- お役立ち記事
- Key Quality Control Points to Prevent Issues in Roll Forming
月間76,176名の
製造業ご担当者様が閲覧しています*
*2025年3月31日現在のGoogle Analyticsのデータより
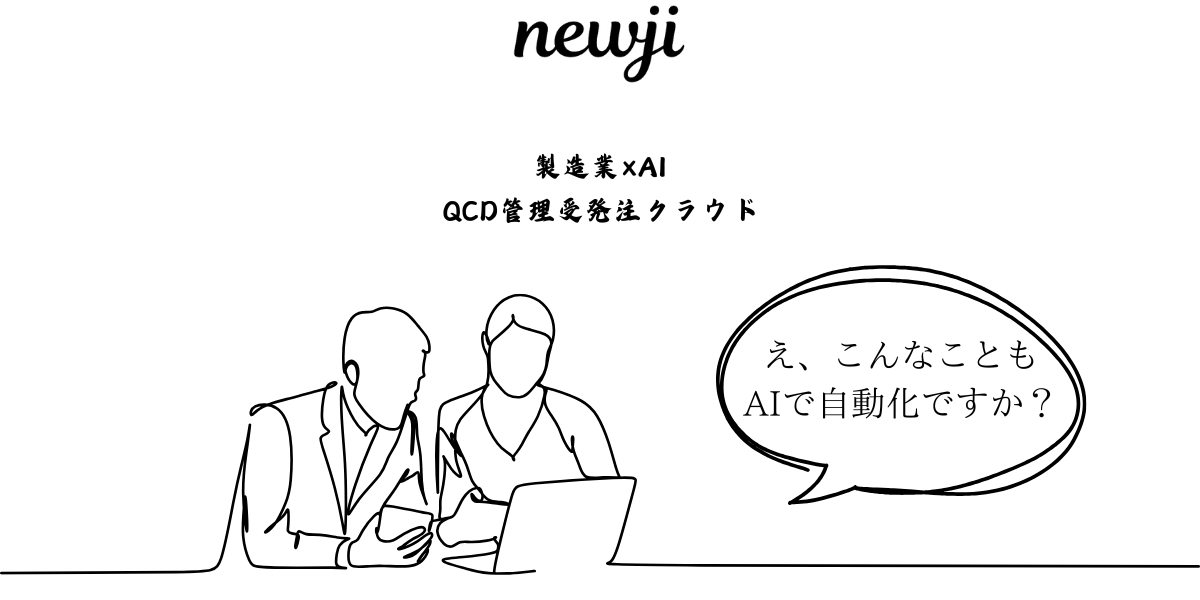
Key Quality Control Points to Prevent Issues in Roll Forming
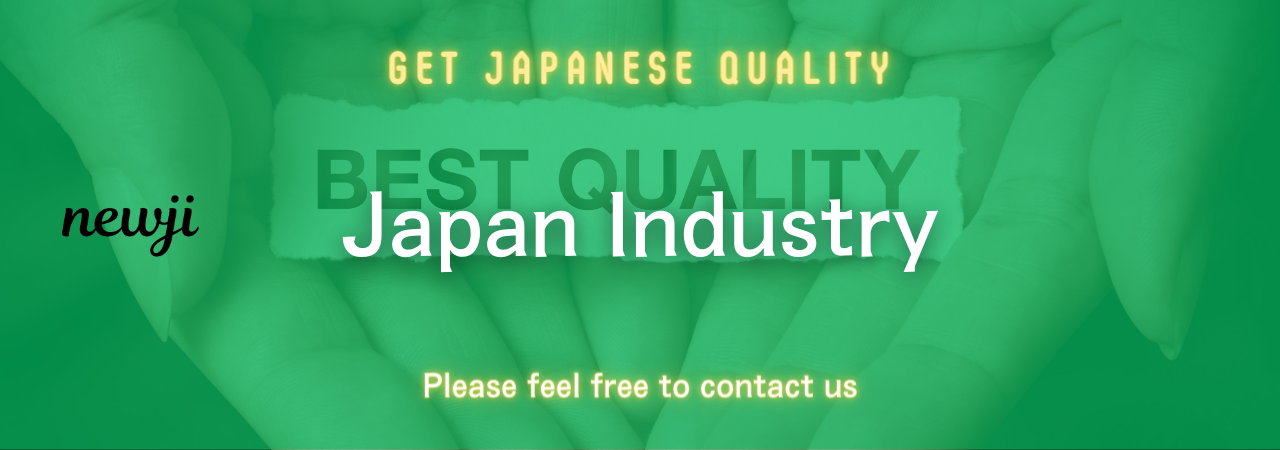
目次
Introduction
Roll forming is a vital process in the manufacturing of various metal components.
It involves the continuous bending of a long strip of metal into a desired cross-section.
As this method provides high efficiency and precision, ensuring the quality control of the roll forming process is crucial to prevent issues.
Understanding the key quality control points can significantly enhance the final product’s reliability and performance.
Let’s explore some important aspects to monitor during roll forming.
Material Selection and Specifications
Importance of Material Quality
The selection of the right material is the cornerstone of any successful roll forming project.
Using poor quality or incorrect materials can lead to product failures and operational inefficiencies.
Key properties to check include the material’s thickness, tensile strength, and ductility.
Testing for Consistency
Consistency in material quality is also essential.
Regular testing for material properties ensures uniformity, eliminating variations that may cause defects.
Implementing thorough inspection protocols can help detect issues early, preventing downstream problems.
Equipment Calibration and Maintenance
Precision in Tooling and Machinery
For optimal results in roll forming, machines and tooling must be meticulously calibrated.
Even slight inaccuracies can lead to defects in the end product.
Regular calibration of roll forming machines ensures adherence to desired dimensions and tolerances.
Regular Maintenance Routines
Preventive maintenance is crucial in maintaining high-quality production.
Scheduled maintenance routines help in identifying wear and tear, preventing unexpected breakdowns.
Ensuring that all components are in good working condition reduces the risk of production downtimes and maintains the quality of output.
Process Monitoring and Control
Setting Up process Parameters
Establishing precise and repeatable process parameters is vital for quality control.
This includes settings such as roll speed, pressure, and alignment.
Adherence to these parameters ensures consistent product quality.
Real-Time Monitoring Systems
Incorporating real-time monitoring systems can provide immediate feedback on the process.
These systems detect deviations from set parameters and alert operators to take corrective actions swiftly.
This proactive approach minimizes waste and enhances production efficiency.
Quality Inspections and Testing
Dimensional Accuracy Checks
Regular dimensional checks are vital to maintaining product standards.
Measuring components’ length, width, and thickness ensures they meet the specified requirements.
Advanced measuring tools and technologies can enhance the accuracy of these inspections.
Surface Finish and Visual Inspections
Apart from dimensional checks, visual inspections of the surface finish can detect imperfections like scratches, dents, or uneven surfaces.
Such defects can affect the product’s performance and aesthetics.
Conducting these inspections at various production stages ensures defects are caught early.
Employee Training and Expertise
Skill Development Programs
A well-trained workforce is integral to maintaining quality in roll forming.
Regular training programs ensure that operators are knowledgeable about the latest techniques and best practices.
This helps in efficient troubleshooting and maintaining high process standards.
Fostering a Quality-Centric Culture
Encouraging a culture that prioritizes quality can lead to continuous improvement.
Employees should be motivated to identify and report potential issues.
This collaborative approach helps in maintaining consistent product quality and operational efficiency.
Documentation and Record Keeping
Tracking Batch Records
Maintaining detailed records of each production batch is a critical quality control practice.
These records should include material used, process parameters, inspection results, and any deviations noted.
Such documentation helps in tracing back defects and implementing corrective measures.
Compliance and Standards
Adhering to industry standards and regulations is essential.
Compliance ensures that the products meet specific safety and quality benchmarks.
Regular audits and reviews of documentation help in maintaining these standards and boosting customer confidence.
Conclusion
Implementing robust quality control measures in roll forming is essential to prevent issues and ensure high standards.
By focusing on material selection, equipment maintenance, process monitoring, inspections, employee training, and thorough documentation, manufacturers can achieve consistent product quality.
These practices not only enhance operational efficiency but also ensure customer satisfaction and long-term success in the market.
資料ダウンロード
QCD管理受発注クラウド「newji」は、受発注部門で必要なQCD管理全てを備えた、現場特化型兼クラウド型の今世紀最高の受発注管理システムとなります。
ユーザー登録
受発注業務の効率化だけでなく、システムを導入することで、コスト削減や製品・資材のステータス可視化のほか、属人化していた受発注情報の共有化による内部不正防止や統制にも役立ちます。
NEWJI DX
製造業に特化したデジタルトランスフォーメーション(DX)の実現を目指す請負開発型のコンサルティングサービスです。AI、iPaaS、および先端の技術を駆使して、製造プロセスの効率化、業務効率化、チームワーク強化、コスト削減、品質向上を実現します。このサービスは、製造業の課題を深く理解し、それに対する最適なデジタルソリューションを提供することで、企業が持続的な成長とイノベーションを達成できるようサポートします。
製造業ニュース解説
製造業、主に購買・調達部門にお勤めの方々に向けた情報を配信しております。
新任の方やベテランの方、管理職を対象とした幅広いコンテンツをご用意しております。
お問い合わせ
コストダウンが利益に直結する術だと理解していても、なかなか前に進めることができない状況。そんな時は、newjiのコストダウン自動化機能で大きく利益貢献しよう!
(β版非公開)