- お役立ち記事
- Key points for extending the lifespan of mechanical equipment through lifespan prediction and condition monitoring
月間76,176名の
製造業ご担当者様が閲覧しています*
*2025年3月31日現在のGoogle Analyticsのデータより
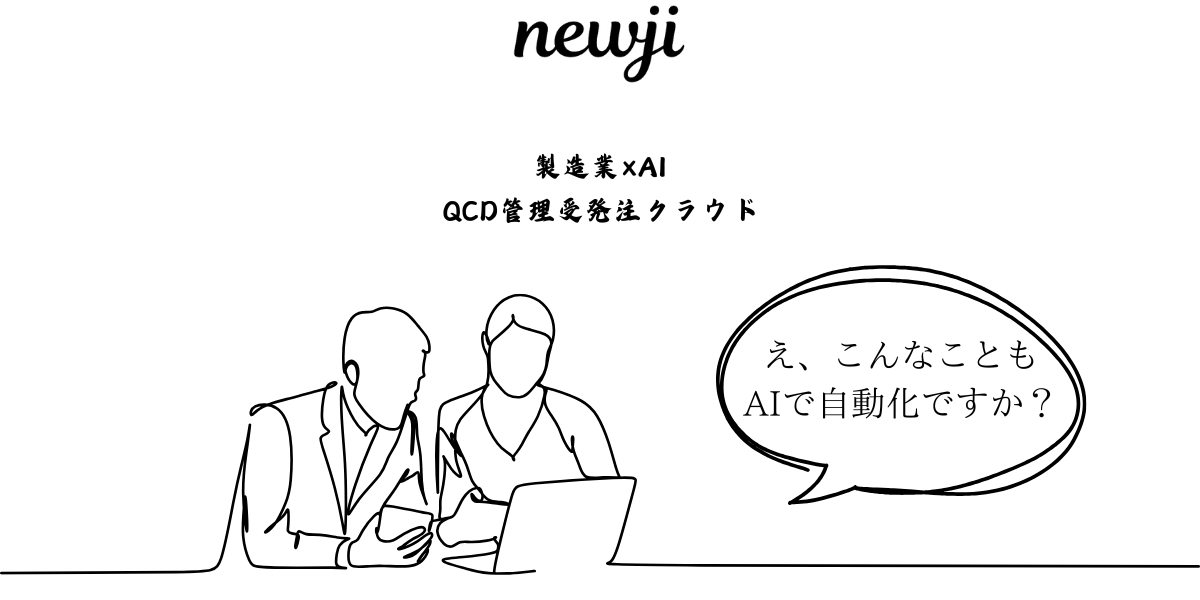
Key points for extending the lifespan of mechanical equipment through lifespan prediction and condition monitoring
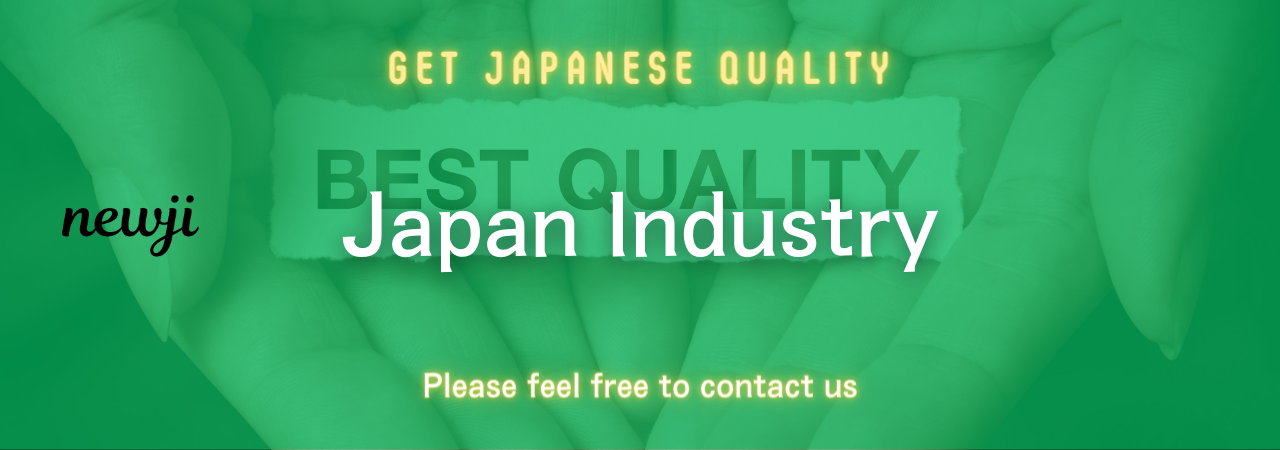
目次
Understanding Lifespan Prediction
Lifespan prediction is a critical aspect of maintaining mechanical equipment.
It involves estimating how long a piece of equipment will function before it requires repair or replacement.
By accurately predicting the lifespan, businesses can plan maintenance activities effectively, reducing unexpected breakdowns and operational downtime.
Modern techniques rely on data analytics and machine learning models to analyze equipment performance over time.
Predictive maintenance is an advanced approach where data from sensors, historical maintenance records, and operational conditions are used to forecast when an equipment component might fail.
By examining patterns and anomalies in the data, organizations can predict potential issues before they actually occur.
Benefits of Lifespan Prediction
One major advantage is cost savings.
By knowing precisely when to perform maintenance, businesses can avoid unnecessary service costs and reduce the incidence of emergency repairs, which tend to be more expensive.
Moreover, lifespan predictions can help in optimizing resource allocation, ensuring that manpower and materials are available when needed.
Operational efficiency also improves significantly.
Predicting equipment lifespan helps in scheduling maintenance during non-peak times, minimizing disruption to normal operations.
This proactive approach enhances the reliability of machinery, consequently improving productivity.
Condition Monitoring Explained
Condition monitoring is the practice of continuously observing a machine’s state through various means, typically sensors and diagnostic tools.
It is an essential component of predictive maintenance, providing real-time insights into equipment health.
Common parameters monitored include vibration analysis, temperature, pressure, and lubrication quality.
By regularly checking these indicators, businesses can assess the current condition of equipment and make informed decisions about required maintenance actions.
This real-time data collection and analysis help in understanding how equipment behaves under different conditions and determines which components are wearing out faster than expected.
Essential Tools for Condition Monitoring
Several tools are integral to effective condition monitoring.
Vibration analysis tools, for instance, help detect imbalances or misalignments in rotating machinery.
Infrared thermography is another tool used to identify heat deviations, which could indicate issues such as electrical faults or friction problems.
Ultrasonic testing is frequently used to detect changes in fluid levels or spot leaks in pressurized systems.
Oil analysis can determine the presence of contaminants in lubricants, alerting maintenance teams to potential internal wear or damage.
Integrating Lifespan Prediction and Condition Monitoring
Integrating lifespan prediction with condition monitoring creates a robust maintenance strategy.
By combining data from both predictive models and real-time monitoring, businesses gain a comprehensive understanding of their equipment’s health.
This integration enables more accurate predictions and informed maintenance decisions.
The integration process often involves implementing IoT devices and advanced analytics platforms.
These technologies allow for seamless data collection and analysis, providing actionable insights to maintenance teams.
Additionally, integrating these systems helps in setting up automated alerts, ensuring timely interventions when anomalies are detected.
Steps to Successful Integration
Firstly, assess current equipment and monitoring capabilities.
Determine what data is available and identify any gaps in information.
Next, deploy necessary sensors and monitoring devices to fill these gaps.
Subsequently, invest in a centralized analytics platform capable of processing vast amounts of data and generating insights.
This platform should support machine learning algorithms for predictive analysis and offer easy-to-understand visualizations.
Finally, train your maintenance team on how to interpret the data and integrate insights into your maintenance schedule.
Continual training ensures that teams stay updated on the latest tools and techniques, maximizing the benefits of this integrated approach.
Challenges and Considerations
Despite the advantages, there are challenges in implementing lifespan prediction and condition monitoring.
The accuracy of predictions heavily depends on quality data.
Therefore, improper sensor placement or unreliable data sources can lead to incorrect conclusions.
Organizations must also consider the initial investment required for equipment and training.
Although the long-term savings usually justify the expense, budget constraints can pose short-term challenges.
Moreover, resistance to change within an organization can slow down implementation.
Ensuring all stakeholders understand the benefits is crucial for gaining support and facilitating a smooth transition to this advanced maintenance strategy.
Overcoming Implementation Hurdles
To address these challenges, start small with a pilot project involving critical pieces of equipment.
Demonstrating success on a smaller scale can ease concerns and showcase the value of predictive maintenance and condition monitoring.
Ensure cross-department collaboration, involving both IT and maintenance teams in the process.
This collaboration helps in integrating systems efficiently and addressing any technical or practical issues that arise.
Conclusion
Extending the lifespan of mechanical equipment requires a strategic combination of lifespan prediction and condition monitoring.
These techniques, when effectively integrated, offer considerable benefits, including cost savings, operational efficiency, and improved equipment reliability.
With the right tools, data, and processes, businesses can not only predict potential failures but also enhance their maintenance strategies.
While initial implementation may present challenges, the long-term advantages far outweigh the hurdles, ensuring sustained performance and streamlined operations.
資料ダウンロード
QCD管理受発注クラウド「newji」は、受発注部門で必要なQCD管理全てを備えた、現場特化型兼クラウド型の今世紀最高の受発注管理システムとなります。
ユーザー登録
受発注業務の効率化だけでなく、システムを導入することで、コスト削減や製品・資材のステータス可視化のほか、属人化していた受発注情報の共有化による内部不正防止や統制にも役立ちます。
NEWJI DX
製造業に特化したデジタルトランスフォーメーション(DX)の実現を目指す請負開発型のコンサルティングサービスです。AI、iPaaS、および先端の技術を駆使して、製造プロセスの効率化、業務効率化、チームワーク強化、コスト削減、品質向上を実現します。このサービスは、製造業の課題を深く理解し、それに対する最適なデジタルソリューションを提供することで、企業が持続的な成長とイノベーションを達成できるようサポートします。
製造業ニュース解説
製造業、主に購買・調達部門にお勤めの方々に向けた情報を配信しております。
新任の方やベテランの方、管理職を対象とした幅広いコンテンツをご用意しております。
お問い合わせ
コストダウンが利益に直結する術だと理解していても、なかなか前に進めることができない状況。そんな時は、newjiのコストダウン自動化機能で大きく利益貢献しよう!
(β版非公開)