- お役立ち記事
- Key points of “why-why analysis” to prevent defects from occurring and leaks and their application to preventing recurrence
月間76,176名の
製造業ご担当者様が閲覧しています*
*2025年3月31日現在のGoogle Analyticsのデータより
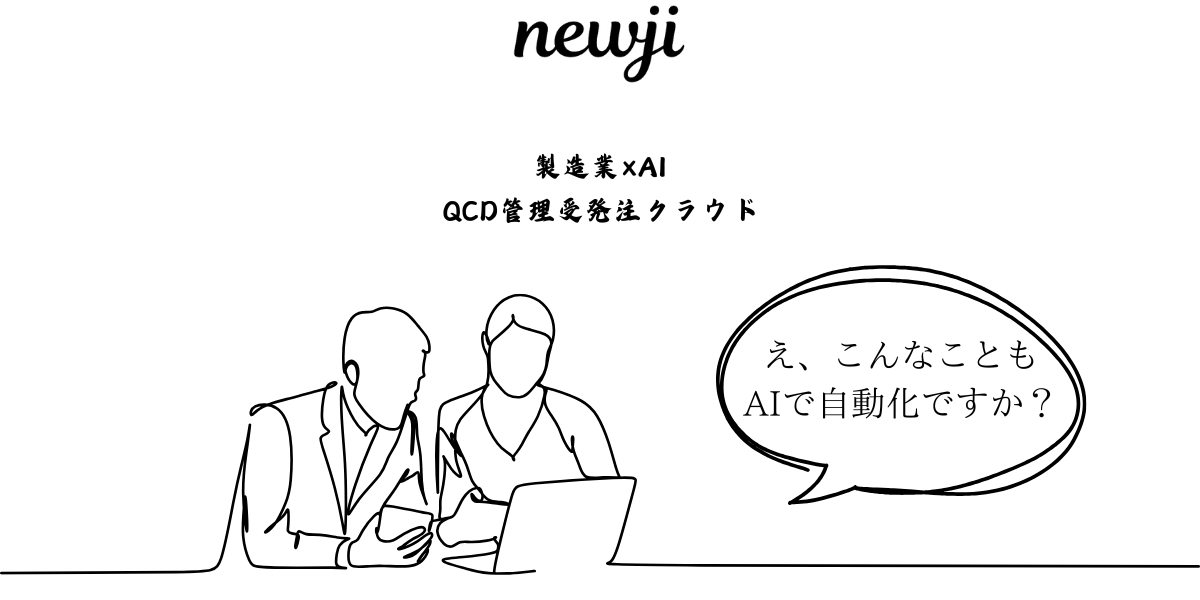
Key points of “why-why analysis” to prevent defects from occurring and leaks and their application to preventing recurrence
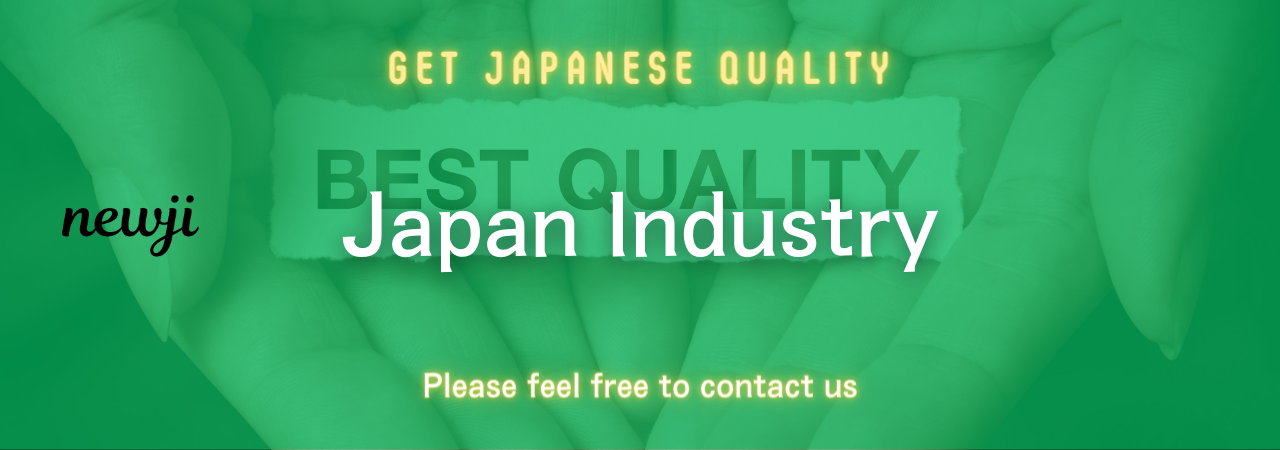
目次
Understanding Why-Why Analysis
Why-Why Analysis is a powerful tool used to identify the root cause of a problem.
Unlike other approaches that might focus on symptoms, this method digs deeper to find the origin of the issue.
It involves asking “why” repeatedly, typically five times, until the fundamental cause is revealed.
The primary goal is to prevent defects or problems from recurring.
In the manufacturing industry, for instance, addressing root causes rather than symptoms can significantly reduce production errors.
Businesses in various sectors have adopted this technique to bolster their problem-solving processes.
The Benefits of Why-Why Analysis
Implementing Why-Why Analysis offers several advantages.
Firstly, it promotes a thorough understanding of issues.
By exploring various layers of a problem, teams can grasp the complexities that might be overlooked if only surface issues are considered.
Secondly, Why-Why Analysis is both simple and cost-effective.
It doesn’t require elaborate tools or significant financial investment.
All it needs is a collaborative approach and a willingness to dig deeper into the issues at hand.
Thirdly, it encourages teamwork and communication.
Since this method is often conducted in groups, it allows team members to share their insights and perspectives on the problem.
This collaborative approach often leads to more comprehensive and effective solutions.
Enhancing Problem-Solving Skills
Employing Why-Why Analysis can enhance problem-solving skills within an organization.
As team members regularly engage in identifying and resolving the root causes of problems, their analytical thinking improves.
This, in turn, builds a culture of continuous improvement and proactive problem-solving.
Steps to Conduct a Why-Why Analysis
To effectively perform a Why-Why Analysis, follow these key steps.
Step 1: Define the Problem
The first step in the analysis is to clearly define the problem.
Understanding the issue in detail is crucial.
This involves gathering all the relevant information and data about the problem to ensure a comprehensive overview.
Step 2: Ask “Why”
Begin asking “why” regarding the problem’s occurrence.
The first “why” should aim to uncover the immediate reason for the problem.
It’s essential to base each question on facts rather than assumptions or guesses.
Step 3: Continue Asking “Why”
For every answer provided, ask “why” again.
Repeat this process at least five times or until the root cause becomes apparent.
This iterative questioning helps peel back the layers of the issue, potentially revealing unexpected insights.
Step 4: Identify the Root Cause
Once you reach a logical stopping point, assess whether you have identified the root cause.
Sometimes, additional research or information may compel you to modify your findings.
Step 5: Develop an Action Plan
After identifying the root cause, create an action plan to address it.
The action plan should be specific, detailing what will be done, who will do it, and a timeline for completion.
This ensures accountability and clarity in the problem-solving process.
Applying Why-Why Analysis to Prevent Recurrence
Preventing issues from recurring is one of the primary benefits of Why-Why Analysis.
By addressing the root cause, you can implement permanent corrective actions that eliminate the problem’s reappearance.
Real-World Application
In the automotive industry, for example, Why-Why Analysis has been pivotal in improving safety and quality.
When a fault is detected, teams use this method to trace back to the root cause and implement design or process changes to prevent similar occurrences in the future.
In healthcare, Why-Why Analysis can help reduce medical errors.
By examining the reasons behind mistakes or failures, healthcare providers can bolster protocols and training to safeguard against future errors.
Challenges and Considerations
While powerful, Why-Why Analysis is not without challenges.
One must be cautious of human biases that can affect the questioning process.
Additionally, the success of this method hinges on the accuracy and completeness of the information collected.
Time constraints can also limit the depth of the analysis.
Conclusion
Why-Why Analysis is an invaluable tool for identifying and addressing the root causes of problems.
Its simplistic nature belies the profound impact it can have on reducing defects and preventing their recurrence.
By fostering a culture of inquiry and continuous improvement, organizations can enhance their operational efficiency and output quality.
Integrating this method into daily problem-solving not only prevents issues from recurring but also strengthens the overall resilience of systems and processes.
資料ダウンロード
QCD管理受発注クラウド「newji」は、受発注部門で必要なQCD管理全てを備えた、現場特化型兼クラウド型の今世紀最高の受発注管理システムとなります。
ユーザー登録
受発注業務の効率化だけでなく、システムを導入することで、コスト削減や製品・資材のステータス可視化のほか、属人化していた受発注情報の共有化による内部不正防止や統制にも役立ちます。
NEWJI DX
製造業に特化したデジタルトランスフォーメーション(DX)の実現を目指す請負開発型のコンサルティングサービスです。AI、iPaaS、および先端の技術を駆使して、製造プロセスの効率化、業務効率化、チームワーク強化、コスト削減、品質向上を実現します。このサービスは、製造業の課題を深く理解し、それに対する最適なデジタルソリューションを提供することで、企業が持続的な成長とイノベーションを達成できるようサポートします。
製造業ニュース解説
製造業、主に購買・調達部門にお勤めの方々に向けた情報を配信しております。
新任の方やベテランの方、管理職を対象とした幅広いコンテンツをご用意しております。
お問い合わせ
コストダウンが利益に直結する術だと理解していても、なかなか前に進めることができない状況。そんな時は、newjiのコストダウン自動化機能で大きく利益貢献しよう!
(β版非公開)