- お役立ち記事
- Know-how on schedule compliance and quality cost management in the development and design department
月間76,176名の
製造業ご担当者様が閲覧しています*
*2025年3月31日現在のGoogle Analyticsのデータより
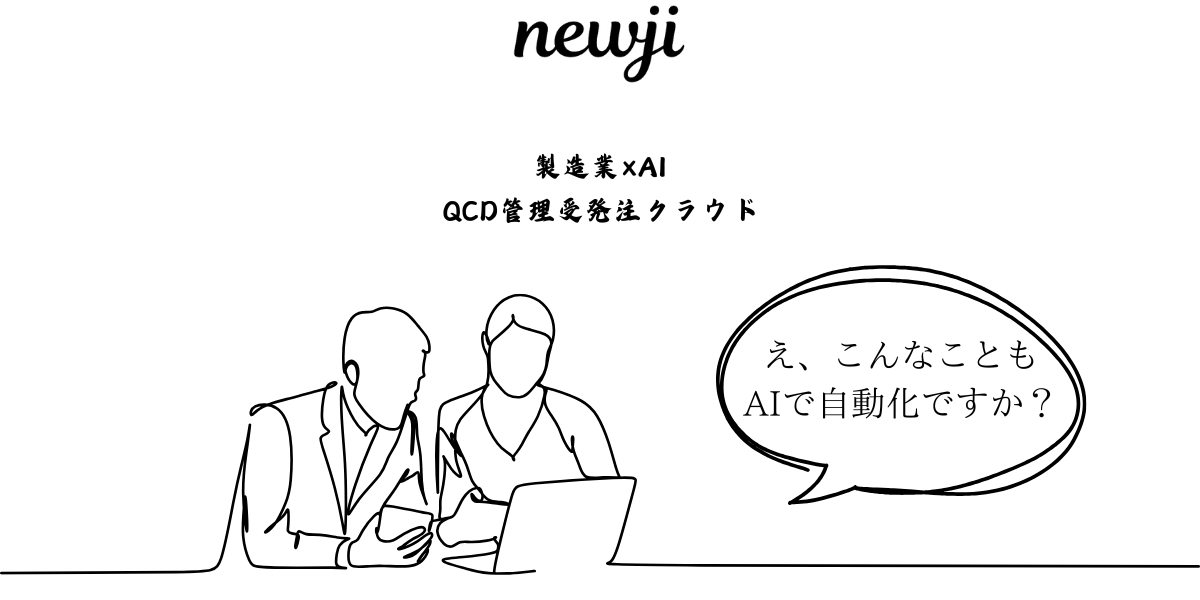
Know-how on schedule compliance and quality cost management in the development and design department
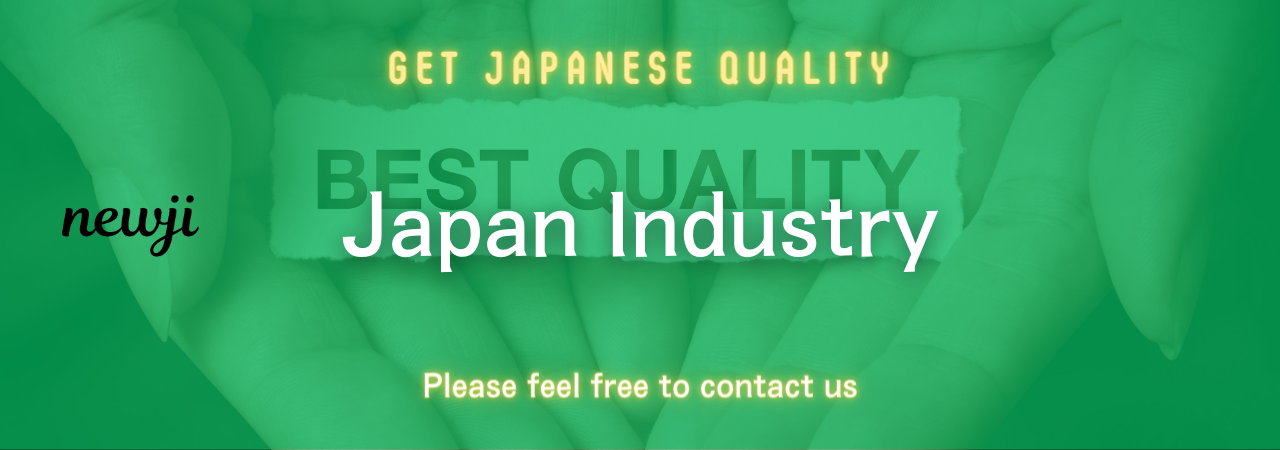
目次
Understanding Schedule Compliance in Development and Design
Schedule compliance in the development and design department is a critical component for ensuring that projects are delivered on time.
It involves setting realistic timelines and consistently adhering to them throughout the project life cycle.
Achieving schedule compliance requires a clear understanding of project goals, efficient planning, and coordination among team members.
To begin with, it’s essential to establish a project timeline that considers all aspects of the development and design process.
This includes accounting for planning, drafting, prototyping, testing, and revisions.
The timeline should be developed with input from all team members to ensure accuracy and buy-in.
Once the timeline is established, adhering to it requires diligent monitoring and adjustment.
Project managers should regularly track progress against the timeline and identify any potential risks or delays early on.
This allows for timely interventions and adjustments to keep the project on schedule.
Effective communication among team members is also crucial for maintaining schedule compliance.
Regular meetings and status updates ensure everyone is on the same page and aware of their responsibilities.
By fostering a collaborative environment, team members can work more efficiently and hold each other accountable for meeting deadlines.
Strategies for Quality Cost Management
Quality cost management is an essential element of ensuring that products meet or exceed customer expectations while remaining cost-effective.
It involves understanding and managing the costs associated with quality assurance, such as prevention, appraisal, and failure costs.
Prevention costs are proactive measures taken to ensure quality from the start.
These include training, process improvement, and quality planning.
By investing in prevention, organizations can reduce the likelihood of defects and errors, ultimately saving money in the long run.
Appraisal costs are associated with evaluating and inspecting products to ensure they meet quality standards.
This includes testing, audits, and inspections.
While appraisal costs are necessary, they should be balanced with prevention efforts to ensure cost efficiency.
Failure costs are incurred when products fail to meet quality standards and require rectification.
These can be internal failures, detected before the product reaches the customer, or external failures, identified once the product is in use.
Minimizing failure costs requires a robust quality management system that emphasizes prevention and early detection.
Integrating Schedule Compliance and Quality Cost Management
Successfully integrating schedule compliance and quality cost management leads to optimal project outcomes and customer satisfaction.
To achieve this integration, organizations must prioritize both time management and quality within their processes.
One approach is to implement a comprehensive project management system that aligns schedule compliance with quality objectives.
Project managers should ensure that timelines include all quality-related activities, such as inspections and testing, to avoid delays caused by oversight.
Furthermore, cultivating a culture of excellence within the department encourages team members to value quality and timeliness equally.
Providing training on quality management principles and time management techniques enhances the team’s overall effectiveness.
Regular assessment and feedback loops are essential for continuous improvement.
By evaluating project outcomes and team performance, organizations can identify areas for improvement and implement necessary changes.
Leveraging Technology for Better Compliance and Cost Management
Technology plays a vital role in improving schedule compliance and quality cost management.
Utilizing project management software streamlines scheduling and tracking, providing real-time insights into project progress and potential risks.
This enables teams to make informed decisions and adjust plans proactively.
Quality management systems, integrated with project management tools, allow organizations to maintain high quality standards efficiently.
Automated testing and inspection tools can reduce appraisal costs and improve detection of defects, ensuring issues are resolved promptly.
Data analytics can also provide valuable insights into trends and patterns in schedule compliance and quality performance.
By analyzing historical data, organizations can identify root causes of delays or quality issues and develop strategies to address them.
Developing Strong Leadership and Team Dynamics
Effective leadership is crucial for achieving schedule compliance and managing quality costs.
Leaders should demonstrate strong organizational skills and the ability to motivate and guide their teams toward common goals.
By setting clear expectations and providing support, leaders can empower their teams to deliver projects on time and maintain quality standards.
Team dynamics also significantly impact schedule and quality outcomes.
Encouraging open communication, collaboration, and mutual respect among team members fosters a positive work environment.
When teams work cohesively, they can address challenges more effectively and maintain focus on delivering high-quality results on time.
Conclusion: Balancing Quality and Time for Successful Projects
Schedule compliance and quality cost management are interconnected components that play a pivotal role in the success of development and design projects.
By establishing clear timelines, investing in quality management, leveraging technology, and fostering strong leadership and teamwork, organizations can achieve the right balance between time and quality.
Ultimately, this balance leads to increased customer satisfaction, cost savings, and enhanced reputation in the marketplace.
By prioritizing both schedule compliance and quality cost management, companies can ensure that their development and design departments consistently deliver excellent results.
資料ダウンロード
QCD管理受発注クラウド「newji」は、受発注部門で必要なQCD管理全てを備えた、現場特化型兼クラウド型の今世紀最高の受発注管理システムとなります。
ユーザー登録
受発注業務の効率化だけでなく、システムを導入することで、コスト削減や製品・資材のステータス可視化のほか、属人化していた受発注情報の共有化による内部不正防止や統制にも役立ちます。
NEWJI DX
製造業に特化したデジタルトランスフォーメーション(DX)の実現を目指す請負開発型のコンサルティングサービスです。AI、iPaaS、および先端の技術を駆使して、製造プロセスの効率化、業務効率化、チームワーク強化、コスト削減、品質向上を実現します。このサービスは、製造業の課題を深く理解し、それに対する最適なデジタルソリューションを提供することで、企業が持続的な成長とイノベーションを達成できるようサポートします。
製造業ニュース解説
製造業、主に購買・調達部門にお勤めの方々に向けた情報を配信しております。
新任の方やベテランの方、管理職を対象とした幅広いコンテンツをご用意しております。
お問い合わせ
コストダウンが利益に直結する術だと理解していても、なかなか前に進めることができない状況。そんな時は、newjiのコストダウン自動化機能で大きく利益貢献しよう!
(β版非公開)