- お役立ち記事
- Key points of powder metallurgy/MIM process and high-performance/high-strength technology
月間76,176名の
製造業ご担当者様が閲覧しています*
*2025年3月31日現在のGoogle Analyticsのデータより
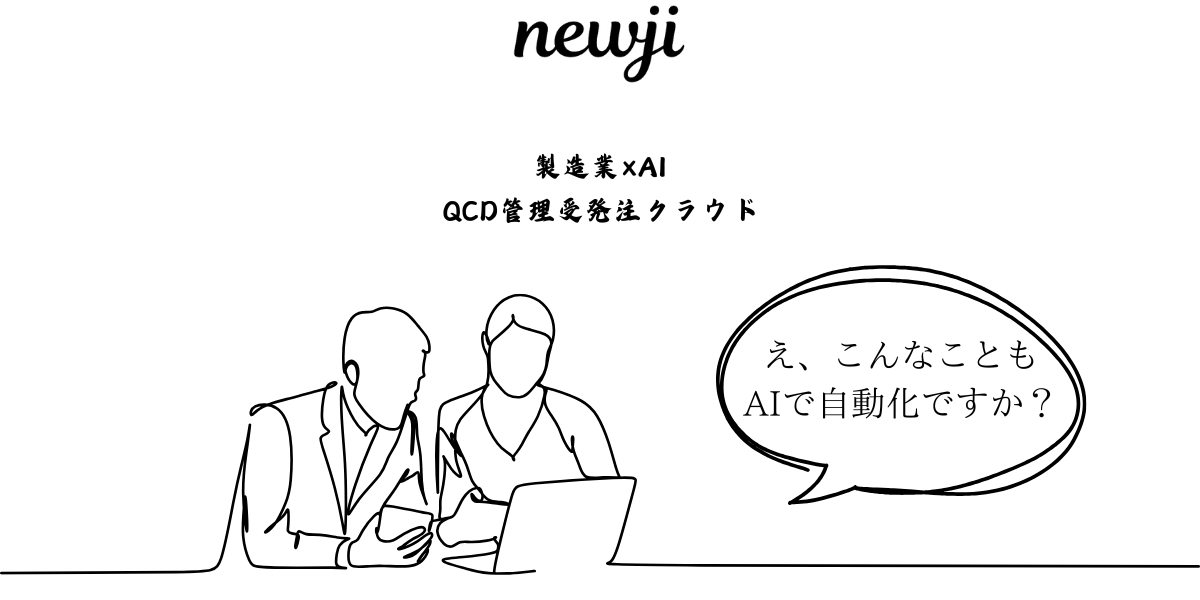
Key points of powder metallurgy/MIM process and high-performance/high-strength technology
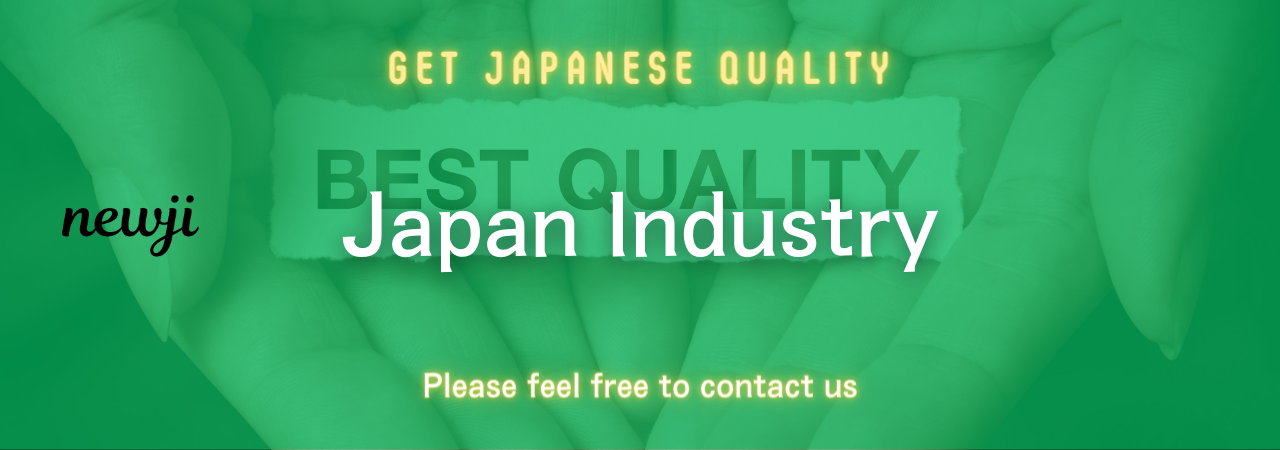
目次
Understanding Powder Metallurgy and MIM Process
Powder metallurgy is a specialized method for creating metal parts and components from powdered metal materials.
This process is highly efficient, offering benefits in terms of sustainability and precision.
Metal Injection Molding (MIM), a subset of powder metallurgy, combines the versatility of plastic injection molding with the strength and integrity of metal.
Together, these methods allow manufacturers to produce complex, high-performance components with minimal waste.
The process begins with the selection of metal powders, typically mixed with bonding agents to form a feedstock.
In the case of MIM, the feedstock is then injected into a mold, taking on its desired shape.
Following injection, the part undergoes a series of thermal and chemical processes to remove the binding agents and sinter the metal particles into a solid form.
Advantages of Powder Metallurgy and MIM
One of the most significant benefits of powder metallurgy, and specifically MIM, is the ability to produce intricate shapes that would otherwise be impossible or too costly to create through traditional manufacturing processes.
This is invaluable for industries such as aerospace, automotive, and medical, where precision and performance are critical.
Another advantage is the efficient use of materials.
Since components are formed from powder, there’s minimal waste compared to traditional machining, which generates scrap.
This not only lowers material costs but also aligns with growing environmental concerns by reducing the carbon footprint of production processes.
Additionally, powder metallurgy offers uniformity in production, ensuring that each piece is consistent in quality.
The process also allows for the incorporation of various alloys and composite materials, further enhancing the mechanical properties and performance of the final product.
High-Performance and High-Strength Techniques
Optimizing Material Selection
Material selection plays a crucial role in the performance and strength of components produced through powder metallurgy and MIM.
Choosing the right combination of metal powders not only defines the mechanical attributes of the component but also affects the processibility of the feedstock.
Advanced high-strength alloys like stainless steel, titanium, and cobalt-chrome are commonly used due to their excellent mechanical properties and resistance to wear and corrosion.
Process Parameter Optimization
The performance and strength of MIM components depend heavily on controlling process parameters.
Parameters such as temperature, pressure, and time must be precisely managed during the injection, debinding, and sintering stages.
By meticulously optimizing these factors, manufacturers can enhance the density and cohesion of the metal parts, directly influencing their strength and durability.
Innovations in process monitoring and control technologies allow for real-time adjustments, improving component quality and consistency.
This aspect is particularly important for sectors requiring stringent adherence to standards, such as the aerospace and medical device industries.
Enhancing Final Product Properties
Post-processing techniques are equally vital in boosting the properties of metal parts produced by MIM.
Techniques such as heat treatment, surface finishing, and coating are employed to enhance the mechanical properties, surface quality, and performance of the final product.
Heat treatment helps to attain desired levels of hardness and strength.
Surface finishing processes, such as polishing or blasting, improve aesthetic appeal and surface integrity.
Additionally, coatings can provide extra layers of protection against environmental factors, further extending the lifespan of components.
Applications in Modern Industries
Automotive Industry
In the automotive industry, where reliability, efficiency, and innovation drive development, powder metallurgy and MIM are key technologies.
Automotive components, such as gear parts, turbocharger rotors, and fuel-system components, benefit from the high precision and high performance achieved through these processes.
The ability to produce lightweight, structurally complex components helps automotive manufacturers meet increasing demands for energy efficiency and emissions reduction without compromising on performance.
Aerospace Industry
The aerospace sector requires components that can withstand extreme environmental conditions while maintaining optimal performance.
Powder metallurgy and MIM cater to this need by producing lightweight, robust, and reliable parts such as turbine blades, brackets, and fasteners.
These processes are crucial in helping aerospace manufacturers meet stringent regulatory standards while pushing the boundaries of innovation and performance.
Medical Industry
In the medical field, precision and performance are paramount.
MIM is used extensively to manufacture components for surgical instruments, orthopedic devices, and dental implants.
The process enables the production of highly complex and customized parts that meet exact specifications, ensuring high functionality and reliability in medical applications.
Moreover, the use of biocompatible materials in the MIM process aligns with health sector requirements, contributing to patient safety and outcomes.
Conclusion
Powder metallurgy and MIM are transforming industries with their ability to produce high-performance, high-strength components with exceptional efficiency and accuracy.
As technology advances, these processes continue to evolve, offering even greater potential for innovation and environmental responsibility.
By understanding the key factors involved in powder metallurgy and MIM processes, manufacturers can better leverage these technologies to meet modern-day challenges and demands.
The combination of material science, precision engineering, and process optimization makes powder metallurgy and MIM indispensable in today’s competitive industrial landscape.
資料ダウンロード
QCD管理受発注クラウド「newji」は、受発注部門で必要なQCD管理全てを備えた、現場特化型兼クラウド型の今世紀最高の受発注管理システムとなります。
ユーザー登録
受発注業務の効率化だけでなく、システムを導入することで、コスト削減や製品・資材のステータス可視化のほか、属人化していた受発注情報の共有化による内部不正防止や統制にも役立ちます。
NEWJI DX
製造業に特化したデジタルトランスフォーメーション(DX)の実現を目指す請負開発型のコンサルティングサービスです。AI、iPaaS、および先端の技術を駆使して、製造プロセスの効率化、業務効率化、チームワーク強化、コスト削減、品質向上を実現します。このサービスは、製造業の課題を深く理解し、それに対する最適なデジタルソリューションを提供することで、企業が持続的な成長とイノベーションを達成できるようサポートします。
製造業ニュース解説
製造業、主に購買・調達部門にお勤めの方々に向けた情報を配信しております。
新任の方やベテランの方、管理職を対象とした幅広いコンテンツをご用意しております。
お問い合わせ
コストダウンが利益に直結する術だと理解していても、なかなか前に進めることができない状況。そんな時は、newjiのコストダウン自動化機能で大きく利益貢献しよう!
(β版非公開)