- お役立ち記事
- Key points for standardizing production lines and promoting equipment automation to maximize cost effectiveness
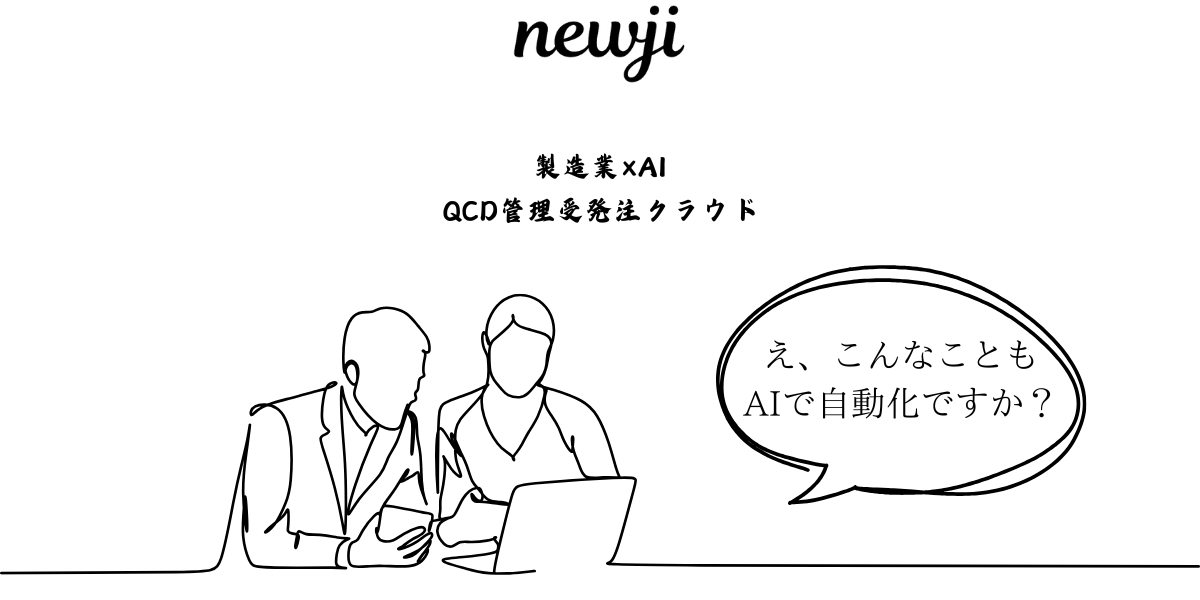
Key points for standardizing production lines and promoting equipment automation to maximize cost effectiveness
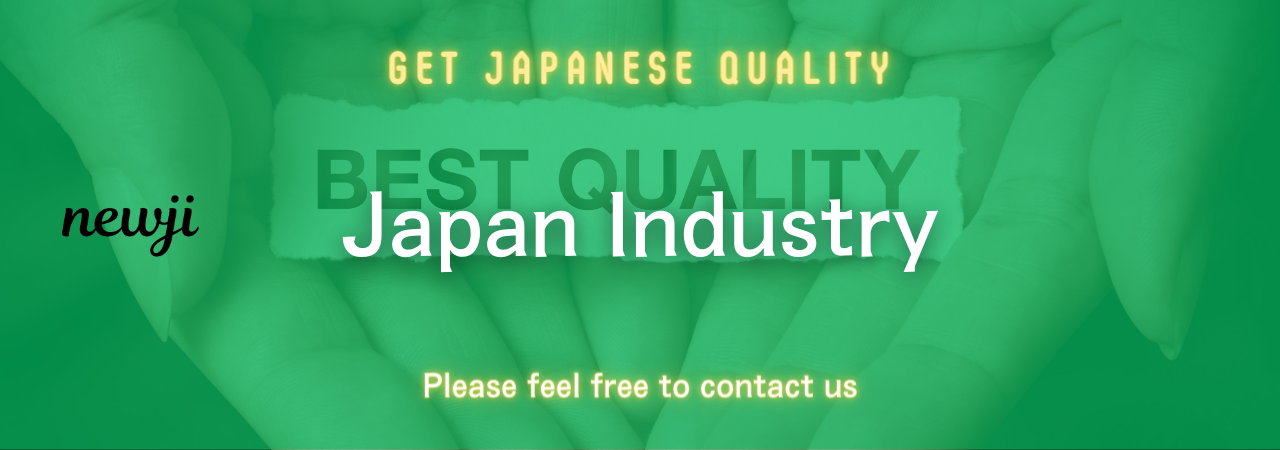
目次
Understanding Production Line Standardization
Standardizing production lines involves implementing uniform processes and systems across various manufacturing stages.
This effort aims to enhance efficiency and minimize variability in production output.
By adopting standardized processes, factories can ensure consistency, improve quality control, and reduce production errors.
When production lines are standardized, there’s a clear framework that guides all operations.
This uniformity eliminates the guessing game and allows team members to focus on improvement and optimization.
Benefits of Standardization
Standardization offers several advantages for manufacturing facilities.
Firstly, it simplifies training for new employees as there’s a definitive way to complete tasks.
Employees can quickly become proficient since they can refer to documented procedures and guidelines.
Secondly, there’s a significant reduction in material waste.
A standardized production line optimally utilizes resources, ensuring that materials are used efficiently to produce high-quality outputs.
This reduces overhead costs, contributing to the overall cost-effectiveness of the production process.
Thirdly, it aids in maintaining quality.
Consistent operations lead to predictable product quality, which is crucial for customer satisfaction and brand reputation.
Standardization ensures that each product meets the set quality standards, reducing returns and rework.
The Role of Equipment Automation
Automation in production lines further elevates efficiency and reliability.
By integrating automated machinery, tasks are performed with precision and speed, which manual labor may struggle to achieve consistently.
Automation reduces human error and enhances production by maintaining a constant pace without breaks or fatigue.
Advanced technologies enable machines to carry out complex operations, increasing production capacity and throughput.
Moreover, automated equipment allows for data collection and monitoring, assisting in predictive maintenance and minimizing downtime.
Advantages of Automation
Automating equipment offers several substantial benefits beyond improving production speeds.
One predominant advantage is the ability to operate continuously.
Machines do not require rest, which means the production line can run longer hours, increasing output and helping meet demand rapidly.
Automation enhances safety as it eliminates the need for humans to engage in potentially dangerous tasks.
Robotic systems can manage hazardous materials and operate in extreme conditions, reducing accidents and injuries.
Moreover, automation ensures consistency in the quality of products.
Machines perform tasks identically each time, which maintains the standard quality level across all products, boosting customer trust and satisfaction.
Maximizing Cost Effectiveness Through Combined Implementation
The integration of standardization with automation creates a synergy that significantly boosts cost effectiveness in production.
By reducing errors and waste through standardized operations and enhancing speed and precision via automation, manufacturers can dramatically cut costs.
The combination allows for optimized resource allocation.
Standardized processes ensure that resources are used efficiently, while automation keeps operations running smoothly and at full capacity.
This reduces operational expenses and increases profit margins.
Strategic Implementation
It’s crucial to undertake a strategic approach when integrating standardization and automation.
Start by assessing current production processes to identify inefficiencies and areas ripe for standardization.
Documenting every stage is essential for benchmarking and setting metrics.
Invest in technologies that align with your production goals.
Selecting the right automation equipment that complements standardized processes facilitates seamless operations and maximizes returns.
Collaborate with technology providers to ensure that machinery fits into your production lines effectively.
Additionally, training and development for staff are paramount.
Even with automated systems, skilled personnel are vital to oversee operations and troubleshoot issues.
Employees should be well-versed with both standardized procedures and the technology being employed.
Challenges and Considerations
While the benefits are noteworthy, there are challenges in achieving seamless standardization and automation.
The initial investment in technology and training can be substantial, requiring careful financial planning and budgeting.
It’s crucial to remain adaptable to changes and advancements in technology.
Regular updates and maintenance are necessary to keep systems efficient and reduce the risk of obsolescence.
Moreover, companies must also address cybersecurity, especially when integrating interconnected automated systems.
Ensuring data safety and process integrity is paramount in a technologically advanced production environment.
Future Insights
Looking ahead, innovation in technology will continue to shape production landscapes.
Artificial intelligence and machine learning may offer more advanced solutions for standardization and automation.
These technologies will further refine predictive maintenance, optimize production schedules, and streamline logistics.
Sustainable manufacturing practices will likely intersect with standardization and automation, providing eco-friendly solutions that optimize energy use and reduce waste.
As these technologies evolve, manufacturers who proactively integrate them can expect further gains in efficiency and cost effectiveness, maintaining a competitive edge in the market.
In conclusion, by understanding and implementing the key points of standardizing production lines and promoting equipment automation, manufacturers can unlock significant cost, quality, and productivity benefits.
This strategic approach will serve as a solid foundation for meeting current market needs and preparing for future challenges.
資料ダウンロード
QCD調達購買管理クラウド「newji」は、調達購買部門で必要なQCD管理全てを備えた、現場特化型兼クラウド型の今世紀最高の購買管理システムとなります。
ユーザー登録
調達購買業務の効率化だけでなく、システムを導入することで、コスト削減や製品・資材のステータス可視化のほか、属人化していた購買情報の共有化による内部不正防止や統制にも役立ちます。
NEWJI DX
製造業に特化したデジタルトランスフォーメーション(DX)の実現を目指す請負開発型のコンサルティングサービスです。AI、iPaaS、および先端の技術を駆使して、製造プロセスの効率化、業務効率化、チームワーク強化、コスト削減、品質向上を実現します。このサービスは、製造業の課題を深く理解し、それに対する最適なデジタルソリューションを提供することで、企業が持続的な成長とイノベーションを達成できるようサポートします。
オンライン講座
製造業、主に購買・調達部門にお勤めの方々に向けた情報を配信しております。
新任の方やベテランの方、管理職を対象とした幅広いコンテンツをご用意しております。
お問い合わせ
コストダウンが利益に直結する術だと理解していても、なかなか前に進めることができない状況。そんな時は、newjiのコストダウン自動化機能で大きく利益貢献しよう!
(Β版非公開)