- お役立ち記事
- Key Points in Gate Design: Enhancing Product Strength and Precision
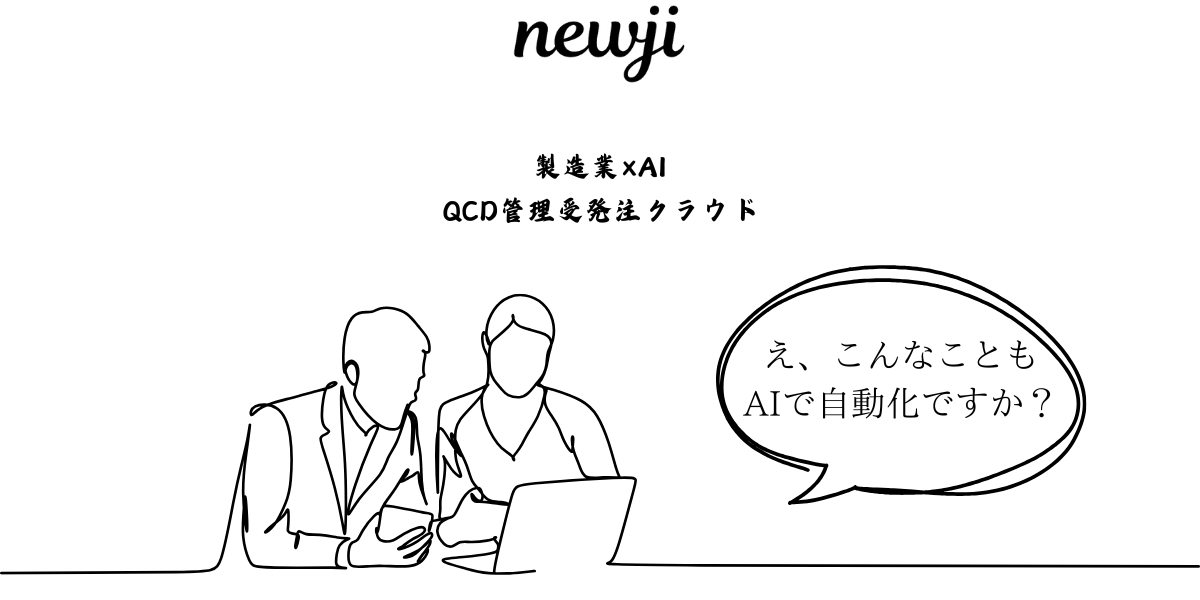
Key Points in Gate Design: Enhancing Product Strength and Precision
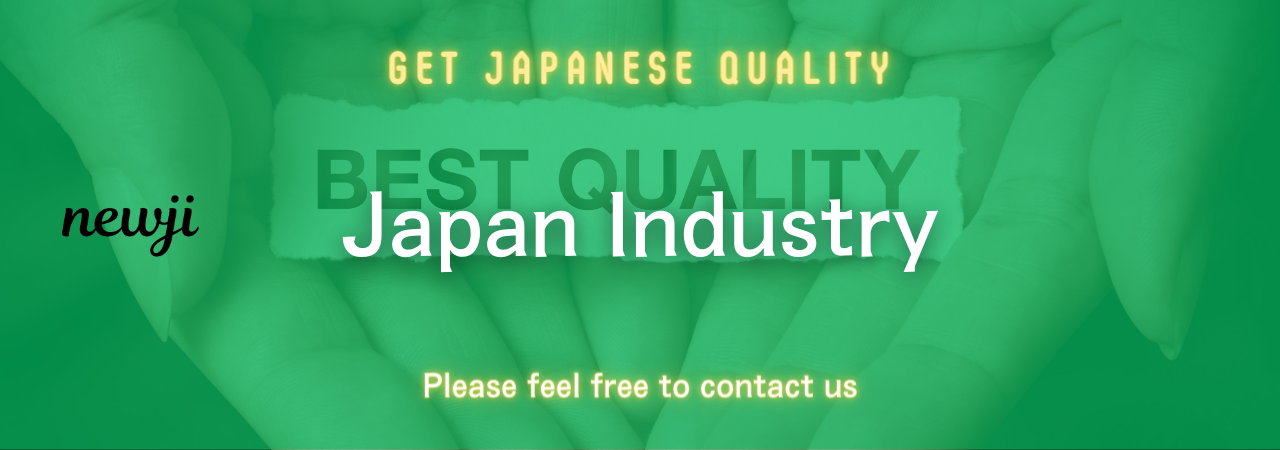
目次
Understanding Gate Design in Manufacturing
Gate design plays a crucial role in the manufacturing process, especially in molding and casting processes.
It serves as the entry point for molten material to flow into the mold cavity, shaping the final product.
The design of a gate can significantly impact the strength, precision, and overall quality of the manufactured product.
In industries where high precision and durability are essential, such as automotive, aerospace, and consumer electronics, the importance of proper gate design cannot be overstated.
The Role of Gate Design in Product Strength
One of the primary objectives of gate design is to enhance the mechanical strength of the final product.
A well-designed gate ensures that the molten material is distributed evenly throughout the mold, reducing the likelihood of weak spots or internal stresses.
When the material flows seamlessly into the mold, it hardens uniformly, enhancing the structural integrity of the product.
The gate location and size are crucial factors in determining how effectively the material is distributed.
A poorly located or undersized gate can lead to insufficient filling, causing defects such as warping, sink marks, or incomplete sections.
These defects can significantly compromise the product’s strength and durability.
Choosing the Right Gate Type
There are numerous gate types available, each suited for specific applications and material types.
Common gate types include edge gates, side gates, tunnel gates, and pin gates, among others.
The choice of gate type depends on various factors such as part geometry, material type, and production volume.
For instance, edge gates are often used for larger parts and provide a straightforward flow path for the material.
In contrast, pin gates are suitable for more complex geometries and are often used when surface aesthetics are crucial, as they leave minimal marks on the product.
Selecting the appropriate gate type is essential to ensure optimal material flow and minimize potential defects.
Precision in Gate Design
Precision in gate design is equally important as strength when it comes to producing high-quality products.
Precision affects how accurately the finished product matches the intended design specifications.
Factors such as gate size, placement, and shape all influence the dimensional accuracy of the final product.
Minimizing Flash and Waste
Flash, the excess material that leaks out of a mold cavity during molding, is a common issue that can impede precision.
Proper gate design can help minimize flash by controlling the flow of material and ensuring it fits perfectly within the mold boundaries.
Reducing flash not only improves precision but also reduces material waste and the need for additional finishing processes.
Controlling Shrinkage and Warpage
Shrinkage and warpage are two other challenges that can affect precision in molded products.
These issues occur when the material cools unevenly, leading to dimensional inaccuracies.
Effective gate design helps control these effects by ensuring even material distribution and cooling within the mold.
By doing so, manufacturers can produce parts that adhere closely to their specified dimensions.
Factors Influencing Gate Design Decisions
Several factors come into play when designing gates, including material properties, product requirements, and production constraints.
Understanding and addressing these factors is key to designing gates that enhance strength and precision.
Material Characteristics
Different materials have unique properties that affect flow behavior, cooling times, and shrinkage rates.
For instance, thermoplastics and metals behave differently under heat and pressure, requiring distinct gate designs.
A deep understanding of material characteristics is essential for designing gates that optimize material flow and final product quality.
Product Complexity and Functionality
The complexity of the product and its intended functionality also influence gate design decisions.
Intricate designs or products with multiple functions may require more sophisticated gate systems to ensure even material distribution and maintain precise specifications.
Careful planning and simulation can assist in designing gates that meet these complex requirements.
Production Volume and Cost
Production volume and cost considerations can also affect gate design.
For high-volume production runs, minimizing cycle times and reducing material waste are crucial to keeping costs down.
However, this should not compromise the quality or precision of the product.
Balancing these factors requires careful thought and possibly iterative testing and refinement of gate designs.
Advancements in Gate Design Technologies
As technology advances, so too does the ability to enhance gate design for improved strength and precision.
Computer-aided design (CAD) and computer-aided engineering (CAE) tools allow for accurate simulations of material flow and cooling patterns.
These tools enable designers to experiment with different gate configurations and optimize designs before production begins.
3D printing technologies also offer new possibilities for rapid prototyping and testing of gate designs.
By creating physical models quickly, engineers can assess the viability of various gate designs, resulting in optimized final products.
Furthermore, Industry 4.0 technologies, such as the Internet of Things (IoT) and artificial intelligence (AI), provide valuable data insights that can be used to refine gate designs continually.
Conclusion
Gate design is a fundamental aspect of the manufacturing process that greatly influences product strength and precision.
A comprehensive understanding of gate design principles, coupled with advanced technologies, can lead to improved product quality and manufacturing efficiency.
By carefully considering factors such as material properties, product complexity, and production constraints, manufacturers can design effective gates that meet specific needs.
As technology continues to evolve, the possibilities for innovation in gate design are only set to expand, offering new opportunities for enhancing product performance in various industries.
資料ダウンロード
QCD調達購買管理クラウド「newji」は、調達購買部門で必要なQCD管理全てを備えた、現場特化型兼クラウド型の今世紀最高の購買管理システムとなります。
ユーザー登録
調達購買業務の効率化だけでなく、システムを導入することで、コスト削減や製品・資材のステータス可視化のほか、属人化していた購買情報の共有化による内部不正防止や統制にも役立ちます。
NEWJI DX
製造業に特化したデジタルトランスフォーメーション(DX)の実現を目指す請負開発型のコンサルティングサービスです。AI、iPaaS、および先端の技術を駆使して、製造プロセスの効率化、業務効率化、チームワーク強化、コスト削減、品質向上を実現します。このサービスは、製造業の課題を深く理解し、それに対する最適なデジタルソリューションを提供することで、企業が持続的な成長とイノベーションを達成できるようサポートします。
オンライン講座
製造業、主に購買・調達部門にお勤めの方々に向けた情報を配信しております。
新任の方やベテランの方、管理職を対象とした幅広いコンテンツをご用意しております。
お問い合わせ
コストダウンが利益に直結する術だと理解していても、なかなか前に進めることができない状況。そんな時は、newjiのコストダウン自動化機能で大きく利益貢献しよう!
(Β版非公開)