- お役立ち記事
- Key points for introducing an automatic ordering system to increase procurement efficiency in the manufacturing industry
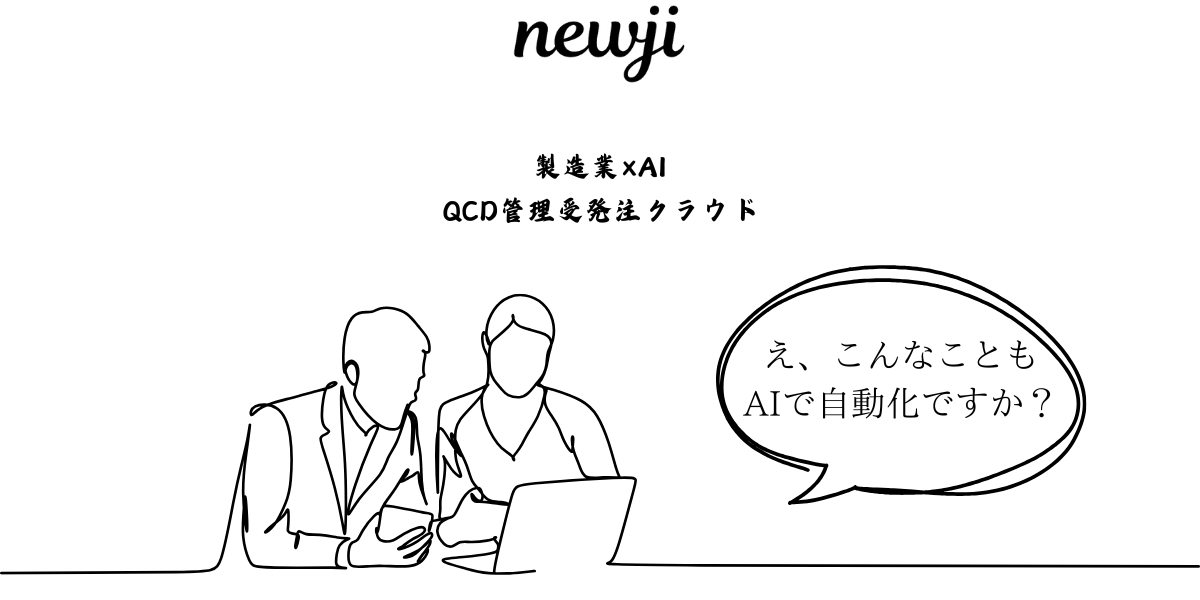
Key points for introducing an automatic ordering system to increase procurement efficiency in the manufacturing industry
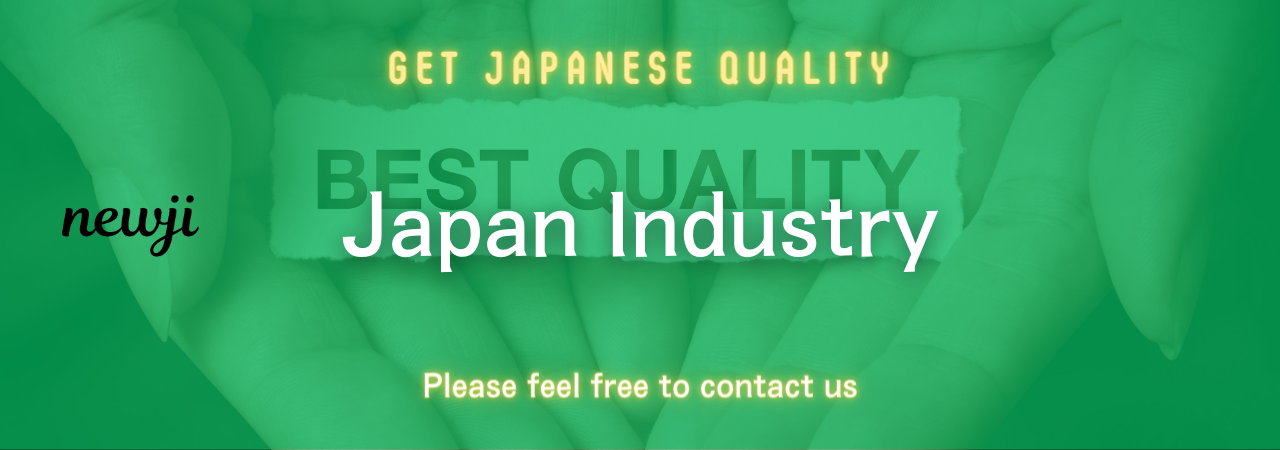
目次
Understanding Automatic Ordering Systems
In the manufacturing industry, efficiency is a crucial factor that significantly impacts the bottom line.
One area where efficiency can be dramatically improved is in procurement, specifically through the introduction of automatic ordering systems.
These systems streamline the procurement process, enabling manufacturers to optimize supply chain operations and reduce costs.
In this article, we’ll explore key points to consider when introducing an automatic ordering system to increase procurement efficiency.
The Benefits of Automatic Ordering Systems
Automatic ordering systems bring a host of benefits to manufacturers.
Primarily, they help in reducing human errors that are often inevitable in manual order processing.
This not only ensures accuracy in order quantities but also reduces delays caused by errors that require correction.
Moreover, these systems efficiently manage inventory by predicting demand and automatically placing orders for necessary materials. This predictive ability ensures that materials are procured just in time, minimizing excess inventory and lowering storage costs.
Automatic ordering systems also enhance supplier relationships.
By generating timely and accurate orders, these systems improve communication with suppliers, leading to better negotiation outcomes and consistent supply.
The increased reliability and predictability in ordering foster a strong partnership ambiance with suppliers.
Streamlined Workflows
Another advantage of automatic ordering systems is the streamlining of procurement workflows.
Traditional procurement processes can be cumbersome with layers of approval and extensive paperwork.
With automation, much of this time-consuming bureaucracy is eliminated, allowing procurement professionals to focus on strategic initiatives instead of administrative tasks.
The increased efficiency also allows for the reallocation of resources to more value-added activities, enhancing productivity across the organization.
Key Considerations for Implementation
While the benefits are clear, successful implementation of an automatic ordering system requires careful planning and execution.
Below are key considerations that manufacturers should keep in mind:
Assessing Current Processes
Before implementing an automatic ordering system, it is essential to thoroughly assess the current procurement processes.
Identify areas that require improvement and determine specific pain points that an automated system can address.
Understanding your starting point helps in selecting a system that best fits your needs.
Choosing the Right System
Selecting the appropriate automatic ordering system is critical.
There are various solutions available in the market, each offering different features and capabilities.
Consider factors such as ease of integration with existing systems, scalability, user-friendliness, and cost.
Seeking input from stakeholders across departments can also provide valuable insights into choosing the right system.
Data Integration and Management
Automatic ordering relies heavily on accurate data.
Ensuring that the system has access to real-time, accurate data is crucial for its successful operation.
This may involve integrating the system with existing enterprise resource planning (ERP) systems or other databases to provide a seamless flow of information.
Manufacturers should also have a plan in place for data management and maintenance.
Regular updates and validation are necessary to maintain data integrity and prevent errors in the ordering process.
Training and Change Management
Introducing new technology requires adequate training for all users involved.
Ensure that your team is well-equipped to utilize the system effectively by providing comprehensive training sessions.
Change management is equally important.
Communicate the benefits and capabilities of the new system clearly to all stakeholders to promote acceptance and minimize resistance.
A phased rollout may also be beneficial, allowing for adjustments based on feedback and smooth transition from manual to automated processes.
Evaluating Success
Post-implementation, it’s important to evaluate the system’s performance regularly.
Set measurable criteria to assess improvements in procurement efficiency, such as order accuracy, reduced lead times, and cost savings.
Regular reviews will help identify areas for optimization and adjustment to continually improve procurement processes.
Conclusion
Introducing an automatic ordering system is a strategic decision that can substantially enhance procurement efficiency in the manufacturing industry.
The transition requires careful consideration of current processes, system selection, data management, and training.
However, once implemented effectively, an automatic ordering system can lead to improved accuracy, reduced costs, and strengthened supplier relationships, driving overall operational success.
By following the key points outlined in this article, manufacturers can maximize the benefits of automation in procurement and remain competitive in an ever-evolving industry landscape.
資料ダウンロード
QCD調達購買管理クラウド「newji」は、調達購買部門で必要なQCD管理全てを備えた、現場特化型兼クラウド型の今世紀最高の購買管理システムとなります。
ユーザー登録
調達購買業務の効率化だけでなく、システムを導入することで、コスト削減や製品・資材のステータス可視化のほか、属人化していた購買情報の共有化による内部不正防止や統制にも役立ちます。
NEWJI DX
製造業に特化したデジタルトランスフォーメーション(DX)の実現を目指す請負開発型のコンサルティングサービスです。AI、iPaaS、および先端の技術を駆使して、製造プロセスの効率化、業務効率化、チームワーク強化、コスト削減、品質向上を実現します。このサービスは、製造業の課題を深く理解し、それに対する最適なデジタルソリューションを提供することで、企業が持続的な成長とイノベーションを達成できるようサポートします。
オンライン講座
製造業、主に購買・調達部門にお勤めの方々に向けた情報を配信しております。
新任の方やベテランの方、管理職を対象とした幅広いコンテンツをご用意しております。
お問い合わせ
コストダウンが利益に直結する術だと理解していても、なかなか前に進めることができない状況。そんな時は、newjiのコストダウン自動化機能で大きく利益貢献しよう!
(Β版非公開)