- お役立ち記事
- Key points for production line layout design and productivity improvement for automation
月間76,176名の
製造業ご担当者様が閲覧しています*
*2025年3月31日現在のGoogle Analyticsのデータより
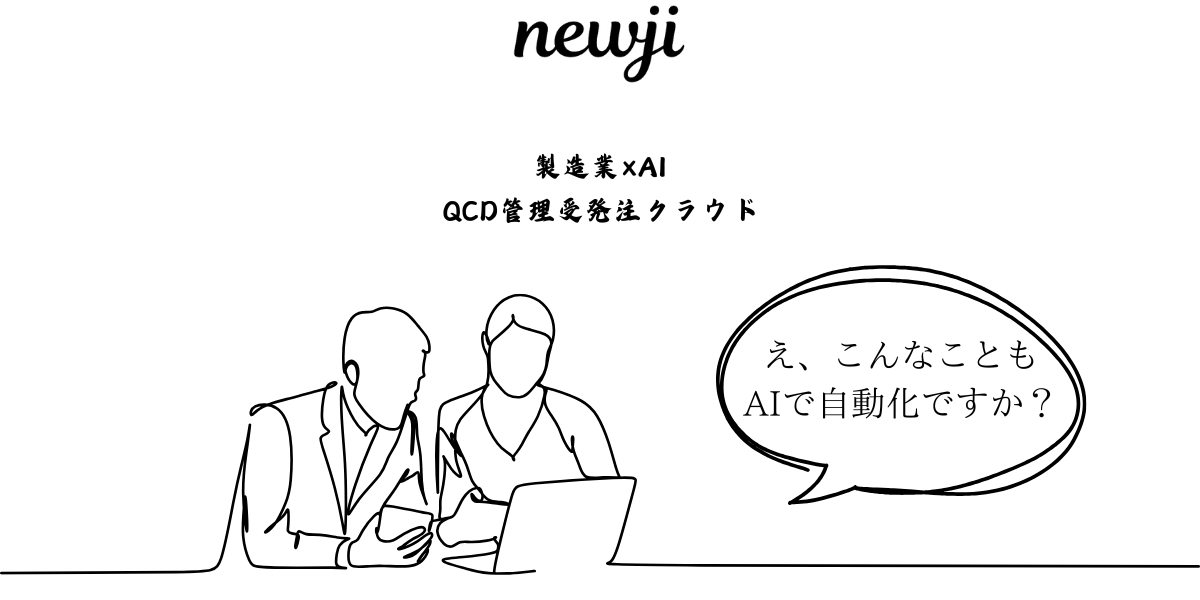
Key points for production line layout design and productivity improvement for automation
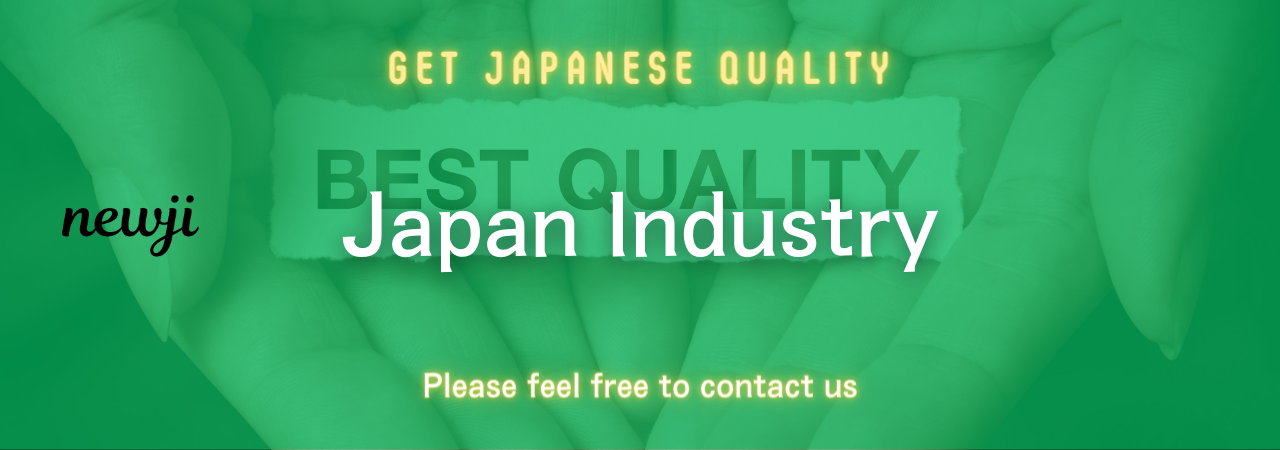
目次
The Importance of Production Line Layout
In today’s competitive manufacturing environment, the efficiency of your production line is critical.
An optimized production line layout can significantly improve productivity, reduce costs, and increase output.
Whether you’re just setting up or looking to improve an existing line, understanding production line layout is essential.
The production line layout is more than just the physical arrangement of machinery and workstations.
It involves strategically planning every element to enhance the flow of materials, information, and workforce.
When well-executed, it minimizes waste, shortens delivery times, and boosts overall efficiency.
Core Principles of Production Line Layout Design
To create an effective production line layout, there are several core principles you should consider.
1. Workflow Efficiency
Workflow is the heart of any production line.
Design your layout in a linear fashion where processes seamlessly transition from one to the next.
This minimizes unnecessary movements and potential bottlenecks.
2. Flexibility and Adaptability
In an ever-evolving market, flexibility is key.
Your production line layout should be designed to easily adapt to changes in product design, production volumes, and technology upgrades.
Modular design principles can be beneficial, allowing sections of the line to be reconfigured quickly.
3. Space Utilization
Optimal use of space is essential for efficiency.
Consider vertical solutions if horizontal space is limited.
Properly utilizing your available space can improve operator comfort and safety, enhance workflow, and increase storage options.
4. Worker Safety and Ergonomics
The safety and comfort of your workforce are paramount.
Ergonomic designs reduce the risk of injury and fatigue, contributing to enhanced productivity.
Ensure that walkways are clear and that workstations are designed to meet ergonomic standards.
Tips to Improve Productivity Through Automation
Automation is a powerful tool in boosting production line productivity.
Here are some strategies to consider when integrating automation.
1. Identify Repetitive Tasks
Evaluate the production line to identify tasks that are repetitive and can be automated.
This can free up valuable human resources for more complex tasks, improving both efficiency and morale.
2. Invest in Smart Technology
Incorporating smart technology, such as IoT devices, can provide real-time data and insights into your production processes.
This data can be invaluable for identifying inefficiencies and making informed decisions about process improvements.
3. Utilize Robotics
Robotics can handle tasks from assembling to packaging with precision and speed.
Robots can work continuously, significantly reducing production times.
However, it’s vital to consider the initial investment and ongoing maintenance costs.
4. Integrate Machine Learning
Machine learning can optimize processes by predicting and preventing maintenance issues, analyzing production bottlenecks, and providing strategic insights.
With machine learning, your production line can become smarter over time, continuously improving productivity.
The Role of Continuous Improvement
A production line layout is never truly complete.
Continuous improvement should be a cornerstone of your manufacturing strategy.
Regularly analyze production data to spot trends and areas for enhancement.
1. Employee Feedback
Encourage employees to provide feedback on the production line.
Often, the best insights come from those who work within the system daily.
Create an open environment where suggestions are valued and considered.
2. Regular Maintenance Review
Regularly scheduled maintenance can prevent unexpected downtimes and keep equipment running at peak efficiency.
Use a proactive approach by scheduling maintenance based on machine usage patterns rather than a fixed calendar.
3. Benchmarking and Performance Metrics
Use benchmarking to compare your production line performance against industry standards or competitors.
Track key performance metrics, such as cycle times and defect rates, to identify areas needing improvement.
Conclusion
Designing a production line layout and enhancing its productivity through automation requires careful consideration and planning.
By focusing on workflow efficiency, flexibility, space utilization, and safety, you can create a layout that supports growth and change.
Embracing technology, such as robotics and machine learning, opens up new avenues for productivity improvements.
Remember, continuous improvement isn’t just a practice—it’s a culture.
Engage your team, leverage technology, and consistently refine your processes to stay ahead in the competitive manufacturing landscape.
資料ダウンロード
QCD管理受発注クラウド「newji」は、受発注部門で必要なQCD管理全てを備えた、現場特化型兼クラウド型の今世紀最高の受発注管理システムとなります。
ユーザー登録
受発注業務の効率化だけでなく、システムを導入することで、コスト削減や製品・資材のステータス可視化のほか、属人化していた受発注情報の共有化による内部不正防止や統制にも役立ちます。
NEWJI DX
製造業に特化したデジタルトランスフォーメーション(DX)の実現を目指す請負開発型のコンサルティングサービスです。AI、iPaaS、および先端の技術を駆使して、製造プロセスの効率化、業務効率化、チームワーク強化、コスト削減、品質向上を実現します。このサービスは、製造業の課題を深く理解し、それに対する最適なデジタルソリューションを提供することで、企業が持続的な成長とイノベーションを達成できるようサポートします。
製造業ニュース解説
製造業、主に購買・調達部門にお勤めの方々に向けた情報を配信しております。
新任の方やベテランの方、管理職を対象とした幅広いコンテンツをご用意しております。
お問い合わせ
コストダウンが利益に直結する術だと理解していても、なかなか前に進めることができない状況。そんな時は、newjiのコストダウン自動化機能で大きく利益貢献しよう!
(β版非公開)