- お役立ち記事
- Key Points for High-Precision Part Manufacturing Using Grinding Technology
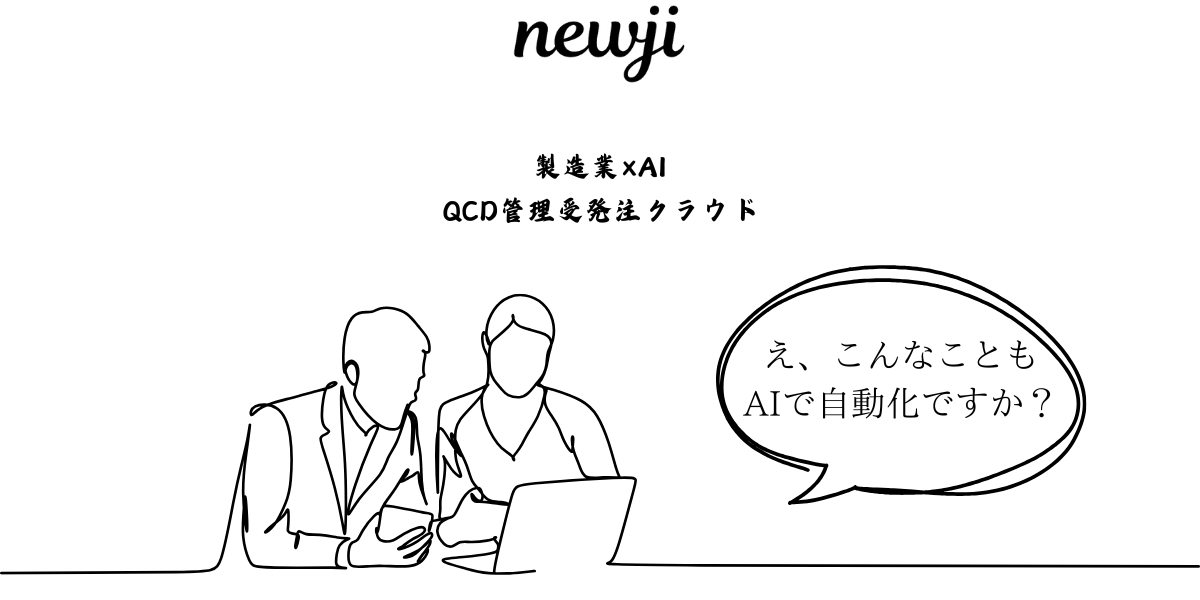
Key Points for High-Precision Part Manufacturing Using Grinding Technology
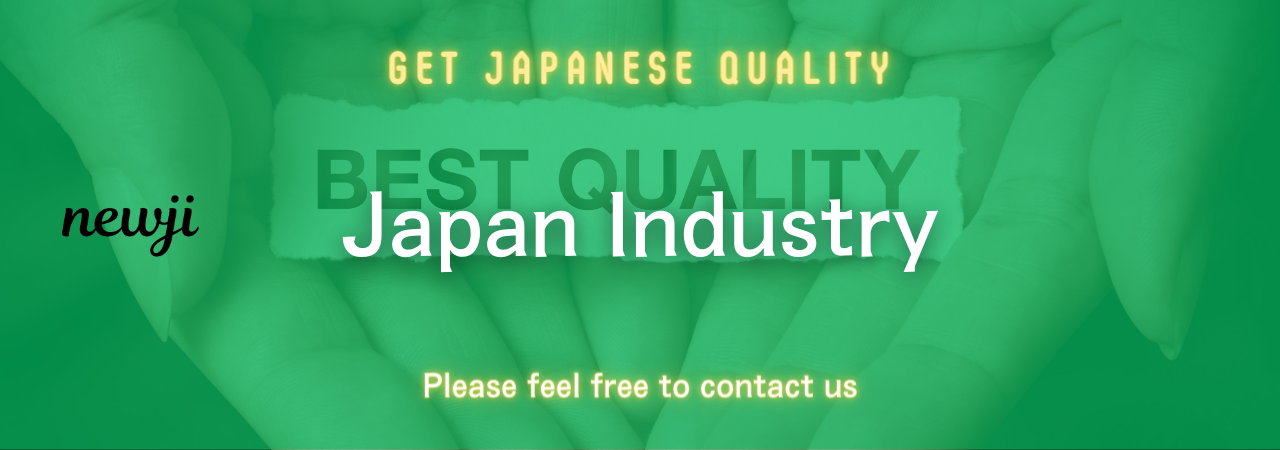
目次
Understanding High-Precision Part Manufacturing
High-precision part manufacturing is essential in various industries, including aerospace, medical, and automotive.
This meticulous process ensures that each component meets strict dimensional and functional standards.
One key technique used in achieving high-precision parts is grinding technology.
In this article, we will delve into the critical aspects of using grinding technology for manufacturing high-precision parts.
The Importance of Grinding Technology
Grinding technology plays a pivotal role in high-precision manufacturing.
This process uses abrasive wheels to remove material from workpieces, achieving tight tolerances and smooth surface finishes.
It’s particularly beneficial for parts requiring stringent geometrical accuracies and fine finishes, often impossible with other machining techniques.
High Precision and Geometric Accuracy
Grinding technology enables the production of parts with high dimensional accuracy.
This is crucial in industries where even minor deviations can lead to significant problems.
For instance, in the aerospace industry, high-precision parts are essential to ensure the safety and efficiency of aircraft.
Superb Surface Finish
Achieving a superior surface finish is another advantage of grinding technology.
The smooth surfaces produced through grinding reduce friction and wear, extending the life of components.
In the medical industry, for example, implants and surgical tools require exceptional surface finishes to ensure patient safety and device longevity.
Types of Grinding Techniques
Various grinding techniques are employed based on the material and desired outcome.
Each method offers distinct advantages, making it suitable for specific applications.
Surface Grinding
Surface grinding is a common technique used to produce flat surfaces.
The workpiece is secured on a table, and the grinder’s rotating wheel removes material, creating a smooth, precise surface.
This method is extensively used in creating machine parts and tools requiring minute flatness tolerances.
Cylindrical Grinding
Cylindrical grinding is ideal for shaping the external surfaces of cylindrical objects.
The workpiece rotates while being ground by a smaller wheel, ensuring uniform material removal.
Industries manufacturing components like shafts, axles, and spindles frequently rely on cylindrical grinding for precision and consistency.
Centerless Grinding
In centerless grinding, the workpiece is held between two wheels: a driving wheel and a grinding wheel.
This technique is advantageous for producing high-volume parts with consistent diameter.
Automotive industries, in particular, benefit from centerless grinding for producing components such as engine pistons and transmission parts.
Internal Grinding
Internal grinding is used to refine the internal surfaces of cylindrical workpieces.
A smaller grinding wheel is used to achieve precise inner diameters and smooth finishes.
This technique is often utilized in manufacturing components like bearings and precision tubes.
Factors Influencing Precision in Grinding
Achieving high precision in grinding requires careful consideration of various factors.
Understanding and controlling these variables ensures optimal results.
Grinding Wheel Selection
The choice of grinding wheel is critical in determining the quality of the final product.
Factors such as wheel material, grit size, and bonding should be selected based on the workpiece material and desired surface finish.
For instance, a finer grit wheel may be chosen for a smoother finish, while coarser grits are suited for rapid material removal.
Workpiece Material
Understanding the properties of the workpiece material is essential.
Different materials respond uniquely to grinding processes.
For instance, harder materials like hardened steel require specific wheel materials and grinding parameters to achieve precision without damaging the workpiece.
Machine Condition
The condition of the grinding machine significantly impacts the precision of the manufacturing process.
Regular maintenance and calibration are necessary to ensure machine accuracy.
Factors such as spindle stability, table movement, and wheel alignment must be meticulously checked and adjusted.
Cooling and Lubrication
Effective cooling and lubrication are crucial during grinding to prevent overheating, which can distort the workpiece and degrade the grinding wheel.
Using appropriate coolants and lubricants decreases friction and heat generation, ensuring the stability of tolerances and prolonging tool life.
Best Practices in High-Precision Grinding
Employing best practices consistently ensures the quality and precision of the ground parts, leading to superior end products.
Accurate Setup
Setting up the workpiece and grinding equipment accurately is essential.
Ensure precise alignment of the workpiece and secure it firmly to avoid vibrations or displacements during grinding.
Verify that the grinding wheel is properly balanced and aligned to maintain consistent contact with the workpiece.
Controlled Environment
Perform grinding operations in a controlled environment to minimize the impact of external factors such as temperature and humidity.
Fluctuations in these variables can affect the dimensions and surface integrity of the workpiece.
Maintain a stable temperature in the working area to prevent thermal expansion and contraction of materials.
Regular Monitoring and Inspection
Continuous monitoring and inspection during the grinding process help identify any deviations or issues early.
Use precision measurement tools like micrometers and coordinate measuring machines (CMM) to verify component dimensions.
Regularly inspect the grinding wheel condition and replace it when worn out to maintain consistent quality.
Skilled Workforce
A skilled and experienced workforce is invaluable in high-precision grinding.
Train operators thoroughly on machine handling, maintenance, and best practices.
Encourage a culture of attention to detail and pride in workmanship to achieve the highest standards of precision.
Conclusion
High-precision part manufacturing using grinding technology is a cornerstone in fields demanding exacting standards.
By understanding the significance of grinding technology, selecting appropriate techniques, and controlling influential factors, manufacturers can consistently produce precise components.
Employing best practices and fostering a skilled workforce ensures sustained excellence and reliability in high-precision manufacturing.
Stay ahead in the competitive landscape by mastering the art and science of grinding technology, ensuring your components meet the highest standards of accuracy and finish.
資料ダウンロード
QCD調達購買管理クラウド「newji」は、調達購買部門で必要なQCD管理全てを備えた、現場特化型兼クラウド型の今世紀最高の購買管理システムとなります。
ユーザー登録
調達購買業務の効率化だけでなく、システムを導入することで、コスト削減や製品・資材のステータス可視化のほか、属人化していた購買情報の共有化による内部不正防止や統制にも役立ちます。
NEWJI DX
製造業に特化したデジタルトランスフォーメーション(DX)の実現を目指す請負開発型のコンサルティングサービスです。AI、iPaaS、および先端の技術を駆使して、製造プロセスの効率化、業務効率化、チームワーク強化、コスト削減、品質向上を実現します。このサービスは、製造業の課題を深く理解し、それに対する最適なデジタルソリューションを提供することで、企業が持続的な成長とイノベーションを達成できるようサポートします。
オンライン講座
製造業、主に購買・調達部門にお勤めの方々に向けた情報を配信しております。
新任の方やベテランの方、管理職を対象とした幅広いコンテンツをご用意しております。
お問い合わせ
コストダウンが利益に直結する術だと理解していても、なかなか前に進めることができない状況。そんな時は、newjiのコストダウン自動化機能で大きく利益貢献しよう!
(Β版非公開)