- お役立ち記事
- Key points of mechanics and design calculations necessary for machine designers and their application to machine tool design technology
月間77,185名の
製造業ご担当者様が閲覧しています*
*2025年2月28日現在のGoogle Analyticsのデータより
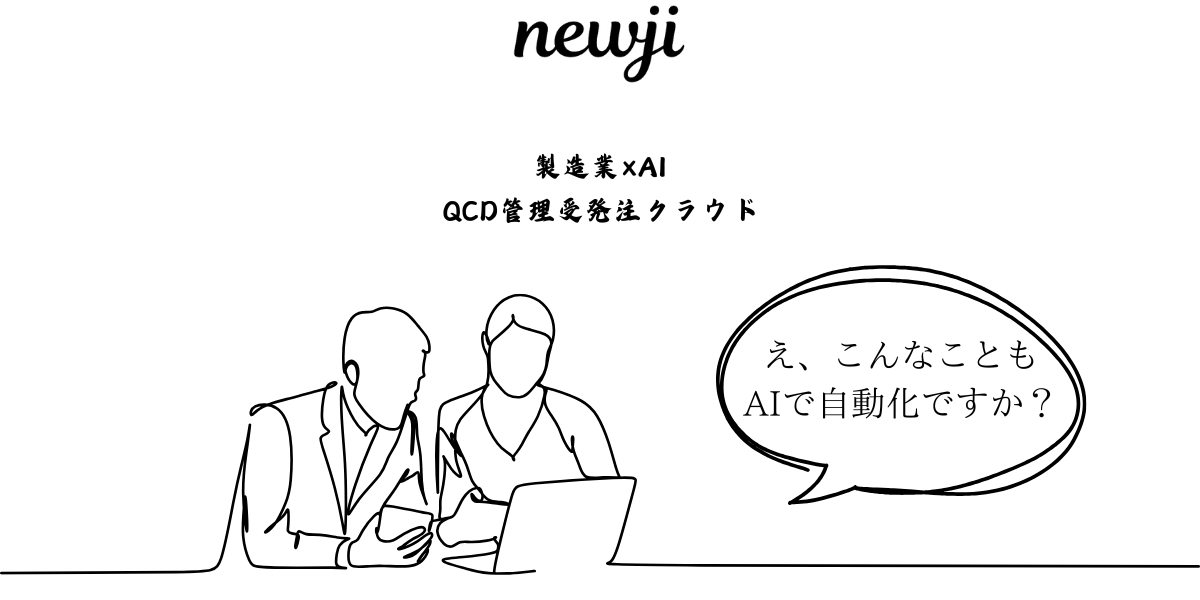
Key points of mechanics and design calculations necessary for machine designers and their application to machine tool design technology
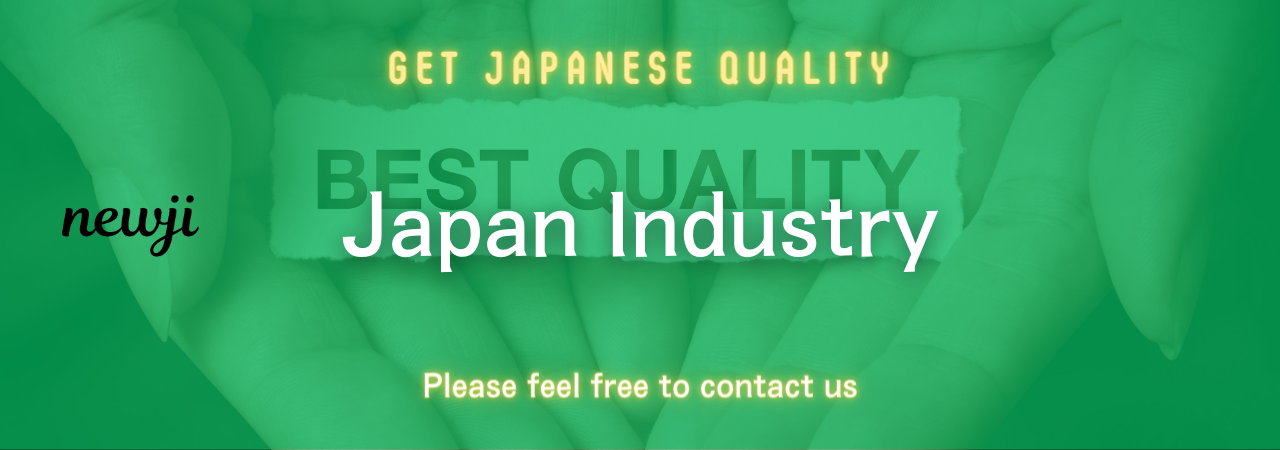
目次
Understanding the Basics of Mechanics for Machine Designers
Mechanics is a foundational aspect of machine design that allows engineers to predict how machines will perform under various conditions.
For machine designers, understanding principles such as force, motion, and energy is crucial.
These principles guide the calculations that ensure machines are safe, efficient, and reliable.
Mechanical systems often require the application of Newton’s laws of motion to determine forces and accelerations.
By understanding these basic mechanics, designers can begin to predict how different forces will affect machine components and the overall system.
Machine designers must also comprehend the concepts of stress and strain, as they are vital for materials selection and structural integrity.
When designing machines, the knowledge of material properties ensures that components can withstand operational demands without failure.
This understanding also helps designers to make informed choices on materials that optimize performance and cost-effectiveness.
Design Calculations: Precision in Machine Design
Design calculations are a critical part of the machine design process.
These calculations are utilized to specify the dimensions, specifications, and characteristics of each component.
For example, a designer will need to calculate the appropriate size of gears to transmit power efficiently without failure.
Such calculations involve determining forces, torques, and material properties to ensure a harmonious function.
Calculations also play a significant role in thermal management.
Managing heat is essential in machine design, as excess heat can lead to premature failure or reduced efficiency.
Designers use thermal calculations to determine cooling requirements or to select materials that minimize thermal expansion and contraction.
Furthermore, tolerance analysis is another vital calculation that ensures components fit together properly within an assembly.
It addresses the permissible limits of variation in dimensions that ensure functions without interference.
Using Simulations in Design Calculations
Modern machine designers frequently use computer-aided engineering (CAE) tools to perform design simulations.
These tools allow for virtual testing of machine components and systems under various conditions.
Simulations can identify potential issues before creating physical prototypes, saving time and resources.
Finite Element Analysis (FEA) is one simulation method used to assess stresses and deformations in components.
By dividing a component into finite elements, designers can predict how the part will behave under real-world conditions.
This data helps in refining the design before production, enhancing accuracy and efficiency.
Applying Mechanics and Calculations to Machine Tool Design
Machine tool design requires a blend of mechanical principles and precise calculations to create tools that are reliable and efficient.
Tools need to be designed for specific operations while ensuring strength, durability, and precision.
For example, calculating the optimal cutting forces in a milling machine is crucial to avoid tool breakage or workpiece damage.
This involves understanding how materials react under force and ensuring that the tool and workpiece interaction is optimized for cutting efficiency.
Machine designers must also consider the dynamics of machine tools, such as vibrations and resonance, which can affect precision and lead to wear.
By conducting modal analysis, designers can identify potential resonance issues and modify the design to mitigate them.
Additionally, ergonomics and safety are integral to machine tool design.
Calculations are used to ensure that the design minimizes human error and ensures the safety of the user.
The Role of Software in Machine Tool Design
Software applications enhance the design process by providing tools for detailed modeling and analysis.
Computer-aided design (CAD) software allows machine designers to create accurate 3D models of tools.
These models facilitate the visualization of complex assemblies and allow for thorough inspection before prototypes are made.
Moreover, integrated CAD and CAE systems can conduct stress tests, simulate operations, and optimize design iterations swiftly.
This results in better tools, reduced time to market, and lowers costs.
Conclusion
Understanding mechanics and performing meticulous design calculations are essential for machine designers to develop innovative and functional machinery.
These principles and processes are particularly critical in the realm of machine tool design, where precision and reliability are non-negotiable.
By applying knowledge of mechanics, using advanced simulation tools, and diligent calculations, designers can ensure that machine tools meet and exceed operational demands.
This not only leads to efficient and effective machinery but also advances the capabilities of industries that rely on machine tool innovations.
資料ダウンロード
QCD管理受発注クラウド「newji」は、受発注部門で必要なQCD管理全てを備えた、現場特化型兼クラウド型の今世紀最高の受発注管理システムとなります。
ユーザー登録
受発注業務の効率化だけでなく、システムを導入することで、コスト削減や製品・資材のステータス可視化のほか、属人化していた受発注情報の共有化による内部不正防止や統制にも役立ちます。
NEWJI DX
製造業に特化したデジタルトランスフォーメーション(DX)の実現を目指す請負開発型のコンサルティングサービスです。AI、iPaaS、および先端の技術を駆使して、製造プロセスの効率化、業務効率化、チームワーク強化、コスト削減、品質向上を実現します。このサービスは、製造業の課題を深く理解し、それに対する最適なデジタルソリューションを提供することで、企業が持続的な成長とイノベーションを達成できるようサポートします。
製造業ニュース解説
製造業、主に購買・調達部門にお勤めの方々に向けた情報を配信しております。
新任の方やベテランの方、管理職を対象とした幅広いコンテンツをご用意しております。
お問い合わせ
コストダウンが利益に直結する術だと理解していても、なかなか前に進めることができない状況。そんな時は、newjiのコストダウン自動化機能で大きく利益貢献しよう!
(β版非公開)