for any manufacturing company that wants to establish itself as a leader in its industry known for high standards. A thoughtful global quality control system can help you meet customer expectations consistently no matter where your products are made or sold. Here are some key points to consider as you develop and operate your quality assurance processes on an international scale.
目次
Define Quality Standards
The foundation of any quality system begins with clearly defining what quality means for your business and your brand. Establish measurable criteria for factors like design specifications, material integrity, workmanship levels, safety regulations, and customer satisfaction. Document these standards and ensure they can be understood by all employees, whether working in your home country or overseas. Consider having standards professionally translated so language is no barrier to consistent quality worldwide.
Train Locally, Oversee Globally
While quality control training and protocols may start at your headquarters, make sure they are adapted appropriately for other locations. cultural and regulatory differences. Assign quality managers in each region who understand local needs but report directly to your central quality leadership. Conduct in-person or virtual audits regularly to ensure uniform understanding and application of standards globally. Address any issues promptly to maintain continuous improvement across your operations.
Standardize Processes
Having documented, consistent processes is key to replicating quality no matter the manufacturing site. Map out each step from design to distribution and establish standard operating procedures all sites must follow. Use visual management tools to communicate expectations clearly on factory floors worldwide. Empower local quality teams to customize processes respectfully as needed but always within conformance to your core standards. Regular process reviews can identify optimization opportunities for even higher quality globally.
Select Suppliers Carefully
The quality of incoming materials directly affects your products. Develop a global supplier approval process including audits to ensure all partners meet your standards. Qualify suppliers on criteria like certification, traceability, defect rates, delivery reliability, and financial stability. Consider dual sourcing for critical components to mitigate supply chain risks. Maintain ongoing performance reviews and work with suppliers on continuous improvement initiatives for sustained quality into the future.
Incorporate Technology
Leverage digital tools to streamline quality management on a global scale. Centralized quality information systems allow oversight of KPIs, corrective actions, documentation control and more from any location. Industrial IoT and analytics can optimize processes through remote monitoring of manufacturing equipment health or real-time defect detection. Robotic vision inspection boosts consistency by removing human subjectivity. Blockchain brings supply chain traceability and transparency. An integrated technology approach strengthens quality control worldwide.
Establish Clear Feedback Loops
Quality is not a destination but a journey of refinement. Empower all stakeholders worldwide to freely provide feedback on potential issues and areas for enhancement. Respond transparently and work cross-functionally toward solutions. Celebrate improvement successes as well to nurture a culture where quality excellence is a driver of pride rather than fear. Customer insights like warranty data analysis and post-purchase surveys also fuel your quality evolution. Continuous feedback guided by leadership keeps global quality control vibrant and future-proof.
Certification Demands Compliance
Pursuing certification to recognized global standards demonstrates your commitment to quality control and reassures customers. Manage the audit process for schemes like ISO 9001 across all your locations. Certification elevates trust in your brand worldwide and strengthens compliance to your documented quality management system. It can even open doors to new markets by meeting predefined criteria customers expect. Maintain certification with ongoing conformance to achieve long term competitive advantage through globally recognized quality.
Effective quality control on a global scale requires diligent planning, communication and adaptability. With the right strategy, structure, processes and leadership tone, every manufacturing site can consistently meet high standards worldwide no matter its distance from corporate headquarters. Your customers will reward reliability they can count on regardless of where in the world your product is delivered from.
In summary, establishing a robust quality control system across diverse international operations takes discipline but pays off in customer loyalty, cost optimization and sustainable growth over the long term. A focus on quality sets the foundation for global manufacturing excellence and a strong worldwide brand.
資料ダウンロード
QCD調達購買管理クラウド「newji」は、調達購買部門で必要なQCD管理全てを備えた、現場特化型兼クラウド型の今世紀最高の購買管理システムとなります。
ユーザー登録
調達購買業務の効率化だけでなく、システムを導入することで、コスト削減や製品・資材のステータス可視化のほか、属人化していた購買情報の共有化による内部不正防止や統制にも役立ちます。
NEWJI DX
製造業に特化したデジタルトランスフォーメーション(DX)の実現を目指す請負開発型のコンサルティングサービスです。AI、iPaaS、および先端の技術を駆使して、製造プロセスの効率化、業務効率化、チームワーク強化、コスト削減、品質向上を実現します。このサービスは、製造業の課題を深く理解し、それに対する最適なデジタルソリューションを提供することで、企業が持続的な成長とイノベーションを達成できるようサポートします。
オンライン講座
製造業、主に購買・調達部門にお勤めの方々に向けた情報を配信しております。
新任の方やベテランの方、管理職を対象とした幅広いコンテンツをご用意しております。
お問い合わせ
コストダウンが利益に直結する術だと理解していても、なかなか前に進めることができない状況。そんな時は、newjiのコストダウン自動化機能で大きく利益貢献しよう!
(Β版非公開)