- お役立ち記事
- Key points for preventing quality problems through reliability testing and failure analysis of electronic components
月間76,176名の
製造業ご担当者様が閲覧しています*
*2025年3月31日現在のGoogle Analyticsのデータより
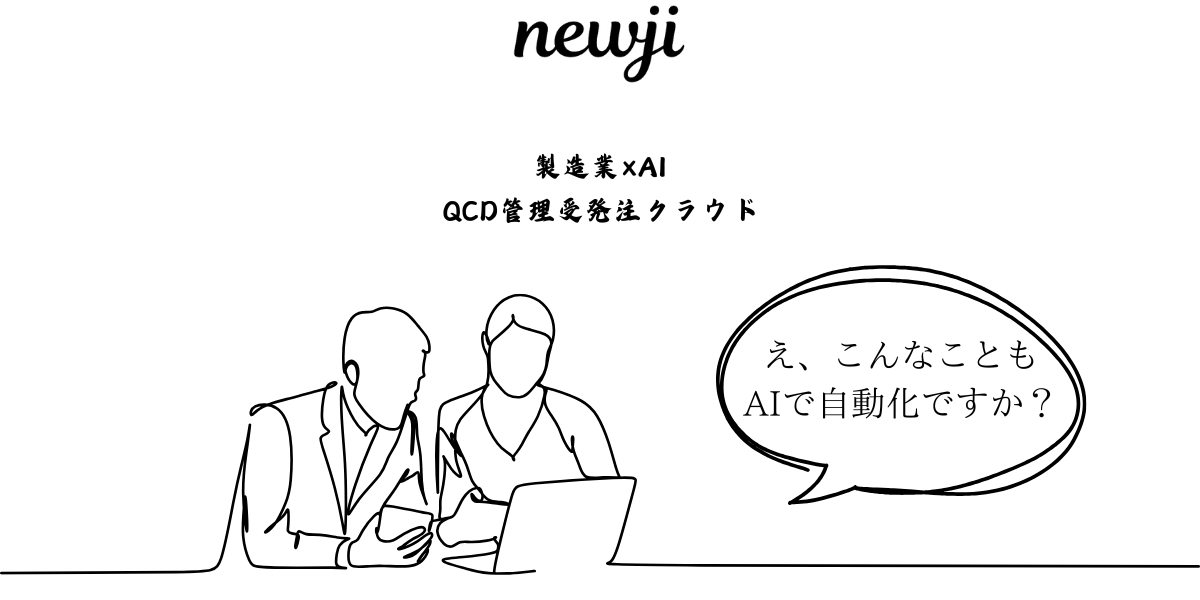
Key points for preventing quality problems through reliability testing and failure analysis of electronic components
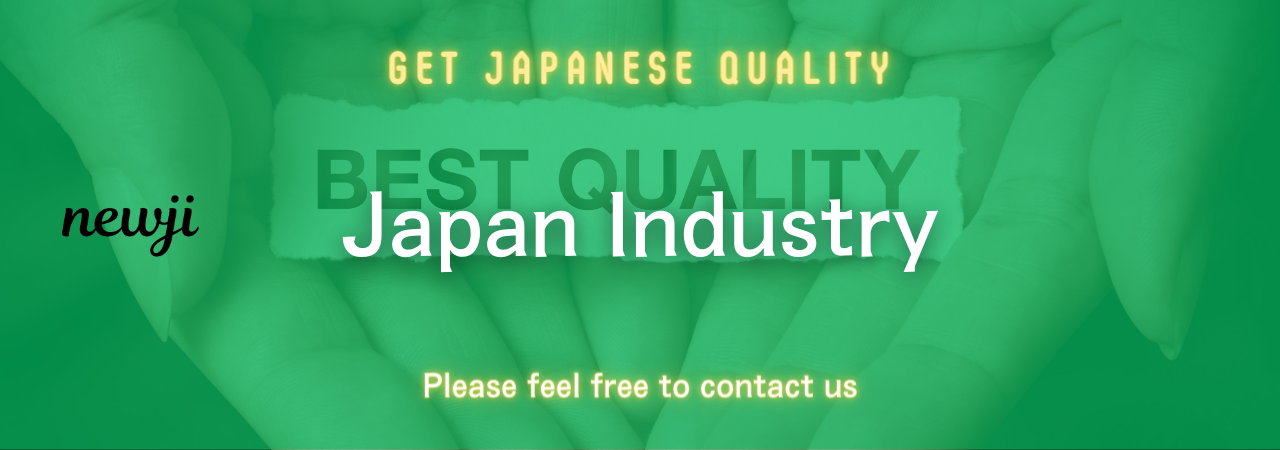
目次
Understanding Reliability Testing
Reliability testing is a crucial process in the electronic components industry.
It measures how well a component can perform under various conditions over time.
The objective is to ensure that electronic components will function as intended without failure.
Reliability testing involves replicating real-life conditions in a controlled environment.
By doing so, manufacturers can predict potential failures and mitigate them before they cause problems in actual usage.
Types of Reliability Testing
There are several types of reliability tests conducted to uncover any weaknesses in electronic components.
Temperature Testing
Temperature testing subjects electronic components to extreme hot and cold environments.
This helps assess their performance in varying climates.
Temperature cycling tests move components from high to low temperatures to expose potential material weaknesses.
Humidity Testing
Humidity testing evaluates components in high moisture environments.
The purpose is to identify any potential for corrosion or damage due to moisture that could impair functioning.
Manufacturers often use humidity chambers to simulate these conditions over extended periods.
Vibration Testing
Vibration testing simulates the vibrational forces that components experience during transit or operation.
It assesses whether a component can withstand physical shocks and movements.
By identifying these vulnerabilities early, manufacturers can reinforce components and ensure durability.
Mechanical Shock Testing
Mechanical shock testing provides insight into how components react to sudden impacts or drops.
It mimics real-life situations where accidental drops can occur.
These tests are crucial for components integral to devices that undergo frequent handling or transportation.
The Role of Failure Analysis
Failure analysis complements reliability testing by identifying the root cause of defects.
It investigates why a component failed and how it can be improved.
Failure analysis encompasses a variety of techniques, from simple visual inspections to advanced electronic diagnostics.
Visual Inspection
Visual inspections are the initial step in failure analysis.
They involve examining the component for visible defects such as cracks, discoloration, or burns.
Often, visual clues lead analysts to suspect certain types of electrical failures.
Electrical Testing
Electrical testing goes beyond visual analysis to determine functional problems.
Techniques like circuit analysis and signal testing help evaluate the electrical performance of components.
These tests can pinpoint failures at the microscopic level that are not visible to the naked eye.
Microscopy and Surface Analysis
Advanced failure analysis employs microscopy and surface analysis to examine the component’s microstructure.
These tools can reveal cracks and material anomalies causing failures.
Techniques like scanning electron microscopy (SEM) provide high-resolution images of the component’s surface.
Preventing Quality Problems
Combining reliability testing and failure analysis is key to preventing quality issues in electronic components.
Early Detection
Early detection of potential issues is paramount in preventing quality problems.
Reliability testing serves as a preemptive strike against future failures.
By subjecting components to rigorous testing, manufacturers can catch defects long before products reach the market.
Continuous Improvement
Reliability testing and failure analysis support continuous improvement.
They provide invaluable data that informs design changes and material selection.
As manufacturers learn from past failures, they can innovate more robust and reliable components for consumers.
Cost Efficiency
Investing in reliability testing and failure analysis can lead to significant cost savings.
By identifying potential failures early, companies can prevent costly recalls and repairs.
This proactive approach enhances a company’s reputation and consumer trust by ensuring only high-quality products are delivered to the market.
Conclusion
Reliability testing and failure analysis are integral processes in the electronics industry.
They ensure that electronic components can withstand various conditions without failure, leading to high-quality products.
By implementing rigorous testing regimes and learning from failures, manufacturers can create components that meet the highest reliability standards.
This proactive approach not only enhances product quality but also safeguards a company’s reputation and bottom line.
資料ダウンロード
QCD管理受発注クラウド「newji」は、受発注部門で必要なQCD管理全てを備えた、現場特化型兼クラウド型の今世紀最高の受発注管理システムとなります。
ユーザー登録
受発注業務の効率化だけでなく、システムを導入することで、コスト削減や製品・資材のステータス可視化のほか、属人化していた受発注情報の共有化による内部不正防止や統制にも役立ちます。
NEWJI DX
製造業に特化したデジタルトランスフォーメーション(DX)の実現を目指す請負開発型のコンサルティングサービスです。AI、iPaaS、および先端の技術を駆使して、製造プロセスの効率化、業務効率化、チームワーク強化、コスト削減、品質向上を実現します。このサービスは、製造業の課題を深く理解し、それに対する最適なデジタルソリューションを提供することで、企業が持続的な成長とイノベーションを達成できるようサポートします。
製造業ニュース解説
製造業、主に購買・調達部門にお勤めの方々に向けた情報を配信しております。
新任の方やベテランの方、管理職を対象とした幅広いコンテンツをご用意しております。
お問い合わせ
コストダウンが利益に直結する術だと理解していても、なかなか前に進めることができない状況。そんな時は、newjiのコストダウン自動化機能で大きく利益貢献しよう!
(β版非公開)