- お役立ち記事
- Key points for implementing FMEA
Key points for implementing FMEA
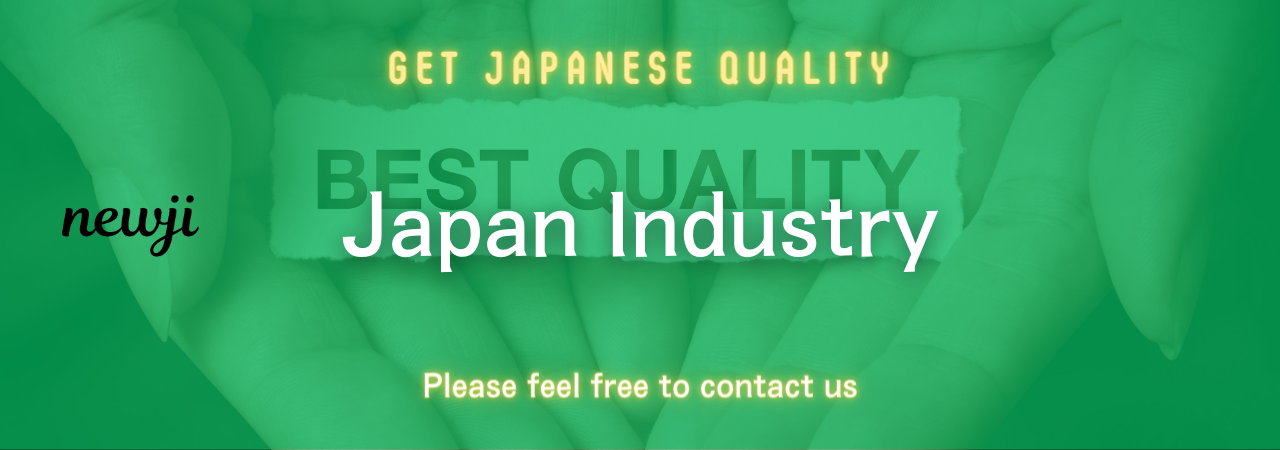
目次
Understanding FMEA
Failure Mode and Effects Analysis, commonly known as FMEA, is a systematic approach used to identify potential failures in a process, product, or system.
The primary goal is to understand what might go wrong, how it might happen, and what the impacts would be.
By pinpointing these potential issues early, teams can prioritize them and develop strategies to mitigate risks.
Understanding FMEA is crucial for any organization striving for high-quality standards and reduced risk in their operations.
This method helps in eliminating errors and improving overall reliability.
Benefits of FMEA
Implementing FMEA brings several benefits to an organization.
First, it enhances the quality of products and processes by identifying potential failures before they occur.
Second, it reduces costs associated with defects and failures by allowing companies to address issues early in the design or production phase.
Third, FMEA helps companies comply with industry standards and regulations, ensuring their products or processes meet required safety and quality standards.
Additionally, it fosters a culture of continuous improvement and teamwork as it encourages collaboration among cross-functional teams.
Overall, FMEA increases customer satisfaction and trust by delivering consistent, high-quality products and services.
Key Steps in Implementing FMEA
1. Assemble a Team
The first step in implementing FMEA is to assemble a cross-functional team.
This team should include members from various departments, such as design, engineering, manufacturing, quality assurance, and customer service.
Having diverse perspectives ensures a comprehensive analysis as different expertise contributes to identifying potential failures in different areas.
2. Define the Scope
Next, clearly define the scope of the FMEA process.
Identify the product, process, or system that will be analyzed.
Determining the scope helps focus efforts and resources on the areas that are most critical.
It sets boundaries and ensures that the analysis remains manageable and relevant.
3. Identify Potential Failure Modes
Once the scope is defined, brainstorm potential failure modes.
These are the different ways in which a process, product, or system could fail.
Use tools like brainstorming sessions, checklists, and past data analysis to gather information.
Encourage open communication and a non-judgmental environment to ensure everyone shares their insights.
4. Determine the Effects of Failures
For each identified failure mode, determine its effects.
Effects are the consequences of a failure on the product, customer, or process.
Consider asking questions like how the failure impacts the end user or what happens if the error reaches the production line.
5. Assign Severity Ratings
Assign a severity rating to each effect of failure.
The severity rating reflects the potential impact of a failure on a scale from low to high.
A higher rating indicates more severe consequences, prompting a need for immediate attention and action.
6. Identify Causes of Failures
Identify potential causes for each failure mode.
Understanding what might cause a failure is crucial for developing effective mitigation strategies.
Discuss and document all possible reasons, considering factors such as human error, machine failure, material defects, or environmental conditions.
7. Assign Occurrence Ratings
Once causes are identified, assign occurrence ratings.
This rating estimates the likelihood of each cause happening, using a scale from low to high.
High occurrence ratings indicate a higher probability of the failure mode happening, thereby requiring preventive measures.
8. Evaluate Detection Methods
Evaluate the current detection methods in place for identifying each failure mode.
Determine how effectively the current processes can detect the issue before it impacts the product or customer.
Rate the detection methods’ capability using a similar scale, where lower ratings suggest poor detectability.
9. Calculate the Risk Priority Number (RPN)
Calculate the Risk Priority Number (RPN) by multiplying the severity, occurrence, and detection ratings together for each failure mode.
The RPN helps prioritize which failures require immediate attention based on their overall risk.
Focus on failure modes with higher RPNs first to develop action plans to address them.
10. Develop and Implement Action Plans
For each prioritized failure mode, develop and implement action plans to mitigate risks.
Actions may include design changes, additional quality checks, staff training, or improved processes.
Ensure the plans are specific, measurable, and achievable, and assign responsibilities to team members to ensure accountability.
Continual Improvement and Review
Implementing FMEA is not a one-time task but a continual process.
Periodically review the FMEA results to assess the effectiveness of the implemented actions and make improvements as necessary.
Encourage a culture where team members routinely identify potential failures and use the FMEA framework to address them.
Incorporating lessons learned from past failures and successes into future projects ensures continuous improvement.
Conclusion
FMEA is a powerful tool for enhancing quality, reducing costs, and improving customer satisfaction by proactively addressing potential failures.
By following key steps such as assembling a cross-functional team, identifying potential failure modes, and developing action plans, organizations can effectively implement FMEA.
Through continual improvement and regular review, companies can maintain high standards and minimize risks, ensuring the delivery of reliable and high-quality products and services.
資料ダウンロード
QCD調達購買管理クラウド「newji」は、調達購買部門で必要なQCD管理全てを備えた、現場特化型兼クラウド型の今世紀最高の購買管理システムとなります。
ユーザー登録
調達購買業務の効率化だけでなく、システムを導入することで、コスト削減や製品・資材のステータス可視化のほか、属人化していた購買情報の共有化による内部不正防止や統制にも役立ちます。
NEWJI DX
製造業に特化したデジタルトランスフォーメーション(DX)の実現を目指す請負開発型のコンサルティングサービスです。AI、iPaaS、および先端の技術を駆使して、製造プロセスの効率化、業務効率化、チームワーク強化、コスト削減、品質向上を実現します。このサービスは、製造業の課題を深く理解し、それに対する最適なデジタルソリューションを提供することで、企業が持続的な成長とイノベーションを達成できるようサポートします。
オンライン講座
製造業、主に購買・調達部門にお勤めの方々に向けた情報を配信しております。
新任の方やベテランの方、管理職を対象とした幅広いコンテンツをご用意しております。
お問い合わせ
コストダウンが利益に直結する術だと理解していても、なかなか前に進めることができない状況。そんな時は、newjiのコストダウン自動化機能で大きく利益貢献しよう!
(Β版非公開)