- お役立ち記事
- Key points for success in multi-location procurement strategies proposed by the purchasing department
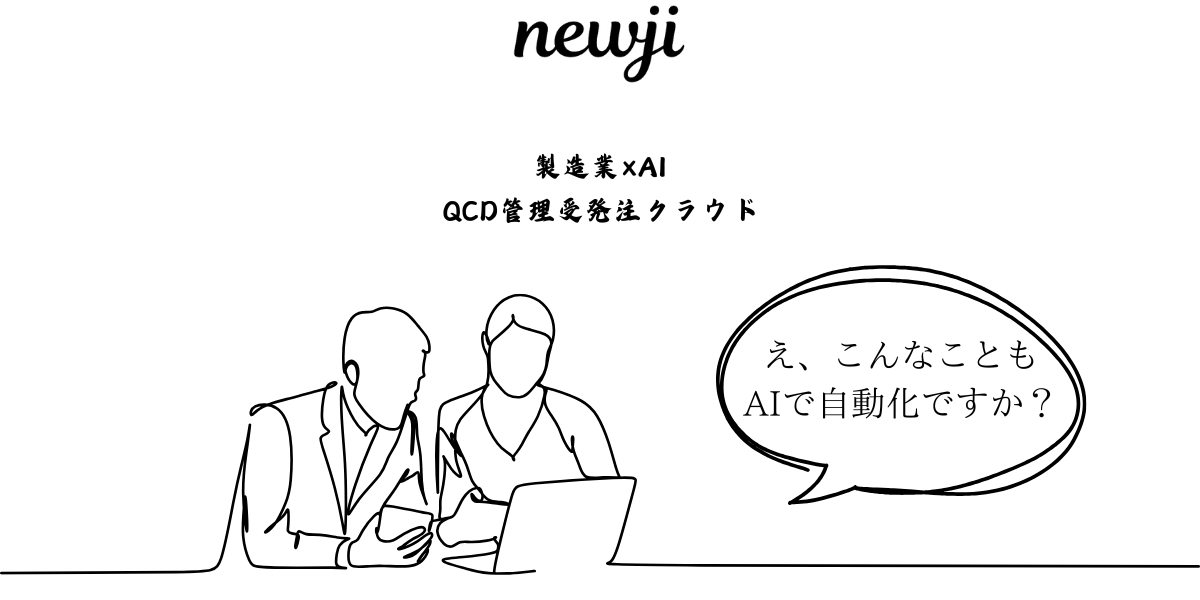
Key points for success in multi-location procurement strategies proposed by the purchasing department
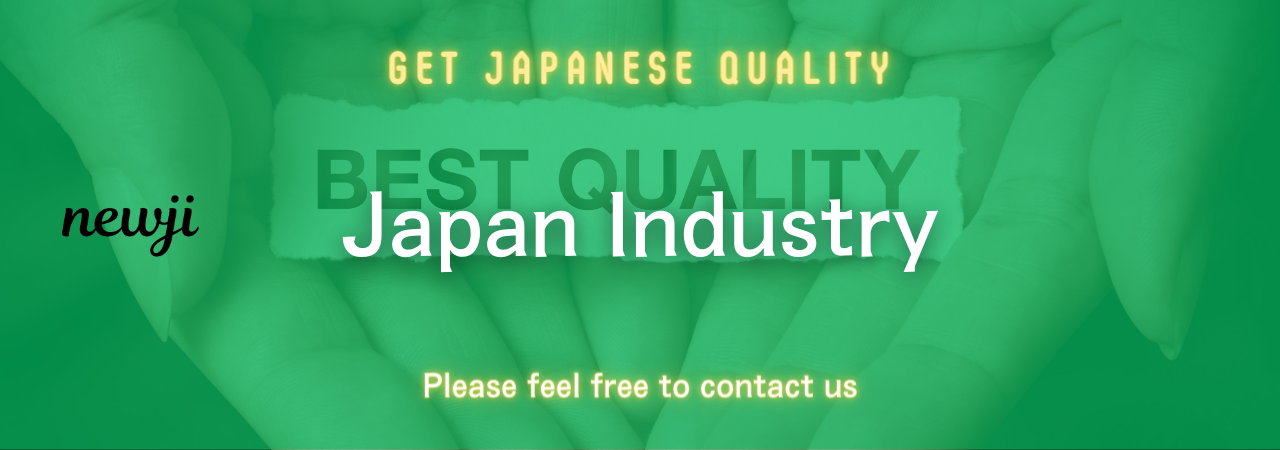
目次
Understanding Multi-Location Procurement Strategies
In today’s globalized business environment, companies are often seeking ways to optimize their operations and reduce costs.
One effective strategy is multi-location procurement.
This involves sourcing products or services from multiple locations to take advantage of cost savings, improve supply chain efficiency, and mitigate risks associated with relying on a single supplier.
It’s crucial for the purchasing department to develop successful multi-location procurement strategies that align with the company’s overall goals.
By considering several key points, businesses can maximize the benefits of this approach.
The Benefits of Multi-Location Procurement
The primary benefit of multi-location procurement is its potential to reduce costs.
By sourcing from different regions, companies can take advantage of varying labor rates, material costs, and transportation expenses.
This flexibility allows them to secure the best possible prices for their needs.
Additionally, multi-location procurement reduces reliance on any single supplier.
This is especially important in times of global uncertainty or disruption.
For example, if one supplier is unable to deliver due to unforeseen circumstances, businesses can rely on alternate sources to maintain their supply chain operations.
This strategy also enhances supply chain resilience.
When multiple suppliers are in place, companies are less vulnerable to delays or disruptions from factors such as natural disasters, political instability, or transportation issues.
Key Challenges in Multi-Location Procurement
While there are numerous benefits to multi-location procurement, it is not without its challenges.
One of the main hurdles is managing the complexity that comes with coordinating multiple suppliers.
Each supplier may have different lead times, quality standards, and cost structures, which can make the procurement process more complicated.
Additionally, maintaining consistent communication between all parties is critical to ensure smooth operations.
This requires robust systems and processes, as well as dedicated personnel, to manage the intricate web of relationships.
Finding and managing the right mix of local and international suppliers can also be challenging.
Balancing the need for low-cost options with the requirement for high-quality products or services is crucial for success.
Developing a Successful Procurement Strategy
To overcome these challenges, the purchasing department must develop a comprehensive strategy for multi-location procurement.
Several key points should be considered when crafting this plan.
1. Conduct Thorough Market Research
Before implementing a multi-location procurement strategy, it’s essential to conduct thorough market research.
This involves identifying potential suppliers and assessing their capabilities, costs, and reliability.
Understanding the strengths and weaknesses of each supplier will help determine the best fit for the company’s needs.
Market research should also include an analysis of the economic and political environment in each region.
This information can help predict potential risks and guide decision-making.
2. Establish Clear Objectives and Criteria
The purchasing department must establish clear objectives and criteria for selecting suppliers.
These should align with the company’s overall business goals, such as cost reduction, quality improvement, or risk mitigation.
By setting specific criteria, businesses can evaluate potential suppliers more effectively and make informed choices.
Criteria might include lead times, cost competitiveness, quality standards, and the ability to scale operations as needed.
3. Build Strong Supplier Relationships
Effective multi-location procurement hinges on strong supplier relationships.
Cultivating these relationships involves regular communication, collaboration, and mutual understanding.
Establishing trust with suppliers can lead to better terms, improved service, and increased willingness to accommodate changes and challenges.
Regular performance reviews and feedback sessions can also help maintain a high level of service and foster continuous improvement.
4. Implement Robust Procurement Processes
Having a well-organized procurement process is vital for managing multiple suppliers efficiently.
Standardized processes should be implemented to evaluate, select, and manage suppliers.
This can help reduce errors, improve consistency, and streamline operations.
Leveraging technology, such as procurement software and tools, can further enhance process efficiency.
These tools can automate tasks, provide data analytics, and facilitate collaboration among stakeholders.
5. Develop Risk Management Plans
Risk management is a critical component of successful multi-location procurement strategies.
Businesses must develop plans to identify, assess, and address potential risks associated with their supply chain.
This includes creating contingency plans for supplier disruptions, diversifying sources, and adjusting strategies as needed to account for changing conditions.
By proactively managing risks, companies can better protect their supply chains and ensure continuity.
Conclusion
Multi-location procurement offers a wealth of benefits, from cost savings to improved supply chain resilience.
However, it also presents unique challenges that require careful planning and execution.
By focusing on key success factors, such as thorough market research, clear objectives, strong supplier relationships, efficient processes, and risk management, the purchasing department can develop a successful strategy.
Ultimately, by leveraging the advantages of multi-location procurement, businesses can enhance their competitive edge and drive long-term success.
資料ダウンロード
QCD調達購買管理クラウド「newji」は、調達購買部門で必要なQCD管理全てを備えた、現場特化型兼クラウド型の今世紀最高の購買管理システムとなります。
ユーザー登録
調達購買業務の効率化だけでなく、システムを導入することで、コスト削減や製品・資材のステータス可視化のほか、属人化していた購買情報の共有化による内部不正防止や統制にも役立ちます。
NEWJI DX
製造業に特化したデジタルトランスフォーメーション(DX)の実現を目指す請負開発型のコンサルティングサービスです。AI、iPaaS、および先端の技術を駆使して、製造プロセスの効率化、業務効率化、チームワーク強化、コスト削減、品質向上を実現します。このサービスは、製造業の課題を深く理解し、それに対する最適なデジタルソリューションを提供することで、企業が持続的な成長とイノベーションを達成できるようサポートします。
オンライン講座
製造業、主に購買・調達部門にお勤めの方々に向けた情報を配信しております。
新任の方やベテランの方、管理職を対象とした幅広いコンテンツをご用意しております。
お問い合わせ
コストダウンが利益に直結する術だと理解していても、なかなか前に進めることができない状況。そんな時は、newjiのコストダウン自動化機能で大きく利益貢献しよう!
(Β版非公開)