- お役立ち記事
- Key Points for Procuring Parts and Equipment Supporting Advanced Measurement Technology
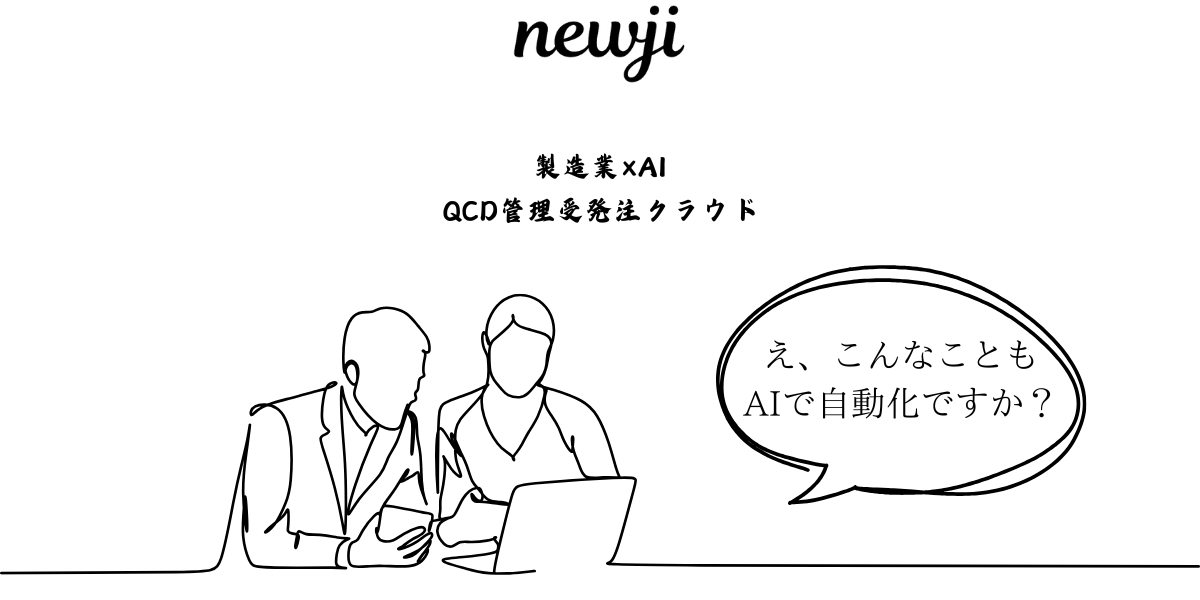
Key Points for Procuring Parts and Equipment Supporting Advanced Measurement Technology
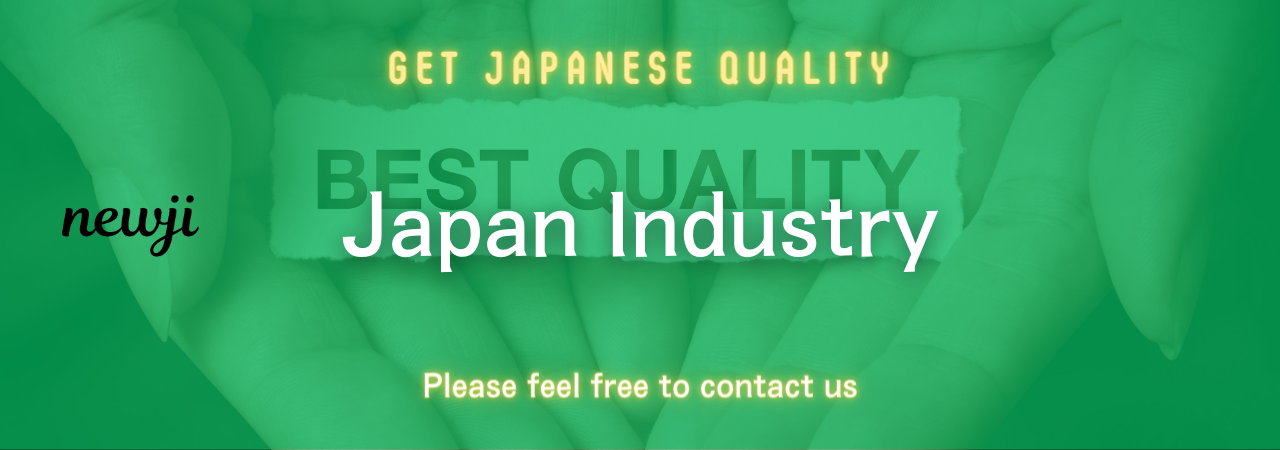
The demand for advanced measurement technology is increasing rapidly across various industries.
Precision instruments, sensors, and devices are critical for data accuracy in numerous applications, from industrial manufacturing to scientific research.
Procuring the right parts and equipment is crucial to ensuring the effectiveness and reliability of these high-tech systems.
Understanding the key considerations for procurement can help organizations secure the best resources at optimal costs.
目次
Understanding Measurement Technology Needs
Before procuring any parts or equipment, it is essential to have a clear understanding of your measurement technology needs.
The specific requirements will vary depending on the application, accuracy tolerance, frequency, and environmental conditions.
For instance, laboratory environments might need different tools compared to those used in harsh industrial settings.
Identify the Specific Application
Identifying the specific application for which the measurement technology is needed is the first step.
This means understanding the type of measurements (electrical, mechanical, chemical, etc.) that need to be performed.
By knowing the purpose, you can start to narrow down the options for the equipment and parts required.
Determine Accuracy and Precision Requirements
Every application has different requirements for accuracy and precision.
High-precision tasks may need equipment with tighter tolerances and advanced features to ensure data reliability.
Ensure the equipment you choose can meet your desired accuracy standards.
Consider Environmental Factors
Environmental factors play a significant role in the performance of measurement devices.
Extreme temperatures, humidity, and exposure to chemicals can affect the accuracy and longevity of the parts.
Ensure that the equipment you select can operate effectively within the environmental conditions where they will be used.
Key Factors in Choosing Parts and Equipment
Several factors should be considered when selecting parts and equipment for advanced measurement technology.
These include quality, compatibility, cost, supplier reliability, and support services.
Quality and Durability
Quality is paramount when it comes to measurement technology.
High-quality parts ensure longevity and reliable performance, reducing the need for frequent replacements and maintenance.
Look for equipment that meets industry standards and has certifications to guarantee their quality and durability.
Compatibility with Existing Systems
Compatibility with existing systems can save time and costs in integration and setup.
Before purchasing, ensure that the parts and equipment are compatible with your current technology and infrastructure.
Check the specifications and consult with the supplier or manufacturer if necessary.
Cost-Effectiveness
While high-quality parts often come at a higher price, consider the long-term cost benefits of investing in superior equipment.
Cheaper alternatives may lead to frequent replacements and downtime, ultimately costing more in the long run.
Perform a total cost of ownership (TCO) analysis to make an informed decision.
Supplier Reliability and Support
Working with a reliable supplier who provides excellent support services is equally important.
Reliable suppliers ensure timely delivery and can offer assistance if any issues arise with the parts and equipment.
Check reviews, ask for references, and evaluate their service and support policies before making a decision.
Navigating the Procurement Process
The procurement process can be complex, but following a structured approach can simplify it.
Breaking the procurement process into manageable steps ensures that nothing is overlooked and that procurement is done efficiently.
Market Research and Supplier Selection
Start by conducting thorough market research to identify potential suppliers.
Look for suppliers with a good reputation, extensive experience, and a range of products that meet your needs.
Visit trade shows, consult industry publications, and use online resources to gather information.
Once you have a list of potential suppliers, evaluate them based on quality, cost, and reliability.
Request for Quotation (RFQ)
Draft a detailed Request for Quotation (RFQ) document that includes all your specific requirements, including technical specifications, quantity, delivery timelines, and any other essential criteria.
Send the RFQ to the shortlisted suppliers and await their responses.
Evaluate the quotations received based on the total cost, including any associated fees such as shipping and handling.
Negotiation and Finalization
Engage in negotiations with the selected suppliers to finalize the best possible deal.
Discuss terms of payment, delivery schedules, and warranty conditions.
Ensure that all agreements are clearly documented to avoid future disputes.
Purchase Order and Delivery
Once negotiations are completed, issue a purchase order (PO) to the selected supplier.
Monitor the delivery process to ensure that the parts and equipment arrive on time and are in the specified condition.
Conduct an inspection upon arrival to confirm that everything meets your requirements.
Ensuring Long-Term Success
Procuring the right parts and equipment is just the first step.
Ensuring long-term success requires maintaining and periodically evaluating the performance of the measurement technology to adapt to any evolving needs.
Regular Maintenance and Calibration
Regular maintenance and calibration are crucial to keeping measurement technology in optimal working condition.
Scheduled maintenance helps identify potential issues before they become major problems, reducing downtime and enhancing accuracy.
Ensure that calibration protocols are followed as per the manufacturer’s recommendations.
Continuous Training and Upgradation
Investing in continuous training for the personnel handling the measurement equipment ensures that they are proficient in using the technology effectively.
Additionally, stay updated with the latest advancements in measurement technology.
Upgrading the equipment periodically can significantly improve performance and capability.
Periodic Performance Assessment
Conduct periodic performance assessments to validate the accuracy and reliability of the measurement systems.
These assessments help in understanding the effectiveness of the equipment and identifying any areas that may need improvement.
Regular assessments also support compliance with industry standards and regulatory requirements.
In conclusion, procuring parts and equipment for advanced measurement technology requires a thorough understanding of application needs, careful selection based on key factors, and a structured procurement process.
By prioritizing quality, compatibility, and supplier reliability, and by ensuring regular maintenance, your organization can achieve accurate and reliable measurement results consistently.
資料ダウンロード
QCD調達購買管理クラウド「newji」は、調達購買部門で必要なQCD管理全てを備えた、現場特化型兼クラウド型の今世紀最高の購買管理システムとなります。
ユーザー登録
調達購買業務の効率化だけでなく、システムを導入することで、コスト削減や製品・資材のステータス可視化のほか、属人化していた購買情報の共有化による内部不正防止や統制にも役立ちます。
NEWJI DX
製造業に特化したデジタルトランスフォーメーション(DX)の実現を目指す請負開発型のコンサルティングサービスです。AI、iPaaS、および先端の技術を駆使して、製造プロセスの効率化、業務効率化、チームワーク強化、コスト削減、品質向上を実現します。このサービスは、製造業の課題を深く理解し、それに対する最適なデジタルソリューションを提供することで、企業が持続的な成長とイノベーションを達成できるようサポートします。
オンライン講座
製造業、主に購買・調達部門にお勤めの方々に向けた情報を配信しております。
新任の方やベテランの方、管理職を対象とした幅広いコンテンツをご用意しております。
お問い合わせ
コストダウンが利益に直結する術だと理解していても、なかなか前に進めることができない状況。そんな時は、newjiのコストダウン自動化機能で大きく利益貢献しよう!
(Β版非公開)