- お役立ち記事
- Key points for selecting suppliers and managing delivery dates to reduce inventory costs
Key points for selecting suppliers and managing delivery dates to reduce inventory costs
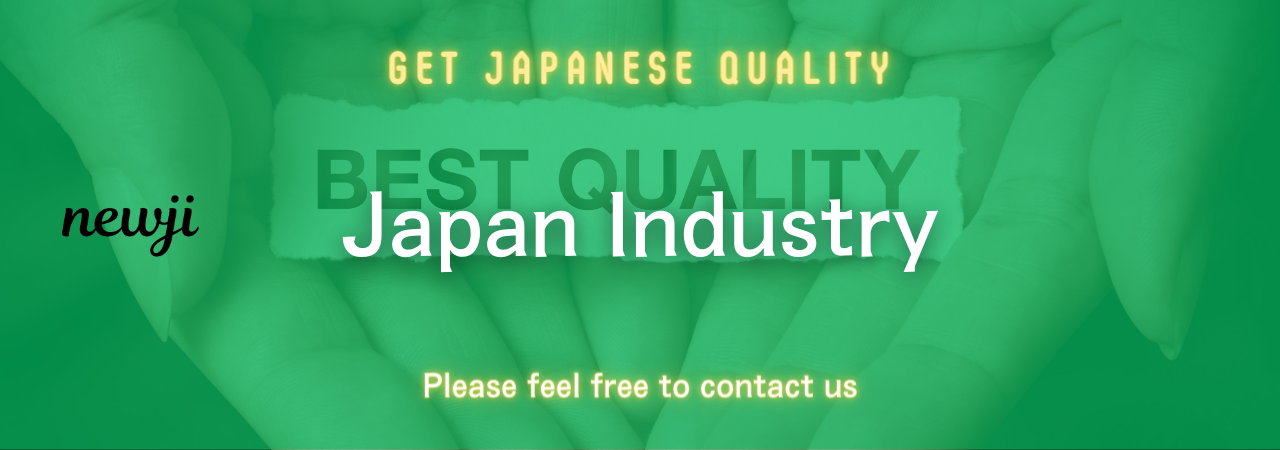
目次
Understanding the Importance of Supplier Selection
Selecting the right suppliers is a critical factor in minimizing inventory costs.
A reliable supplier ensures that you receive quality products on time, which can reduce the need for holding excessive inventory.
The more dependable your suppliers are, the more efficiently you can manage your stock levels and meet customer demands without delays.
Choosing the right supplier can affect not only inventory costs but also the overall efficiency and reputation of your business.
Dedicate time to research and evaluate potential suppliers to find those who can align with your business objectives.
It’s worth noting that collaboration with suppliers should be considered a partnership rather than merely a transactional relationship.
Criteria for Evaluating Suppliers
When assessing suppliers, several key factors must be taken into account.
Price is always a primary consideration, but it’s not the only one.
Quality, reliability, and delivery performance are equally essential.
Quality impacts customer satisfaction and returns, while reliability ensures consistent supply.
Delivery performance affects your ability to meet your customers’ expectations.
Look for suppliers with the capability to grow with your business.
Flexibility and scalability are critical characteristics that determine whether a supplier can adapt to your evolving needs.
Check their financial stability.
A supplier struggling financially may present a risk to your supply chain.
Assess their communication capabilities.
Clear and efficient communication helps prevent misunderstandings and allows you to respond quickly to changes in demand or supply issues.
Managing Delivery Dates Effectively
Effective delivery date management is crucial for maintaining optimal inventory levels and minimizing associated costs.
Understanding and tracking lead times is the first step in managing delivery dates.
Lead time is the period from placing an order to receiving the goods.
A shorter lead time typically means you can order stock more frequently, reducing the need for large amounts of inventory.
Building a buffer into your schedule for potential delays can prevent disruptions in your supply chain.
Establish a standard procedure for regular communication with suppliers to stay informed about delivery status and potential issues.
Lead time variability can impact inventory levels significantly.
Reducing lead time variability enables a leaner inventory, driving costs down.
Implementing Just-in-Time (JIT) Inventory
Implementing a Just-in-Time (JIT) inventory system can help manage delivery dates effectively.
JIT aims to receive goods only as they are needed, minimizing inventory costs.
For JIT to be successful, strong relationships with reliable suppliers are essential.
It requires precise coordination to ensure that materials arrive exactly when needed, reducing waste and storage costs.
Any disruptions in the supply chain can result in stock-outs, so establishing backup plans is crucial.
Using Technology for Better Delivery Management
Advancements in technology provide tools and systems that make managing delivery dates more efficient.
Supply chain management software offers real-time data and analytics, helping businesses optimize their inventory levels and respond quickly to changes in demand.
Such systems can provide insights into lead times, supplier performance, and potential risks.
Automating communication and ordering processes reduces manual errors and enhances supplier collaboration.
Digital platforms can help track shipments, forecast demand, and suggest optimal order quantities, further reducing inventory costs.
Building a Collaborative Relationship with Suppliers
Fostering a strong partnership with suppliers is essential for reducing inventory costs and managing delivery dates effectively.
Communicate your business goals and expectations clearly to align your operations.
Regularly review supplier performance.
Provide feedback to address any inconsistencies or issues promptly.
Joint problem-solving can result in more innovative solutions and improvements in operational efficiency.
Engage in regular discussions about future plans, demand forecasts, and any potential changes in the supply chain.
Consider establishing agreements or long-term contracts with suppliers that include terms beneficial for both parties.
The Role of Vendor Managed Inventory (VMI)
Vendor Managed Inventory (VMI) is another effective way to manage delivery dates and inventory levels.
In a VMI arrangement, the supplier takes responsibility for maintaining an agreed inventory level at your site, based on the demand data you provide.
This approach can significantly reduce the risks associated with overstocking or stockouts.
The supplier’s vested interest in replenishing your stock efficiently can lead to improved service levels and reductions in inventory holding costs.
It’s important to establish clear guidelines and expectations in a VMI agreement to ensure both parties benefit equitably.
Monitoring and Continuous Improvement
Finally, regular monitoring of your supply chain, supplier performance, and inventory levels is crucial.
Adopting an approach of continuous improvement enables you to refine processes and strategies over time.
Conduct regular audits and evaluations of your inventory management processes to identify areas for cost savings and efficiency gains.
Implementing key performance indicators (KPIs) will help measure the effectiveness of your supply chain and supplier relationships.
Encourage feedback from your team and suppliers to gain insights into potential improvements or challenges within your operations.
By focusing on supplier selection, delivery date management, and collaborative relationships, businesses can significantly reduce inventory costs and optimize their supply chain performance.
資料ダウンロード
QCD調達購買管理クラウド「newji」は、調達購買部門で必要なQCD管理全てを備えた、現場特化型兼クラウド型の今世紀最高の購買管理システムとなります。
ユーザー登録
調達購買業務の効率化だけでなく、システムを導入することで、コスト削減や製品・資材のステータス可視化のほか、属人化していた購買情報の共有化による内部不正防止や統制にも役立ちます。
NEWJI DX
製造業に特化したデジタルトランスフォーメーション(DX)の実現を目指す請負開発型のコンサルティングサービスです。AI、iPaaS、および先端の技術を駆使して、製造プロセスの効率化、業務効率化、チームワーク強化、コスト削減、品質向上を実現します。このサービスは、製造業の課題を深く理解し、それに対する最適なデジタルソリューションを提供することで、企業が持続的な成長とイノベーションを達成できるようサポートします。
オンライン講座
製造業、主に購買・調達部門にお勤めの方々に向けた情報を配信しております。
新任の方やベテランの方、管理職を対象とした幅広いコンテンツをご用意しております。
お問い合わせ
コストダウンが利益に直結する術だと理解していても、なかなか前に進めることができない状況。そんな時は、newjiのコストダウン自動化機能で大きく利益貢献しよう!
(Β版非公開)