- お役立ち記事
- Kinematic Analysis and Optimization of Industrial Robots
Kinematic Analysis and Optimization of Industrial Robots
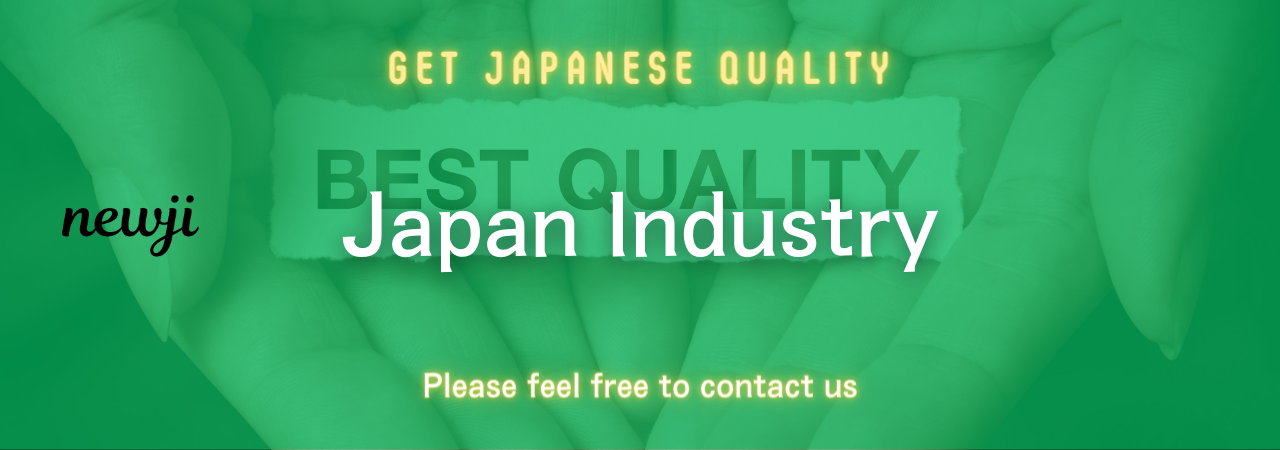
目次
Understanding Kinematics in Industrial Robotics
Kinematics is a fundamental concept that plays a significant role in robotics, particularly in industrial applications.
In essence, it is the study of motion without considering the forces that cause it.
For industrial robots, kinematics helps engineers and technicians understand and predict the movement of robot arms and other parts.
By analyzing kinematics, professionals can ensure that robots operate efficiently and safely in various tasks, from assembly lines to complex manufacturing processes.
There are two main types of kinematics used in robotics: forward kinematics and inverse kinematics.
Forward kinematics involves calculating the position and orientation of the robot’s end effector (the part of the robot that interacts with the environment) based on given joint parameters.
This type of kinematic analysis is relatively straightforward and involves simple mathematical calculations.
Inverse kinematics, on the other hand, is more complex.
It involves determining the joint parameters needed to achieve a desired position and orientation of the end effector.
This process can be challenging because multiple joint configurations can lead to the same end-effector position.
As a result, inverse kinematics often requires sophisticated algorithms and mathematical techniques to achieve optimal solutions.
Optimization Techniques in Industrial Robots
Optimization is a crucial aspect of industrial robotics, as it ensures that robots operate effectively and efficiently.
There are several optimization techniques that professionals use to enhance the performance and capabilities of industrial robots.
One common optimization technique is trajectory planning, which involves determining the best path for a robot to follow to achieve a specific task.
Trajectory planning accounts for factors such as speed, accuracy, and energy consumption, and it helps prevent collisions with other objects or robots.
By optimizing trajectories, engineers can ensure that robots perform tasks quickly and without unnecessary delays.
Another important aspect of optimization in industrial robotics is the selection of appropriate hardware and software components.
Choosing the right motors, controllers, and sensors can significantly impact the robot’s performance.
For example, high-precision sensors can improve a robot’s ability to detect and respond to environmental changes, while advanced controllers can provide better accuracy and control in complex tasks.
Additionally, optimizing the workspace layout is essential for industrial robotic applications.
Arranging equipment and materials in a manner that minimizes the robot’s travel distance can enhance overall efficiency and productivity.
Workspaces that are designed with optimization in mind often feature streamlined processes and strategically placed components to facilitate smooth and uninterrupted operations.
The Importance of Kinematic Analysis and Optimization
Kinematic analysis and optimization are integral to the success of industrial robotics.
By understanding kinematics, engineers can design robots that move accurately and predictably, leading to improved performance and safety.
Kinematic analysis helps identify potential issues in robot design and movement, allowing for timely adjustments to prevent failures or accidents.
Moreover, optimization techniques play a crucial role in maximizing the capabilities of industrial robots.
They help reduce operational costs by improving energy efficiency and minimizing wear and tear on equipment.
Optimal robot performance also contributes to higher product quality, as robots can consistently execute tasks with precision and accuracy.
In today’s rapidly evolving industrial landscape, the demand for efficient and adaptable robots continues to grow.
Businesses that invest in kinematic analysis and optimization can gain a competitive edge, as they can operate with greater flexibility and respond quickly to changing manufacturing needs.
Challenges and Future Directions
Despite the numerous benefits of kinematic analysis and optimization, there are still challenges that professionals face in the field of industrial robotics.
One challenge is the increasing complexity of industrial robots.
As robots become more sophisticated, the kinematic models and optimization algorithms used to control them must also evolve.
This requires ongoing research and development to keep pace with technological advancements.
Another challenge is the integration of robots into existing manufacturing systems.
Many industries have established processes and equipment that may not be immediately compatible with new robotic technologies.
As a result, effective communication and collaboration between robot manufacturers and end-users are essential to ensure seamless integration and adoption of advanced robotic solutions.
Looking to the future, the development of artificial intelligence and machine learning technologies holds great promise for enhancing kinematic analysis and optimization.
These technologies can enable robots to learn from their environment, adapt to new tasks, and optimize their performance autonomously.
The integration of AI-driven solutions in industrial robotics can lead to more efficient, flexible, and intelligent robotic systems.
Furthermore, the use of digital twins, which are virtual replicas of physical robots, can provide valuable insights into kinematic performance and optimization.
Digital twins allow engineers to simulate and analyze robot movements in a virtual environment, making it easier to test and refine designs before implementing them in the real world.
In conclusion, kinematic analysis and optimization are essential components of industrial robotics that contribute to improved performance, efficiency, and safety.
As technology advances, new methods and tools will continue to emerge, shaping the future of industrial robotics and enabling new possibilities for automation and manufacturing.
資料ダウンロード
QCD調達購買管理クラウド「newji」は、調達購買部門で必要なQCD管理全てを備えた、現場特化型兼クラウド型の今世紀最高の購買管理システムとなります。
ユーザー登録
調達購買業務の効率化だけでなく、システムを導入することで、コスト削減や製品・資材のステータス可視化のほか、属人化していた購買情報の共有化による内部不正防止や統制にも役立ちます。
NEWJI DX
製造業に特化したデジタルトランスフォーメーション(DX)の実現を目指す請負開発型のコンサルティングサービスです。AI、iPaaS、および先端の技術を駆使して、製造プロセスの効率化、業務効率化、チームワーク強化、コスト削減、品質向上を実現します。このサービスは、製造業の課題を深く理解し、それに対する最適なデジタルソリューションを提供することで、企業が持続的な成長とイノベーションを達成できるようサポートします。
オンライン講座
製造業、主に購買・調達部門にお勤めの方々に向けた情報を配信しております。
新任の方やベテランの方、管理職を対象とした幅広いコンテンツをご用意しております。
お問い合わせ
コストダウンが利益に直結する術だと理解していても、なかなか前に進めることができない状況。そんな時は、newjiのコストダウン自動化機能で大きく利益貢献しよう!
(Β版非公開)