- お役立ち記事
- Key Points for Evaluating Product Heat Resistance with Thermal Shock Tests
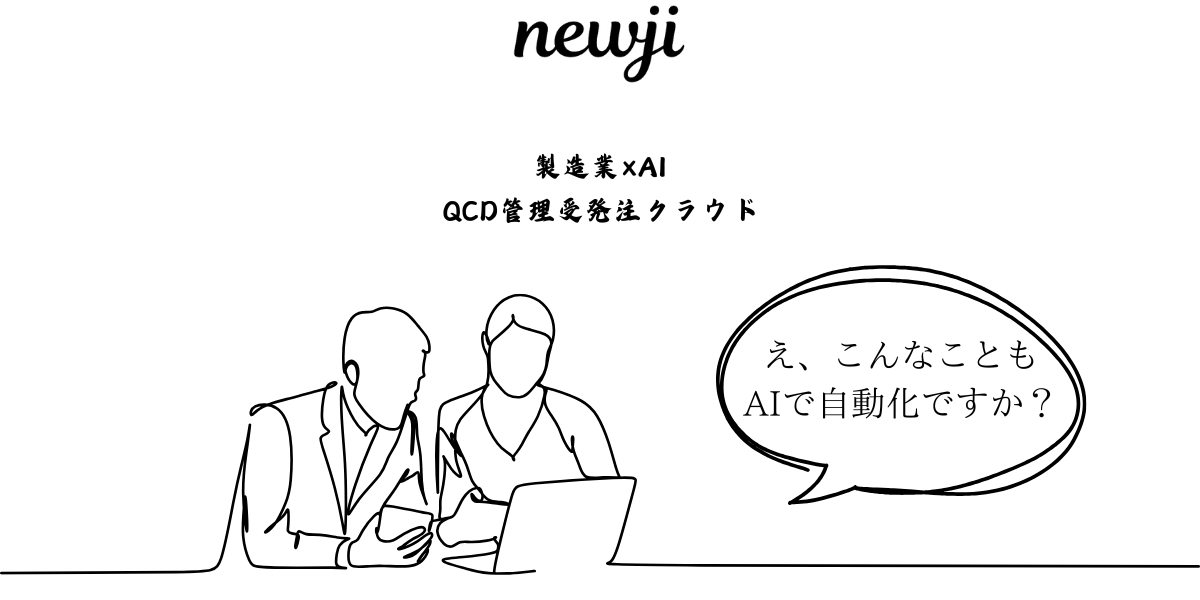
Key Points for Evaluating Product Heat Resistance with Thermal Shock Tests
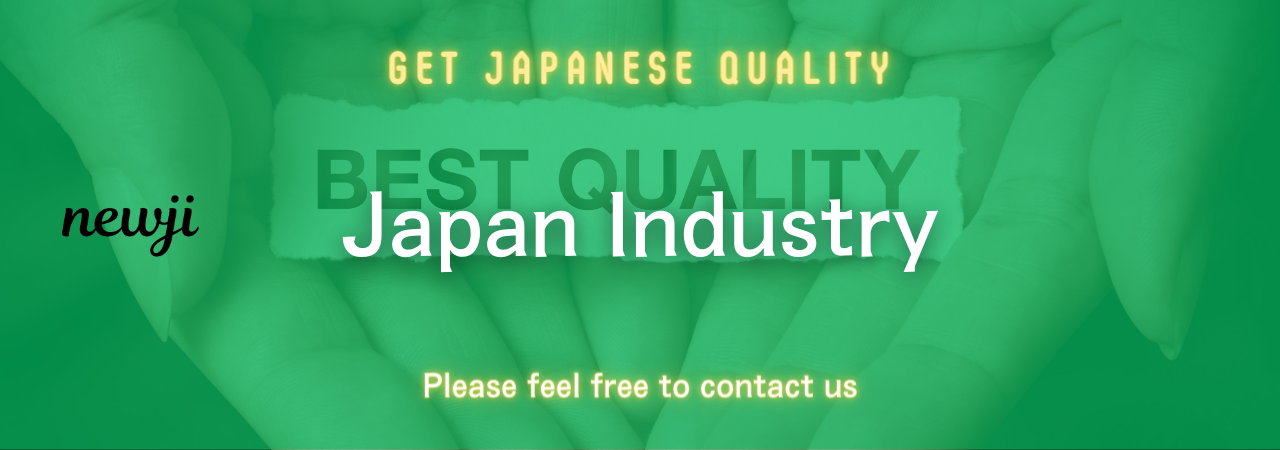
Understanding how a product withstands extreme temperature changes is crucial for ensuring its durability and reliability.
Thermal shock tests are designed to evaluate this capability.
Let’s delve into the key points for evaluating product heat resistance with thermal shock tests.
目次
What are Thermal Shock Tests?
Thermal shock tests are a method of assessing how well a product can endure sudden changes in temperature without compromising its integrity.
The test subjects the product to rapid temperature cycles, moving from one extreme to another.
This process helps to identify any weaknesses or potential for failure when exposed to real-world conditions.
Why Are Thermal Shock Tests Important?
Products in various industries, from electronics to automotive, are often exposed to rapid temperature fluctuations.
If a product cannot handle these changes, it may fail prematurely.
Thermal shock tests help manufacturers ensure that their products can withstand such conditions.
This is particularly important for ensuring safety, performance, and longevity.
Preparing for Thermal Shock Tests
Preparation is key to obtaining accurate and meaningful results from thermal shock tests.
Here are some important steps to consider:
Selecting the Right Equipment
Choosing the appropriate testing equipment is crucial.
Thermal chambers should be capable of providing rapid temperature changes.
The equipment must be calibrated and maintained regularly to ensure accuracy and consistency in test results.
Understanding Testing Standards
Different industries have specific standards for thermal shock testing.
Familiarize yourself with the relevant standards, such as MIL-STD-883 for electronics or ASTM standards for materials.
Adhering to these standards ensures that the test results are valid and comparable.
Conducting the Thermal Shock Test
Once you are prepared, it is time to conduct the test.
Follow these steps for a successful thermal shock test:
Defining Test Parameters
Establish clear parameters for the test, including temperature extremes, dwell time at each temperature, and the number of cycles.
These parameters should reflect the conditions the product will encounter in real-world applications.
Placing the Product in the Thermal Chamber
Carefully place the product in the thermal chamber.
Ensure that the product is not obstructed and receives uniform temperature exposure.
Monitor the product and chamber closely throughout the test to identify any anomalies.
Recording Test Data
Accurate data recording is essential for analyzing the test results.
Use data loggers to capture temperature changes and any signs of product failure, such as cracks, deformation, or electrical malfunctions.
Document every observation meticulously.
Analyzing Results and Making Improvements
After completing the thermal shock test, the next step is to analyze the results and make necessary improvements.
Interpreting Data
Examine the recorded data to identify how the product responded to temperature changes.
Look for patterns or specific points where failures occurred.
Compare the results with expected performance standards to determine if the product meets the required criteria.
Identifying Weak Points
Use the test results to pinpoint any weaknesses in the product design or materials.
For instance, if a specific component consistently fails, it may need reinforcement or replacement with a more durable material.
Implementing Design Changes
Based on the insights gained from the test, implement necessary design or material changes.
Modifying the product to enhance its thermal resistance will help improve its overall performance and longevity.
Final Thoughts on Thermal Shock Testing
Thermal shock tests are an invaluable tool for evaluating a product’s heat resistance.
By following proper preparation steps, defining clear test parameters, and accurately recording and analyzing data, manufacturers can ensure their products are reliable and durable in varying temperature conditions.
Ultimately, these tests help to deliver products that can stand the test of time, providing consumers with safe and dependable solutions.
資料ダウンロード
QCD調達購買管理クラウド「newji」は、調達購買部門で必要なQCD管理全てを備えた、現場特化型兼クラウド型の今世紀最高の購買管理システムとなります。
ユーザー登録
調達購買業務の効率化だけでなく、システムを導入することで、コスト削減や製品・資材のステータス可視化のほか、属人化していた購買情報の共有化による内部不正防止や統制にも役立ちます。
NEWJI DX
製造業に特化したデジタルトランスフォーメーション(DX)の実現を目指す請負開発型のコンサルティングサービスです。AI、iPaaS、および先端の技術を駆使して、製造プロセスの効率化、業務効率化、チームワーク強化、コスト削減、品質向上を実現します。このサービスは、製造業の課題を深く理解し、それに対する最適なデジタルソリューションを提供することで、企業が持続的な成長とイノベーションを達成できるようサポートします。
オンライン講座
製造業、主に購買・調達部門にお勤めの方々に向けた情報を配信しております。
新任の方やベテランの方、管理職を対象とした幅広いコンテンツをご用意しております。
お問い合わせ
コストダウンが利益に直結する術だと理解していても、なかなか前に進めることができない状況。そんな時は、newjiのコストダウン自動化機能で大きく利益貢献しよう!
(Β版非公開)