- お役立ち記事
- Key points for machine/equipment condition monitoring technology, life prediction, and longevity
月間76,176名の
製造業ご担当者様が閲覧しています*
*2025年3月31日現在のGoogle Analyticsのデータより
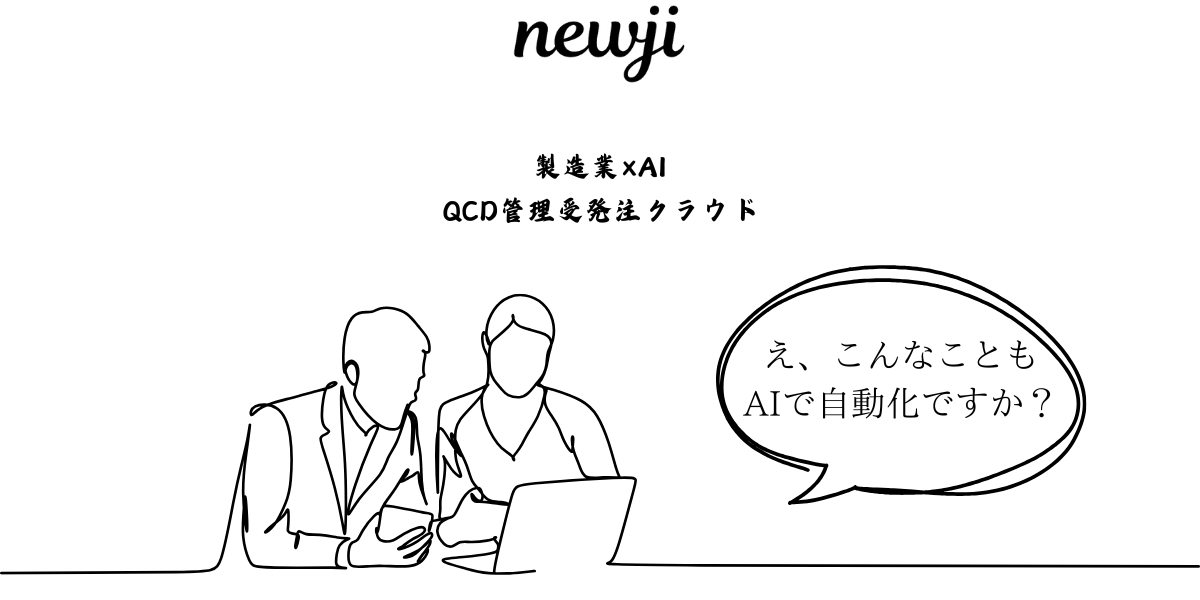
Key points for machine/equipment condition monitoring technology, life prediction, and longevity
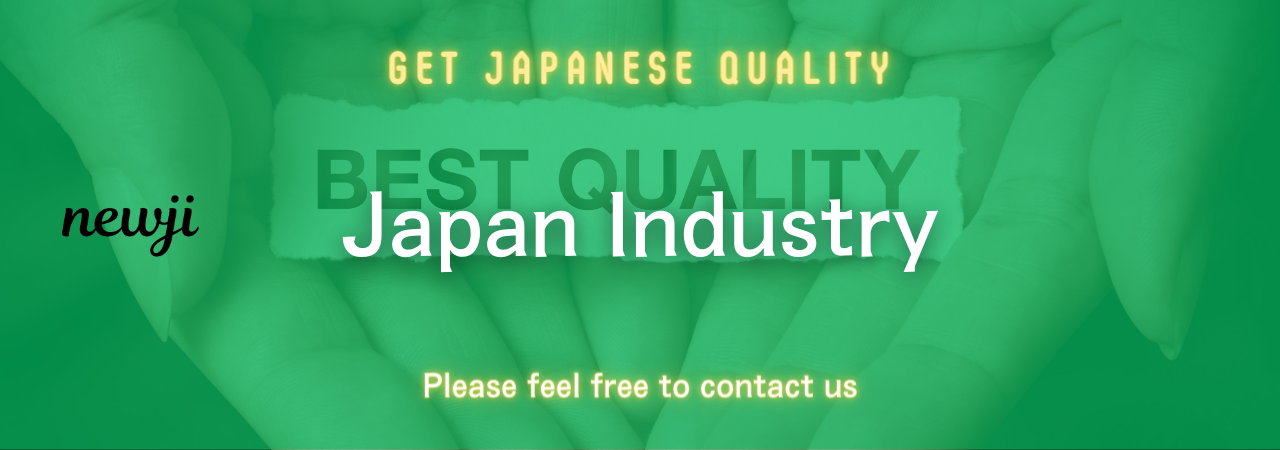
目次
Understanding Condition Monitoring Technology
Condition monitoring technology is a critical aspect of maintaining machinery and equipment in optimal working condition.
It involves the process of monitoring the operational parameters of equipment to identify significant changes that may indicate a developing fault.
By early identification of potential issues, maintenance can be scheduled to prevent unexpected failures, thereby enhancing productivity and safety.
The primary goal of condition monitoring is to minimize downtime and extend the lifespan of machinery.
This is achieved through continuous observation and analysis of various parameters such as vibration, temperature, and noise levels.
Sophisticated sensors and data acquisition systems are utilized to gather the data for analysis.
Benefits of Condition Monitoring
One of the key benefits of condition monitoring technology is the ability to prevent costly downtimes.
Predictive maintenance, enabled by condition monitoring, helps in identifying issues before they lead to equipment failure.
This proactive approach not only saves time and money but also ensures that machinery operates at peak efficiency.
Moreover, condition monitoring can extend the life of equipment.
By understanding the wear and tear mechanisms and addressing them promptly, the overall lifespan of machinery can be increased.
Companies can thus maximize their investment in equipment and reduce the frequency of costly replacements.
Additionally, condition monitoring plays a crucial role in improving safety.
By identifying potential failures before they occur, it helps prevent accidents and ensures the safety of personnel and processes.
Techniques and Tools for Monitoring
Various techniques and tools are employed in condition monitoring to cater to different types of equipment and operational environments.
One such method is vibration analysis, which is highly effective in detecting imbalances and misalignments in rotating machinery.
By analyzing the vibration patterns, maintenance teams can identify bearings or gears that are likely to fail.
Another common method is thermal imaging.
It involves using an infrared camera to detect unusual heat patterns in equipment.
Anomalies in temperature distribution can be an early indicator of problems such as electrical faults or mechanical friction.
Ultrasonic testing is also popular, particularly in detecting leaks and mechanical defects.
This technique uses high-frequency sound waves to detect anomalies within the internal structure of materials.
Implementing a Condition Monitoring System
To successfully implement a condition monitoring system, it is essential to start by identifying the critical machinery and equipment that need monitoring.
This involves assessing the potential impact of their failure on production and safety.
Next, selecting the appropriate monitoring techniques and tools is crucial.
This choice should be based on the specific characteristics of the equipment and the environmental conditions in which they operate.
Integration of the condition monitoring system with existing maintenance management systems can enhance decision-making processes.
Data from condition monitoring systems can be analyzed to forecast maintenance needs and plan interventions effectively.
Training personnel in the use of condition monitoring equipment and analysis of data is also vital.
Technical staff must understand how to use the monitoring tools and interpret the data to make informed maintenance decisions.
Life Prediction and Longevity of Equipment
Predicting the useful life of machinery is a fundamental aspect of condition monitoring.
Life prediction involves estimating the remaining useful life of equipment based on wear and tear data.
This helps in planning maintenance schedules and lifecycle management.
Factors Influencing Equipment Longevity
Several factors influence the longevity of machinery and equipment.
These include operating conditions, maintenance practices, and the quality of installation and materials used.
Proper installation and adherence to operational guidelines can significantly impact equipment lifespan.
Regular and effective maintenance practices ensure that machines operate within their optimal performance range, reducing the risk of premature failure.
Environmental factors, such as temperature, humidity, and exposure to harsh conditions, also play a role in how long equipment lasts.
Choosing materials and designs that can withstand the specific conditions of operation is crucial for maintaining longevity.
Maximizing Equipment Lifespan
To maximize the lifespan of machinery, it is important to regularly review and update maintenance schedules based on monitoring data.
Early detection of issues through condition monitoring should lead to timely maintenance interventions.
Furthermore, investing in quality components and ensuring proper installation can significantly extend equipment life.
Using proven, high-quality parts can prevent frequent breakdowns and associated maintenance costs.
Finally, adapting operational practices to reduce stress on equipment can also enhance its longevity.
This involves ensuring that machinery is not operated beyond its capacity or under unsuitable conditions.
In conclusion, machine and equipment condition monitoring technology is an essential component of modern maintenance strategies.
By employing the appropriate monitoring techniques and systems, companies can predict potential failures, optimize maintenance schedules, and extend the working life of their machinery.
This proactive approach not only boosts productivity but also secures personnel safety and operational efficiency.
資料ダウンロード
QCD管理受発注クラウド「newji」は、受発注部門で必要なQCD管理全てを備えた、現場特化型兼クラウド型の今世紀最高の受発注管理システムとなります。
ユーザー登録
受発注業務の効率化だけでなく、システムを導入することで、コスト削減や製品・資材のステータス可視化のほか、属人化していた受発注情報の共有化による内部不正防止や統制にも役立ちます。
NEWJI DX
製造業に特化したデジタルトランスフォーメーション(DX)の実現を目指す請負開発型のコンサルティングサービスです。AI、iPaaS、および先端の技術を駆使して、製造プロセスの効率化、業務効率化、チームワーク強化、コスト削減、品質向上を実現します。このサービスは、製造業の課題を深く理解し、それに対する最適なデジタルソリューションを提供することで、企業が持続的な成長とイノベーションを達成できるようサポートします。
製造業ニュース解説
製造業、主に購買・調達部門にお勤めの方々に向けた情報を配信しております。
新任の方やベテランの方、管理職を対象とした幅広いコンテンツをご用意しております。
お問い合わせ
コストダウンが利益に直結する術だと理解していても、なかなか前に進めることができない状況。そんな時は、newjiのコストダウン自動化機能で大きく利益貢献しよう!
(β版非公開)