- お役立ち記事
- Key points of machine conceptual design and strength design to prevent breakage, and troubleshooting
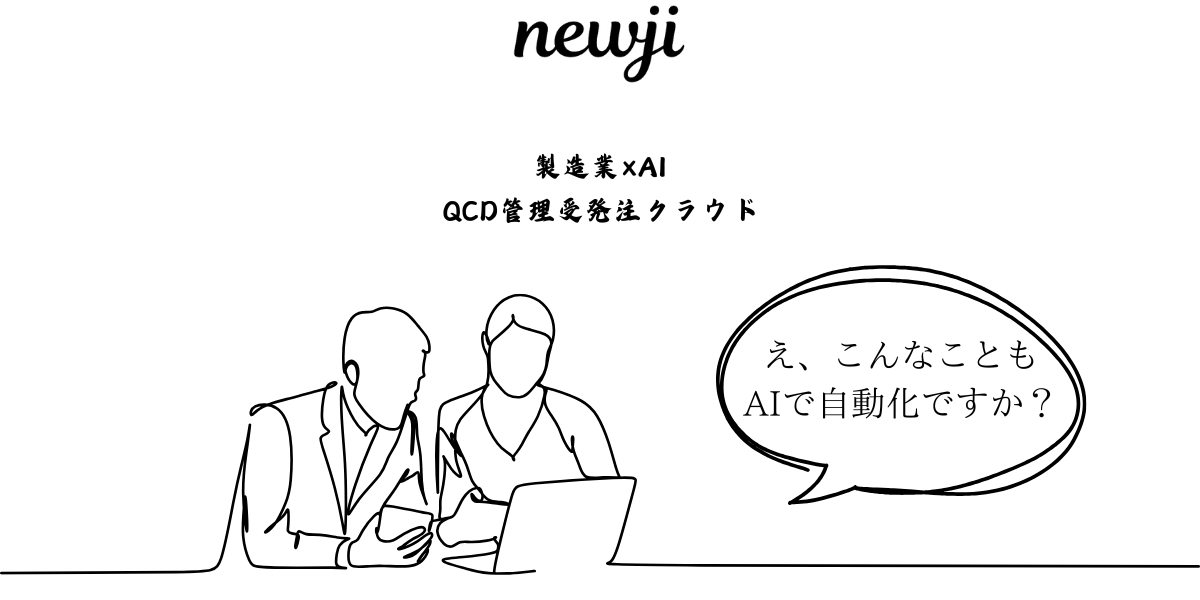
Key points of machine conceptual design and strength design to prevent breakage, and troubleshooting
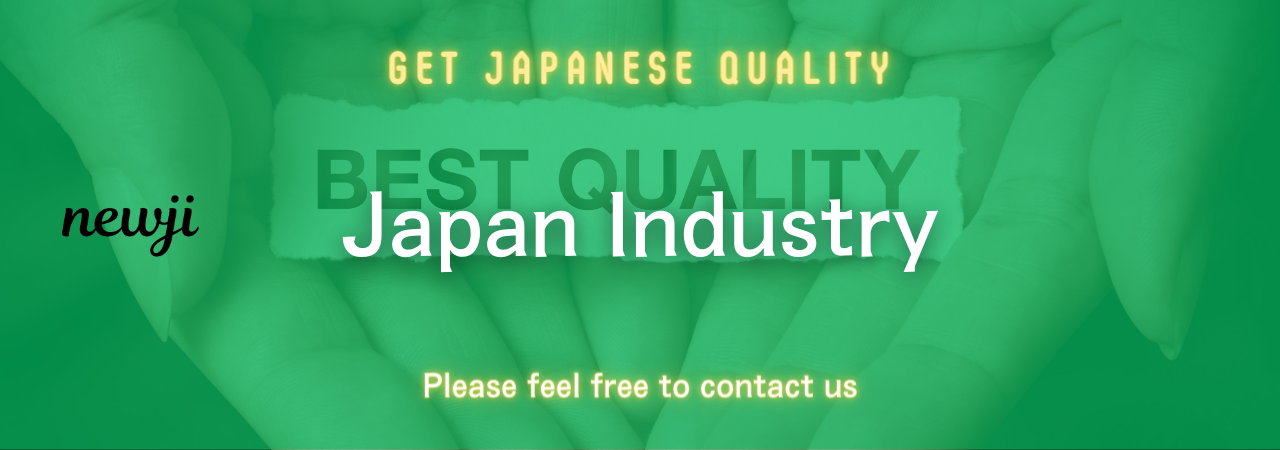
目次
Understanding Machine Conceptual Design
Machine conceptual design is the process of planning and creating a blueprint for machines before they are physically built.
At this stage, designers and engineers imagine how the machine will function and solve any potential problems that may arise.
It is crucial for ensuring that the final product is efficient, effective, and safe to use.
Here, we explore key points in conceptual design that help prevent breakage.
Initial Research and Analysis
A successful conceptual design begins with thorough research and analysis.
Understanding the needs and expectations of the market is essential.
This involves studying current machines, competitor products, and technological advancements.
Additionally, feedback from end-users can provide valuable insights.
Such information guides designers in identifying features that improve user experience and prevent potential breakage.
Creating Detailed Specifications
Once initial research is complete, the next step is to define precise specifications.
These specifications outline the dimensions, capabilities, and constraints of the machine.
Clear and detailed specifications prevent misunderstandings during the design process.
This step also involves deciding the materials and components to be used, considering their durability and potential for wear and tear.
Selecting high-quality materials is pivotal in preventing breakage and ensuring longevity.
Developing Initial Designs
With specifications in place, designers create initial design layouts.
These are usually sketches or 3D models that visualize the machine’s structure.
During this phase, designers consider factors such as weight distribution, stress points, and load capacity.
This helps in identifying areas where additional support might be needed to prevent breakage.
Using simulations at this stage can reveal stress points and help refine the design before moving to the production phase.
Strength Design to Prevent Breakage
Strength design focuses on ensuring that machines can withstand the stresses they will encounter during operation.
This is critical to prevent mechanical failures and extend the machine’s lifespan.
Stress Analysis and Load Testing
Performing stress analysis is vital in strength design.
This process evaluates how different forces affect the machine components.
Engineers use mathematical models and simulations to predict where the structures are most likely to break or deform.
Load testing, which involves applying controlled stress to a prototype, can validate these models.
By identifying weak points early, engineers can reinforce the design to prevent future failures.
Material Selection
Selecting the right materials is inseparable from a good strength design.
The choice of material directly impacts durability and resistance to factors such as temperature, corrosion, and fatigue.
For example, metals like steel and titanium are preferred for their strength and resistance to deformation.
Meanwhile, composites may be used in areas where weight is a concern, without sacrificing durability.
Employing materials suited for specific functions minimizes the likelihood of breakage.
Design for Manufacturing and Assembly (DFMA)
DFMA is a design approach that simplifies the manufacturing and assembly processes.
This method reduces the complexity and cost of production and enhances the overall strength of the machine.
Designing parts that are easy to produce and assemble minimizes potential errors during manufacturing.
Standardizing components where possible also helps in reducing stress points and facilitates easier maintenance.
Troubleshooting Mechanical Designs
Even with a strong conceptual and strength design, unforeseen issues may arise.
Troubleshooting is an essential process for identifying and resolving these problems.
Regular Maintenance Checks
Conducting regular maintenance checks is a proactive approach to avoid machine breakdowns.
These checks can detect wear and tear early and prevent catastrophic failures.
Routine inspections include checking for signs of stress, lubricating moving parts, and replacing worn components.
A well-maintained machine is less prone to breakage and operates more efficiently.
Monitoring Performance
Implementing performance monitoring systems can provide real-time data on machine operations.
This helps in identifying anomalies that may indicate deeper issues.
For example, unexpected vibrations or changes in temperature can signal underlying problems.
Addressing these issues promptly helps in preventing breakdowns and extends the machine’s service life.
Continuous Improvement
Troubleshooting should not only focus on fixing issues but also on understanding their root causes.
A continuous improvement mindset encourages learning from past failures to enhance future design processes.
Feedback from the troubleshooting phase can inform adjustments in conceptual and strength designs.
This iterative process ensures machines are not only fixed but also made more resilient over time.
In conclusion, a robust approach to conceptual and strength design, coupled with effective troubleshooting, is essential in preventing machine breakage.
By thoroughly researching, specifying, testing, and monitoring, engineers and designers can create machines that are durable, reliable, and efficient.
資料ダウンロード
QCD調達購買管理クラウド「newji」は、調達購買部門で必要なQCD管理全てを備えた、現場特化型兼クラウド型の今世紀最高の購買管理システムとなります。
ユーザー登録
調達購買業務の効率化だけでなく、システムを導入することで、コスト削減や製品・資材のステータス可視化のほか、属人化していた購買情報の共有化による内部不正防止や統制にも役立ちます。
NEWJI DX
製造業に特化したデジタルトランスフォーメーション(DX)の実現を目指す請負開発型のコンサルティングサービスです。AI、iPaaS、および先端の技術を駆使して、製造プロセスの効率化、業務効率化、チームワーク強化、コスト削減、品質向上を実現します。このサービスは、製造業の課題を深く理解し、それに対する最適なデジタルソリューションを提供することで、企業が持続的な成長とイノベーションを達成できるようサポートします。
オンライン講座
製造業、主に購買・調達部門にお勤めの方々に向けた情報を配信しております。
新任の方やベテランの方、管理職を対象とした幅広いコンテンツをご用意しております。
お問い合わせ
コストダウンが利益に直結する術だと理解していても、なかなか前に進めることができない状況。そんな時は、newjiのコストダウン自動化機能で大きく利益貢献しよう!
(Β版非公開)