- お役立ち記事
- Key Points in Manufacturing DX and Industrial Data Collaboration from the 2024 Manufacturing White Paper
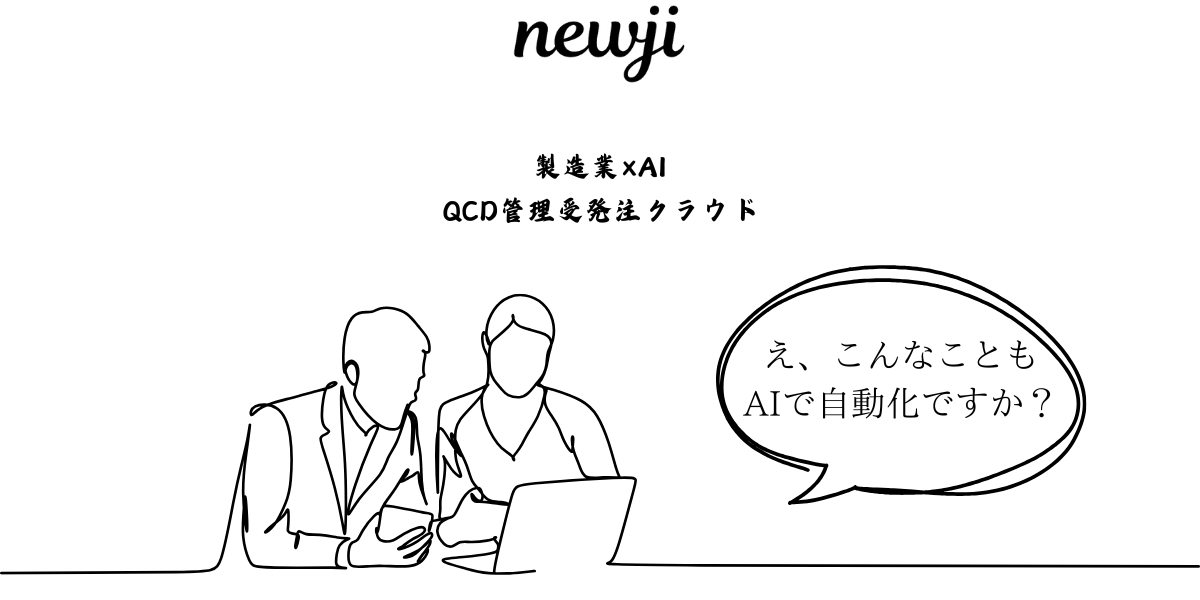
Key Points in Manufacturing DX and Industrial Data Collaboration from the 2024 Manufacturing White Paper
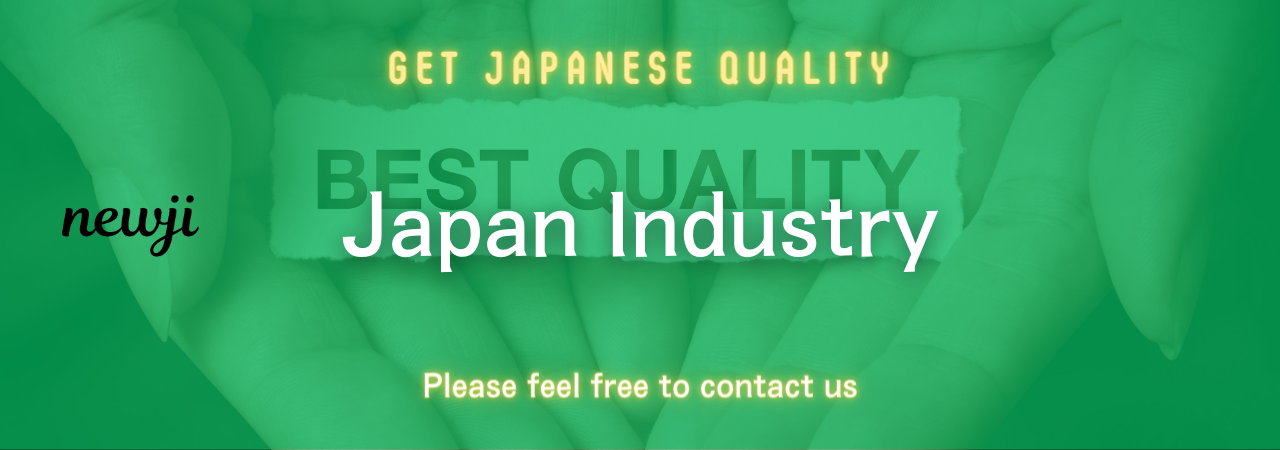
Manufacturing is on the cusp of a digital revolution, often referred to as Manufacturing Digital Transformation (DX).
This transformation is powered by technologies such as the Internet of Things (IoT), artificial intelligence (AI), and big data analytics.
Understanding the key points in Manufacturing DX and industrial data collaboration can help businesses stay competitive and efficient.
目次
What is Manufacturing DX?
Manufacturing DX refers to the integration of digital technologies into all areas of the manufacturing process.
This transformation goes beyond simply incorporating new tools; it involves changing the way businesses operate and deliver value to customers.
The goal is to create more efficient production processes, reduce costs, and unlock new business opportunities.
Why is Manufacturing DX Important?
Manufacturing DX is essential for several reasons.
First, it increases efficiency by automating tasks that were previously done manually.
Automation reduces human error and speeds up production times.
Second, digital transformation helps manufacturers to improve product quality through better data analysis and process monitoring.
Third, it enables companies to respond more quickly to market changes and customer demands.
The Role of IoT in Manufacturing DX
The Internet of Things (IoT) plays a critical role in Manufacturing DX by connecting machines, devices, and people.
IoT sensors embedded in equipment collect data in real-time, providing insights into performance and potential issues.
This data can be analyzed to optimize production processes, predict maintenance needs, and reduce downtime.
Artificial Intelligence and Machine Learning
AI and machine learning are key components of Manufacturing DX.
These technologies enable manufacturers to analyze vast amounts of data quickly and accurately.
Machine learning algorithms can identify patterns and anomalies in production data, helping to predict equipment failures before they occur.
AI-driven automation also allows for more flexible and adaptive manufacturing processes.
Industrial Data Collaboration
Industrial data collaboration involves sharing data between different parts of the manufacturing ecosystem.
This collaboration can take place within a single company or between multiple companies.
The purpose is to create a more integrated and transparent supply chain, leading to better coordination and efficiency.
Benefits of Industrial Data Collaboration
There are several benefits to industrial data collaboration.
Firstly, it helps to break down silos between departments, leading to more cohesive operations.
Secondly, sharing data with suppliers and partners ensures that everyone has the information they need to make informed decisions.
Thirdly, it can lead to innovations in product design and production methods.
Challenges of Data Collaboration
While the benefits are clear, industrial data collaboration also presents challenges.
Data security is a major concern, as sharing information increases the risk of breaches.
Companies must invest in robust cybersecurity measures to protect sensitive information.
Additionally, there can be resistance to change from employees who are used to traditional ways of working.
Overcoming these challenges requires a combination of technology and change management strategies.
Strategies for Effective Data Collaboration
To make industrial data collaboration work, companies should follow several best practices.
Firstly, establish clear data governance policies that define how data is collected, stored, and shared.
Secondly, invest in scalable and secure data infrastructure.
Thirdly, foster a culture of collaboration by encouraging communication and information sharing between departments and with external partners.
Key Takeaways from the 2024 Manufacturing White Paper
The 2024 Manufacturing White Paper highlights several important trends and recommendations for manufacturing DX and industrial data collaboration.
One key takeaway is the importance of leadership in driving digital transformation.
Leaders must be committed to the process and prepared to invest in the necessary technologies and training.
Another takeaway is the need for companies to adopt a customer-centric approach.
This means understanding customer needs and preferences and using digital technologies to meet these needs more effectively.
The white paper also emphasizes the importance of flexibility and agility in manufacturing processes.
By leveraging digital tools, companies can respond more quickly to changes in demand and market conditions.
Focus on Workforce Development
The white paper also stresses the importance of workforce development in support of Manufacturing DX.
Employees need to be trained in new technologies and processes.
This includes not only technical skills but also soft skills such as problem-solving and adaptability.
Investing in workforce development ensures that employees are prepared to work in a digitally transformed environment, driving improved outcomes for the business.
Leveraging Big Data Analytics
A significant point made in the white paper is the transformative potential of big data analytics.
Collecting and analyzing data from all aspects of the manufacturing process can lead to deeper insights and better decision-making.
Big data helps to identify inefficiencies, predict maintenance needs, and understand customer behaviors.
The Future of Manufacturing
The future of manufacturing lies in embracing digital transformation and data collaboration.
Businesses that invest in these areas will be better positioned to compete in a rapidly changing market.
They will be able to operate more efficiently, deliver higher-quality products, and respond more quickly to customer needs.
Furthermore, the adoption of digital tools will lead to the creation of new business models and revenue streams.
For example, manufacturers can offer predictive maintenance services or use customer data to develop personalized products.
Long-term Success
Achieving long-term success in the digital era requires a commitment to continuous improvement.
Manufacturers should regularly review and update their DX strategies to incorporate new technologies and industry best practices.
They should also remain open to feedback from employees, customers, and partners.
In conclusion, Manufacturing DX and industrial data collaboration are not just trends; they are essential strategies for the future.
By understanding and implementing the key points outlined in the 2024 Manufacturing White Paper, businesses can ensure they are ready to thrive in the digital age.
資料ダウンロード
QCD調達購買管理クラウド「newji」は、調達購買部門で必要なQCD管理全てを備えた、現場特化型兼クラウド型の今世紀最高の購買管理システムとなります。
ユーザー登録
調達購買業務の効率化だけでなく、システムを導入することで、コスト削減や製品・資材のステータス可視化のほか、属人化していた購買情報の共有化による内部不正防止や統制にも役立ちます。
NEWJI DX
製造業に特化したデジタルトランスフォーメーション(DX)の実現を目指す請負開発型のコンサルティングサービスです。AI、iPaaS、および先端の技術を駆使して、製造プロセスの効率化、業務効率化、チームワーク強化、コスト削減、品質向上を実現します。このサービスは、製造業の課題を深く理解し、それに対する最適なデジタルソリューションを提供することで、企業が持続的な成長とイノベーションを達成できるようサポートします。
オンライン講座
製造業、主に購買・調達部門にお勤めの方々に向けた情報を配信しております。
新任の方やベテランの方、管理職を対象とした幅広いコンテンツをご用意しております。
お問い合わせ
コストダウンが利益に直結する術だと理解していても、なかなか前に進めることができない状況。そんな時は、newjiのコストダウン自動化機能で大きく利益貢献しよう!
(Β版非公開)