- お役立ち記事
- Kitchen Aluminum Foil Manufacturing Process and Thickness Improvement
月間77,185名の
製造業ご担当者様が閲覧しています*
*2025年2月28日現在のGoogle Analyticsのデータより
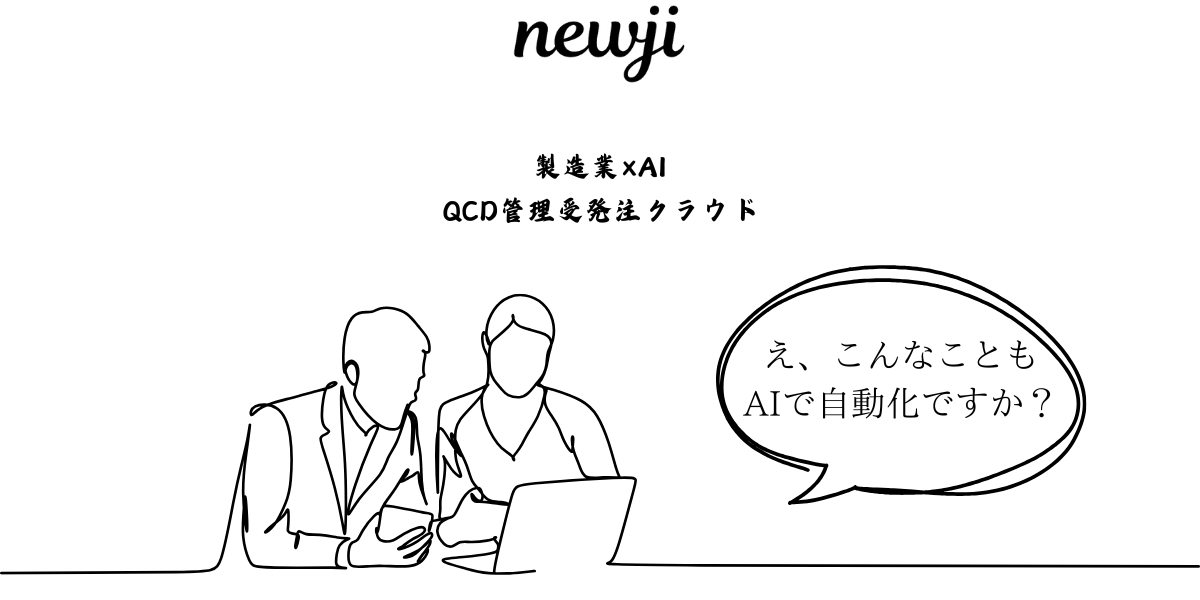
Kitchen Aluminum Foil Manufacturing Process and Thickness Improvement
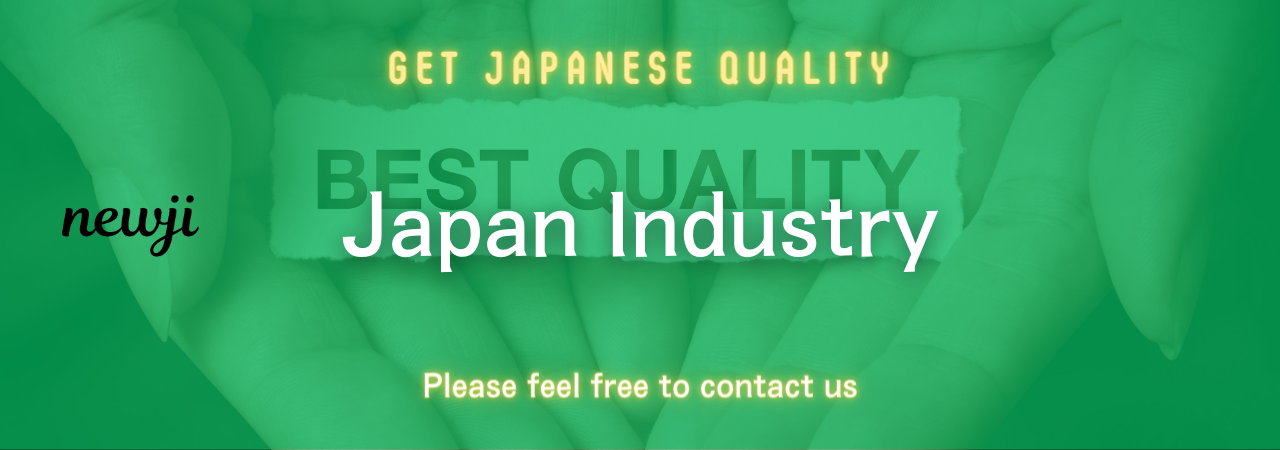
Aluminum foil is an essential item in most kitchens.
It’s versatile and useful for cooking, storage, and even cleaning.
But have you ever wondered how it’s made?
This article will explain the process of manufacturing kitchen aluminum foil and explore ways to improve its thickness.
目次
How Aluminum Foil Is Made
Raw Material Extraction
The primary raw material for aluminum foil is bauxite.
This mineral is found in abundance in various parts of the world.
The first step in manufacturing aluminum foil is to extract bauxite from the earth.
This usually involves open-pit mining techniques.
Once the bauxite is extracted, it needs to be processed to produce alumina, or aluminum oxide.
Alumina Production
After extraction, the bauxite is crushed and mixed with sodium hydroxide (caustic soda).
This mixture is then heated in high-pressure containers.
The heating process causes the bauxite to dissolve, leaving behind impurities.
The result is a solution rich in alumina.
This solution is then cooled, and aluminum hydroxide crystals form.
These crystals are filtered out and heated to create pure alumina powder.
Electrolysis
To transform alumina into aluminum metal, manufacturers use a process called electrolysis.
This involves dissolving the alumina in a molten electrolyte and passing an electrical current through it.
The electrical current separates the aluminum atoms from the oxygen atoms, causing molten aluminum to form at the bottom of the container.
This molten aluminum is then siphoned off and cast into large blocks called ingots.
Rolling Process
Once the aluminum has been cast into ingots, it undergoes a rolling process to transform it into a thin sheet.
The ingots are heated to make them soft and malleable.
They are then passed through a series of rolling mills.
These mills gradually reduce the thickness of the ingots.
The final rolling mill reduces the thickness of the aluminum to the desired level for kitchen foil, usually between 0.007 mm to 0.024 mm.
Annealing
Annealing is an essential part of the manufacturing process.
After rolling, the aluminum foil is often too hard and brittle.
Annealing involves heating the foil to a specific temperature and then cooling it at a controlled rate.
This process softens the aluminum, making it more pliable and easier to use.
Quality Control in Aluminum Foil Manufacturing
Thickness Measurement
Ensuring the right thickness is crucial for aluminum foil.
Manufacturers use precise instruments to measure the thickness of the foil.
This helps in maintaining consistency and quality.
Advanced techniques like laser thickness gauges or X-ray machines are often used in modern manufacturing facilities.
Surface Finish
A smooth surface finish is essential for aluminum foil.
Imperfections can lead to tearing or poor performance during use.
Manufacturers inspect the surface of the foil for any defects.
If any issues are detected, the foil is either fixed or discarded.
Tensile Strength
The tensile strength of aluminum foil is another critical quality parameter.
Manufacturers conduct strength tests to ensure the foil can withstand normal usage without breaking.
This involves pulling a sample piece of foil until it breaks and measuring the force required to do so.
By ensuring high tensile strength, manufacturers can provide a durable product for consumers.
Improving Aluminum Foil Thickness
Advanced Rolling Techniques
One way to improve the thickness of aluminum foil is by using advanced rolling techniques.
Manufacturers continuously invest in new technologies to achieve more precise control over the rolling process.
This can involve using more sophisticated rolling mills that can make finer adjustments to the thickness.
Better Quality Control
Improving quality control processes can also help in achieving the desired thickness.
By employing more advanced measurement equipment, manufacturers can detect even the smallest deviations in thickness.
This allows for real-time adjustments during the rolling process, leading to a more consistent product.
Material Additives
In some cases, manufacturers can add certain materials to improve the properties of aluminum foil.
These additives can help make the foil stronger, allowing it to be rolled thinner without compromising its durability.
Research and development in this area are ongoing, with many manufacturers experimenting with different additives to find the best solutions.
Heat Treatment Improvements
Enhancing heat treatment processes can also contribute to improving the thickness of aluminum foil.
By optimizing annealing temperatures and times, manufacturers can achieve better material properties.
This makes the foil easier to roll to thinner dimensions while maintaining its strength and flexibility.
Aluminum foil is an indispensable item in any kitchen, and its manufacturing process is fascinating.
From raw material extraction and alumina production to the intricate rolling and annealing processes, each step plays a crucial role in producing this versatile product.
By continuously improving techniques and adopting advanced technologies, manufacturers can achieve better thickness control, resulting in higher quality aluminum foil.
Understanding how aluminum foil is made and the efforts put into improving its quality can enhance our appreciation of this everyday kitchen essential.
資料ダウンロード
QCD管理受発注クラウド「newji」は、受発注部門で必要なQCD管理全てを備えた、現場特化型兼クラウド型の今世紀最高の受発注管理システムとなります。
ユーザー登録
受発注業務の効率化だけでなく、システムを導入することで、コスト削減や製品・資材のステータス可視化のほか、属人化していた受発注情報の共有化による内部不正防止や統制にも役立ちます。
NEWJI DX
製造業に特化したデジタルトランスフォーメーション(DX)の実現を目指す請負開発型のコンサルティングサービスです。AI、iPaaS、および先端の技術を駆使して、製造プロセスの効率化、業務効率化、チームワーク強化、コスト削減、品質向上を実現します。このサービスは、製造業の課題を深く理解し、それに対する最適なデジタルソリューションを提供することで、企業が持続的な成長とイノベーションを達成できるようサポートします。
製造業ニュース解説
製造業、主に購買・調達部門にお勤めの方々に向けた情報を配信しております。
新任の方やベテランの方、管理職を対象とした幅広いコンテンツをご用意しております。
お問い合わせ
コストダウンが利益に直結する術だと理解していても、なかなか前に進めることができない状況。そんな時は、newjiのコストダウン自動化機能で大きく利益貢献しよう!
(β版非公開)