- お役立ち記事
- Key points of geometric tolerances in mechanical design, appropriate design instructions, and points to keep in mind
月間76,176名の
製造業ご担当者様が閲覧しています*
*2025年3月31日現在のGoogle Analyticsのデータより
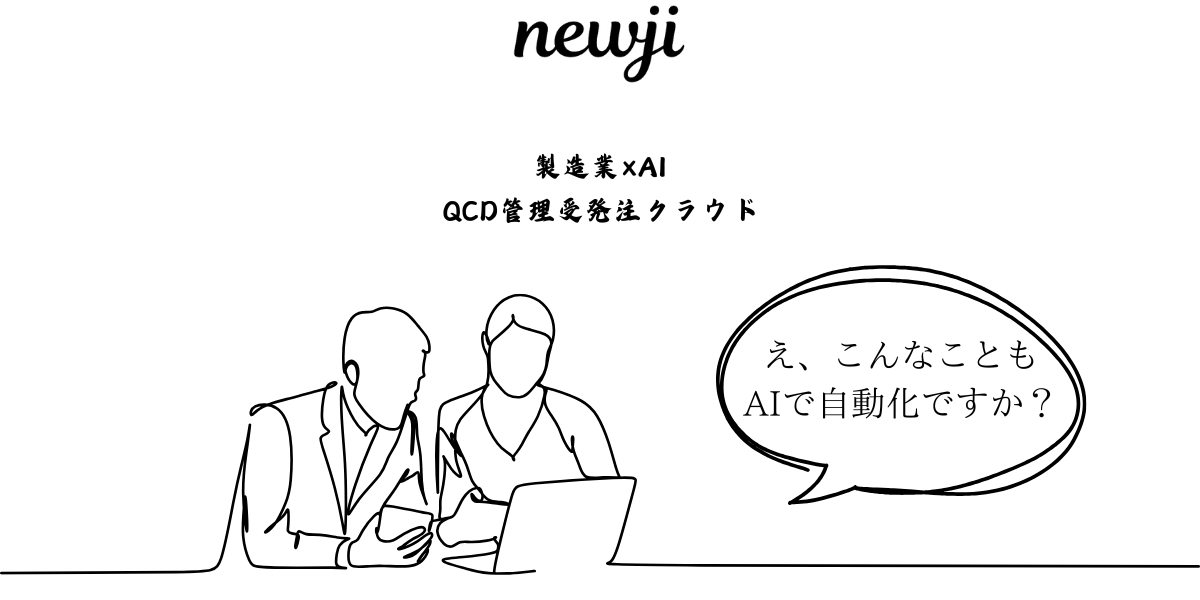
Key points of geometric tolerances in mechanical design, appropriate design instructions, and points to keep in mind
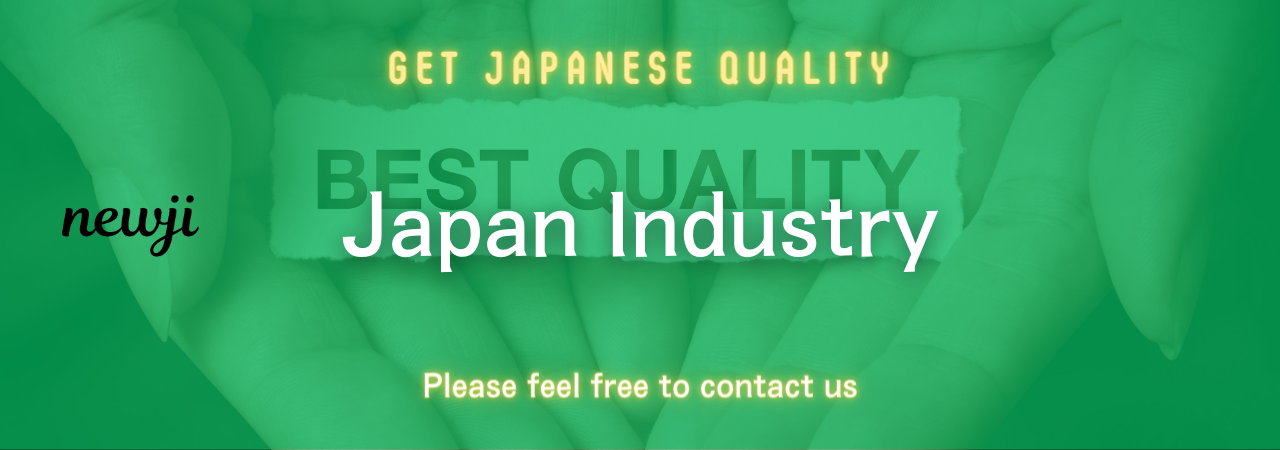
目次
Understanding Geometric Tolerances
When designing mechanical components, geometric tolerances are crucial for ensuring that parts fit and function correctly within an assembly.
These tolerances define the allowable deviations from the nominal dimensions, ensuring parts align, fit, and operate seamlessly.
Geometric tolerances differ from dimensional tolerances, as they focus more on a part’s shape, orientation, and position, rather than just its size.
This includes various aspects like flatness, parallelism, perpendicularity, and concentricity.
Using geometric tolerances allows engineers to specify the permissible variation in the form and relationship between features on a part.
This level of control is essential for high-precision engineering applications.
Importance of Geometric Tolerances
Implementing geometric tolerances in mechanical design significantly impacts the quality and functionality of the final product.
They offer numerous benefits, including improved fit and functionality, cost efficiency, and reduced manufacturing errors.
1. **Improved Fit and Functionality:**
By specifying geometric tolerances, designers can ensure parts fit together accurately, leading to better assembly and operation.
Accurate tolerances prevent misalignment and can also lead to smoother mechanical motion.
2. **Cost Efficiency:**
Applying geometric tolerances efficiently can reduce waste during production.
Tight tolerances can increase manufacturing costs, but by optimizing them, the costs can be controlled while maintaining product quality.
3. **Reduced Manufacturing Errors:**
Clear geometric tolerances minimize the risk of errors in both manufacturing and inspection processes.
This leads to high-quality outputs and reduces the need for costly adjustments or reworks.
Key Types of Geometric Tolerances
Understanding different types of geometric tolerances helps in applying them effectively in mechanical design.
Here are some key types:
1. **Form Tolerances:**
– **Flatness:** Ensures a surface does not deviate from a perfect plane.
– **Straightness:** Checks how straight an edge or axis is, allowing a deviation from a theoretically perfect line.
2. **Orientation Tolerances:**
– **Parallelism:** Controls the extent to which two surfaces or features are parallel to each other.
– **Perpendicularity:** Ensures that a surface or edge is at perfect right angles to a reference plane or axis.
3. **Location Tolerances:**
– **Position:** Specifies the exact location of a feature within certain limits, crucial for ensuring parts align as intended.
– **Concentricity:** Ensures that the center of one or more features coincides with the center of a datum feature.
4. **Runout:**
– **Circular Runout:** Deals with any deviation in a rotating component.
– **Total Runout:** Controls the deviation from the entire surface as the part rotates, ensuring minimal wobble.
Design Instructions for Geometric Tolerances
When incorporating geometric tolerances in the design, follow these instructions to achieve the desired outcomes:
1. **Identify Critical Features:**
– Determine which features are critical to the part’s function and prioritize these for tight tolerances.
– Understanding the function of each feature helps in deciding the appropriate level of tolerance.
2. **Consider Manufacturing Processes:**
– Different processes have varying levels of accuracy.
– Select suitable manufacturing techniques that can achieve the required tolerances economically.
3. **Communicate Specifications Clearly:**
– Use standardized notations and symbols from industry standards like GD&T (Geometric Dimensioning and Tolerancing) to convey requirements clearly.
– Ensure drawings are clear and unambiguous to prevent misinterpretations.
4. **Use Datum References Effectively:**
– Datums are points, lines, or surfaces from which measurements are made.
– Proper use of datums helps in defining the tolerancing framework and eases part verification.
Points to Keep in Mind
When working with geometric tolerances, consider the following points to avoid potential pitfalls:
1. **Balance Between Tolerance and Cost:**
– While tighter tolerances may be desirable, they come at increased costs.
– Aim to find a balance where the tolerance meets functional requirements without undue expense.
2. **Understanding the Limitations:**
– Be aware of the limitations of measurement tools and techniques.
– Use appropriate methods for verification, considering the smallest feature sizes or tightest tolerances.
3. **Adapt to Changes:**
– Be open to adapting the tolerances as needed.
– Design changes or unforeseen manufacturing issues may warrant adjustments to the original tolerancing plan.
4. **Continuous Learning:**
– Regularly update your understanding of advances in materials, machining technologies, and tolerancing standards.
– This ensures that your designs remain innovative and competitive.
In conclusion, mastery of geometric tolerances requires understanding both theoretical and practical aspects.
By applying these principles effectively, mechanical designers can ensure the efficient production of high-quality, reliable components.
資料ダウンロード
QCD管理受発注クラウド「newji」は、受発注部門で必要なQCD管理全てを備えた、現場特化型兼クラウド型の今世紀最高の受発注管理システムとなります。
ユーザー登録
受発注業務の効率化だけでなく、システムを導入することで、コスト削減や製品・資材のステータス可視化のほか、属人化していた受発注情報の共有化による内部不正防止や統制にも役立ちます。
NEWJI DX
製造業に特化したデジタルトランスフォーメーション(DX)の実現を目指す請負開発型のコンサルティングサービスです。AI、iPaaS、および先端の技術を駆使して、製造プロセスの効率化、業務効率化、チームワーク強化、コスト削減、品質向上を実現します。このサービスは、製造業の課題を深く理解し、それに対する最適なデジタルソリューションを提供することで、企業が持続的な成長とイノベーションを達成できるようサポートします。
製造業ニュース解説
製造業、主に購買・調達部門にお勤めの方々に向けた情報を配信しております。
新任の方やベテランの方、管理職を対象とした幅広いコンテンツをご用意しております。
お問い合わせ
コストダウンが利益に直結する術だと理解していても、なかなか前に進めることができない状況。そんな時は、newjiのコストダウン自動化機能で大きく利益貢献しよう!
(β版非公開)